Features of the Boosting Handwheel in Die Casting include adjusting the pressure by rotation (tightening for boosting, loosening for reducing), adjusting the pressure building time, adjusting the flow rate to suit castings with different wall thicknesses, and preventing mold damage caused by overpressure.
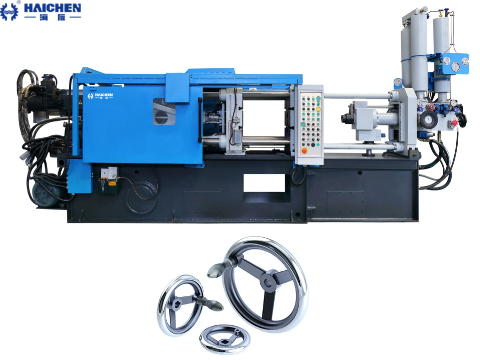
Features of Boosting Handwheel in Die Casting
- Precision Control and Enhanced Resolution
The dual transmission system (gearbox and gear assembly) amplifies the handwheel’s operational stroke, significantly improving manual feed resolution. This design allows operators to fine-tune the boosting process, enhancing the dimensional accuracy of die-cast components. - Effort-Saving Operation and Safety
The gearbox’s ratio reduces the force required to rotate the handwheel, enabling ergonomic operation. The system integrates a safety lock mechanism to prevent accidental handwheel rotation during automatic boosting modes, ensuring production safety. - Self-Adaptive Pressure Parameter Adjustment
The boosting handwheel adjusts flow rates dynamically based on casting wall thickness: thicker walls require smaller boosting flow rates, while thinner walls need higher flow rates for rapid filling. Operators must precisely control boosting time—for instance, certain die-casting machines achieve pressure buildup in ≤20ms, minimizing internal defects caused by delays. - Balanced Pressure-Time Control
Operators should avoid blindly increasing boosting pressure. Instead, the handwheel allows precise adjustment of pressure buildup time. Excessive pressure increases flash formation and shortens mold longevity. By combining the handwheel with the gearbox, the system optimizes the pressure-time balance, ensuring efficient boosting while protecting the mold.

In summary, the boosting handwheel delivers high-precision, low-effort manual control. Its safety mechanisms, adaptive flow adjustments, and time-pressure optimization guarantee stable processes and high-quality castings.
How to operate the Boosting Handwheel in Die Casting
The intensification Boosting handwheel controls boost speed adjustment and pressure settings (depending on the machine type). Below is a detailed guide:
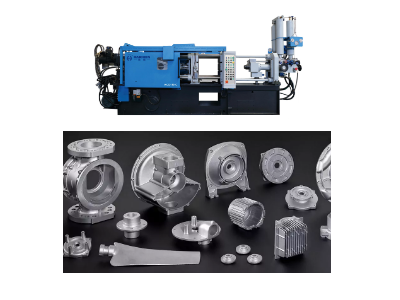
1. Core Functions of the Intensification Handwheel
- Adjusting Boost Speed
The handwheel regulates the oil flow rate to the intensification cylinder, affecting the speed of the intensification phase.- Clockwise rotation (turning outward) typically increases speed.
- Counterclockwise rotation (turning inward) decreases speed.
- Example reference values:
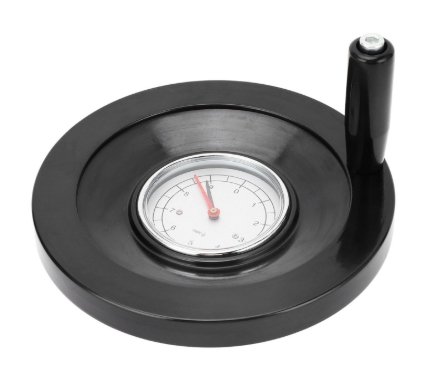
- For a 300-ton die casting machine:
- 2 turns → ~0.5 m/s
- 4 turns → ~2 m/s
- 6 turns → ~6.5 m/s (speed plateaus beyond this range).
- Pressure Setting (Specific Models)
For machines with pressure-setting capabilities (e.g., SMC VBA series boost valves):- Initial setup: Pull the handwheel outward while supplying air, rotate in the “+” direction (as indicated by arrows), then push it back.
- Caution: Do not exceed the rotation limits to avoid damaging internal components.
2. Operational Steps and Precautions
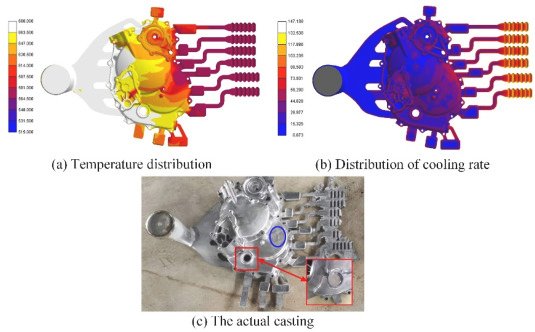
- Basic Workflow
- Step 1 (Speed adjustment): Rotate the handwheel on the valve block.
- Clockwise = faster speed (outward).
- Counterclockwise = slower speed (inward).
- Step 2 (Pressure-setting models):
- If overflow occurs during air supply, pull the handwheel outward and rotate to set pressure.
- Push the handwheel back after adjustment.
- Step 3: Verify adjustments using pressure gauges (e.g., check injection cylinder pressure). Adjust accumulator pressure if discrepancies exist.
- Key Precautions
- Rotation direction: Ensure clockwise/counterclockwise matches the machine’s design (some models only adjust speed, not pressure).
- Avoid over-rotation: Exceeding limits may damage valve cores or pistons.
- Process compatibility: Adjust based on casting thickness, mold temperature, etc. (e.g., thin-walled parts require faster boost speeds).
3. Contradictions and Clarifications
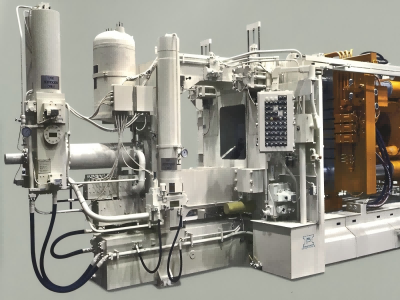
- Function differences: Some manuals describe the handwheel as a speed controller, others as a pressure adjuster. This depends on the machine model. Always refer to the specific equipment manual.
- Modern upgrades: Advanced machines use digital shot profiles for precision, but manual handwheel adjustment remains foundational.
4. Summary and Recommendations
- Traditional mechanical machines: Focus on speed adjustment via Boosting handwheel rotation.
- Pressure-setting models: Follow the pull-rotate-push sequence and validate with pressure gauges.
- Critical reminder: Always follow the equipment manual to avoid mechanical failures or casting defects.
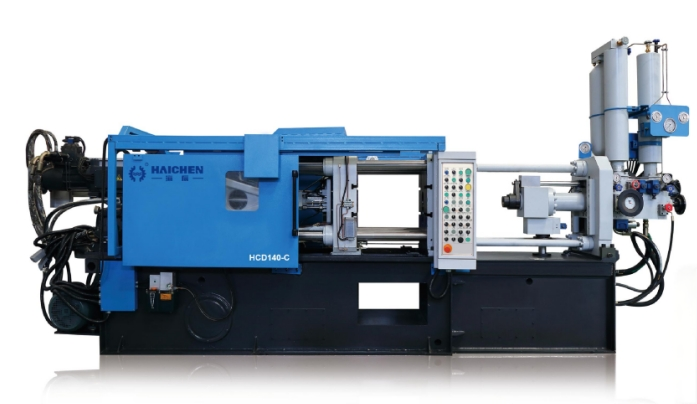
Come to contact Haichen, we will give you more technical knowledge of die casting machines.