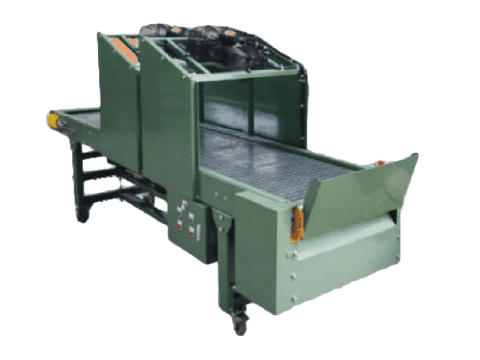
The die casting conveyor is an important part of the die casting machine, which is used to realize automation and intelligence and reduce labor costs. It can run intermittently or continuously, transport granular materials and finished products, and form a production line.
The main functions of die casting conveyors include automated transportation of castings, integration into production lines, support for continuous processing, improved efficiency, and involve a variety of types and structural designs.
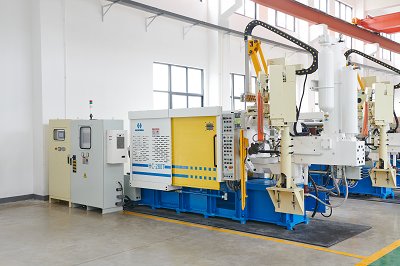
The design of high-temperature die casting conveyor systems must integrate factors such as high-temperature alloy properties, mold material selection, temperature control, and process optimization. Below is an evidence-based analysis and proposed solution:
1. Metal Transfer & Injection System
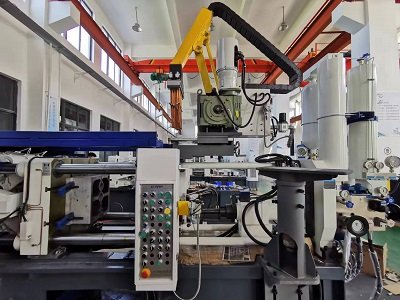
- Automated Transfer Technology: Early studies used vacuum lifting devices (e.g., vacuum suction systems) for molten metal transfer, but heat resistance of equipment at high temperatures must be prioritized. Modern solutions combine induction heating or composite sleeves (e.g., ceramic-based Al₂O₃ sleeves) to maintain metal fluidity.
- Injection System Design:
- High-pressure injection is employed, with speeds of 30–40 m/s to rapidly fill molds.
- Optimize pressure distribution to minimize porosity (e.g., increasing gate thickness and vent design to reduce gas entrapment).
2. Mold Materials & Structure
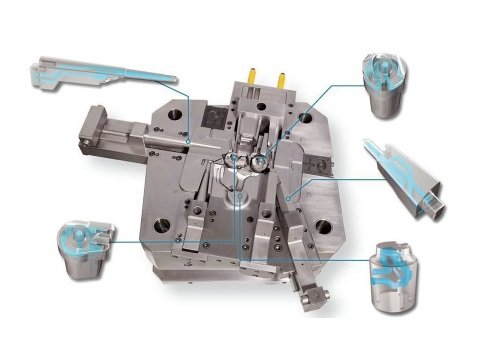
- High-Temperature-Resistant Materials:
- Molybdenum-based alloys (TZM): Ideal for iron-based alloys due to high melting points and thermal fatigue resistance.
- Nickel-based alloys (INCONEL 617/625): Suitable for copper alloys, extending mold lifespan.
- Advanced Tool Steels: Cr/Ni/W-alloyed steels with high thermal conductivity for large-section molds.
- Composite Structure: Stainless steel shells (e.g., AISI 304) paired with refractory metal liners to balance thermal expansion and oxidation resistance.
- Cooling & Insulation: Integrated water or oil-cooling channels and thermal barriers to manage heat stress and prevent overheating.
3. Temperature Control & Monitoring
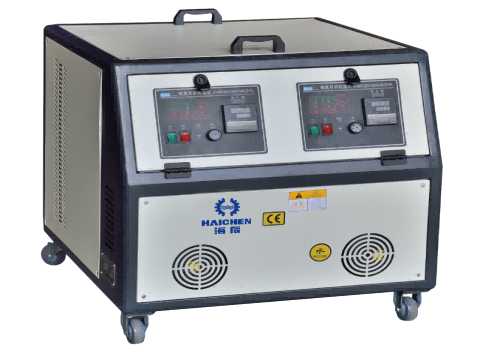
- Molten Metal Temperature:
- Use platinum/platinum-rhodium thermocouples or closed-loop feedback systems to maintain precise temperature control, avoiding solidification or oxidation.
- Mold Preheating & Cooling:
- Preheating to 500°F (260°C) minimizes thermal shock.
- Real-time surface temperature monitoring via thermal imaging; optimal working range: 210–215°C.
- Thermal Mass Design: Ensure sufficient mold mass (e.g., 50x the casting mass) to absorb heat released during solidification.
4. Ejection & Post-Processing
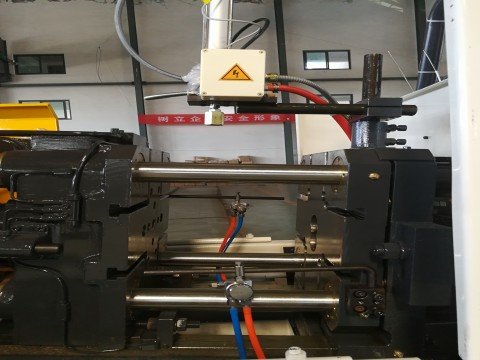
- Vacuum-Assisted Ejection: Replace mechanical ejectors with vacuum grippers to reduce deformation risks in thin-walled castings.
- Anti-Sticking Measures: Apply graphite-based lubricants or optimize draft angles to prevent mold-casting adhesion.
5. Process Optimization & Cost Control
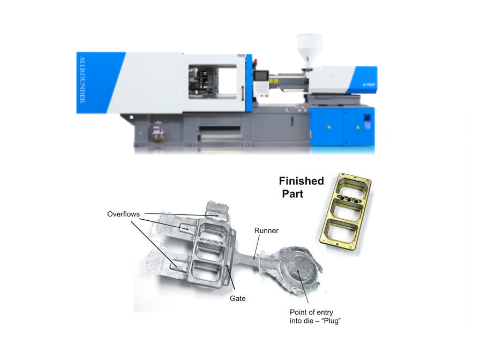
- Multi-Cavity Molds: Use 8-cavity molds to boost productivity while optimizing runners to reduce metal waste.
- Semi-Solid Manufacturing (SSM): Lower injection temperatures to reduce thermal loads and extend mold life.
- Scrap Recycling: Re-melt scrap material to cut raw material costs.
6. Challenges & Solutions
- Porosity & Gas Defects:
- Optimize gate/runner design and vent placement.
- Combine high-pressure injection with low-speed filling to minimize gas entrapment.
- Mold Lifespan:
- Select high-ductility materials (e.g., TZM).
- Regular stress-relief annealing and surface polishing to delay crack initiation.
7. Equipment Selection
- Cold-Chamber Machines: Suitable for high-melting-point alloys (e.g., copper, iron-based), requiring >400-ton clamping forces.
- Hot-Chamber Machines: Limited to low-melting-point alloys (e.g., zinc, magnesium), with max operating temperatures of 450°C.
Conclusion
A robust high-temperature die-casting conveyor system requires:
- Heat-resistant mold materials.
- Precise thermal management.
- High-efficiency injection systems.
- Innovative ejection techniques.
Cost reduction can be achieved through multi-cavity molds and scrap recycling. Future advancements may focus on numerical simulations and directional solidification to optimize thermal management and production efficiency.
Aluminum die casting conveyor
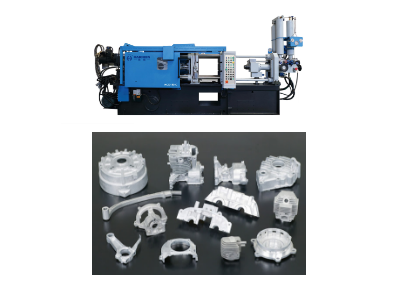
1. Material Selection
Aluminum alloys are preferred for conveyor die-cast components due to their lightweight, high strength, and corrosion resistance. Common alloys include:
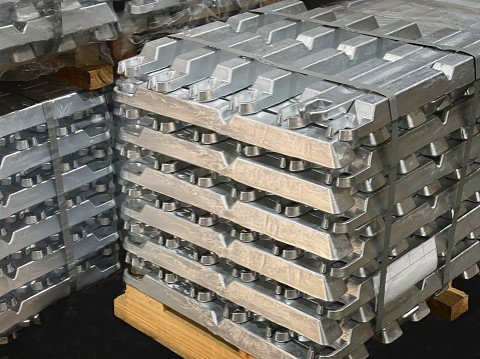
- A380/A383: Cost-effective and versatile, ideal for structural parts.
- A413: Superior airtightness for sealing-critical joints.
- A360: Excellent corrosion resistance for humid or corrosive environments.
- YL102a: High fluidity for intricate thin-walled designs (e.g., valve bodies).
2. Process Parameter Optimization
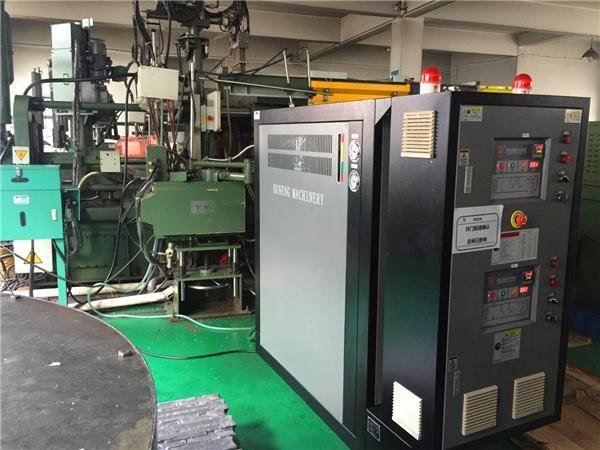
- Mold Temperature: Fixed die at 200°C, moving die at 220°C to minimize shrinkage and improve surface finish.
- Melt Temperature: Optimal pouring temperature of 670°C balances fluidity and solidification.
- Injection Speed: Combination of slow (0.18 m/s) and fast (4.5 m/s) injection speeds ensures uniform filling and reduces turbulence.
- Low-Speed Casting Systems: Conveyor troughs with 15–25° tilt angles minimize air entrapment for precision components.
3. Die casting conveyor Equipment Selection
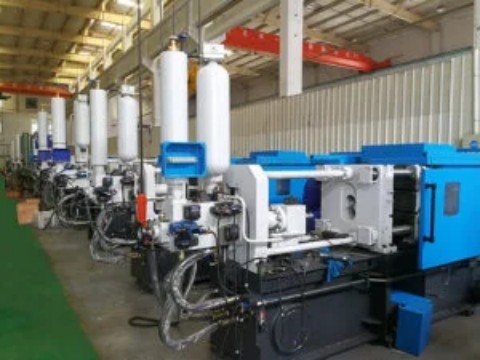
- Machine Tonnage: Haichen 300–880-ton machines for standard parts; e.g., 3000-ton HAICHEN die-casting machines for gearbox housings.
- High-Cycle Machines: HCD880-C ton models achieve 22.6-second cycle times for mass production.
- Dosing Systems: Twin-chamber furnaces ensure ±1% temperature stability for precise pouring.
4. Gating System Design
- Gate Optimization: Bottom-flat gates (3mm thickness) reduce porosity.
- Overflow Design: Overflow reservoirs added to high-shrinkage zones (e.g., “triangle zones”) to compensate for contraction.
- Parting Line Design: Maximum cross-section parting simplifies demolding; side cores handle complex geometries (e.g., flange holes).
5. Die casting conveyor Quality Control & Post-Processing
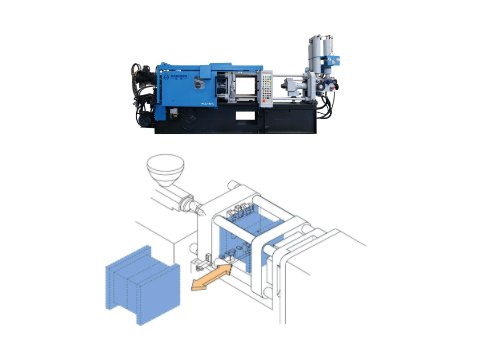
- Defect Prevention: Nitrogen rotary degassing reduces impurities, lowering porosity to <3%.
- Simulation Tools: MAGMAsoft/ProCAST software optimizes filling and solidification.
- Post-Processing: Deburring, CNC machining (±0.05mm tolerance), anodizing, or powder coating for enhanced durability.
6. Industry Trends & Innovations
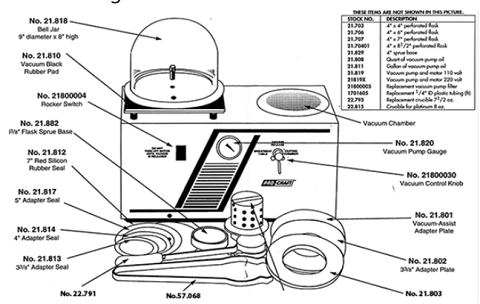
- Vacuum Die Casting: Reduces porosity and improves internal density.
- Diffusion Bonding: Enables high-efficiency cooling structures for EV/semiconductor parts.
- Advanced Mold Steels: ASSAB 8407 alloy improves mold thermal crack resistance, doubling service life.
Overall
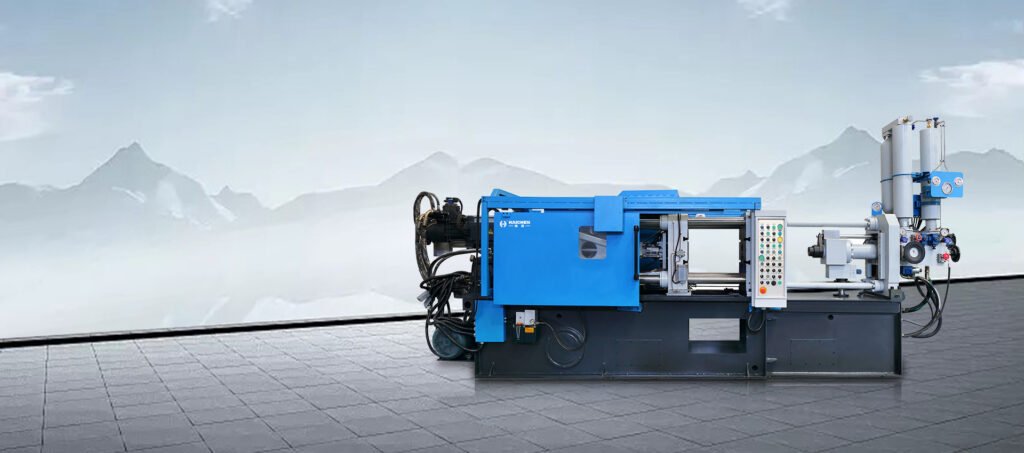
Aluminum die casting for conveyor components requires synergy between material properties, process parameters, and equipment capabilities. Advanced gating systems, simulation tools, and high-cycle machines boost productivity and yield. Innovations like vacuum casting and new alloys further expand applications, solidifying aluminum’s role in modern conveyor manufacturing.