Hot Chamber Die Casting Services: Key Insights for Optimal Results
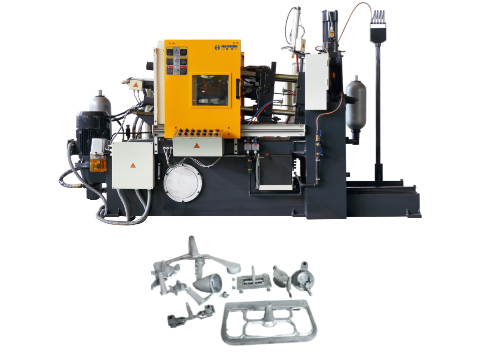
Hot chamber die casting is a specialized process ideal for producing high-volume, intricate parts from low-melting-point metals like zinc, magnesium, and lead alloys. Below is a refined guide to understanding these services, including cost considerations, vendor selection criteria, and industry advancements, tailored for businesses and engineers.
1. Core Benefits of Hot Chamber Die Casting Services
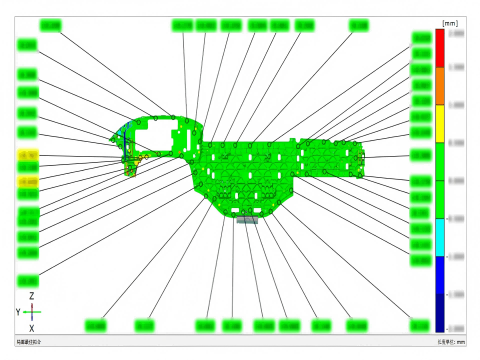
- Speed & Efficiency:
- Cycle times as low as 10–30 seconds due to integrated molten metal systems.
- Ideal for mass production (e.g., 50,000+ parts/month).
- Precision & Detail:
- Achieves tight tolerances (±0.1 mm) and fine features (e.g., thin walls down to 0.5 mm).
- Cost Savings:
- Lower energy consumption vs. cold chamber processes.
- Minimal post-processing (e.g., machining, polishing) reduces labor costs.
2. Typical Applications
- Automotive: Zinc alloy door handles, sensor housings, and transmission components.
- Electronics: Magnesium laptop frames, heat sinks, and connector housings.
- Consumer Goods: Decorative hardware (e.g., zippers, buckles) and kitchen fixtures.
- Medical: Sterilizable magnesium instrument housings and surgical tools.
3. Cost Drivers for Hot Chamber Die Casting Services
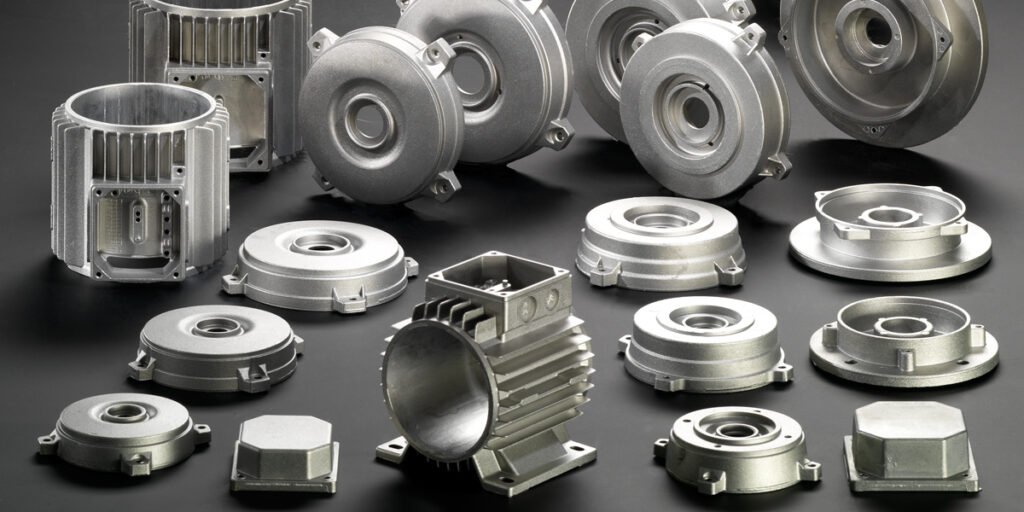
Factor | Impact on Cost |
---|---|
Part Complexity | Multi-slide dies or cores add 20–50% to tooling costs. |
Material | Magnesium alloys cost 2–3× more than zinc. |
Volume | High-volume orders (10,000+ units) reduce per-part costs by 30–60%. |
Surface Finish | Textured or mirror finishes increase costs by 10–25%. |
Secondary Operations | Coating (e.g., powder coating, plating) adds 0.50–0.50–5.00 per part. |
4. Choosing a Service Provider: Key Criteria
- Material Expertise:
- Ensure experience with your alloy (e.g., Zamak 3 for corrosion resistance, AZ91D magnesium for strength).
- Tooling Capabilities:
- Look for H13 tool steel dies for durability (100,000+ cycles).
- Ask about conformal cooling technology to reduce cycle times.
- Quality Assurance:
- Certifications like IATF 16949 (automotive) or ISO 13485 (medical).
- Advanced inspection tools (e.g., CMM, X-ray for porosity checks).
- Sustainability Practices:
- Closed-loop recycling systems for excess material.
- Energy-efficient furnaces and biodegradable release agents.
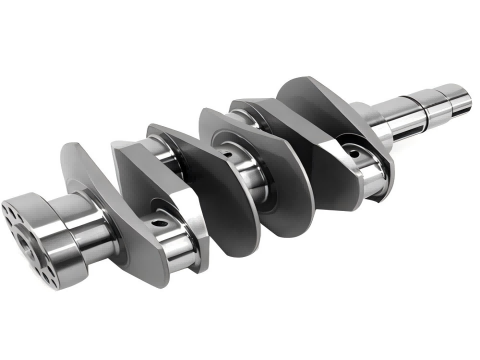
5. Industry Advancements
- AI-Driven Process Optimization:
- Machine learning algorithms predict defects (e.g., porosity) and optimize injection parameters.
- Hybrid Molds:
- 3D-printed inserts for rapid prototyping reduce lead times by 50%.
- Lightweighting Trends:
- High-strength magnesium alloys (e.g., Elektron 21) replace steel in aerospace and automotive parts.
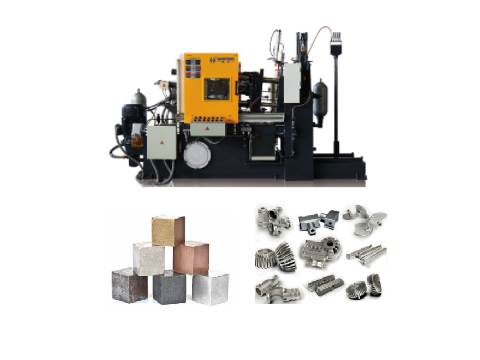
6. Cost-Saving Tips
- Design Simplification: Avoid undercuts and complex geometries to reduce die costs.
- Standardize Tolerances: Looser tolerances (±0.2 mm vs. ±0.05 mm) cut machining expenses.
- Volume Bundling: Combine multiple small orders into larger batches for discounts.
7. Leading Service Providers
- Dynacast: Specializes in zinc and magnesium micro-casting for electronics.
- Gibbs Die Casting: Known for automotive-grade solutions and large-scale production.
- Rockman Industries: Offers end-to-end services from design to assembly.
Hot chamber die casting services deliver unmatched efficiency and precision for high-volume production of low-melting-point metal parts. By prioritizing material expertise, advanced tooling, and sustainability, businesses can optimize costs and quality. For projects requiring rapid prototyping or complex geometries, partnering with providers offering 3D-printed mold inserts or AI-driven process control is recommended.
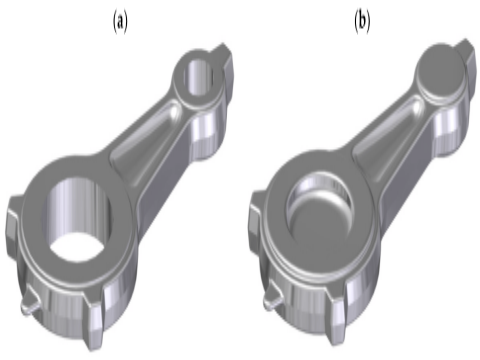
How much does a casting die cost?
The cost of a casting die depends on several factors, including the type of casting process, die complexity, material, and production volume. Below is a detailed breakdown of the factors influencing die costs and typical price ranges for different casting methods.
1. Key Factors Affecting Die Cost
- Type of Casting Process
- Die Casting (Hot or Cold Chamber): Dies are typically more expensive due to high-pressure requirements and precision.
- Sand Casting: Patterns and molds are cheaper but less durable.
- Investment Casting: Wax patterns and ceramic molds are cost-effective for small batches.
- Die Complexity
- Simple Dies: Minimal features, straight pulls, and no undercuts.
- Complex Dies: Intricate geometries, multiple slides, and cores increase costs.
- Material
- Tool Steel (e.g., H13, P20): High durability but expensive.
- Aluminum: Cheaper but less durable for high-volume production.
- Size and Weight
- Larger dies require more material and machining, increasing costs.
- Production Volume
- High-volume dies are made from hardened steel for longevity, while low-volume dies may use softer materials.
- Surface Finish and Tolerances
- High-precision dies with fine surface finishes cost more due to additional machining and polishing.
- Additional Features
- Cooling channels, ejector pins, and venting systems add to the cost.
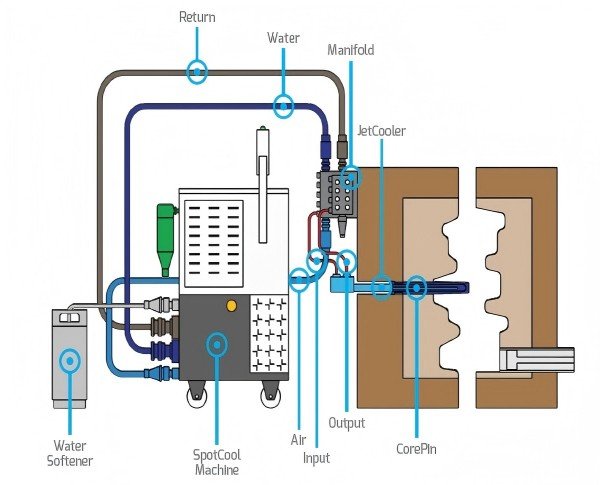
2. Typical Die Costs by Casting Method
Casting Method | Die Cost Range | Key Considerations |
---|---|---|
Die Casting | 10,000–10,000–100,000+ | High-pressure dies require hardened steel (e.g., H13). Complex geometries and multi-cavity dies increase costs. |
Sand Casting | 1,000–1,000–20,000 | Patterns and molds are cheaper but less durable. Suitable for low-volume production. |
Investment Casting | 500–500–10,000 | Wax patterns and ceramic molds are cost-effective for small batches. |
Gravity Casting | 5,000–5,000–50,000 | Dies are simpler than die casting but still require precision. |
Low-Pressure Casting | 10,000–10,000–60,000 | Dies are similar to gravity casting but may require additional features for pressure control. |
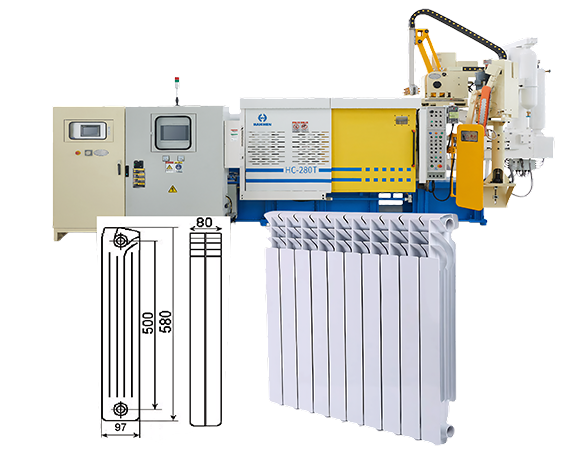
3. Cost Breakdown for Die Casting Dies
- Material: Tool steel (e.g., H13) costs 50–50–100 per kg. A typical die may weigh 500–5,000 kg.
- Machining: CNC machining accounts for 30–50% of the total cost.
- Heat Treatment: Hardening and tempering add 1,000–1,000–5,000.
- Surface Finishing: Polishing and texturing cost 500–500–5,000.
- Design and Prototyping: CAD design and prototyping can add 2,000–2,000–10,000.
4. Examples of Die Costs
- Simple Die (Single Cavity): 10,000–10,000–20,000.
- Complex Die (Multi-Cavity): 50,000–50,000–100,000+.
- Large Die (Automotive Part): 100,000–100,000–200,000+.
5. Ways to Reduce Die Costs
- Simplify Design: Minimize undercuts, slides, and complex features.
- Use Standard Components: Off-the-shelf ejector pins, cooling channels, and inserts reduce costs.
- Optimize Production Volume: For low volumes, consider softer materials or alternative casting methods.
- Prototype First: Test designs with 3D-printed or low-cost molds before investing in high-end dies.
Haichen hot chamber die casting
1. Product Line and Technical Parameters
Applicable Materials:
Designed for low melting point metals, mainly for zinc (Zn) and lead (Pb) alloys, and some models can also process copper alloys.
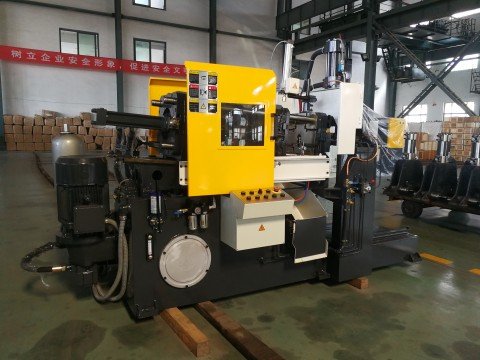
Zinc alloy has become the mainstream material for hot chamber die casting due to its low melting point (about 420°C) and good fluidity. Typical applications include automotive parts, bathroom hardware, etc.
Tonnage Range:
The clamping force of Haichen hot chamber die casting machine covers 15 tons to 280 tons, meeting the production needs from small precision parts to medium-sized parts.
For example, the HCD50-H model is 50 tons, suitable for a single injection of 1.1 kg of zinc liquid; the HCD180-H model can reach 180 tons, and the single injection volume reaches 2.2-2.6 kg.
Automation Configuration:
Optional automatic spraying unit, pick-up machine and spoon feeding system support intelligent production.
2. Design and technical advantages
Structural features:
Adopting the “gooseneck” design, the injection cavity is immersed in the molten metal, no external feeding is required, and the production cycle is shortened.
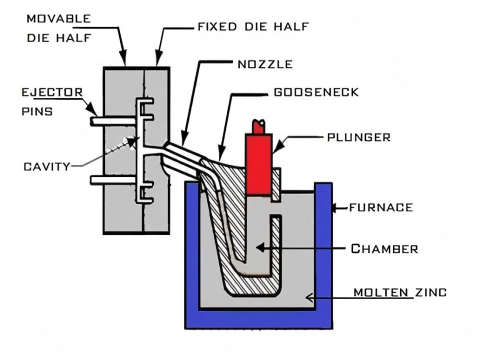
The hydraulic system uses brand components such as American Vickers and German Yuken to ensure high stability.
Control system:
Equipped with Mitsubishi (MITSUBISHI) industrial controller and Siemens PLC, supporting multi-language interface (such as English, Spanish, Russian), easy to operate.
Energy saving and environmental protection:
Some models can be equipped with optional servo system, which reduces energy consumption through precise control, in line with the green production trend of modern industry.
3. Quality control and certification
Haichen has passed ISO 9001 quality management system certification and EU CE standards to ensure that the equipment meets international safety and performance requirements.
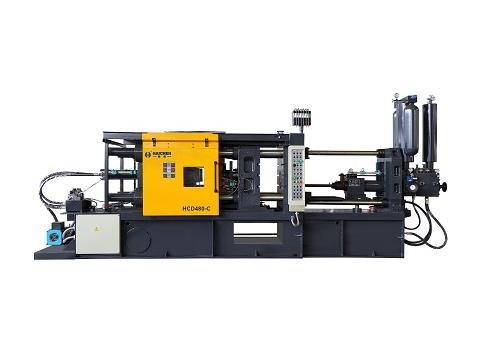
Each machine must undergo rigorous testing before leaving the factory. The warranty period for key components (such as templates and tie rods) is 12 months, and the warranty period for wearing parts (such as nozzles and plungers) is 2 months.
4. Application areas
Hot chamber die casting machines are suitable for the production of large-scale, thin-walled complex parts. Typical applications include:
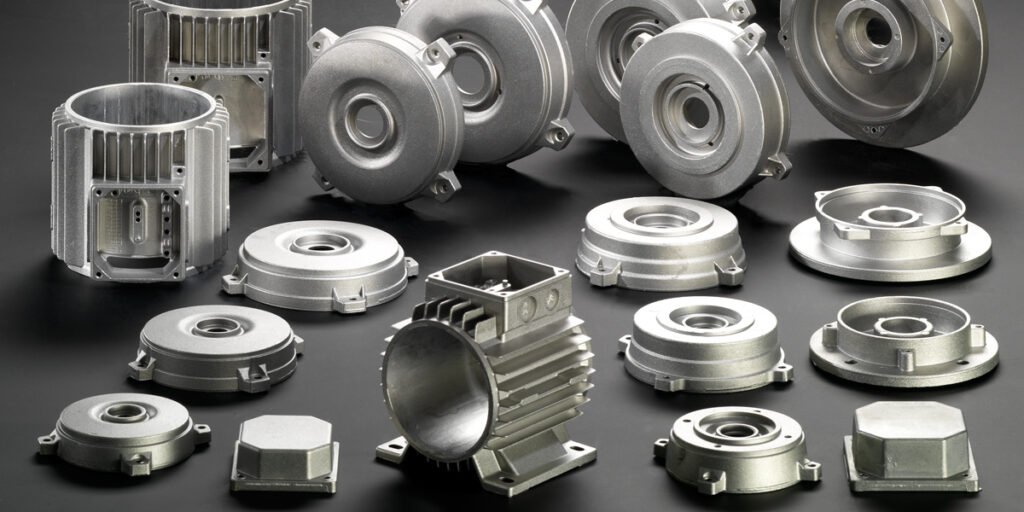
Automotive industry: motorcycle accessories, balance blocks, etc.
Consumer electronics: radiators, connectors, etc.
Household hardware: faucets, door lock accessories, etc.
Conclusion
The cost of a casting die varies widely based on the casting method, die complexity, material, and production volume. Die casting dies are the most expensive, ranging from 10,000toover10,000toover100,000, while sand casting and investment casting dies are more affordable. To minimize costs, simplify designs, optimize production volumes, and work with experienced suppliers.
Welcome to contact us for more options.
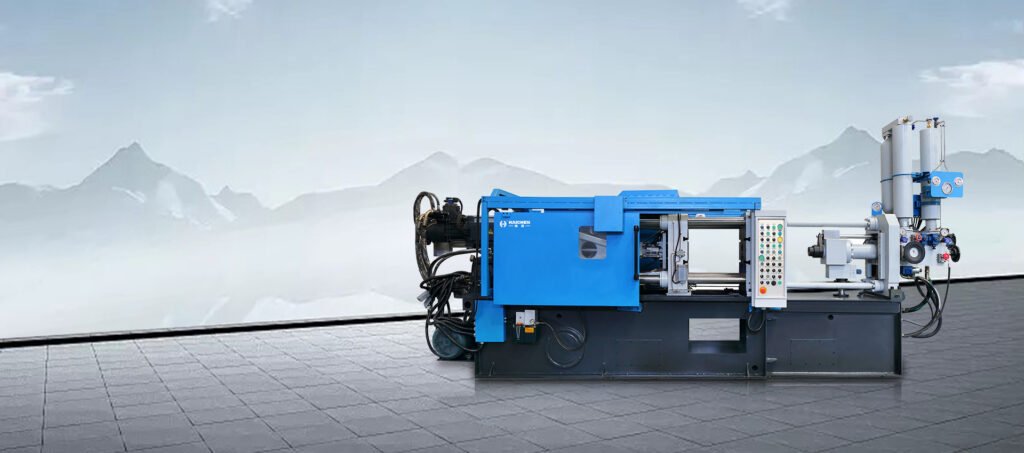