Die casting machine ejector force is the force used by the die-casting machine to eject the formed casting from the die after the die-casting process is completed. Sometimes we also call die casting machine ejector force, ejector pressure.
This is the key force to ensure that the casting can be smoothly separated from the die for subsequent processing. In the precision manufacturing industry, the die-casting machine’s performance directly affects the product’s quality and production efficiency. The ejector force is one of the important parameters used to measure this performance.
How to calculate ejector force?
Ejector force calculation formula based on shape and pressure, as below:
F=S×L×P(μcosα−sinα)
- F is the ejection force
- S is the area of the shape to be ejected
- L is the ejection length
- P is the pressure of the die casting machine
- μ is the friction coefficient
- α is the slope angle
This parameter is directly related to whether the casting can be removed from the die without damage and enter the subsequent processing or packaging stage.
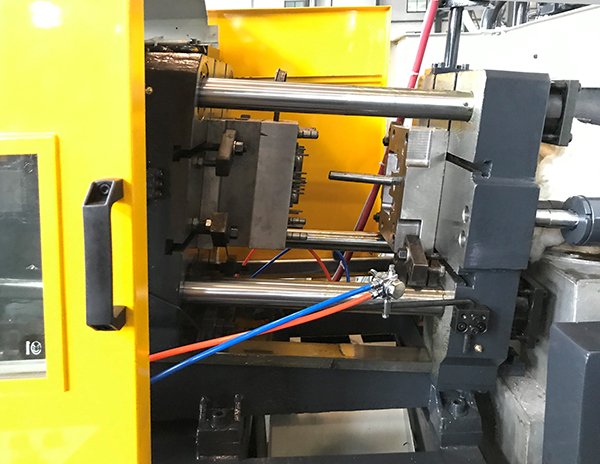
Appropriate ejector force can ensure the integrity and precision of the casting and avoid damage or deformation caused by improper demolding. In addition, the size of the ejector force will also affect production efficiency. Inappropriate ejector force may cause production interruptions and reduce the overall production process speed.
In order to achieve the best production results, manufacturers need to adjust the number, speed, and layout of ejectors of the die casting machine according to the material, size and shape of the casting, as well as the specific design of the mold. By accurately controlling the ejector force, the yield rate and production efficiency of the casting can be improved.
Factors affecting the ejector force of die casting machines
The technical parameters and specification selection standards of the ejector force of the die-casting machine are crucial to ensure the quality of die-casting parts, production efficiency, and the life of the mold. So what are the factors that affect the ejector force of the die-casting machine?
- Hydraulic system pressure
The ejection movement is achieved by pushing the piston through the pressure of the hydraulic oil in the ejector hydraulic cylinder, and then transmitted to the push rod plate by the piston rod. The pressure and flow of the hydraulic system directly affect the size of the ejector force.
- Ejector arrangement
The arrangement of the ejector should make the ejector force as balanced as possible. The ejection force required for complex structural parts is large, and the number of ejectors should be increased accordingly. Reasonable ejector arrangement can ensure the uniform distribution of the ejector force and avoid excessive or insufficient local force.
- Mold design
The design of the mold directly affects the balance and uniformity of the ejector force. The finish and slope of the mold surface will affect the size and distribution of the ejector force.
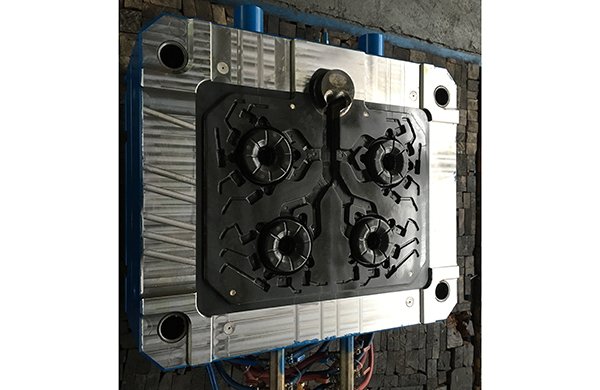
- Casting size and weight
The size and weight of the casting directly affect the required ejector force. Larger castings or heavier castings require greater ejector force to ensure smooth demolding.
- Casting shape and structure
The shape complexity and structural design of the casting, especially castings with deep cavities or narrow parts, may require higher ejector force.
- Alloy properties
The physical and chemical properties of different alloys will also affect the ejector force. For example, aluminum alloys have better fluidity, but changes in their strength and hardness will also affect the demand for ejector force.
Practical application of ejector force
After die casting is completed, the casting needs to be ejected from the mold. Ejector force plays a role in this process, ensuring that the casting can be smoothly and completely separated from the mold. If the ejector force is insufficient, the casting may break or deform during the demolding process. On the contrary, if the ejector force is too large, it may cause mold damage or increased wear. Therefore, the correct application of ejector force is essential to ensure product quality and production efficiency.
In the application of multi-cavity molds, evenly distributed ejector force helps to ensure that each casting can be demolded smoothly. And for castings with complex geometries or thin-walled parts, accurate calculation and adjustment of ejector force is the key to preventing product damage.
Correct understanding and application of ejector force can significantly improve product quality and production efficiency, reduce material waste, and extend the service life of the mold. When faced with complex casting designs, reasonable ejector force settings and mold design optimization are the key to ensuring smooth production.
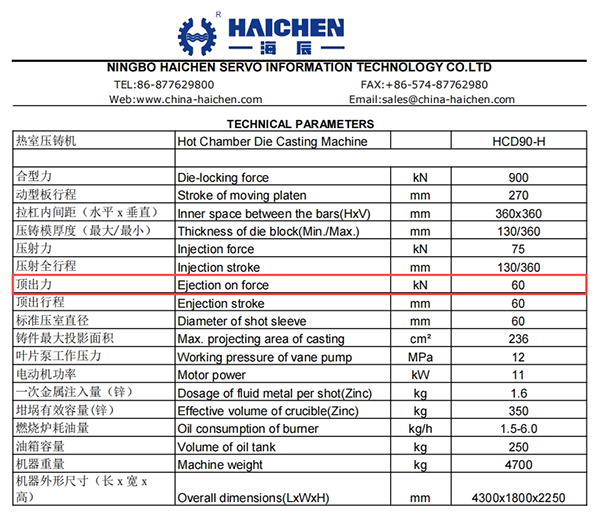
Haichen die casting machine
In the field of die casting, ejector force is one of the key factors to ensure product quality and production efficiency. Haichen die casting machine excels in ejector force control with its advanced technology and reliable performance. Through precise ejector force adjustment and optimization, Haichen die casting machine helps manufacturers effectively solve the challenge of demolding from complex castings, significantly improving production efficiency and product quality.
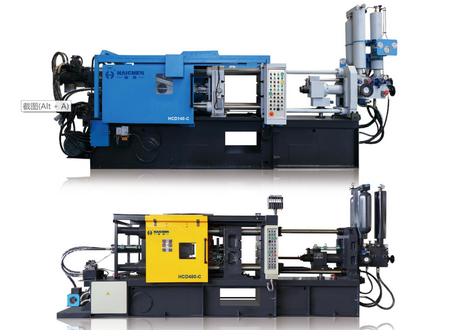
The intelligent control system of Haichen die casting machine can monitor ejector force in real time to ensure stability and consistency in the production process of various castings. Whether it is automotive parts, building hardware or electronic products, Haichen die casting machine can provide customized solutions to meet the needs of different customers.