Hot Chamber Die Casting Fundamental is an efficient and high-precision metal casting process that is mainly used for the forming of low-melting alloys such as zinc, tin, lead, and magnesium-based alloys.
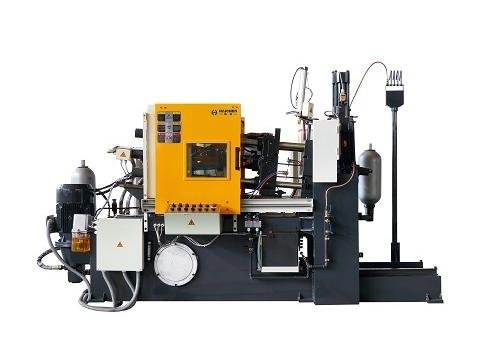
Hot Chamber Die Casting Historical Milestones
1849
J.J. Sturgiss builds the first manual piston hot chamber die casting machine for lead casting.
Laying the foundation for the process.
1915
The first commercial production of aluminum alloy die castings in the United States.
But due to the problem of material corrosion, the hot chamber machine mainly turned to zinc alloy.
1992
Toyo Machinery of Japan developed a hot chamber die-casting machine for vertical aluminum.
Breaking through the bottleneck of high melting point alloy application.
21st century
Popularization of automation and computer control technology to optimize cycle times (3000–7000 cycles/8 hours for small machines).
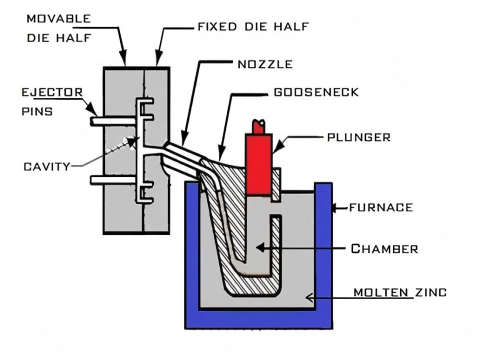
Hot Chamber Die Casting Key Features
Hot Chamber Integration
The molten metal is always stored in the furnace connected to the die casting machine.
Without the need for external transfer, reducing heat loss and oxidation risk.
Gooseneck Injection System
A piston is used to drive liquid metal through a gooseneck tube into the mold, ensuring a fast, continuous flow of metal.
Low melting point material adaptability
Only suitable for alloys with melting point lower than 420°C to avoid corrosion of equipment components at high temperatures.
Hot Chamber Die Casting Fundamental
Metal melting
The furnace is built into the die casting machine, and the metal remains liquid at a temperature below about 400°C generally.
Injection stage
In general,the piston sucks the molten metal into the chamber through the gooseneck and injects it into the mold at high pressure (7-35 MPa).
Cooling & Demolding
A cooling system inside the mold quickly solidifies the metal, after which the ejector pin pushes out the molded part.
The cycle time of this process is only about 20 minutes, which is suitable for high-volume production.
Applicable material type
Zinc alloy (Zamak series) Advantages
Melting point of only 380-390°C , excellent flowability, suitable for delicate small parts (e.g. electronic connectors) correspondingly.
Magnesium alloy (e.g. AZ91) Characteristics
Density 1.8 g/cm³, high specific strength, excellent electromagnetic shielding performance eventually.
Applications
laptop shells, drone frames. Lead/tin alloy Uses: nuclear radiation shielding parts, battery plates (gradually replaced).
Limitations
Copper alloys (e.g., brass) are occasionally used, but furnace temperatures need to be controlled to prevent equipment corrosion.
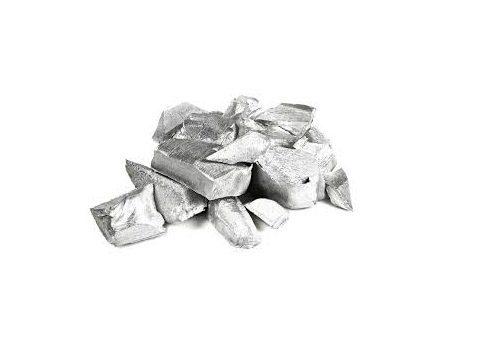