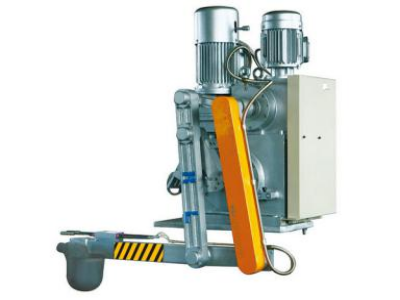
The material selection for ladle in die casting significantly impacts their performance, durability, and casting quality.
In cold chamber die casting, a ladle is used to transfer the molten metal into a cooling chamber where it is then pressed into the die using a plunger.
The ladle needs to be made of heat-resistant steel or cast iron and coated to prevent metal sticking and heat loss. In alloy die casting, manual pouring has oxidation and slag problems, and the use of coated ladles can extend the service life.
Below is an evidence-based comparative analysis of materials:
1. Traditional Metallic Materials: Heat-Resistant Steel, Cast Steel, Cast Iron
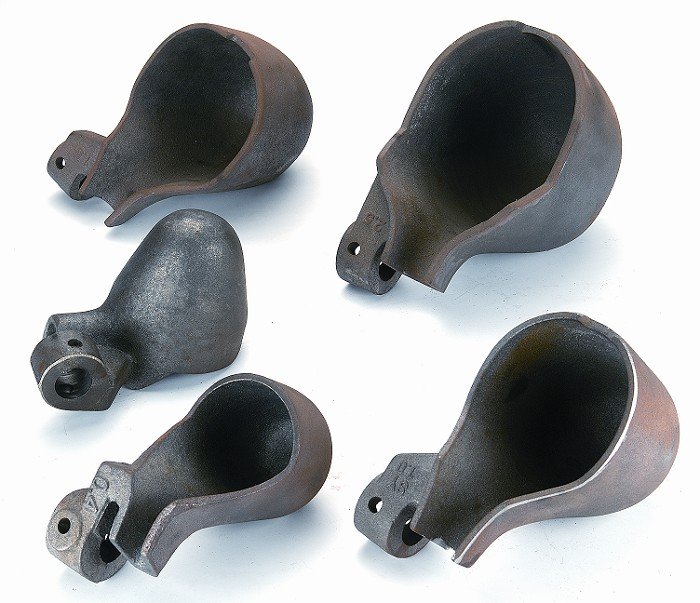
- Material Properties: Ladles are typically made from heat-resistant steel, cast steel, or cast iron, which offer high mechanical strength and thermal resistance.
- Coating Requirements: To prevent molten metal adhesion (e.g., aluminum dissolving into iron) and thermal degradation, these metallic ladles require refractory coatings (e.g., refractory concrete or specialized coatings). For example, direct contact between molten aluminum and steel ladles in aluminum die casting can cause iron contamination, making coatings essential.
- Applications: Suitable for automated die casting systems, often integrated with robots or machinery, such as molten metal transfer in cold-chamber die casting.
2. Titanium Alloys
- Innovative Design: Japanese manufacturers have developed titanium alloy (DT series) ladles, which are ultra-lightweight and long-lasting, with weights under 4 kg.
- Advantages: Titanium’s low density (~4.5 g/cm³) and high corrosion resistance reduce operator fatigue and extend tool life. Titanium alloys also exhibit low oxidation tendencies at high temperatures, making them ideal for precision casting.
- Limitations: Higher cost and the need for specialized coatings/surface treatments to prevent molten metal reactions.
3. Ceramic Materials
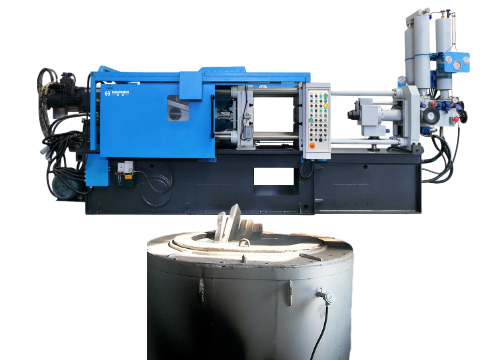
- Types: Include ceramic fiber ladles (e.g., MARUKO Corporation’s ceramic fiber ladles) and full-ceramic ladles (capacity range: 0.3–8.0 kg).
- Advantages:
- Thermal Insulation: Ceramic fibers minimize temperature loss in molten metal. For example, traditional ladles in iron casting may cause excessive temperature drop, while ceramics mitigate this issue.
- Chemical Inertness: Ceramics react minimally with molten metals, reducing impurity contamination, especially in high-purity applications (e.g., aerospace components).
- Drawbacks: High brittleness, low impact resistance, and susceptibility to damage during handling.
4. Refractory Linings
- Regardless of the ladle’s primary material, refractory linings are critical. Traditional refractory bricks are increasingly replaced by refractory concrete due to its flexibility and lower cost.
- Linings require regular maintenance (e.g., preheating and recoating) to prevent erosion and iron contamination.
5. Specialized Designs
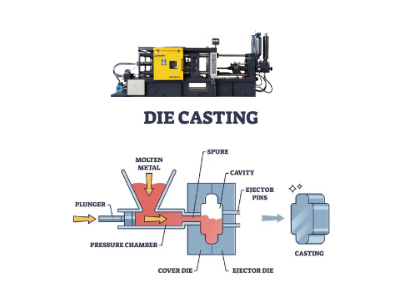
- Bottom-Pour Ladles: Feature a bottom nozzle for controlled metal flow, reducing oxidation and turbulence. Ideal for high-quality castings but complex to maintain.
- Teapot Ladles: Use an external spout to draw metal from below the surface, minimizing slag inclusion. Suitable for high-purity applications.
Comparative Summary
Material Type | Advantages | Limitations | Typical Applications |
---|---|---|---|
Heat-Resistant Steel/Cast Steel/Cast Iron | High strength, low cost, easy machining | Requires coatings, heavy weight | General die casting, automated lines |
Titanium Alloy | Lightweight, corrosion-resistant, durable | High cost, requires coatings | Precision casting, high-frequency use |
Ceramic | Excellent insulation, inert, high purity | Brittle, low impact resistance | High-temperature alloys, high-purity casting |
Refractory Linings | Protects ladle, reduces contamination | Regular maintenance (preheating, recoating) | Essential for all ladle types |
Design Optimization Trends
- Reducing Turbulence and Oxidation: Improved ladle geometry (e.g., blunting the ladle tip) minimizes splashing and oxide inclusions, enhancing mechanical properties of castings.
- Temperature Control: Optimizing ladle tilting speed balances productivity and thermal loss. For example, slow operation in aluminum die casting risks cold shut defects.
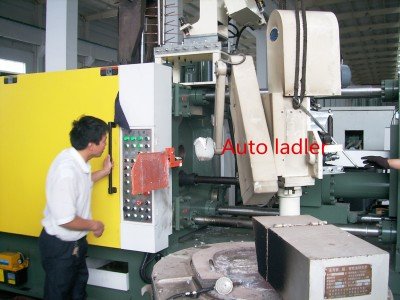
In conclusion, ladle material selection must balance process requirements (temperature, metal type), cost, and maintenance complexity. Hybrid solutions (e.g., titanium alloy ladles with ceramic linings) may emerge as a future trend.
Why ladle is used in die casting?
1. Safe Transfer of Molten Metal
- The ladle serves as a key tool for transferring high-temperature molten metals (e.g., aluminum, magnesium, zinc alloys) from the furnace to the cold chamber or shot sleeve of the die casting machine. It ensures controlled pouring to prevent splashing or spillage, enhancing operational safety.
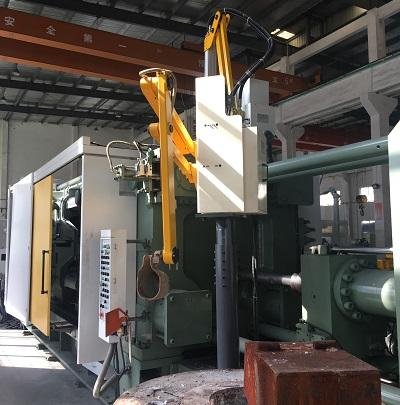
2. Compatibility with High-Melting-Point Metals
- In cold chamber die casting, metals like aluminum alloys (with high melting points) can damage sensitive machine components if directly exposed. The ladle acts as an intermediary, isolating molten metal from the machine’s critical parts, thereby extending equipment lifespan.
3. Automation and Efficiency
- Modern ladles are often integrated with robotic systems or automated mechanisms. For example:
- Automated tilting via linkage systems or linear actuators enables rapid, precise pouring.
- Sensors (e.g., electrodes) monitor molten metal levels to prevent overfilling and adjust tilt angles for consistent dosing.
- This automation minimizes cycle times and optimizes production consistency.
4. Temperature Control and Defect Prevention
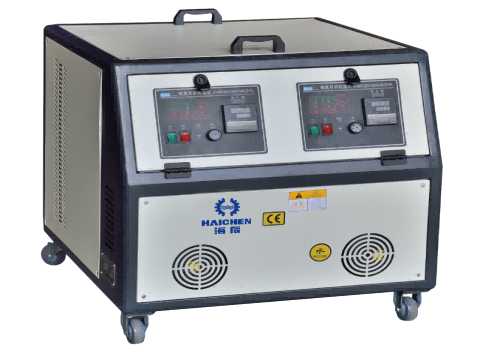
- Ladle design and operation directly affect temperature stability of the molten metal. Key measures include:
- Preheating ladles to red-hot states (e.g., using gas burners) to reduce heat loss.
- Applying ceramic coatings or refractory linings to prevent skull formation (solidified metal) and adhesion.
- Optimizing tilt speed to minimize temperature drops, avoiding defects like misruns (incomplete filling).
5. Material and Coating Adaptability
- Ladles are made from heat-resistant materials (e.g., heat-resistant steel, cast iron, or graphite-clay composites) to withstand corrosion and thermal stress.
- Specialized coatings (e.g., ceramic or Arco-Perm 100) further protect against metal adhesion and contamination. For instance, ceramic-coated stainless steel ladles are used in iron alloy casting to prevent molten iron from welding to surfaces.
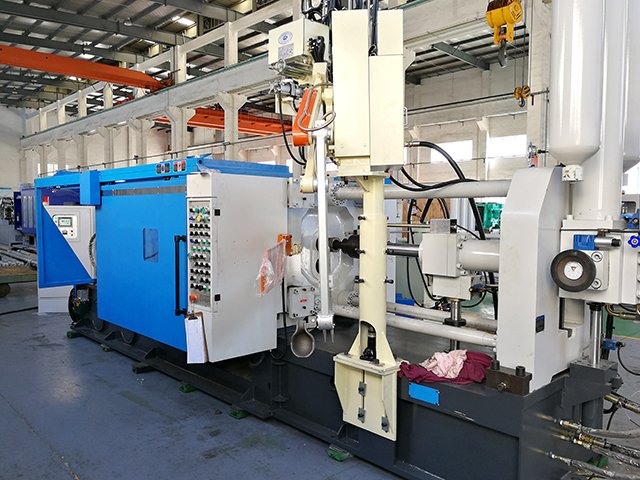
6. Process Flexibility
- Ladles enable in-process metallurgical treatments, such as:
- Degassing (removing dissolved gases) and oxide removal in aluminum alloys.
- Grain refinement (e.g., adding titanium-boron agents) or inoculation (e.g., introducing silicon-magnesium alloys to iron melts).
- These steps improve metal quality and casting performance.
7. Reduced Oxidation and Air Entrapment
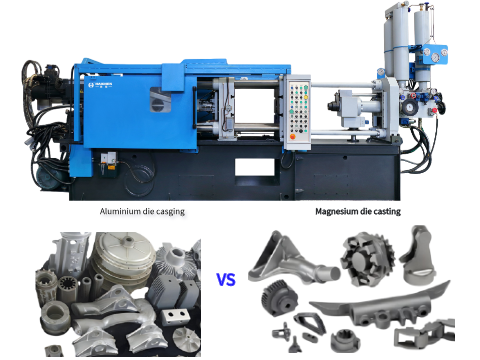
- Quick, controlled pouring minimizes exposure to air, reducing oxidation and slag inclusion risks.
- Simulation tools optimize ladle tilting behavior to ensure smooth metal flow, preventing turbulence-induced defects like gas porosity.
Overall
The ladle is far more than a simple transfer tool in die casting. Its design, materials, coatings, and operation critically influence safety, efficiency, and product quality. Whether manually operated or automated, ladles enable precise control over metal flow, temperature, and alloy integrity—making them indispensable for high-volume, precision die casting.
Automation ladle of Haichen die casting machine
Haichen Machinery, a leading manufacturer in die casting technology, integrates advanced automated ladle systems into its cold and hot chamber die casting machines. These systems are critical for achieving high precision, efficiency, and safety in modern die casting production. Below is a detailed breakdown of their design, operational workflows, and technological innovations:
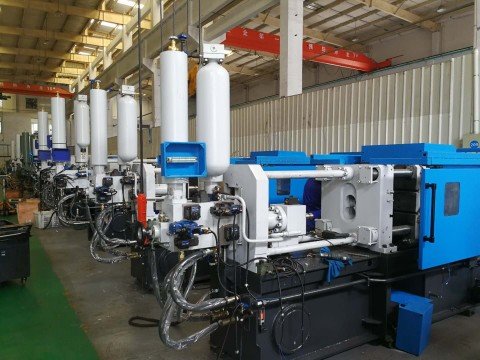
1.Design and Integration with Automation
Haichen’s automated ladle systems are engineered to work seamlessly with robotic arms, PLC controls, and real-time monitoring technologies. Key design features include:
- Linkage Mechanism with Sensors:
The ladle is mounted on a robotic arm equipped with electrodes to detect the molten metal surface in the furnace. This prevents over-immersion and ensures consistent metal pickup .- Example: A linkage mechanism (as shown in Figure 3 of ) uses a shortest-path approach to transfer molten metal from the furnace to the shot sleeve, minimizing cycle time .
- Magnetic Grating Ruler Control:
In Haichen’s HDC-C series cold chamber machines, the ladle’s tilt angle and pouring speed are controlled via magnetic grating rulers and PLC systems, enabling millimeter-level precision in metal dosing . - Ceramic-Coated Ladles:
To prevent metal adhesion and heat loss, Haichen uses ladles lined with ceramic or refractory coatings, ensuring durability and temperature stability during repeated cycles .
2.Operational Workflow
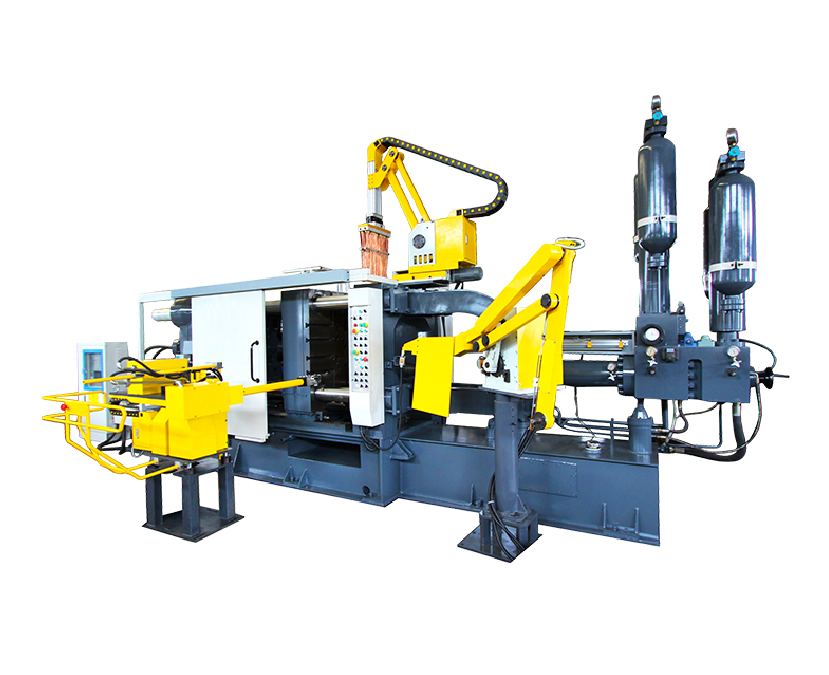
The automated ladle system follows a standardized process in Haichen’s die casting units:
- Molten Metal Pickup:
- The ladle dips into the furnace, with sensors adjusting immersion depth to avoid splashing.
- Tilt angles are dynamically controlled to regulate metal intake volume .
- Shortest-Path Transfer:
- The robotic arm moves the ladle along an optimized trajectory to the cold chamber or shot sleeve, reducing heat loss and oxidation risks .
- Precision Pouring:
- The ladle pours molten metal into the shot sleeve via a pouring hole, with flow rate adjusted by servo motors to match injection requirements .
- Self-Cleaning and Maintenance:
- Post-pouring, the ladle is automatically cleaned to remove residual metal or slag, ensuring consistency in subsequent cycles .
3.Technological Innovations
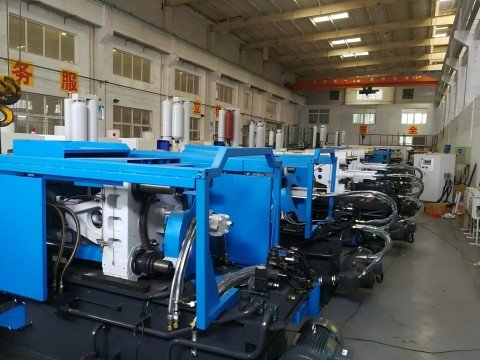
Haichen’s automated ladle systems incorporate several cutting-edge technologies:
- Real-Time Closed-Loop Control:
The HDC series uses a closed-loop control system (cycle time: 0.25ms) to monitor and adjust ladle tilt speed, metal flow, and temperature. This minimizes defects like cold shuts or gas porosity . - Integration with Servo Systems:
High-performance servo valves and pumps synchronize ladle movements with the injection unit, achieving rapid acceleration (up to 8m/s) and precise pressure control during metal charging . - Intelligent Temperature Management:
Thermocouples and 3D-printed cooling inserts in the mold work with the ladle system to maintain optimal metal temperatures (e.g., below 205°C for aluminum), preventing premature solidification .
4.Applications and Customization
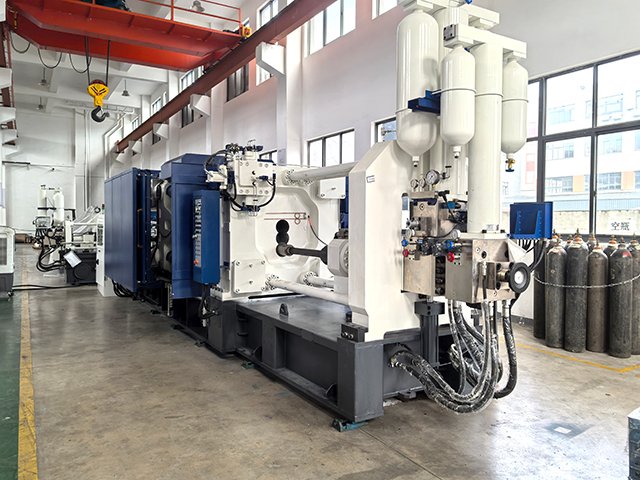
Haichen’s automated ladles are tailored for diverse production needs:
- High-Volume Automotive Parts:
Used in producing aluminum engine blocks and structural components, where consistent metal dosing is critical for weight reduction and strength . - Zinc and Magnesium Alloys:
Optional automatic ladlers in Haichen’s HCD-H series hot chamber machines enable cost-effective production of small parts like door handles, with dosing accuracy down to 1.6 kg per shot . - Custom Automation Lines:
Haichen offers modular configurations, integrating ladles with auxiliary equipment (e.g., automatic sprayers, extractors) to form fully unmanned production cells .
5.Advantages Over Manual Systems
- Safety:
Eliminates manual handling of molten metal, reducing burn risks and exposure to hazardous fumes. - Efficiency:
Reduces cycle time by 20–30% through optimized transfer paths and automated adjustments . - Quality Consistency:
Real-time monitoring and closed-loop controls ensure repeatable metal dosing, minimizing scrap rates . - Energy Savings:
Servo-driven systems reduce hydraulic oil consumption by 15–25%, aligning with Haichen’s eco-friendly production goals .
6.Case Study: Automotive Aluminum Casting
In a production line for automotive crankcases:
- Haichen’s 1300T cold chamber machine uses an automated ladle to transfer 17.5 kg of molten aluminum per cycle.
- The system achieved a defect rate of <0.5% through precise temperature control and rapid pouring, validated by real-time PLC analytics .
7.Future Trends
Haichen is advancing its ladle systems with:
- AI-Driven Predictive Maintenance:
Machine learning algorithms analyze ladle wear patterns and predict failure points, reducing downtime. - Hybrid Hot/Cold Chamber Compatibility:
Developing universal ladle systems for multi-alloy production lines (e.g., switching between zinc and aluminum without hardware changes) .
Conclusion
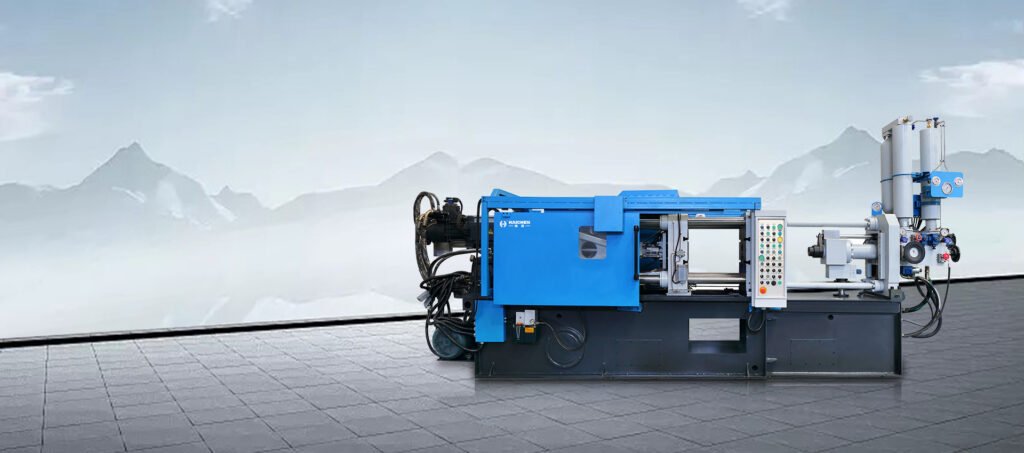
Haichen’s automated ladle systems exemplify the integration of precision engineering, real-time controls, and robotics in die casting.
By optimizing metal transfer accuracy, temperature stability, and production speed, these systems are pivotal for manufacturers aiming to scale high-quality, cost-effective die casting operations.
For technical specifications or customization inquiries, Haichen provides dedicated engineering support to tailor solutions to specific production needs