Die casting machine open stroke is the distance the moving die (or part of the die) moves from one position to another during the die casting process.
This stroke is usually associated with the opening and closing action of the die and is an important parameter in die casting machine operation.
During the die casting process, the opening and closing action of the moving and fixed dies is controlled by a hydraulic system. When the die casting machine starts to work, the moving die will move towards the fixed die and close the die to form a closed mold cavity into which the molten metal will be injected. After the metal has cooled and solidified, the movable die moves again and opens the mold so that the casting can be removed.
The exact value of the open stroke depends on the design of the die casting machine and the structure of the die. For example, in some cases, open stroke may need to be adjusted to the size and shape of the die to ensure that the die opens and closes properly. In addition, the open stroke may also be affected by the travel of the die clamps, which need to provide sufficient clamping force to maintain the stability and accuracy of the die.
The significance of the application of open stroke :

In die casting machines, the open stroke is the distance the mold moves when it opens. This parameter is critical to ensure product quality and productivity. Here are some important applications and implications of open stroke:
- Ensure smooth product release: Sufficient mold opening stroke ensures that the product can be completely removed from the mold cavity after the mold is opened, avoiding damage to the product or damage to the mold.
- Affect the production cycle: the size and control accuracy of the mold opening stroke directly affects the entire die casting cycle. Ideal mold opening stroke can reduce the non-productive time in production and improve the production efficiency.
- Mold design and protection: Reasonable opening stroke can reduce mold wear and prolong the life of the mold. Smooth movement of the mold during opening and closing helps reduce shock and stress.
- Adapt to the production of different products: different products may require different open mold stroke. The die casting machine is able to adjust the die opening stroke to adapt to the production needs of different products.
- Improve the level of automation: in the automated die casting production line, accurate control of the opening stroke of the mold is very important for the realization of automated pickup and subsequent processing.
- Reduced post-processing work: By precisely controlling the opening stroke of the mold, it is possible to reduce the post-processing work required after the product has been taken out of the mold, such as trimming and sanding.
- Energy saving and environmental protection: Optimizing the opening stroke reduces energy consumption, as unnecessarily large strokes increase the energy consumption of the machine.
How to calculate the open stroke required for die casting products?
To calculate the required open stroke for an die casting product, several key factors need to be considered, including the size of the mold, the size of the product, the way the mold opens and closes, and the capabilities of the die casting machine. Below are some basic steps and formulas for calculating the required open stroke:
- Determine the maximum dimensions of the product: this includes the height, width and depth of the product.
- Calculate the opening distance of the mold: this usually needs to be at least equal to the maximum size of the product so that the product can be released from the mold.
- Consider space for ejector mechanism: If the mold has an ejector mechanism (used to push the product out of the mold), additional space is required to ensure that the ejector mechanism can be fully extended.
- Consider the safety distance of the mold: In order to ensure that the mold does not collide when it is opened, a certain safety distance is usually added to the calculated stroke.
- Calculation using the formula: If the maximum thickness of the mold when closed (lc) and the maximum size of the product (l) are known, the following formula can be used to estimate the required mold opening stroke:
Mold opening stroke = Maximum thickness of the mold when closed – Maximum size of the product
- Consider the mold design: Sliders, tilting jacks, and other mechanical devices in the mold design can also affect the required mold opening stroke.
- Check the specifications of the die casting machine: Ensure that the selected die casting machine has sufficient open stroke to meet the needs of the mold.
- Simulation using CAE software: For complex mold designs, simulation using CAE (Computer Aided Engineering) software can help to more accurately calculate the required opening stroke.
The open stroke of Haichen machine
Below is the parameter table of our brand die casting machine, you can find all of them in our full range of catalog.
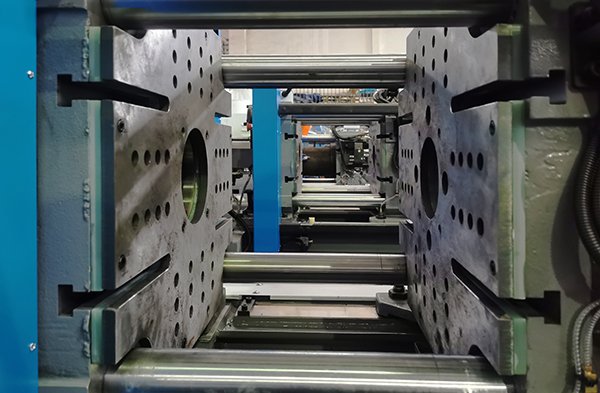
You can check the die stroke of each of our die casting machines against the table, and you can match the die casting machine with different die stroke according to the design requirements of your own products. If you need more similar technical support, please leave a message to us, we are ready to ask you to do the program calculation.