Die casting materials include a variety of metals, each with its unique properties. The most commonly used materials in die casting include aluminum, magnesium, zinc, and copper alloys. These materials are chosen for their ability to be cast at high pressures and retain the fine details of the mold.Die Casting Materials and Properties, will be a little different with each other.
Die casting is a manufacturing process that involves the use of die casting materials to produce precision parts with high detail and strength. This method is widely recognized for its efficiency and versatility, allowing the creation of complex components with a high degree of repeatability. The characteristics of the die casting material are critical in determining the performance and quality of the final product.
Overview of Die Casting Materials
Die casting material – aluminum alloy
Aluminum alloy is one of the most commonly used materials in die casting, with the following characteristics:
Lightweight: The density of aluminum alloy is only about 1/3 of that of iron, copper, and zinc, which makes it very popular in applications that need to reduce weight, such as automotive parts and aerospace.
Good electrical and thermal conductivity: This makes aluminum alloy widely used in the electrical industry.
Excellent corrosion resistance: A dense oxide film is easily formed on the surface of aluminum, which can prevent further oxidation.
Good die-casting performance: The Aluminum alloy die-casting process is simple, forming and cutting performance is good, with high mechanical properties and corrosion resistance.
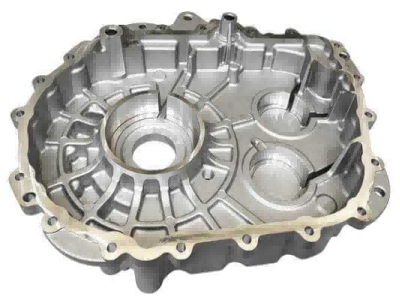
Application: Automobile engine parts, electronic equipment housing, etc.
Die casting material – Magnesium alloy
Magnesium alloy is known for its low density and high strength-to-weight ratio, and has the following characteristics:
Excellent electromagnetic shielding: suitable for electronic products to provide protection against electromagnetic radiation.
Good energy absorption and vibration absorption characteristics: help reduce noise transmission and extend the service life of parts.
Excellent machining performance: small cutting force required, good cutting effect, and long tool life.
Good heat dissipation: second only to aluminum alloy, suitable for parts that need heat dissipation.
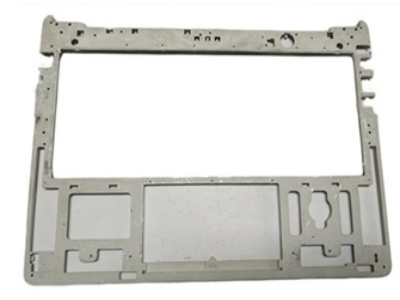
Application: laptop housing, mobile phone frame, etc.
Die casting material -Zinc alloy
Zinc alloy is favored for its high castability and low melting point, and has the following characteristics:
Low cost: The raw material price is low.
Good surface treatment: Suitable for electroplating and painting.
Wear resistance: Suitable for manufacturing wear-resistant parts such as gears and bearings.
Good castability: Suitable for die casting of complex shapes.
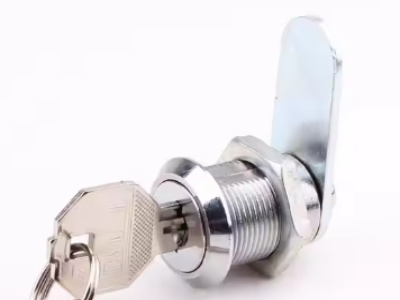
Application: Hardware products, toys, locks, etc.
Die casting material -Copper alloys
Copper alloys are less commonly used in die casting, but have the following properties:
High electrical conductivity: Suitable for manufacturing electrical and electronic components.
High thermal conductivity: Suitable for heat dissipation components.
Good corrosion resistance: Suitable for use in harsh environments.
High strength: Suitable for components that bear high loads.
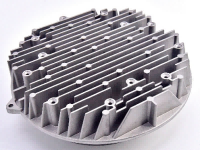
Applications: Electrical connectors, radiators, pumps and valves, etc.
Different material suit for different die casting machine
- Cold chamber die casting machine materials
Aluminum, magnesium
2. Hot chamber die casting machine materials:
zinc, and Lead
3. Cold chamber die casting machine with copper furnace
copper alloys
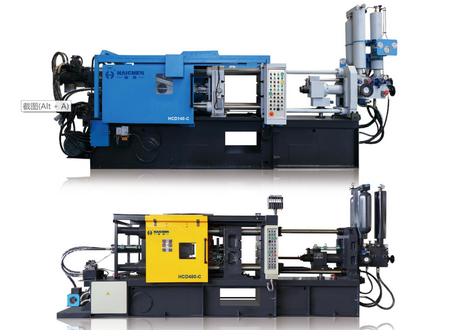
Conclusion
The choice of die casting materials depends on the specific requirements of the product, including factors such as mechanical properties, corrosion resistance, weight, and cost. Through the rational selection of materials, the die casting process can produce metal parts that are both economical and high-performance and are widely used in industries such as automobiles, aerospace, electronics, and consumer goods.
The choice of die-casting materials has a decisive influence on the final performance of the product. Understanding the characteristics of different materials can help designers and engineers make more reasonable decisions during the design and manufacturing process. With the development of new materials and the continuous advancement of die casting technology, the application areas of die casting materials will be further expanded, bringing more possibilities to all walks of life.