The ejector space of the die casting machine is the distance that the die-casting ejector moves during the ejection process. That is, the distance between the end face of the die-casting ejector and the working surface of the fixed template.
The ejector space of the die casting machine is an important parameter to ensure the integrity of the die casting and to avoid the product is stuck in the mold cavity.
The ejector pitch varies depending on the model and design but is typically between tens of millimeters and hundreds of millimeters.
Choosing the right injection head push-out distance needs to consider factors such as the thickness of the mold, the size of the die casting, and the material characteristics to ensure that the die casting process goes smoothly and gets a high-quality casting.
Technical differences between cold chamber and hot chamber die casting machine in the injection head launch distance
The technical differences between cold chamber die casting machines and hot chamber die casting machines of different manufacturers in the injection head launch distance are mainly reflected in the following aspects:
Design of injection mechanism:
Hot Chamber Die Casting Machine: The injection mechanism of the hot chamber die casting machine is usually closely connected to the furnace, and the injection punch and the pressure chamber are immersed in the molten metal, which makes the injection motion move up and down.
Since the injection punch is immersed in liquid metal for a long time and there is no cooling device, this may affect the service life and easily increase the iron content of the alloy.
Cold chamber die casting machine: The injection chamber and injection punch of the cold chamber die casting machine are not immersed in the molten metal, but a quantitative amount of molten metal is poured into the injection chamber and then shot.
This design makes the injection method of the cold chamber die casting machine more flexible, and the push-out distance of the injection head can be adjusted as required.
Injection speed and accuracy: Hot chamber die casting machine: Since the injection punch of the hot chamber die casting machine is immersed in liquid metal for a long time, its injection speed and accuracy may be affected to a certain extent.
In order to reduce the pressure loss caused by friction and turbulence of liquid metal during the flow process, hot chamber die casting machines often need to set a slower injection speed.
Cold Chamber Die Casting Machine: The injection speed and accuracy of the cold chamber die casting machine are relatively high because its injection punch is not immersed in the molten metal, which allows for more precise control of the injection process.
Applicable Materials: Hot Chamber Die Casting Machine: Due to the design of its injection mechanism, the hot chamber die casting machine is mainly used for the production of low melting point alloys such as zinc alloy and magnesium alloy. These materials have a low melting point and are suitable for injection at high temperatures.
Cold Chamber Die Casting Machine: Cold chamber die casting machine is suitable for a wider range of material types, including some high melting point alloys, because its injection mechanism is designed to allow for better control of temperature and pressure.
The technical differences between cold chamber die casting machines and hot chamber die casting machines from different manufacturers in the push out distance of the injection head are mainly reflected in the design of the injection mechanism, the injection speed and accuracy, and the applicable materials.
How to choose the right cold chamber or hot chamber die casting machine’s ejector space according to the material and size of the die casting
Choosing the right cold chamber or hot chamber die casting machine’s injection head push out distance is mainly based on the material and size of the die casting.
In actual production, the choice of die casting machine is mainly based on the type of die casting alloy, the contour size and weight of the casting to decide whether to use a hot chamber die casting machine or a cold chamber die casting machine.
For zinc alloy castings and small magnesium alloy castings, hot chamber die casting machines are usually used.
For aluminum alloys, copper alloy castings and large magnesium alloy castings, cold chamber die casting machines are preferred.
It is further explained how to determine the distance at which the punch is pushed, i.e. by the thickness of the die fixation.
This means that the ejector space of the injection head needs to match the thickness of the mold to ensure that the die casting can be pushed out properly.
Specific parameter settings are provided, including injection pressure, boost pressure, slow injection stroke, fast injection stroke, punch follow-out distance, push-out stroke, push-out reset time, etc., which are all factors to consider when designing and adjusting the die casting process.
After adjustment, soft objects such as cotton silk should be placed in the pressure chamber, and the whole process of injection should be simulated twice to check whether the adjustment is appropriate.
Choosing the right cold chamber or hot chamber die casting machine’s injection head push out distance needs to be decided according to the material (such as zinc alloy, aluminum alloy, etc.) and size (such as mold thickness, casting profile size and weight) of the die casting.
Effect of the injection head push-out distance on the operational efficiency of cold and hot chamber die casting machines.
The ejector pitch distance has a significant impact on the operational efficiency of cold and hot chamber die casting machines.
First and foremost, adjusting the ejector space of the injection head is essential to ensure that the casting can be easily removed and to avoid the use of vibration pick-up, which helps to reduce cake breakage and seizure.
Secondly, the injection punch needs to have enough push-out distance, otherwise it is easy to cause the cake to get stuck in the mold when opening the mold, which will affect the operation efficiency.
In addition, the adjustment of the ejector ejector space involves spraying the ejector for cooling and lubrication, which helps to improve operational efficiency.
How to adjust the ejector space in cold and hot chamber die casting machines to optimize the production process
In practice, adjusting the ejector space of the injection head of the cold and hot chamber die casting machines to optimize the production process is mainly based on the adjustment steps after the mold is installed.
According to the adjustment, the injection parameters include fast injection speed, injection pressure, boost pressure, slow injection stroke, fast injection stroke, punch follow-out distance, push-out stroke, push-out reset time, etc.
Specific to the adjustment of the ejector pushing distance, it is mentioned that the structure of the injection cylinder is optimized to improve the continuous stability of the injection coaxiality and effectively control the ejector pushing distance.
This means that when adjusting the ejector space of the injection head, it is necessary to ensure that the injection cylinder structure is optimized to maintain the stability of the injection coaxiality and thus achieve precise ejector space control.
Adjusting the ejector space of the injection head of the cold chamber and hot chamber die casting machines to optimize the production process requires detailed parameter adjustments after the mold is installed, including but not limited to fast injection speed, injection pressure, boost pressure, slow injection stroke, fast injection stroke, punch follow-out distance, push-out stroke, push-out reset time, etc.
The ejector space of the Haichen die casting machine
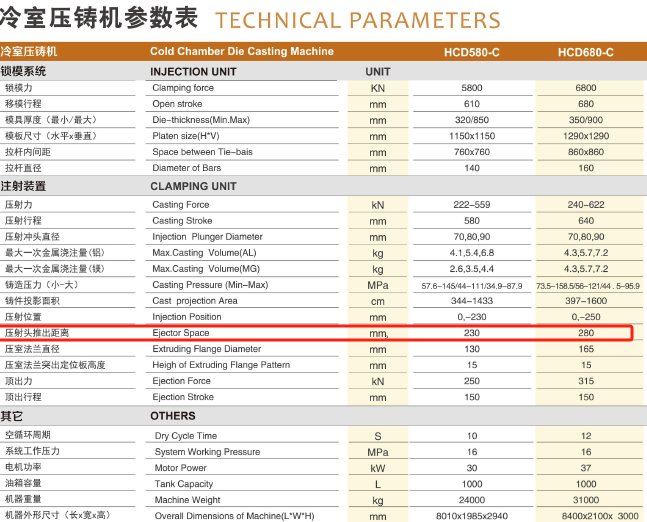
Haichen’s space adjustment in the mold design of the die-casting machine: the cushion block is between the moving mold base plate and the supporting plate, forming an activity space for the work of the push-out mechanism.
For small die-casting molds, the thickness of the spacer is also used to adjust the total thickness of the mold to meet the requirements of the minimum clamping distance of the die-casting machine.
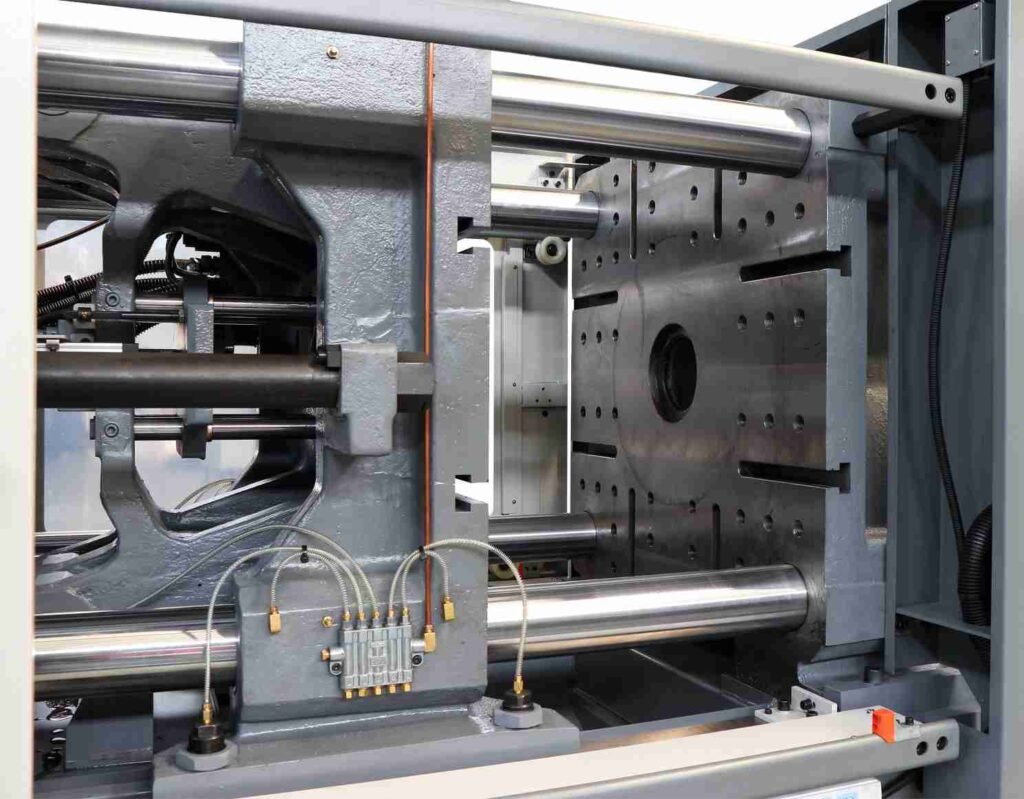
Optimize process conditions: For more complex casting geometries, Haichen uses a complete model to analyze parameters such as wait time and punch speed to optimize process conditions.
Mold space design: Haichen die-casting machine adopts a larger mold space design, which can reduce the opportunity of flying materials, avoid material waste, and save production costs for customers.
If you need any help from Haichen in terms of die casting machine, please feel free to contact us.