Die casting spray nozzles are the final segment of equipment in a die cast sprayer.
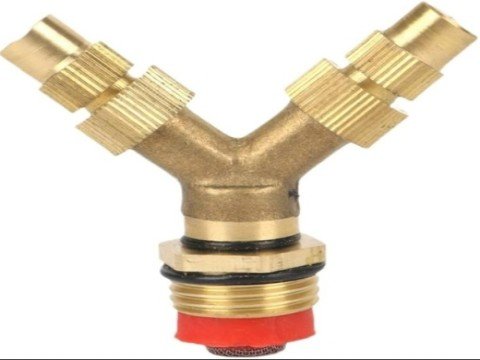
They are extremely important for the entire automated die cast production setup.
The different die casting product shapes and mould designs are the basic reference for the choice of nozzle type.
There are five key factors to consider when selecting the right die casting nozzle:
1. Spray flow and pressure
2. Spray pattern and angle
3. Spray liquid type
4. Die-casting nozzle material selection
5. Atomisation quality
1. Spraying flow rate and pressure:
Select the appropriate flow rate (GPM or LPM) and operating pressure according to the application requirements.
to ensure fluid delivery and spray effectiveness.
2. Spray pattern and angle:
Select the appropriate spray pattern (e.g. solid flow, fan, cone, etc.) and spray angle.
To achieve the desired coverage and spray effect.
3.Spray liquid type:
Select the appropriate nozzle according to the type of liquid to be sprayed (e.g. water, lubricant, etc.).
Ensure good atomisation effect and spray uniformity.
4. Die-casting nozzle material selection:
According to the working environment and liquid characteristics to choose the right nozzle material, such as brass, stainless steel, etc..
Used to improve corrosion resistance and service life.
5. Atomisation quality:
For applications requiring fine atomisation (e.g. coating, wetting, etc.), air atomisation nozzles can be selected.
This type of nozzle uses compressed air to achieve finer droplets.
Through a combination of the above factors, you can choose the best nozzle for the die casting process, thereby increasing productivity and reducing defects.
Select Die casting spray nozzles according to spray pattern
When choosing the right spray nozzle, use different spray nozzles for different spray patterns and angles.
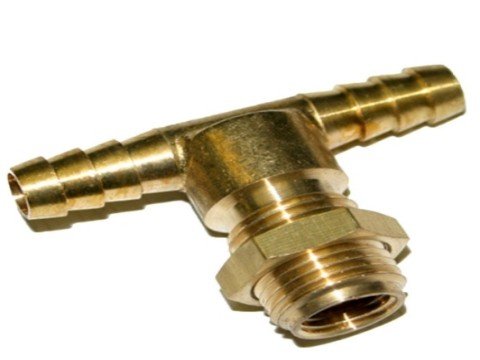
Below are a few common types of nozzles and their application scenarios:
1. Flat Fan Nozzles
2. Hollow Cone Nozzles (Hollow Cone Nozzles)
3. Fine Spray Nozzles (Fine Spray Nozzles)
4. Air Atomising Nozzles (Air Atomising Nozzles)
5. Full Cone Nozzles (Full Cone Nozzles)
6. Spray Angle
1. Flat Fan Nozzles:
Suitable for cleaning, rinsing and coating, they are available in a wide range of spray angles (1° to 170°) and produce a uniform fan spray pattern.
2. Hollow Cone Nozzles:
Suitable for cooling, cleaning and dust control, with spray angles ranging from 43° to 180°, usually used for applications requiring greater coverage.
3. Fine Spray Nozzles:
Known for the small water droplets they produce, they are suitable for humidification, atomisation and dust control, with spray angles ranging from 30° to 165°.
4. Air Atomising Nozzles:
Atomising liquids by compressed air, suitable for coating, humidification and atomisation, with a wide range of flow rates and spray patterns.
5. Full Cone Nozzles:
Produces a uniformly distributed conical spray, suitable for occasions where full coverage is required.
6. Spray Angle:
Wide angle nozzles (e.g. 110° to 120°) are suitable for large area coverage, while narrow angle nozzles (e.g. 80° to 95°) are suitable for precise application.
Depending on the specific application requirements, choose the nozzle type and spray angle wisely to achieve the best results.
Different materials and options for die casting nozzles
The material selection of die-casting nozzles needs to consider its working environment, the chemical properties of the liquid medium.
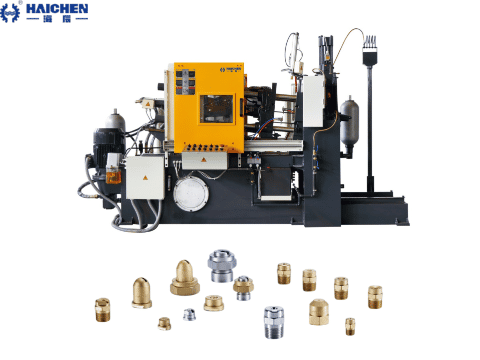
As well as the nozzle’s working pressure and flow requirements.
Commonly used materials include:
1. Bronze
2.Plastic
3. Stainless steel
4.Ceramic
5.Carbide
1.Bronze:
Suitable for non-corrosive tank fluid, with good processing performance and toughness.
But the hardness is low, easy to wear.
2.Plastic:
Such as nylon plastic, suitable for strong corrosive tank fluid.
Low cost and easy to replace.
3. Stainless steel:
Good corrosion resistance, suitable for chemical industry and phosphating tank fluid.
But the cost is high.
4. Ceramic:
Extremely wear-resistant, suitable for high pressure and long time use.
5.Carbide:
Suitable for high abrasion environment, such as Zamak alloy die casting.
Factors such as nozzle geometry, pressure, flow rate and application area also need to be taken into account when selecting.
Selection of different die-casting nozzles by type of fluid sprayed
When selecting die-casting nozzles, the appropriate type of nozzle should be determined according to the type of spraying liquid and spraying requirements.
Haichen has a full range of well researched die casting nozzles to match all types of die casting machines for automated production.
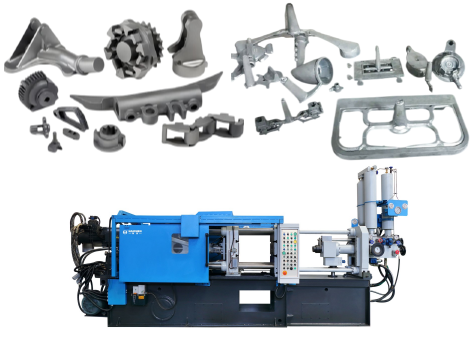
1. For example, fan nozzle is suitable for large area spraying, while atomised nozzle is suitable for fine spraying.
2. In addition, the material of the nozzle also need to consider the chemical properties of the liquid, such as non-corrosive liquids can be selected bronze or plastic materials.
3. Strong corrosive liquid need to choose ceramic, silicon carbide or stainless steel and other corrosion-resistant materials.
In the die-casting process, automatic spraying system can improve the mould life and reduce maintenance costs.