A trim press is a hydraulic shearing or cutting operation for the precise trimming of material and the removal of burrs.
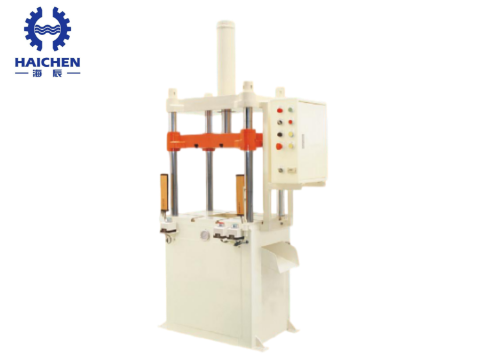
A machine for removing excess material from sheet metal, castings or other materials.
The following are the working principle and features of a trim press:
1.Working principle
2.Equipment Configuration
3.Operating characteristics
4.Application areas
5.Safety and efficiency
1.Working principle:
Trim press typically include a shearing device that cuts the sheet along a predetermined cut line, separating the product portion from the non-product portion.
Presses use hydraulic tool change slides to allow for quick changeover of large, heavy tools at the push of a button.
Presses can be hydraulically or mechanically driven.
Hydraulic presses offer power and versatility, while mechanical presses are suitable for high volume production due to their high speed operation.
Servo presses, on the other hand, provide precise control and are suitable for trimming complex parts.
2. Equipment Configuration:
Hydraulic presses shear and cut by applying pressure through hydraulic cylinders.
Mechanical presses, on the other hand, utilise motors and flywheel mechanisms and are suitable for high speeds, making them effective in high volume production.
Servo presses use servo motors to control the speed, position and pressure of the punch, providing precise control of the trimming operation and are ideal for complex parts.
3. Operating characteristics:
Trim press typically feature multi-side access, allowing die setup from all directions, and support multiple feed configurations, making them easy to integrate into an assembly line or manufacturing cell.
In some applications, trim press can be equipped with automated tool change systems, such as hydraulic tool change slides that allow for quick tool changes.
Trim press can also be integrated with a variety of additional functions such as drilling, sawing, tapping and milling to increase productivity.
4. Areas of application:
Trim press have widely using range of applications such as metalworking, automotive manufacturing and plastic moulding.
For example, in the automotive industry, trim press can to remove burrs from die-cast castings.
In the plastic moulding process, trim press can remove excess parts from thermoformed parts.
5. Safety and efficiency:
Trim press’ design need with safety and efficiency in mind.
The Vertical Trimming Stacking Press utilises an automatic sheet adjustment and servo feeding system to achieve cycle speeds of up to 200 cycles per minute.
During operation, the trimming press uses laser displacement sensors and a data acquisition system to record force and displacement signals.
for subsequent data processing and analysis.
The Trimming Press effectively removes excess material through precise shearing and cutting operations, improving productivity and product quality.
Its diverse configurations and flexible operation make it an important application in modern manufacturing.
Die casting hydraulic trim press machine work process
The working process of die casting hydraulic trimming machine is mainly to clean up the excess part of die casting products.
Including six steps:
1. Picking up parts
2. Mould closing and pressing
3.Cutting edge
4. Static pressure shaping
5. Open the mould and take pieces
6.Cleaning and blowing
1. Picking up pieces:
Firstly, the die casting is fed to the lower mould position of the trimming machine by means of a conveyor belt or a manipulator.
At this stage, it is necessary to ensure that the die casting is placed on the follower support plate.
The placement of the die casting part is also detected by means of a photoelectric sensor switch.
2. Mould closing and pressing:
In the process of mould closing, the following shape pressure plate gradually contacts the die casting, and gradually presses the die casting under the action of the ejector plate.
When the pressure reaches the set value, the controller controls the driving parts to start the pressure relief.
So that the following plate, fixed plate, connecting block and ejector plate as a whole will not continue to fall.
3. Cutting edge:
The upper mould seat plate continues to descend with the connecting column, pallet and upper punching and cutting knife mouth.
By the upper punch cutting knife mouth on the die casting for cutting edge processing.
After the edge-cutting is finish, the cut material drops down through the drop port on the lower mould seat plate.
4. Static pressure shaping:
After the mould clamp the die casting is shaping by static pressure for a set period of time using the mould closing force.
To ensure the dimensional accuracy and surface finish of the die casting.
5. Open the mould and take pieces:
After the static pressure shaping is completed, the controller controls the edge cutter to drive the upper mould to rise and reset as a whole, completing the opening of the mould.
At this time, the cylinder gripper’s gripper supports the die casting and lifts the die casting to rise with the upper mould, so as to achieve the die casting to stay on the upper mould.
When the pallet used to receive the die casting enters between the upper mould and the lower mould, then the cylinder gripper will rotate and reset to the vertical state.
Release the die casting, the die casting automatically fall to the pallet, complete the pickup.
6. Cleaning and blowing:
After taking the pieces, start the blowing device to blow air to the lower die with the shape of the support plate and the lower punch cutting knife mouth.
Clean up the residual drop material.
The above steps show the detailed workflow of the hydraulic trimming machine in dealing with die casting, from picking up to cleaning.
Each step needs precisely controlling to ensure product quality and production efficiency.
How die casting machine trim press do the tapping process
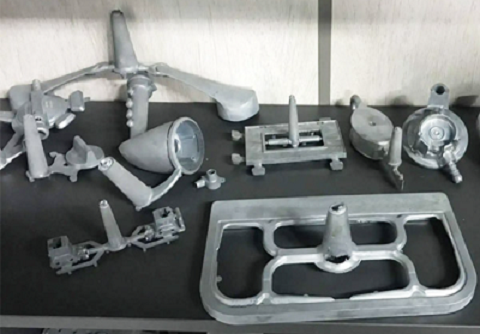
Die casting trimming press assembly and tapping process using specialised tapping equipment and tools.
The following are detail steps and precautions:
1. Positioning and preparation:
Before starting tapping, you first need to make sure that the die casting workpiece is firmly fixed on the die casting trimming press.
To prevent it from moving or wobbling during the tapping process.
Use the drill to drill holes in the workpiece, make sure that the diameter of the drill hole is slightly larger than the tapping calibre.
And the hole should be perpendicular to the surface of the workpiece.
2. Choose the right tap:
Choose the right tap according to the material of the workpiece and the thread specifications.
For example, for steel parts, oil lubrication can be chosen; for aluminium parts, emulsion lubrication can be chosen.
Use a tapping guide to ensure that the tap is perpendicular to the hole axis to improve tapping accuracy.
3. Tapping operation:
Insert the tapping tool into the drilled hole, maintain a certain rotation speed and duration.
And keep adding lubricant until tapping is completed.
During the tapping process, reverse the tapper approximately 1/4 turn after each revolution to aid chip evacuation and reduce cutting resistance.
If a tapping failure is encountered, it is necessary to withdraw the tap to remove chips and then restart tapping.
4. Cooling and lubrication:
Use cutting fluids (e.g. mineral oil based emulsions, synthetic coolants, etc.) for cooling and lubrication to improve thread quality and tool life.
The cutting fluid can be supplied either internally or externally cooled, the choice depending on the material properties and depth of machining.
5. Inspection and testing:
After tapping is complete, use a wire gauge to check the peak and valley parameters of the thread to ensure that the thread meets the requirements.
Clean the tools and working environment to avoid any impact on subsequent machining.
6.Safety Precautions:
During operation, you must wear appropriate labour protection equipment and ensure that the power switch and wiring are normal.
Gloves are strictly prohibited during operation, and long hair of female employees should be pulled into the working cap.
Through the above steps and precautions, you can effectively complete the tapping process of die casting trimming press to ensure the quality and efficiency of thread processing.