Die casting Mold Manufacturing Process involves precision machining and heat treatment to create durable molds for high-volume production.
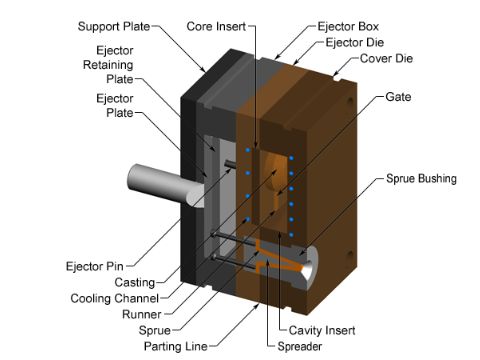
Die casting is a precision manufacturing process used to produce high-quality metal parts with complex geometries and tight tolerances. The heart of this process is the die casting mold, which is a critical component that determines the final shape, quality, and consistency of the cast parts.
This article will provide an in-depth look at the die casting mold manufacturing process, highlighting the key steps and considerations involved.
Die casting Mold Manufacturing Process
1. Design and Engineering
1.1 Design Concept
The first step in manufacturing a die casting mold is to develop a detailed design concept. Engineers develop 3D CAD models of production parts, incorporating precise dimensions (±0.1mm tolerances), surface finishes (Ra 0.8-3.2μm), and functional requirements. The design must also consider factors such as draft angles, parting lines, and gating systems to ensure smooth ejection and filling of the mold.
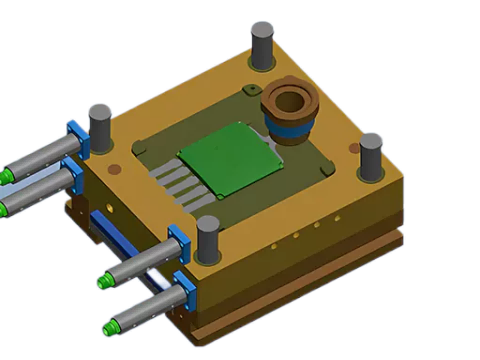
1.2 Simulation and Analysis
Engineers first simulate mold designs using software like Moldflow to detect air pockets, short shots, and warpage risks before cutting steel, enabling virtual corrections. Simulation can save time and reduce costs by minimizing the need for physical prototypes.
2. Material Selection
2.1 Mold Steel
The material used for the mold is crucial for its durability and performance. Mold makers prefer H13/S7 tool steel for its exceptional hardness (50-54 HRC), superior wear resistance (3x lifespan vs. standard steel), and thermal stability up to 600°C. The choice of steel depends on the specific requirements of the part and the production volume.
2.2 Surface Treatment
Surface engineering specialists apply nitriding or hard chrome plating to critical mold components, boosting service life by 300% and reducing downtime. These treatments improve the mold’s resistance to wear and corrosion, ensuring consistent part quality over a longer production run.
3. Machining and Assembly
3.1 CNC Machining
Toolmakers machine mold components on 5-axis CNC equipment, achieving ±0.002mm positioning accuracy for critical surfaces. These machines can achieve the tight tolerances required for die casting molds, ensuring that the final mold matches the design specifications. Toolmakers machine the cavity and core as separate components on 5-axis CNC mills before assembling them with 0.01mm alignment precision.
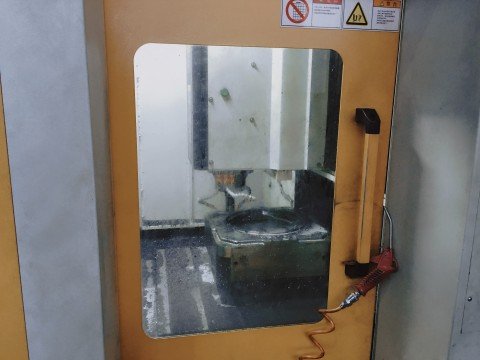
3.2 EDM (Electrical Discharge Machining)
For intricate details and tight tolerances, EDM is often used. This process involves using electrical discharges to erode material from the mold, allowing for the creation of complex shapes and fine details that are difficult to achieve with traditional machining methods.
3.3 Assembly and Fitting
Once all the components are machined, they are assembled to form the complete mold. This involves precise fitting and alignment to ensure that the mold halves come together perfectly, preventing any flash or parting line issues. The assembled mold is then tested to ensure it functions correctly.
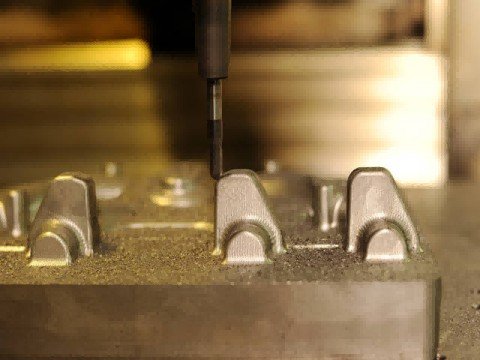
4. Testing and Validation
4.1 Initial Testing
The mold undergoes initial testing to ensure it operates correctly and produces parts that meet the design specifications. This involves injecting molten metal into the mold and inspecting the resulting cast parts for defects, dimensional accuracy, and surface finish.
4.2 Quality Control
Quality control is a critical step in the mold manufacturing process. Quality inspectors employ three verification methods: coordinate measuring machines (CMM) for ±0.01mm dimensional checks, white light scanners for 0.1μm surface analysis, and sectioning tests for internal integrity validation. The tooling team then implements corrective adjustments to the mold.
5. Maintenance and Upgrades
5.1 Regular Maintenance
To ensure the mold continues to produce high-quality parts, regular maintenance is essential. This includes cleaning, inspection, and lubrication of the mold components. Maintenance technicians immediately repair worn or damaged mold components, preventing casting defects in production.
5.2 Upgrades and Repairs
Over time, the mold may require upgrades or repairs to maintain its performance. This can include replacing worn components, reconditioning surfaces, or even modifying the mold to accommodate design changes in the part.
HAICHEN: Your Partner in Die Casting Solutions
At HAICHEN, we specialize in manufacturing advanced die casting machines designed to meet the highest standards of precision and reliability. Our machines are engineered to work seamlessly with high-quality die casting molds, ensuring consistent production quality and efficiency. Whether you are producing automotive parts, aerospace components, or other high-precision products, HAICHEN offers the tools and expertise to help you achieve your production goals.
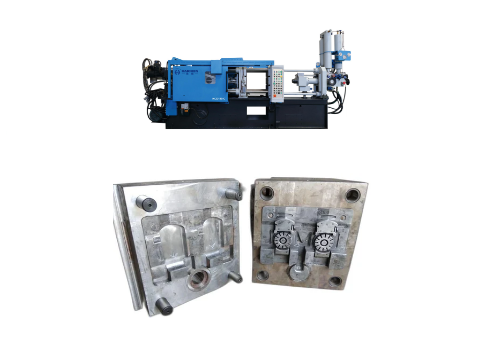
Why Choose HAICHEN?
- Advanced Technology: Our die casting machines are equipped with state-of-the-art control systems and precision components to ensure high-quality production.
- Custom Solutions: We offer tailored machine configurations to meet specific production needs, including mold size, material type, and production volume.
- Quality and Reliability: HAICHEN machines are built to the highest standards of quality and reliability, ensuring consistent performance and minimal downtime.
- Comprehensive Support: Our commitment to customer satisfaction includes comprehensive after-sales support, technical assistance, and maintenance services.
The die casting mold manufacturing process is a complex and critical part of the die casting industry. From design and engineering to machining, assembly, testing, and maintenance, each step plays a vital role in ensuring the production of high-quality, consistent cast parts.