Die Casting Trends and Technologies,die casting is a precision manufacturing process.
In which molten metal is injected into steel molds under high pressure to produce metal parts with high precision and smooth surfaces.
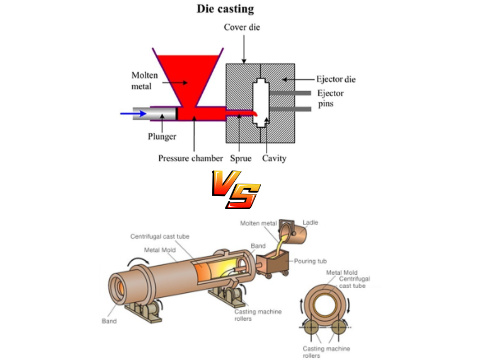
Die Casting Industry & Market
Due to its high efficiency, cost advantage and scalability, die casting technology has become a core process in automotive (60% of die casting applications), electronics, aerospace and consumer goods.
The global die casting market is expected to grow from $65.68 billion in 2023 to $103.65 billion in 2032, at a compound annual growth rate of 5.2%.
Automotive lightweighting demand
The surge in demand for lightweight, high-strength components for electric vehicles (EVs) and gasoline vehicles is driving the use of aluminum and magnesium alloy die casting.
Expansion of consumer electronics
The demand for precision structural parts such as smartphones and AI devices is accelerating the development of die casting technology towards miniaturization and high complexity.
Regional industrial upgrading
Asia-Pacific (especially China and India) dominates investment in aluminum production and manufacturing.
While Europe (e.g., Germany) strengthens its high-end market position through technological innovation.
Die-casting technology innovation and material revolution
Die Casting Trends and Technologies
Robotics
Fully automated in the process of spraying release agents, picking, deburring, etc.
For example, ABB’s IRB6660 robots are applied to heavy-duty truck press lines, improving efficiency by more than 30 percent.
AI & Machine Learning
By monitoring pressure, temperature and other parameters in real time, the mold filling speed is dynamically adjusted to reduce porosity defects (the defect rate is reduced by 15-20%).
Predictive maintenance
Build fault models based on historical data to warn of equipment anomalies in advance and reduce downtime (25% reduction in maintenance costs).
Industrial Internet of Things (IIoT)
Integrate sensors and cloud platforms (such as Yi CMS/MES system) to digitize the entire production process and optimize resource scheduling and energy consumption management.
Sustainable technological innovation
Closed-loop recycling system
95% of scrap aluminum is recycled, and the proportion of recycled aluminum in automotive die castings has increased to more than 40%, reducing carbon emissions by 30%.
Energy-efficient processes
StrikoWestofen’s melting furnace technology reduces energy consumption by 20% through waste heat recovery.
And water-based paints reduce VOCs emissions by replacing traditional electroplating.
Extended mold life
3D printing conformal cooling channel technology improves mold cooling efficiency by 50%.
And increases mold life from 100,000 times to 500,000 times with new hot work steels (such as ESU-EM213 and Anco-T).
Material revolution
Aluminum alloy
With its high strength-to-weight ratio and corrosion resistance.
It has become the first choice for automotive engine parts and battery pack structural parts.
Tesla’s integrated die-casting technology realizes the one-time molding of the rear floor through a die-casting machine of more than 6000T, reducing the number of parts and improving the rigidity of the body.
Magnesium alloy
As the lightest structural metal (density 1.8g/cm³), it is used in aerospace turbine blades and high-end consumer electronics housings, and its electromagnetic shielding performance and recyclability have attracted much attention.
Zinc alloy
High fluidity and surface finish make it irreplaceable in precision electronic connectors and trims.
And its low melting point characteristics (about 385°C) reduce energy consumption and extend mold life.
Application of 3D printing in Die Casting Trends and Technologies
Complex structure manufacturing
The special-shaped cooling channel (such as spiral and multi-layer structure) that is difficult to achieve in traditional processing is realized by metal 3D printing (SLM technology), which improves the uniformity of mold temperature distribution by 60%.
ESU-EM213
Die steel powder specially designed for die casting, with 3 times higher thermal crack resistance than H13 steel, suitable for 600°C high temperature environment.
Anco-T
High toughness (impact toughness ≥20J/cm²) and aluminum melt resistance to solve the cracking problem of traditional materials in high-pressure die casting.
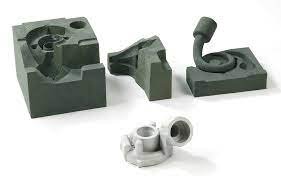
Die casting application examples
Tesla uses the X Line 2000R 3D printer to produce 800mm-class large-scale molds, shortening the development cycle by 70%.
In 2015, Audi demonstrated 3D printed die-casting molds for key components.
Such as engine blocks to achieve a balance between weight and strength.
Challenges and coping strategies of die-casting
Ultra-large die-casting equipment
The R&D and maintenance costs of die-casting machines above 6000T are high (the investment of a single equipment exceeds 150 million yuan).
And it is necessary to cooperate with equipment manufacturers (such as LK Group) to carry out technical research.
Development of heat-free alloy
By optimizing the composition of aluminum-silicon alloy (such as adding Sr and rare earth elements).
The tensile strength of the casting can be ≥300MPa and the elongation ≥ 10% without heat treatment.
Economic and supply chain risks
Raw material fluctuations
Aluminum and magnesium prices are significantly affected by geopolitics (e.g., magnesium prices will fluctuate by ±20% in 2024).
And risks need to be mitigated through long-term contracts and futures hedging.
High investment in molds
The weight of the integrated die-casting mold is more than 100 tons, the design cycle is as long as 6-8 months.
And the modular design and quick mold change technology (SMED) are used to improve the utilization rate.
The development of integrated die-casting technology
The integrated die-casting technology dies casting the dispersed alloy into large-scale alloy parts through a large-tonnage die-casting machine.
Which has the advantages of high efficiency, simplified process and cost saving.
The rapid development of the new energy vehicle market has promoted the application of integrated die-casting technology.
Especially in automotive lightweight, and aluminum-magnesium alloy has become the mainstream customer of integrated die-casting technology.
The application prospect of integrated die-casting technology in the field of automotive lightweight is broad.
And more attention will be paid to taking into account static load strength, coating performance, process performance, fatigue life, corrosion resistance and recyclability in the future.
Future Trends
In the future, die-casting technology will continue to develop in the direction of intelligence and automation.
With the continuous application of big data, cloud computing, artificial intelligence and other technologies, the die-casting production line will achieve a higher degree of intelligence.
For example, intelligent systems will have predictive maintenance capabilities that can identify and resolve potential problems before they occur, reducing downtime and maintenance costs.
The role of industry standards in promoting the development of die casting technology
Technical specifications and quality improvement
Industry standards provide clear technical requirements and operating specifications for die casting technology to ensure product quality and production efficiency.
For example, the “Technical Conditions for Die Casting Unit” standard regulates the technical requirements of die casting machines and their auxiliary equipment.
And improves the safety performance and production efficiency of equipment.
In addition, the standard covers the dimensional stability and surface quality of die castings, reducing defects and improving product consistency.
Technological innovation and industrial upgrading
Industry standards have promoted the innovation and industrial upgrading of die casting technology.
For example, Ningbo City has formulated an implementation plan for the improvement of the standards of the die-casting industry.
Encouraged enterprises to carry out technological transformation and intelligent transformation.
And promoted the development of the die casting trends and technologies in the direction of large-scale, precision, functionalization and greening.
At the same time, the formulation and revision of standards have also promoted the innovation of die-casting materials and processes.
Such as the “General Principles of Manufacturing Process for Green Products of Aluminum Alloy Die-casting”.
Which has promoted the green manufacturing transformation of the die-casting industry.
International Competitiveness and Market Expansion
Industry standards have enhanced the international competitiveness of China’s die casting technology.
By participating in international standardization activities, LK Group and other enterprises have promoted the internationalization of China’s die-casting standards and enhanced China’s influence in the international market.
This will not only help domestic enterprises better participate in international trade.
But also promote the integration of domestic technology with the international advanced level.
Coordinated development of the industrial chain
Industry standards promote the coordinated development of the upstream and downstream industrial chains.
For example, Beilun Industrial Community and Mold Industry Association jointly formulated die-casting mold industry standards.
Which promoted the standardization and standardized development of the mold industry.
In addition, the formulation of standards has also led to the research and development of related equipment and technologies,
Such as the “Die Casting Machine Clamping Force Test Method” standard guides the development and use of die casting machines.
Environmental protection and sustainable development
Industry standards promote environmental protection and sustainable development in the die casting industry.
For example, the “Safety Technical Requirements for Aluminum Alloy Zinc Alloy Die Casting Production” standard regulates the environmental protection requirements of die casting production and promotes the development of a low-carbon economy.
At the same time, the application of integrated die-casting technology is also in line with the national goals of “carbon peak” and “carbon neutrality”.
Policy support and industry norms
The government has provided policy support and technical guidance for the die casting industry by formulating and revising industry standards.
For example, the revision of the Standardization Law of the People’s Republic of China has supplemented the standard system in the field of foundry and provided strong technical support for the development of the foundry industry.