Die casting machine Robot Applications is an upgrading application for the metal working industry.
Especially in the automation of die casting machines.
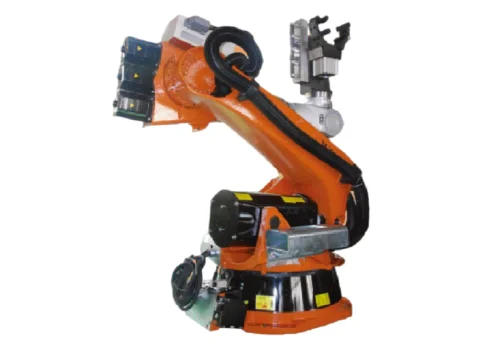
Here are a few different robotics applications for die casting machines:
1.Material handling
2. Mould lubrication
3. Removal of excess metal
4. Castings extraction and handling
5. Non-destructive quality inspection
6.Environmental safety and energy saving
1. material handling:
Robots can handle the pouring and cooling of molten metal during the die casting process.
Robots can perform pouring operations in a stable manner, reducing spillage or turbulence problems caused by unstable manual handling.
In addition, robots can be used to load and unload die casting moulds, ensuring that the mould remains stable during the cooling process.
2. Mould lubrication:
Robots can do spray mould release agents to ensure consistent lubrication of the mould surface.
Improve the quality of castings and the service life of the mould.
3. Excess metal removal:
After the die casting is complete, the robot can be used to remove unwanted excess such as gates, flying edges and risers.
This step is critical to improving the accuracy of the casting and the efficiency of subsequent processing.
4. casting extraction and handling:
The robot can automatically extract the die casting and place it into a quench tank for further cooling.
The robot can then place the casting in a trimmer in order to remove excess metal parts.
5. Non-destructive quality inspection:
Robots can also be used to perform non-destructive quality inspection by integrating optical scanners or specific sensors to detect defects on the surface of the casting and the internal structure.
This improves product quality and productivity.
6. Environmental safety and energy saving:
The use of robots can significantly reduce the environmental risks of the casting process, such as high temperatures, dust and harmful gases.
The ability of robots to work in extreme environments reduces the health risks to operators and, due to their high precision and stability, effectively reduces energy consumption and waste generation.
These applications demonstrate the diverse functions of robots in the die-casting industry, which not only improve production efficiency and product quality, but also enhance operational safety and environmental protection.
By introducing robotics, die casting companies are better able to cope with complex production demands and maintain an edge in a competitive market.
Robot application of material handling in die casting machines
The application of robot in die casting machine is mainly reflected in the handling of raw materials and the automation of die casting process.
In the die casting process, the robot is responsible for quantitatively scooping the molten metal liquid from the holding furnace.
And pour into the die casting machine’s pressure injection chamber, so as to achieve efficient and accurate die casting moulding.
This automated operation not only improves production efficiency, but also reduces human intervention, lowering production costs and the risk of human error.
Specifically, the application of robots in the raw material handling process includes two aspects:
1. Loading and unloading
2. Handling molten metal
1. loading and unloading:
The robot is responsible for placing the raw material metal blocks into the die casting machine furnace for melting.
This process involves extracting solid blocks of raw metal and placing them sequentially into the metal melting furnace.
The speed is controlled to match the required throughput of the die-cast product cycle.
2. Handling molten metal:
Robot can automatically extract the metal solution from the furnace and pour it into the die casting machine’s injection chamber for die casting moulding.
This process requires precise control of the temperature and flow of the aluminium liquid to ensure product quality.
The application of manipulator in die casting machine is an important part of modern die casting process, it improves the production efficiency, reduces the production cost and improves the working environment through automation and intelligent means.
Application of robots in lubricating die casting machine moulds
The special model of the robot in lubricating die casting machine moulds is called sprayer.
Its application is mainly reflected in the improvement of production efficiency, reduce human error and improve product quality and so on.
The following is the detailed application:
1. Improve the uniformity and consistency of lubricant spraying:
2. Automation and flexibility
3. Safety and environmental improvement
4. Cost savings and efficiency improvements
5. Intelligent and digital
1. Improve the uniformity and consistency of lubricant spraying:
In the die casting process, the surface of the mould needs to be sprayed with a layer of lubricant to ensure the casting of smooth demoulding and cooling.
Robots are able to spray the lubricant accurately according to a preset path, avoiding errors in manual operation, thus improving the effect of mould lubrication and the quality of castings.
2. Automation and flexibility:
The application of robots in mould lubrication is not limited to spraying, but also includes tasks such as positioning, cleaning and maintenance of the mould.
Automation of these tasks can significantly reduce cycle times, increase productivity and reduce error rates due to human error.
Robots can adapt to the production of diverse die-casting products, through programming to select different spraying position and trajectory to meet the needs of different moulds.
3. Safety and environmental improvement:
Robots work in high temperature, high dust die-casting environment, can effectively avoid workers long time exposure to harmful substances, so as to improve the safety of the working environment.
At the same time, the robots are able to handle complex mould surface treatment tasks, such as removing flying edges and burrs, further improving product quality.
4. Cost savings and efficiency improvements:
The use of robots for mould lubrication can result in significant labour cost savings.
Traditional manual spraying requires a large amount of manpower investment, while the robot can complete the spraying task in a short period of time, reducing the maintenance time and logistics transfer costs.
5. Intelligent and digital:
With the digital and intelligent development of die casting industry, the application of robot technology in die casting process is also deepening.
For example, through the integration of sensors and control systems, the robot can real-time monitoring of the mould temperature, and according to the temperature difference automatically adjust the spraying trajectory and time, in order to ensure the best lubrication effect.
Robots have demonstrated significant advantages in the application of lubricating die casting machine moulds, including increased productivity, reduced human error, improved product quality, improved workplace safety and cost savings.
These advantages make robots an integral part of modern die casting production.
Robots applications in die casting machine extraction and handling
In the die casting industry applications, robots have expanded from simple pouring and handling to multiple aspects of casting extraction, cleaning and handling.
These applications not only increase the production efficiency, but also improve the working environment and product quality.
Haichen The various applications for the new die casting machine robots are in six areas:
1.Casting cleaning
2. Castings grinding
3. Castings handling and palletising
4. Intelligent casting system
5. Applications in harsh environments
6.Castings cutting and grinding planning
1.Castings cleaning (Fettling) :
Castings often produce flying edges or burrs during the casting process, and these need to be removed by cleaning.
Robots can be used as a positioning tool, using visual feedback technology for casting cleaning, to ensure the safety and consistency of the cleaning process.
For example, robots can use rotary cut-off saws or abrasive belt sanders to deal with fretting and burrs on castings.
2. Castings grinding:
Surface treatment of castings is an important part of improving product quality.
Robot combined with vision detection technology can automatically identify the casting position information.
And according to the three-dimensional model for grinding trajectory adjustment, so as to ensure the consistency and accuracy of the casting surface after grinding.
3. Castings handling and palletising:
The application of robots in the casting production line has been extended to the handling and palletising of castings.
Through the multi-station robot system, it can realise the whole process automation of casting from pouring to cooling to picking up.
Thus improving production efficiency and product quality.
4. Intelligent casting system:
Intelligent casting system based on industrial robots can achieve the cooperative work of multiple equipment.
Such as hydraulic machines, industrial robots and casting machine joint control, so as to achieve fully automated casting production.
5. Applications in harsh environments:
The foundry industry is usually faced with high temperatures, high dust and other harsh environments, which puts forward higher requirements for the application of robots.
Haichen optimises the structure of the robot to make it operate stably in harsh environments and promote the development of casting automation.
6. Castings cutting and grinding planning:
For castings with complex shapes, the robot can use point cloud information for cutting and grinding planning.
Improve the level of automation in the manufacturing process and adaptability to the workpiece.
Haichen’s latest die-casting robotics applications not only improve production efficiency and product quality.
It also improves workers’ labour conditions and promotes the modernisation and intelligent development of the foundry industry.