Die Casting Mold maintenance methods require a combination of measures to ensure their life and performance.
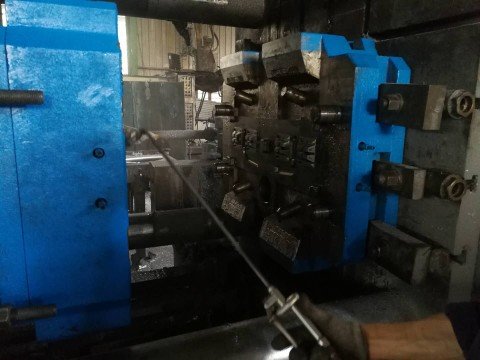
The following is Haichen’s maintenance strategy for you to synthesize the various evidences:
1. Mould preheating
It is necessary to preheat the mould before casting at high temperatures to prevent cracking due to thermal shock.
Complex moulds can be heated by gun or gas, simple moulds can be preheated by slow pressure injection.
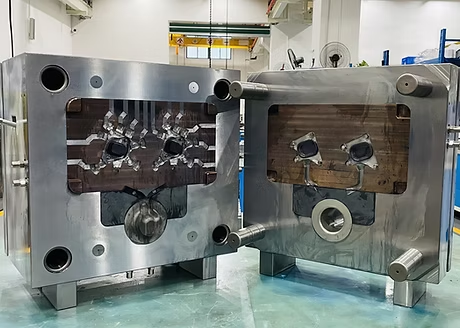
2. Cleaning and lubrication
Regular cleaning:
Timely removal of cavity residues, flying edge and metal debris, to avoid impurities affecting the quality of castings.
Cleaning tools include wire brushes, compressed air or mild solvents.
Uniform lubrication:
Lubricate the sliding parts (e.g., guide pillar, ejector pin) and the inner wall of the mould to reduce friction and assist in mould release.
Wipe off excess residue after lubrication to prevent build-up.
Haichen really care about this step in Die Casting Mold maintenance in Mexico.
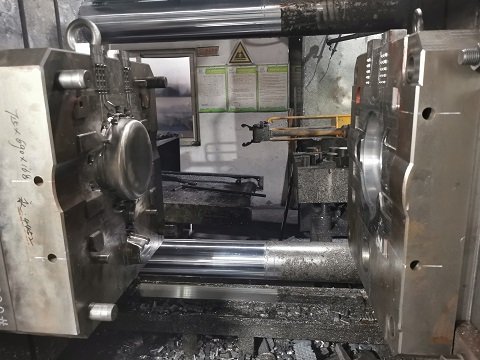
3. Inspection and Repair
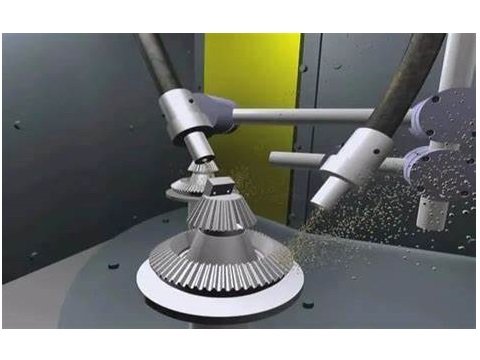
Surface Inspection:
Regularly inspect the surface of the mould for wear, cracks, corrosion or adhesion, especially the parting surfaces and key structures.
Component Repair:
Damage (e.g. cracks, chipped corners) needs to be repaired in time, which can be done by welding, polishing or re-processing and other techniques.
Function check:
Before trial operation, the stability of the mould opening and closing action should be verified, and the parameters (e.g. cooling channel design) should be adjusted through the trial mould.
4. Cooling system and temperature control
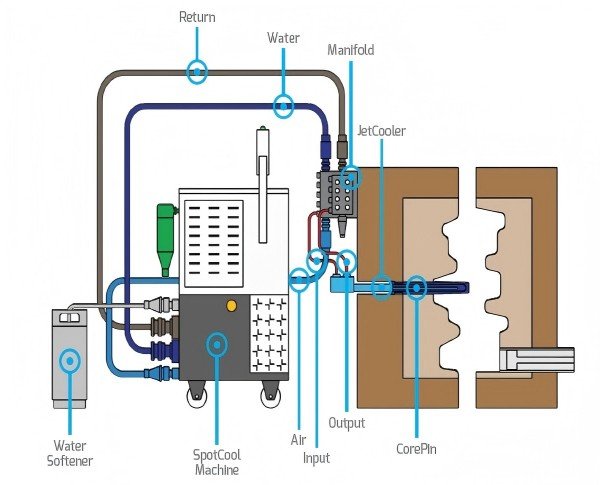
Optimise the cooling channel design to shorten the solidification time of the castings and improve the production efficiency.
Monitor the mould temperature and use cooling medium or heater to maintain a suitable temperature range to avoid deformation due to excessive temperature difference.
5. Stress relief treatment
Stress annealing treatment is carried out regularly, the specific cycle is as follows:
the first production is about 2,000-5,000 moulds;
the second is in the range of 10,000-20,000 moulds; and
the subsequent intervals do not exceed 15,000 moulds.
6. Preventive Maintenance and Parts Replacement
Bolt Tightening:
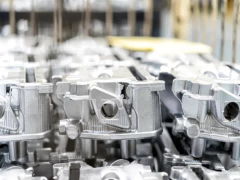
Check whether the fasteners are firm before installation to prevent loosening during operation.
Replacement of wearing parts:
Replace the wearing parts (e.g. ejector pin, guide sleeve) regularly to avoid collateral damage to the main body of the mould.
Surface Strengthening Technology:
Apply PVD/CVD coating to enhance the wear resistance, corrosion resistance and thermal fatigue resistance of the mould surface.
7. Storage and daily management
Moulds need to be stored in a dry and clean environment when they are out of use to avoid moisture and pollutant erosion.
Establish a systematic maintenance record to track the number of times the mould is used and the maintenance history, and formulate a periodic maintenance plan (e.g., comprehensive maintenance every 5000 moulds).
8. Advanced technology application
Adopts intelligent system (e.g. AI monitoring) and modular design to achieve real-time monitoring and optimisation of mould status.
Combine with new technology (e.g. vacuum die casting) to reduce the heat load of mould and prolong the service life.
With the above measures, mould life can be significantly increased (up to hundreds of thousands of cycles).
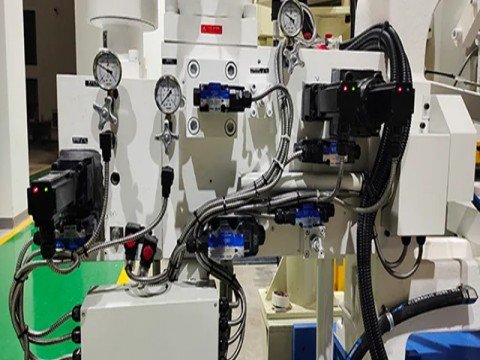
This reduces downtime and ensures consistent casting quality. Maintenance requires a balance between preventive operations and timely repairs, combined with technological advances to achieve efficient management.
Welcome to contact us for more information about die casting process.
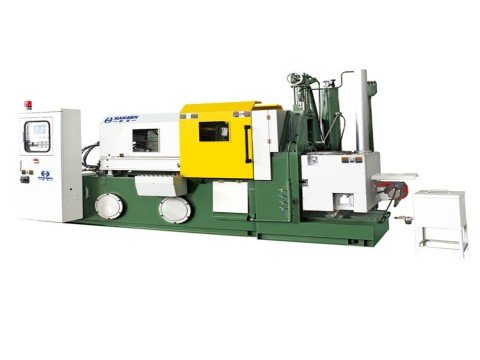