In the die casting process, maintenance of the release agent mixer is an important part of ensuring productivity and product quality.
- Regular cleaning
- Regular sterilization
- Checking and replacing parts
- Monitoring & Maintenance Systems
The maintenance of the die release agent mixer needs to comprehensively consider the selection of die release agent, equipment cleaning, temperature control, spray technology, equipment aging management, environmental protection measures and process optimization and other aspects.
Through scientific and reasonable maintenance strategy, can significantly improve the efficiency of die casting production and product quality.
Regular cleaning
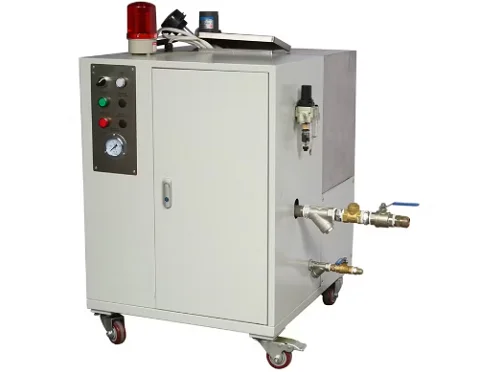
- COMPREHENSIVE CLEANING:
- Daily Cleaning
COMPREHENSIVE CLEANING:
A comprehensive cleaning should be performed at least once a year to remove impurities from the entire release agent system. It includes bacterial films, inorganic substances and release agent residues.
Daily Cleaning:
Clean regularly with a chemical cleaner.
Prior to cleaning, wipe all equipment in contact with the release agent, such as mixing tanks, piping, etc., with a cloth (do not use facecloth), and use high pressure gas for cleaning whenever possible.
When cleaning, completely empty the mixing tank, add the cleaning mixture, and set the equipment power to the highest cycle for at least four hours to improve cleaning efficiency. Filters need to be removed during the cleaning process to avoid clogging. And the flow direction of the ball valve should be switched several times to ensure that all deposits and bacterial films can be removed.
Regular sterilization
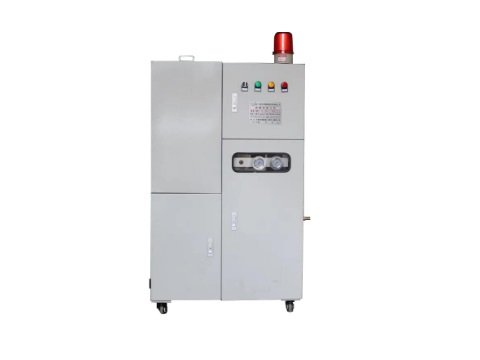
Sterilizing a release agent mixer in die casting is essential to prevent contamination. It ensures consistent release agent performance, and maintain product quality.
After flushing the system with water to neutral, the pipes were circulated and cleaned using water containing DBNPA biocide for at least half an hour. Afterwards, the piping is rinsed with deionized water to remove the biocide. It is important to note that DBNPA may cause corrosion on aluminum surfaces, so install a strainer to check for residue during subsequent rinsing steps and repeat the cleaning process if any.
When sterilization is complete, close all equipment outlets, especially ball valves, to prevent outside contaminants from entering.
Checking and replacing parts
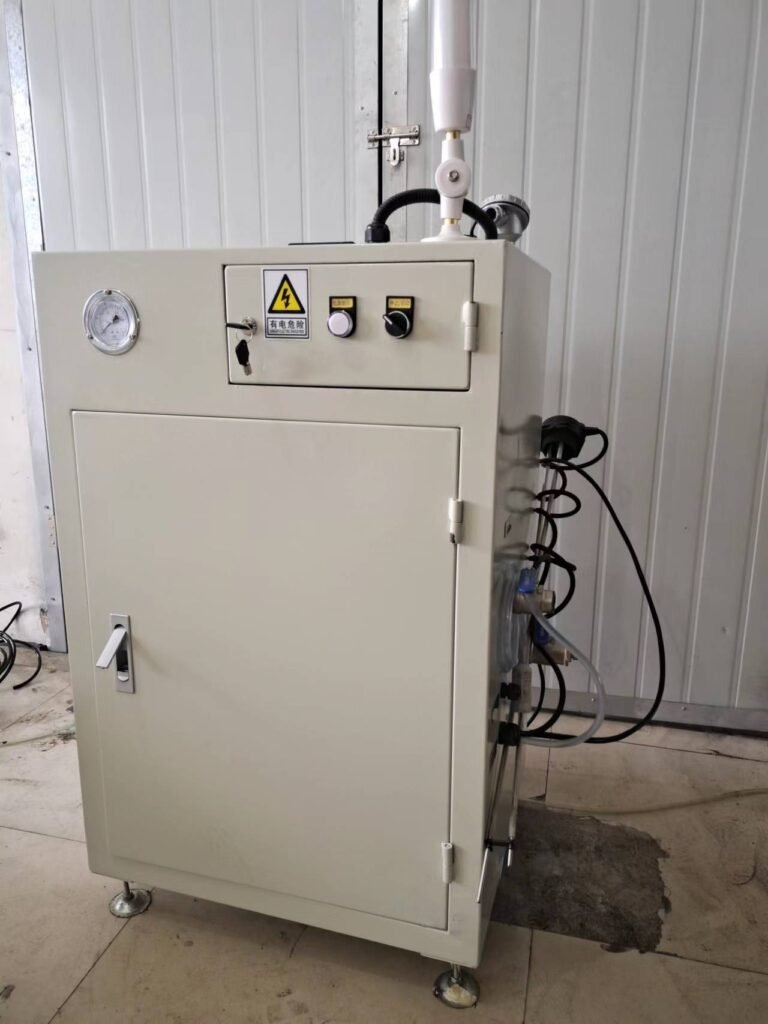
When replacing parts of the release agent mixer, the following points should be noted:
- Selecting the right parts
- Maintenance records
- Cost management
Selecting the right parts:
Select the right parts for a particular model based on the equipment manual or manufacturer’s recommendations. For example, some equipment may require parts made of high-temperature-resistant materials to accommodate mold temperatures.
Maintenance records:
After each part replacement, the date of replacement, part model and usage should be recorded for subsequent tracking and maintenance.
Cost management:
For high-value or critical parts, consider setting up an amortization account to cover the replacement cost by gradually increasing the price of the product.
Monitoring & Maintenance Systems
- Water quality monitoring
- Regular Inspection Frequency
Water quality monitoring:
If a water-based release agent is used, the water quality of the dilution water needs to be tested regularly to ensure that it meets the requirements and is free of bacteria and other contaminants.
Regular Inspection Frequency:
According to the frequency of equipment use and production needs, set a reasonable inspection cycle. For example, a comprehensive inspection should be carried out after every certain number of products produced.
For example, a comprehensive inspection is carried out after every production of a certain number of products.
Selection and proportioning of release agents
The type and proportion of the mold release agent directly affects its performance.
For example, silicone-based mold release agent because of its excellent thermal stability and lubricating properties. It is widely used in aluminum, zinc and other metals die casting. In addition, water-based mold release agent because of its environmental protection and stability is also gradually concerned, especially in aluminum alloy die casting shows good high temperature film formation ability and low corrosion. Therefore, in the choice of release agent, should be according to the specific die casting materials and process requirements for optimization of the proportion.
Role of Mold Release Agents in Die Casting
- lubrication
- isolation
- Improvement of surface quality
lubrication
Mold release agents reduce the coefficient of friction between the liquid metal and the mold by forming a thin film on the surface of the mold, thereby reducing wear and improving mold release.
For example, silicone-based and oil-based release agents have good lubricating properties at high temperatures, which can effectively reduce the adhesion of metallic fluids to the mold and improve the efficiency of mold release.
Isolation
Mold release agents can provide an isolation layer between the liquid metal and the mold surface, reducing heat transfer and improving the working conditions of the mold. For example, silicone-based release agents are widely used in aluminum die casting, especially in high temperature environments, because of their excellent thermal and chemical stability.
Improvement of surface quality
The use of appropriate mold release agents can reduce surface defects of molded parts, such as porosity and scratches. For example, water-based releasing agents are widely used in modern die casting production due to their environmentally friendly properties and their ability to regulate mold temperature.
Die casting machine supplier: Haichen Machinery
Haichen is a die casting machine factory located in Ningbo, China, mainly supplying cold chamber die casting machine and hot chamber die casting machine. Besides machines, we also supply die casting auxiliary equipments and spear parts, including mold temperature controller, conveyor, spray systems, mold temperature controllers, and industrial robots.
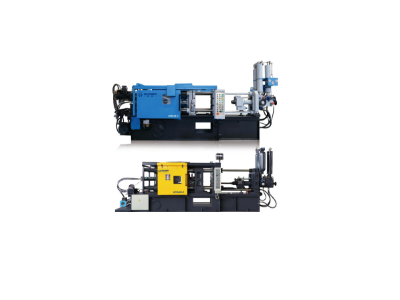
If there is any demand, welcome to consult us.