Selection Guide for Mold Temperature Controller in die casting includes mold temperature, design and optimize cooling system, temperature control technology, etc.
What is mold temperature controller in die casting?
Mold Temperature Controller is a device used to accurately control the temperature of the mold in die casting. Its main purpose is to ensure the quality and production efficiency of the casting by adjusting the cooling or heating process of the mold. The mold temperature has an important influence on the internal structure, surface quality and mold life of the die casting.
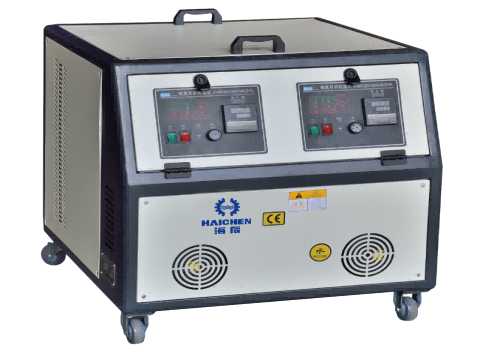
When selecting a temperature controller for a die casting mold, you need to consider multiple factors, including the impact of mold temperature on product quality, the optimal design of the cooling system, and the advancement of temperature control technology. The following is a detailed explanation of several key aspects:
Selection Guide for Mold Temperature Controller in die casting: Importance of mold temperature
In the die casting process, the control of mold temperature is very important, which directly affects the quality of castings, production efficiency and the service life of the mold.
The stability of mold temperature can ensure the fluidity and filling of molten metal in the mold cavity, thereby reducing defects such as cold closure, pores, shrinkage and surface defects.
In addition, mold temperature that is too high or too low will cause deformation of castings, sticking of molds, shortened mold life and other problems.
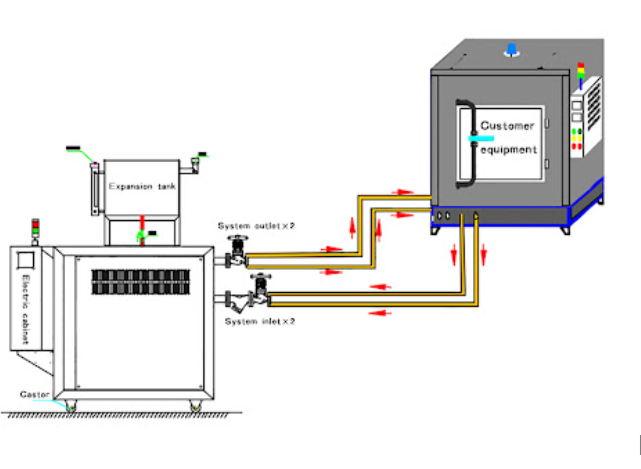
Selection Guide for Mold Temperature Controller in die casting: Design and optimization of cooling system
- Precise temperature control
- Optimization design of cooling system
- Multiple cooling options
- Precise temperature control: Mold temperature has a significant impact on the quality of die castings. The integrated mold temperature control system enables real-time monitoring and precise control of mold temperature. For example, using a closed-loop control system, when the mold temperature exceeds the set value (such as 205°C), the system automatically opens the cooling water solenoid valve to adjust the temperature, thereby improving the stability of casting quality.
- Optimization design of cooling system: The design of cooling system directly affects the cooling speed and quality of die castings. Reasonable cooling channel layout, cooling water flow and temperature regulation are key. For example, by determining the key cooling area of the mold cavity through CAE analysis and adopting single-point independent control technology, shrinkage defects can be effectively reduced and production efficiency can be improved.
- Multiple cooling options: Depending on the material characteristics and production requirements, you can choose water cooling, oil cooling or air cooling. For example, water-cooled mold temperature controllers are suitable for most alloys, while oil cooling is suitable for occasions that require higher heat conduction efficiency.
The cooling system is the core part of mold temperature control. Traditional cooling channel layout has the problem of inefficiency. And topology optimization technology has been proven to significantly improve cooling effects. By optimizing the location and shape of cooling channels, it can achieve a more uniform temperature distribution . And reduce thermal stress and the formation of shrinkage holes.
For example, studies have shown that the closer the cooling channel is to the casting surface, the better the cooling effect, but too close a distance may cause thermal stress concentration in the mold material.
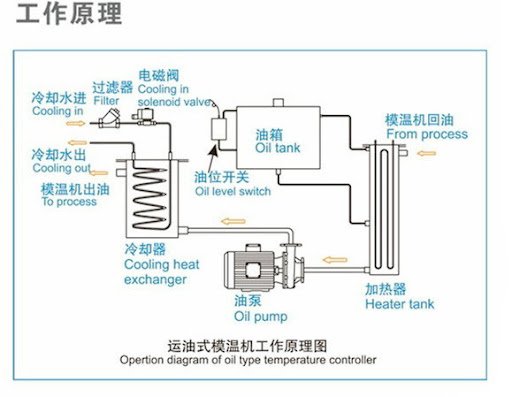
Selection Guide for Mold Temperature Controller in die casting:Choice of temperature control technology
- Water cooling system
- Oil cooling system
- Heat pipe technology
Water cooling system: Water cooling system widely uses due to its fast response and efficient heat dissipation capabilities. By installing temperature sensors and flow controllers, can monitor the flow of cooling water and adjust in real time. Thereby accurately controlling the mold temperature.
Oil cooling system: The oil cooling system is suitable for application scenarios that require a higher temperature range (360°C to 380°C). The oil cooling system has better temperature control accuracy and resistance to thermal shock, and is especially suitable for local temperature control in complex mold areas.
Heat pipe technology: Heat pipe is an efficient heat transfer device that can quickly transfer heat from the mold surface to the external cooling system. Studies have shown that heat pipe technology can significantly improve cooling efficiency and reduce energy consumption, but its structural fragility needs further improvement.
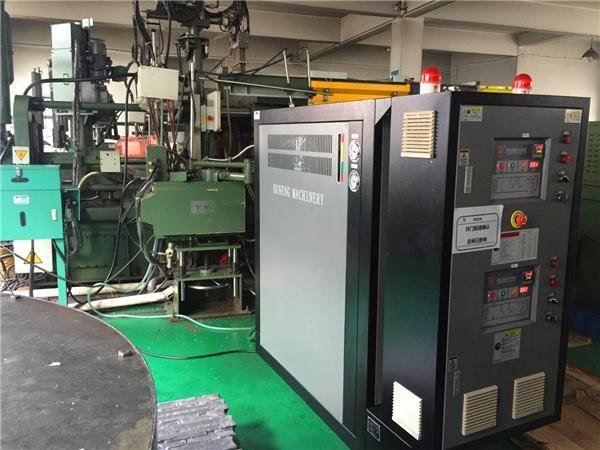
Real-time monitoring and intelligent control
Modern mold temperature controllers usually equippes with multi-channel temperature sensors and real-time monitoring systems, which can record and analyze temperature changes in various parts of the mold. For example, the TP700-16/TP700-40 multi-channel temperature tester can display the mold temperature curve in real time, and combine it with the production status through the curve chart to help operators quickly adjust the process parameters.
Optimization of process parameters
Mold preheating temperature and pouring temperature have an important impact on product quality. Studies have shown that the preheating temperature of fixed molds usually sets to 200°C, while the preheating temperature of movable molds is 220°C. These parameters have been verified by multiple tests and can effectively improve the dimensional accuracy and surface quality of castings.
Application of innovative technologies
With the development of 3D printing technology, the design of cooling channels inside molds has become more flexible. The cooling structure generated by topology optimization not only reduces material waste, but also improves cooling efficiency. In addition, the temperature distribution measurement method based on infrared imaging also provides new possibilities for mold temperature control.
When selecting a temperature controller for die casting molds, you should consider following:
Ensure that the mold temperature controlles within the optimal range of 150°C to 250°C.
Adopt advanced cooling system design (such as topological optimization of cooling channels) to improve cooling efficiency.
Choose the appropriate cooling medium (water cooling, oil cooling or heat pipe) according to specific needs.
Equip with a real-time monitoring system for precise temperature control.
Combining process parameter optimization and innovative technologies (such as 3D printing and infrared imaging) to further improve product quality and production efficiency.
Haichen die casting machine
Haichen is one Chinese die casting machine manufacturer for more than 10years. We produce both high pressure cold chamber die casting machine , hot chamber die casting machine and spare parts. They have durable and highly precise features.
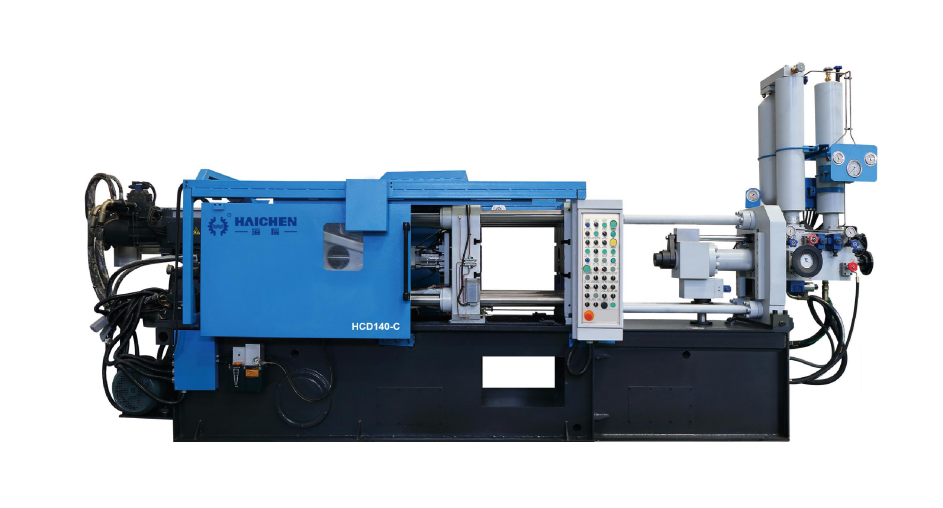
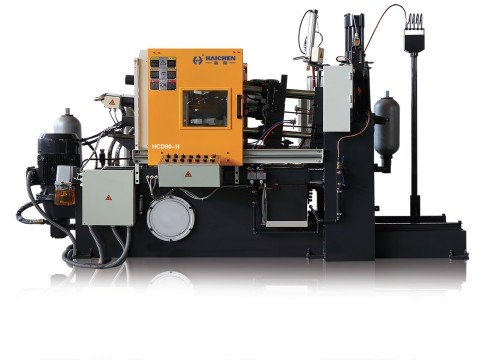
Haichen also produce die casting machine auxiliary equipment. Such as conveyor, vacuum machine, mold temperature controller, industrial robot, sprayer and so on.
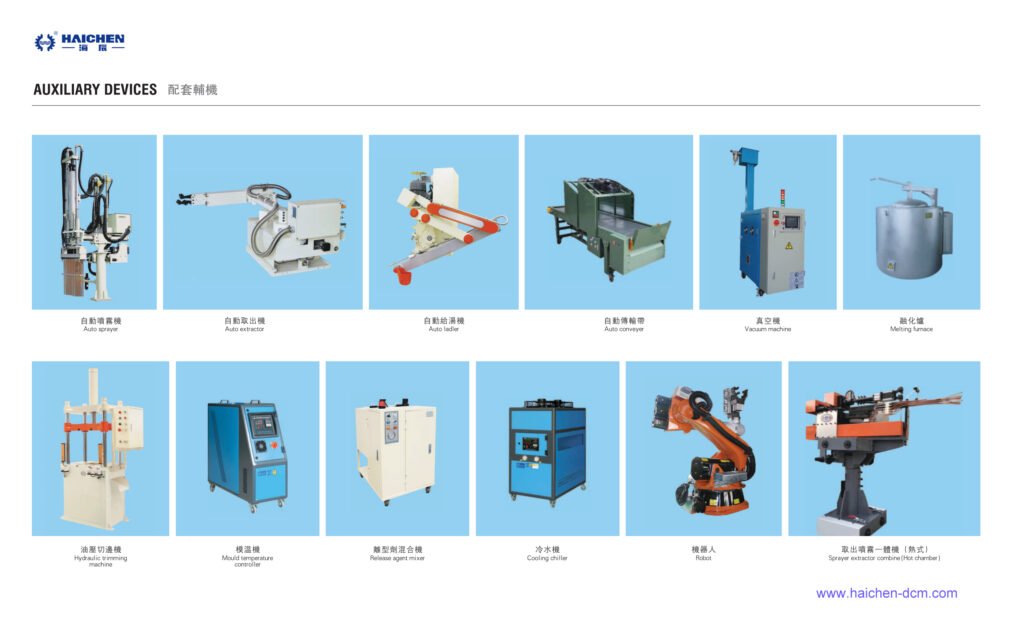
We supply cold chamber and hot chamber die casting machine spare parts.
Welcome contact us.