Here are some important mold temperature controller maintenance tips:
- Routine Cleaning and Examination
- Fluid Maintenance
- Pump & Heating Adjustments
- Electrical and Control System validates
- Preventing Corrosion and Lubricating
- Preventative Maintenance Schedule
- Environmental Considerations
Maintaining your Mold Temperature Controller (MTC) is crucial for ensuring consistent part quality, prolonging equipment life, and preventing costly downtime.
Mold Temperature Controller Maintenance Tips
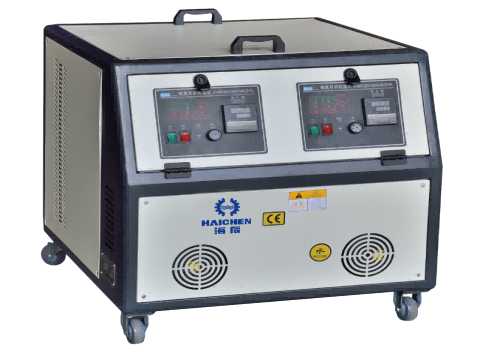
Routine Cleaning and Examination
Remove any cooling water/oil residue: Efficiencies could drop due to clogging from minerals, sludge, or debris.
Look for any leakages: Look for fracture or leak in the fluid circuit including hoses, seals and other relevant parts.
Wipe any dust on air vents and filters: Overheating could result from caps in airflow caused by dust or debris.
Fluid Maintenance
Use Quality thermal fluids: Any contaminated or degraded heat transfer fluid will decrease efficiency. Keep a check on fluid level: Damage to the pump or overheating are risks of low fluid levels. Replace or flush fluids periodically: To prevent excessive build up, follow the manufacturer’s recommendations.
Pump & Heating Adjustments
Check the pump: Listen for whirring noises which would indicate smoother operation.
Inspect for overheating elements: Check for signs of scales, corrosion, or burnout.
Perform pressure and flow rates test: Any out of range reading could mean blockages or pump problems.
Electrical and Control System validates
Check the wiring and connections: Bonds which are loose or eroded may cause issues.
Test safety equips: Check that the overheat protection and flow alarms along with the emergency shutdown are working as intended.
Preventing Corrosion and Lubricating
Lubricate Moving Parts: Remember to lubricate valves, pumps, and other parts to prevent possible wear and damage. Apply
Anti-corrosive Coatings: Apply anti-rust layers on components that are prone to corrosion.
Preventative Maintenance Schedule
- Daily: Check fluid levels, inspect for leaks, and verify temperature stability.
- Weekly: Clean filters, test pump performance, and inspect electrical components.
- Monthly: Flush the system (if needed), calibrate sensors, and check hoses/pipes.
- Annually: Perform a full system inspection, replace worn parts, and verify controller software updates.
Environmental Considerations
- Keep the area around the controller clean & ventilated – Avoid dust buildup and overheating.
- Ensure proper coolant temperature – Excessively hot or cold ambient conditions can affect performance.
What is Mold Temperature Controller
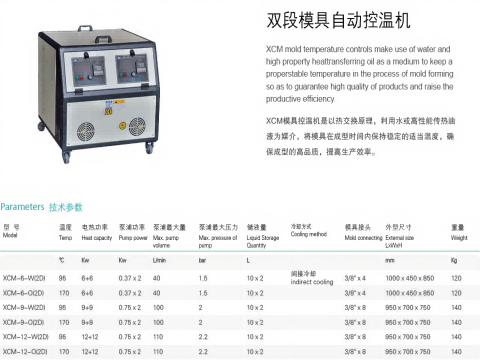
MTC is a device used to accurately control the temperature of the mold, which is widely used in plastic injection molding, metal casting, automotive manufacturing and other fields. Its main function is to regulate the temperature in the mold through the heating or cooling system to ensure that the mold can maintain a stable temperature during the production process, so as to improve product quality, shorten the molding cycle and reduce energy consumption.
How Does a Mold Temperature Controller Unit Work?
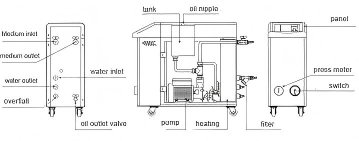
A mold temperature controller unit works by regulating the temperature of a mold during the manufacturing process, typically in plastic or metal molding. Here’s how it operates:
- Preparation
- Heating
- Cooling
- Cyclic control
Preparation:
Before the machine operates, the system verifies that all sensors are working and there are sufficient fluids that are compatible with all processes involved.
Heating:
The controller turns on the hot medium, which can be oil, water, or another substance, to heat the coolant when the set value goes below the set value. The pump then sends the hot medium to the mold’s cooling channel such that there can be heat exchange, and the mold can be warmed in the process.
Cooling
Controller turns into cooling mode when exceeding or reaching preset temperature on mold. The controller activates the cooling system which removes excess heat from the cooling channel and reduces the temperature of the hot medium in turn removing heat from the mold.
Cyclic control:
All steps are controlled electronically in a loop. In this case, a temperature sensor detects the temperature of the mold while the controller receives data in real-time. In response, the controller determines whether it needs to stop the heating and cooling system depending on adjusting systems to bring the molding or cooling system according to the deviation to maintain a stable mold temperature.
Benefits of Using the Mold Temperature Controller
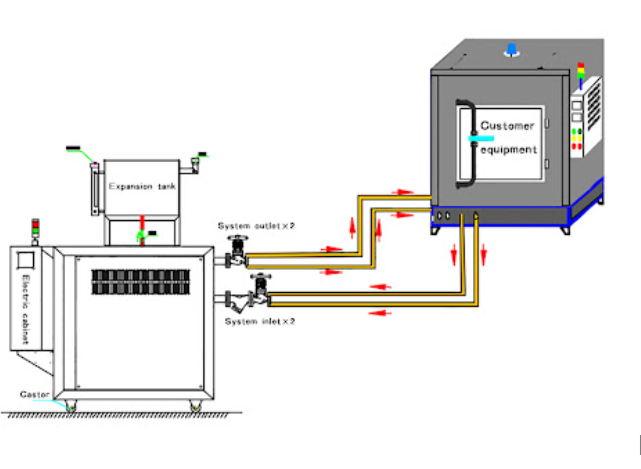
Here are the several key benefits:
- Enhanced Product Quality
- Improved Production Efficiency
- Energy Savings
- Extended Mold Life
- Better Process Control
Enhanced Product Quality:
Consistent mold temperatures reduce defects like warping, sink marks, and inconsistent shrinkage.
Improved Production Efficiency:
Optimized temperatures shorten cycle times, increasing overall productivity.
Energy Savings:
Precise temperature control minimizes energy waste.
Extended Mold Life:
Reduced thermal stress helps prolong the lifespan of molds.
Better Process Control:
Ensures stable and repeatable manufacturing conditions.
Die casting machine supplier: Haichen Machinery
Haichen is a die casting machine factory located in Ningbo, China, mainly supplying cold chamber die casting machine and hot chamber die casting machine. Besides machines, we also supply die casting auxiliary equipments and spear parts, including mold temperature controller, conveyor, spray systems, mold temperature controllers, and industrial robots.
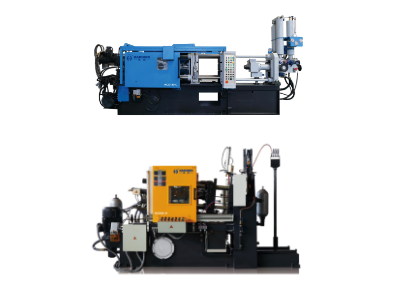
By following these maintenance practices, you can extend the lifespan of your mold temperature controller, improve energy efficiency, and maintain consistent production quality.
If there is any demand for the controller or other equipments, welcome to consult us.