Ladle in die casting process undertakes the functions of transporting and pouring molten metal.
And its technical parameters directly affect the quality of castings and production efficiency.
By holding molten steel, die-cast ladles in low-pressure casting thereby apply gas pressure, thus injecting the metal into the mold.
Their heat preservation performance and sealing property are of vital importance.
Meanwhile, ladles are not only used to hold molten steel during the steelmaking process.
But also involve refining functions such as deoxidation, alloying, and temperature adjustment, and even play a key role in secondary refining technology.
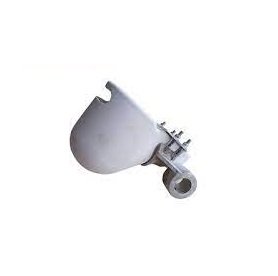
Structural design and material properties
Structural composition
Die-cast steel ladles are usually composed of outer shells, inner linings, riser pipes, sealing devices, etc.
The inner lining adopts a multi-layer design, including an insulation layer lightweight clay brick or high-temperature insulation felt.
A permanent layer high alumina or magnesia-carbon brick, and a working layer aluminum-magnesia-carbon brick, corundum spinel castable, etc.
The working layer needs to be in direct contact with the high-temperature molten metal.
And must possess high resistance to erosion, thermal shock and slag erosion.
Key materials
High-temperature resistant materials: Common materials include H13 die steel, SKD61, 8407 and other alloy steels.
Which are suitable for high-temperature and high-pressure environments.
Stainless steel (such as 3Cr13, 4Cr13) is used for corrosion-resistant components.
Refractory lining
The working layer primarily consists of corundum-spinel castable (Al₂O₃+MgO≥95%).
Additionally, the slag line zone employs magnesia-carbon bricks (C%≤10).
Furthermore, to enhance erosion resistance, the bottom impact zone incorporates precast refractory blocks.
Sealing material
High-temperature resistant silicone or metal sealing parts are required to ensure the airtightness of the steel ladle and reduce heat loss.
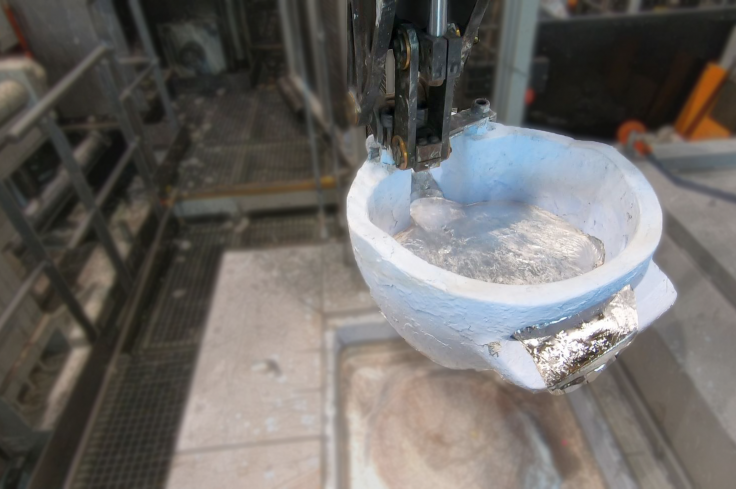
Capacity and size parameters
Standard capacity range
According to the industry standard (YB/T 6168-2024), the conventional ladle capacity is 100-400 tons and is suitable for large-scale steelmaking scenarios.
Small steel ladles have a capacity as low as 21 tons, and they find application in special processes or laboratory environments.
Furthermore, when designing these ladles, engineers must reserve a 10% overloading allowance.
For example, the actual maximum loading capacity of a steel ladle with a rated capacity of 250 tons is 275 tons.
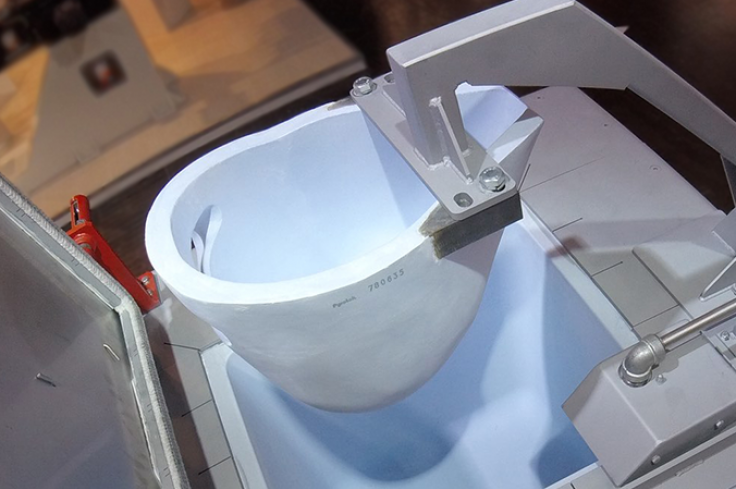
Size ratio
The height-to-diameter ratio is usually close to 1:1.
And the taper is controlled at 0.11 to 0.14 to optimize heat distribution and reduce heat dissipation.
The diameter of the large ladle shell can reach 4.7 meters, the height is approximately 5 meters, and it can hold 300 tons of molten steel.
Working temperature and thermal management
Temperature range
Molten steel temperature
During casting, the internal molten steel temperature should be maintained at around 1600℃.
And the temperature fluctuation during the holding pressure stage should be less than ±20℃.
Shell temperature
Since the creep temperature of common carbon steel ranges from 300℃ to 350℃, operators must strictly control the casing’s surface temperature below 300℃ to prevent creep deformation of the steel shell.
Refractory layer temperature
The working layer temperature can reach below 800℃, and the permanent layer temperature is below 600℃.
Requirements for thermal insulation performance
By optimizing the insulation layer (such as adding high-temperature insulation felt).
The maximum temperature of the cladding can be reduced by 54℃, significantly improving the insulation efficiency.
The formula for calculating heat loss needs to take into account the thermal conductivity of the material (such as λ=0.185 W/m·K for corundum material) and the steady-state heat transfer model.
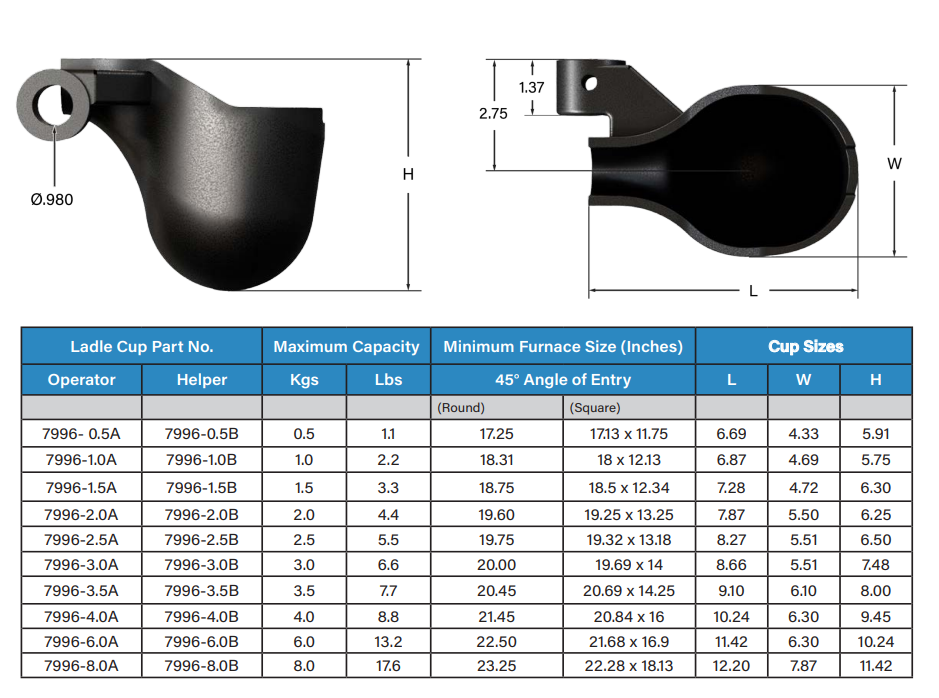
Pressure resistance and mechanical properties
Pressure resistance strength index
Spout seat brick: Compressive strength ≥50 MPa (110℃×24h), volume density ≥3.0 g/cm³.
Castable: For example, the compressive strength of AM-2 type castable is ≥40 MPa (1500℃×3h), and the load-softening temperature is ≥1600℃.
The overall pressure resistance of the ladle: It needs to withstand the pressure of the gas pressurization system (usually 0.2 to 0.5 MPa) and the static pressure of the molten steel.
Erosion resistance and thermal shock resistance
The slag line section should be resistant to the scouring of molten steel circulation (with a flow rate of up to 5 m/s).
And magnesia-carbon bricks or high-chromium steel (Cr12MoV) should be used.
The thermal shock resistance requirement is that the material should not crack under rapid cooling and heating.
Which is verified through thermal shock tests (1100℃ water cooling cycle ≥20 times).
Maintenance and servicing requirements
Daily maintenance
Cleaning and inspection
Clean up metal residues and oil stains daily, and check for blockages in seals and riser pipes.
Lubrication system
The automatic lubrication device needs to be replenished every 8 hours, with a focus on lubricating moving parts such as the elbow and guide column.
Regular maintenance
Hydraulic system
Replace the hydraulic oil and clean the filter element every 2000 hours.
Check the sealing performance of the oil pipe joint every six months.
Refractory layer repair
Inspect the lining thickness every 30 to 100 cycles.
If the wear at the slag line exceeds 50%, local repair is required.
Pressure resistance test
During the annual major overhaul, a gas tightness test is conducted (pressurized to 0.6 MPa and maintained for 30 minutes without leakage).
Special maintenance
Baking system
Newly built steel ladles should be baked in a curve (initial temperature ≤100℃, gradually rising to 800℃ within 24 hours) to prevent the refractory materials from cracking.
Thermal state monitoring
Real-time tracking of the temperature field of the liner through temperature sensors.
And adjustment of heating power to maintain thermal balance.
Safety and environmental protection requirements
Safety specification
Operators must first establish isolation zones in the ladle hoisting area and wear high-temperature resistant protective equipment.
Furthermore, in case of emergency, they can activate the tipping device to rapidly discharge residual molten steel, thereby avoiding potential explosions.
Environmental protection indicators
To comply with industrial emission standards, the dust removal system must capture over 95% of smoke dust and maintain an emission concentration below 20 mg/m³ .
Additionally, waste refractory materials require systematic classification and recycling to align with circular economy principles.
For instance, magnesia-carbon bricks can undergo crushing and grading processes to serve as slag modifiers or raw material substitutes in steelmaking.