The Density of Aluminum & Aluminum Alloys is key for applications. Pure aluminum and common alloys have densities around 2.7 g/cm³.
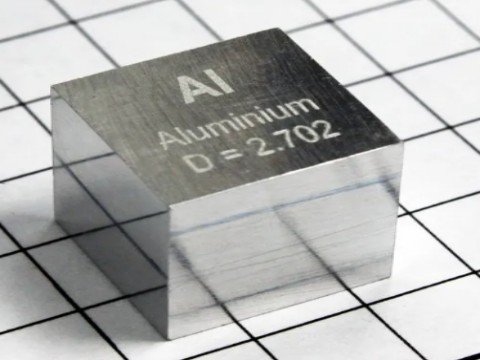
Aluminum is one of the most abundant metal elements in the earth’s crust. We widely use it in aerospace, automobile manufacturing, construction, and other fields due to its light weight, corrosion resistance, and excellent processing performance.
Density, as a key physical property of a material, directly affects its application scenarios. This article will start from the density of pure aluminum and explore the density variation law of aluminum alloys and its relationship with the die-casting process.
Density of Aluminum & Aluminum Alloys
Density of Pure Aluminum
The density of pure aluminum is approximately 2.7 grams per cubic centimeter (g/cm³). This relatively low density makes aluminum an ideal material for applications where weight reduction is critical, such as in the automotive and aerospace industries. The lightweight nature of aluminum helps improve fuel efficiency and overall performance.
Density of Aluminum Alloys
Adding alloying elements like magnesium, silicon, and copper significantly improves aluminum’s mechanical properties and slightly changes its density. The density range of common aluminum alloys is as follows:
- 1xxx series (such as 1100): close to pure aluminum, about 2.71 g/cm³5.
- 2xxx series (such as 2024): after adding copper, the density increases slightly to 2.78 g/cm³5.
- 6xxx series (such as 6061): the addition of magnesium and silicon keeps the density at 2.7 g/cm³ while improving the strength11.
- 7xxx series (such as 7075): high zinc content increases the density to 2.81 g/cm³, but the strength can reach 572 MPa5.
- Special alloys (such as 8090): contain lithium elements, the density is as low as 2.54 g/cm³, suitable for aerospace5.
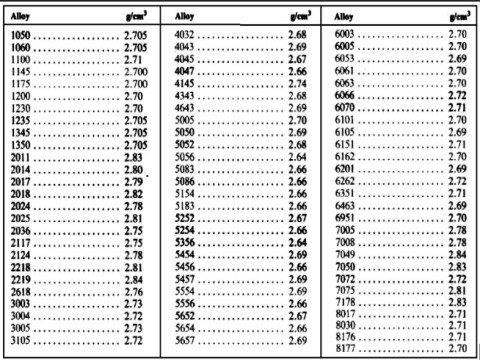
Influencing factors: the atomic weight of the alloying elements, the addition ratio and the heat treatment process will affect the density. For example, T6 heat treatment increases strength through precipitation strengthening but has little effect on density11.
Relationship between die casting process and density
Die casting is a process for efficiently producing complex aluminum parts. During the process, molten aluminum is injected into a steel mold under high pressure and quickly cooled to form. The impact of this process on material density is reflected in two aspects:
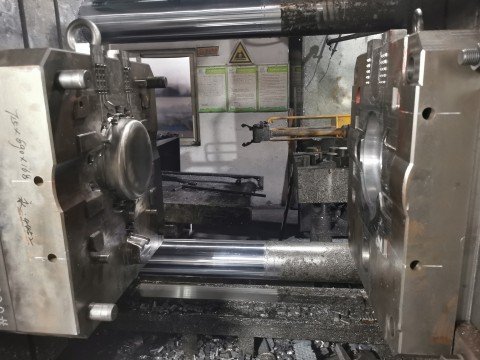
1.Porosity control: The high-pressure environment reduces the residual gas in the melt, improves the density of the material, and thus improves the mechanical properties6.
2.Alloy selection: Die casting commonly uses alloys with good fluidity (such as A380, ADC-12), with a density of about 2.7-2.8 g/cm³, taking into account both molding efficiency and strength6.
Limitations: Tiny pores may remain inside the die casting, so T6 heat treatment is usually not performed (to avoid surface defects caused by gas expansion)
Application advantages of die casting
- High precision: complex parts with uniform wall thickness can be produced with a tolerance of ±0.1 mm6.
- Fast mass production: the mold can be reused, suitable for large-volume needs such as automotive parts and electronic housings614.
- Cost-effectiveness: compared with sand casting, die casting has a high surface finish and reduces subsequent processing steps
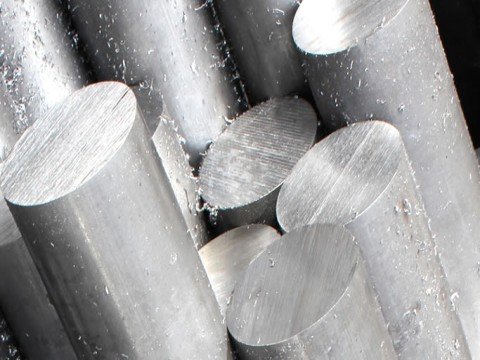
Die-casting machine manufacturer: HAICHEN
As China’s leading die-casting equipment manufacturer, HAICHEN focuses on the research and development and production of high-performance die-casting machines.
Our company offers a wide range of die casting machines, including cold chamber and hot chamber models, to meet different production needs.
Haichen also provides comprehensive after-sales services, including technical support, spare parts supply and training, to ensure that customers get the most from their investment.
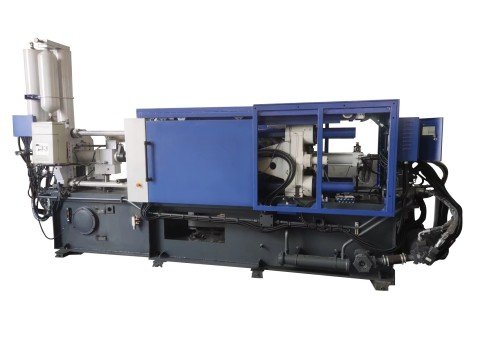
Density of Aluminum & Aluminum Alloys are closely related to their composition and process. Die casting technology further expands the application boundaries of aluminum alloys by optimizing material fluidity and molding efficiency. Choosing a professional equipment manufacturer can ensure the dual improvement of product quality and production efficiency.