Ladle Components in die casting include ladle cup, main frame, pouring spout, handle & lever mechanism, temperature control features, and etc.
In the die casting process, the ladle is an important component used to transfer catalyst metal from the furnace pipe to the die casting mold cavity. The ladle plays a key role in both cold chamber and hot chamber die casting, and its design and use directly affect the quality of castings and production efficiency.
Die casting ladle components

Ladle Cup of ladle components
- Function: The ladle cup is the core component that scoops and pours molten metal. It is designed to withstand high temperatures and resist wear.
- Materials: Ladle cups can be made from high-duty cast iron or ceramic materials. Ceramic cups have a high melting point (1860°C ± 10°C) and low thermal expansion, making them suitable for high-temperature environments. They also prevent oxides from entering the molten metal, reducing defects in the final casting. Cast iron cups, while less resistant to thermal shock and corrosion, are more cost-effective and have good thermal conductivity.
Main Frame
- Function: The main frame supports the entire ladle structure, including the moving mechanism, rocker arm mechanism, and ladle cup.
- Materials: Typically made from steel, the main frame provides the structural strength needed to handle the weight and movement of the ladle.
Pouring Spout (Nozzle)
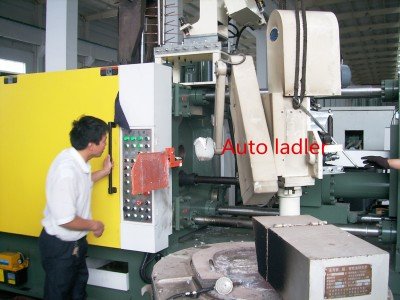
- Designed for controlled metal flow into the die.
- Prevents oxidation and slag inclusion by minimizing turbulence.
- Often tapered to improve accuracy.
Handle & Lever Mechanism
- Allows the operator (or robotic system) to tilt the ladle for pouring.
- Manual ladles have a long handle for operator safety.
- Automated systems may use hydraulic/pneumatic actuators for precision.
Temperature Control Features
- Some ladles include heating elements or ceramic insulation to maintain molten metal temperature.
- Thermocouples may be integrated for real-time monitoring.
Skimming Edge
- Helps remove dross (oxide layer) from the molten metal surface before pouring.
- Ensures cleaner metal enters the die.
Lifting Lugs / Hooks
- Used for mechanical handling (e.g., crane or robotic arm).
- Ensures stability during transport.
Lid (Cover)
- Optional but useful for preventing heat loss and contamination.
- Often used in automated die casting systems.
Weight & Volume Markings
- Helps operators measure the correct amount of molten metal for each shot.
Die casting ladle supplier: Haichen Machinery
Haichen Machinery is a well-known manufacturer of die-casting equipment, including die-casting ladles (pouring ladles or dosing furnaces) used for transferring molten metal (typically aluminum, zinc, or magnesium alloys) into cold chamber die-casting machines. Our ladles provide precision, efficiency, and durability in high-pressure die-casting (HPDC) operations.
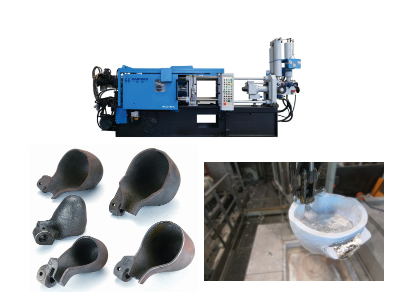
The Haichen Ladle offers several advantages that enhance the efficiency and quality of the die casting process:
High-Quality Materials
Haichen Ladle are made from durable materials such as ductile cast iron, which provides excellent wear resistance and a hardness of 45-50 HRC. This material ensures that the ladle cups can withstand the high temperatures and repeated use associated with die casting operations.
Minimized Heat Loss and Oxidation
The ladle cups can minimize heat loss and exposure of molten metal to air. This reduces oxidation and the formation of defects in the cast product. The preheating and insulation features of the ladle cups help maintain the optimal temperature of the molten metal during the casting process.
Long Service Life
The ladle cups are built to last, with a service life of over 5000 uses. This longevity reduces the frequency of replacements and maintenance, lowering overall production costs.
If there is any demand for die casting ladles cup, welcome to consult us.