In die casting, the placement of thermocouples is crucial for accurately monitoring and controlling the process.
Critical Installation Locations of thermocouples in die casting
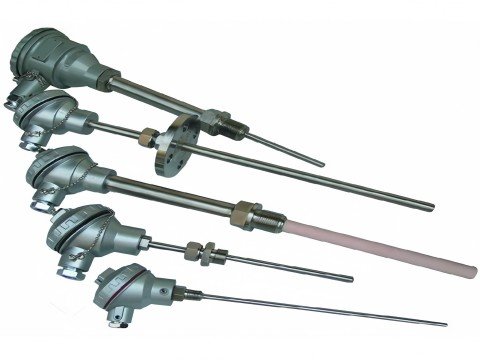
Here are the critical installation locations and guidelines for thermocouples in die casting.
Surface Thermocouple (Ts)
- Location: The surface thermocouple hole should be located in the center of the largest area of the die on the backside. It should be at least 1/4T x 1/4W or mid-radius from the nearest corner.
- Depth and Diameter: The hole should be 1/8” to 1/4” (3.2mm to 6.4mm) in diameter and 0.625” ± 0.125” (15.9mm ± 3.2mm) deep. This ensures that the thermocouple can accurately measure the surface temperature without being too exposed or too recessed.
Core Thermocouple (Tc)
- Location: The core thermocouple should be placed as close to the center of mass as possible, typically using existing coolant holes. If this is not possible, a representative load block with a thermocouple at its center of mass should be used.
- Purpose: This placement helps in monitoring the internal temperature of the die. It is essential for understanding the cooling rate and ensuring uniform heat treatment.
Near Casting-Die Interface
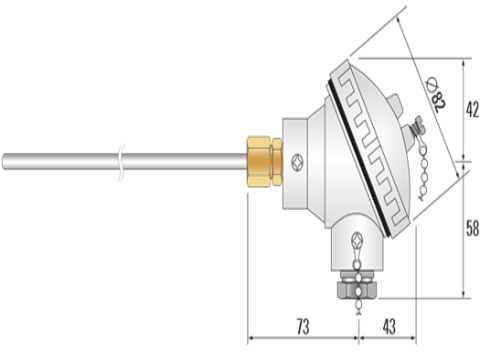
- Location: For accurately determining the heat transfer coefficient (HTC) between the casting and the die, thermocouples should be placed near the casting-die interface. This helps in capturing the temperature changes during the solidification process.
- Distance: The thermocouples should be placed 6–10 mm from the casting surface. This proximity ensures that the temperature measurements reflect the conditions at the interface accurately.
Multiple Thermocouples for Complex Dies
- Location: In complex die designs, multiple thermocouples (e.g., Ts1, Ts2, Ts3) can be used to monitor different sections of the die. This is particularly useful for large dies or those with varying thicknesses.
- Guidelines: Each thermocouple should be placed in a way that it can capture the temperature variations in its specific section. For example, thermocouples can be placed at different steps of a “step shape” casting to study the heat transfer profiles.
General Installation Tips
- Secure Wires: Thermocouple wires must be secured to prevent movement during quenching or other operations.
- Avoid Direct Contact: If a waterline hole is used for a thermocouple. It should be packed with a fiber refractory material to prevent direct contact with the quenchant.
- Accessibility: The thermocouples should be accessible during the heat treatment process for monitoring and maintenance.
Die casting machine supplier: Haichen Machinery
Haichen Machinery is a supplier of die casting machines and related spear parts. We specialize in providing die casting production solutions for various materials, including aluminum, magnesium, zinc, and copper alloys. Our cold chamber and hot chamber die casting machines are used for manufacturing products such as automotive parts, LED lamp shells, radiators, and household appliance components.
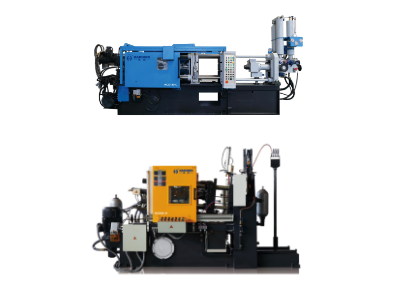
Thermocouple mounting locations should be optimized for specific needs. It includes critical locations within the mold cavity, at the casting interface, in different areas of the mold, near cooling channels, on the mold cover and push-out side. In addition, the use of special mounts or non-intrusive techniques can improve the accuracy and reliability of measurements.
Through proper placement of thermocouples, temperature distribution during the die casting process can be comprehensively monitored to optimize process parameters and improve product quality.