The purpose of die casting machine platen: the opening and closing of the die through the combination of the moving die plate, the fixed die plate and the tail plate.
It is an important functional component and main load-bearing part of the die casting machine. During the die casting process, the die plate system ensures the precise closing and opening of the die. So that the molten metal can be smoothly injected into the die cavity and solidified under high pressure.
The platen also works with other components of the die casting machine. Such as the ejector mechanism and the reset mechanism, to ensure that we can ejected and removed the casting smoothly. During the die casting process, the parallelism and accuracy of the template directly affect the dimensional accuracy and surface quality of the casting. Therefore, the design and manufacture of the template need to consider many factors to ensure the smooth progress of the die casting process and the production of high-quality castings.
How the role of a platen in die casting machines for supporting and connecting molds with the machine?
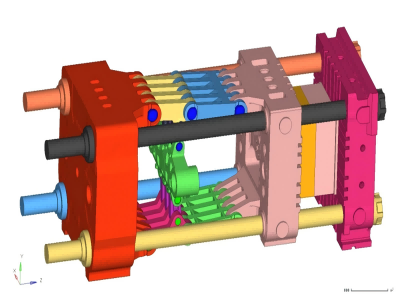
In the die-casting process, the platen is an important functional component and a main load-bearing part. Its functions and roles mainly include the following aspects:
Carrying and fixing the mold:
The platen is used to carry and fix various parts of the mold to ensure that the mold can work stably during the die-casting process. The platen system usually includes a movable platen, a fixed platen and a tail platen. These components work together to ensure the structural integrity and stability of the mold
Support and guide:
The platen plays a supporting and guiding role in the die-casting process. For example, the fixed mold is fixed on the fixed mold plate of the die-casting machine, while the movable mold is fixed on the movable mold base plate of the die-casting machine, and the mold opening and closing actions are realized through the mold opening mechanism. In addition, the template is also used to support parts such as guide pins or guide sleeves in the mold to prevent them from shifting under the molding pressure
Molding and exhaust:
The platen is provided with a cavity to form the outer contour of the casting. At the same time, the exhaust groove on the template is used for exhaust during the metal liquid filling process to reduce air entrainment and vortex and improve the quality of the die-casting
Cooling and ejection:
The platen is also equipped with a cooling water pipe to cool the mold to control the solidification speed and quality of the casting. In addition, the ejector device is used to eject the casting from the moving mold and remove it for subsequent processing.
Increase the service life of the mold:
Reasonableplaten design can increase the service life of the mold. For example, the template made of forged steel material is harder than the cast iron template, and the connection surface is tighter, thereby extending the service life of the mold.
Optimized design:
In order to reduce the quality and cost of the template, we design the structural topology optimization based on the variable density method. We optimize through software to achieve better performance and economy for the fixed template, tail plate and moving template.
What is the protective function of a platen in die casting machines ?
The protection function of die-casting machine template mainly includes low-pressure clamping protection function, three-stage clamping and low-pressure clamping protection, over-stress protection mechanism, automatic lubrication system and safety facilities.
Low-pressure clamping protection:
By optimising the low-pressure clamping protection, we can extende the service life of the mould. This design is usually based on Finite Element Method (FEM), which ensures even stress distribution in the die plate, improves the closing accuracy, and makes the die plate more durable and less prone to deformation.
Three-stage clamping and low-pressure clamping protection:
Through the cooperation of computer and proportional oil circuit, three-stage clamping can be achieved to ensure the protection function in the low-pressure clamping stage, which can effectively protect the template and mould.
Overstress protection mechanism:
Some die-casting machines are equipped with overstress protection mechanism, which can effectively protect the tie rods when the force of the mould is unbalanced, thus significantly prolonging the service life.
Automatic lubrication system:
The use of automatic lubrication system, can reduce mechanical wear and improve the stability and service life of the equipment.
Safety facilities:
Multiple safety facilities, including safety doors and light curtain switches, ensure the safety of operation.
These protective features work together to ensure that the die casting machine can maintain high efficiency and stability during operation and maximise the service life of the template and mould.
The purpose of die casting machine platen about Haichen

The advantages of Haichen’s Adaptive Clamping Force Adjustment Technology include: the function of adaptive clamping force adjustment, more uniform clamping force distribution, the use of high elongation and weldable materials for the clamping contact plate, shortening of the dry cycle period, and closed-loop control.
Adaptive clamping force adjustment function:
This technology can adjust the clamping force in real time according to the actual situation in the production process, so that the clamping force can be better adapted to different production needs, improve production efficiency and product quality.
Clamping force distribution is more uniform:
Through the adaptive adjustment of clamping force, it can ensure that the force of the mould is uniform in the clamping process, thus improving the quality and consistency of the product.
Use of high elongation and weldability materials for the clamping contact plate:
This choice of material not only improves the durability of the clamping contact plate, but also enhances its stability in high temperature and high pressure environments, thus extending the service life of the equipment.
Shortening of dry cycle times:
By redesigning, replacing or optimising several components, such as the optimisation of the parameters of the ‘fast mould transfer’ cylinders, the entire mould transfer operation is made faster, thus shortening the dry cycle time and increasing productivity.
Closed-loop control:
Through adaptive closed-loop control, the machine can adjust the high-pressure clamping position and pressure in real time according to the clamping pressure of the previous mould to ensure the accuracy and consistency of each clamping.
Haichen Adaptive Clamping Force Adjustment technology significantly improves the performance and product quality of the injection moulding machine through the advantages of uniform clamping force distribution, real-time clamping force adjustment, the use of high-performance materials, closed-loop control and optimized component design.
The purpose of die casting machine platen is to control the mold opening and closing. It is the main function of the machine platen.