Thermocouple Types for Die Casting
In die casting, thermocouple selection depends on temperature range, environmental resistance, and measurement accuracy. Key types and their applications are outlined below:
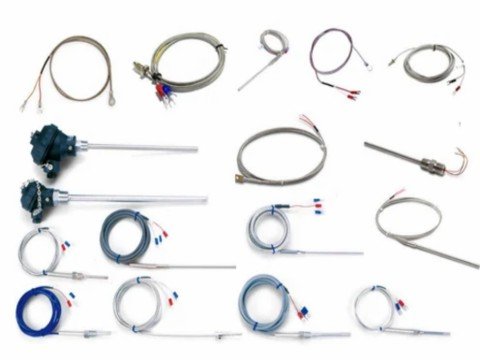
1. Type K Thermocouple (Nickel-Chromium/Nickel-Alumel)
- Core Applications:
Type K is the most widely used thermocouple in die casting. Industrial die-casting machines (e.g., automotive part production) often deploy up to 65 Type K thermocouples to monitor critical zones: mold tops/bottoms, castings, cooling channels, and molten metal interfaces. Its broad temperature range (0°C to 1260°C) suits both mold and molten metal monitoring. - Design Features:
Ruggedized with die-cast alloy heads (IP67-rated) or cast-iron housings for harsh environments. Miniature heads (0.125–0.313″ diameter) fit tight spaces, while heavy-duty variants withstand mechanical stress. - Performance:
Stable in oxidizing/inert atmospheres, fast response (e.g., OMEGA 5TC-TT-KI-30 achieves millisecond-level readings), and cost-effective.
2. Type N Thermocouple (Nicrosil/Nisil)
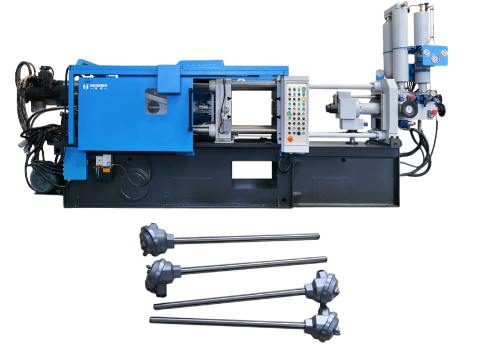
- High-Temperature Alternative:
Type N serves as a cost-effective substitute for Type K in applications below 1100°C. It outperforms Type K in resisting thermal cycling fatigue, ideal for long-term stability. - Use Cases:
Common in budget-sensitive or moderate-temperature die-casting setups, such as cooling channel monitoring.
3. Type S/R Thermocouples (Platinum-Rhodium)
- Extreme Temperatures:
Designed for molten metals exceeding 1400°C (e.g., specialty alloys). Type S (Platinum-10% Rhodium/Platinum) handles up to 1700°C but requires high-purity alumina protection tubes. - Limitations:
High cost and low mechanical strength; reserved for scenarios where standard thermocouples fail.
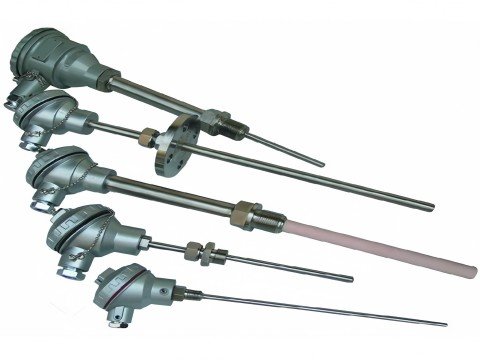
4. Type T Thermocouple (Copper/Constantan)
- Low-Temperature Monitoring:
Suitable for mold preheating or auxiliary systems (e.g., cooling water), operating from -200°C to 350°C. High sensitivity and corrosion resistance make it ideal for secondary measurements.
5. Other Types
- Type J (Iron/Constantan):
Performs well in reducing atmospheres but prone to oxidation; rarely used in die casting. - Type E (Nickel-Chromium/Constantan):
Highest sensitivity but limited high-temperature performance; mainly for lab environments.
Critical Design Considerations
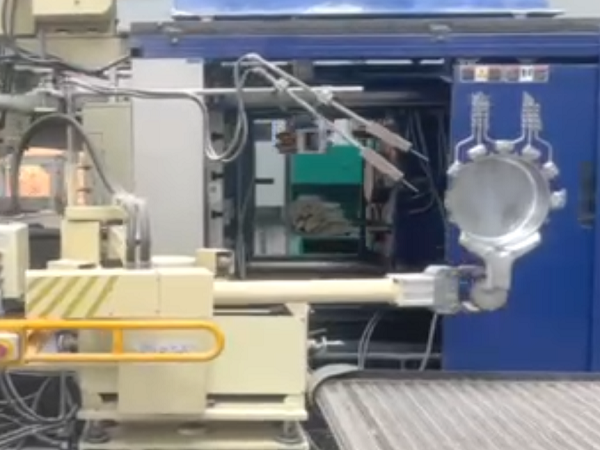
- Installation:
Thermocouples must be positioned close to mold cavity surfaces (e.g., 0.0139″ gap) to capture rapid temperature fluctuations. Pre-embedded units or steel sleeves ensure secure placement. - Protection:
Alumina sheaths (rated to 1700°C) or Inconel tubes prevent molten metal corrosion. Steel clamps enhance mechanical stability. - Redundancy:
Dual thermocouple arrays (e.g., six redundant sensors) improve data reliability. Inverse heat-transfer models can calibrate surface temperatures.
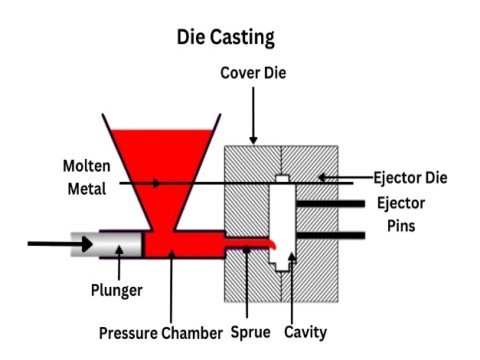
Summary
Type K thermocouples dominate die casting due to their versatility, cost efficiency, and proven industrial performance. For extreme temperatures (>1400°C), Type S/R or Type N may supplement. Final selection should align with process parameters (alloy melting point, cooling rates) and budget constraints.
Working Principle of Thermocouples for Die Casting
Thermocouples are applied in die casting based on the thermoelectric effect, enabling precise mold temperature measurement for process optimization. Below is a detailed breakdown of their operational mechanisms:
1. Fundamental Thermoelectric Principles
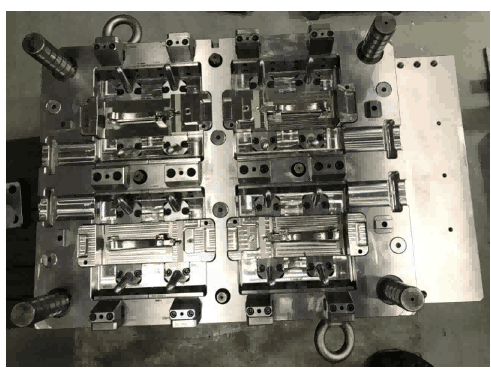
- Seebeck Effect
When two dissimilar metal conductors (e.g., copper-constantan) are welded to form a closed circuit, a temperature difference (TT and T0T0) between the two junctions generates a thermoelectromotive force (EE). Discovered by Thomas Seebeck in 1821, this phenomenon underpins thermocouple temperature sensing. The mathematical expression is:
Et=e(t)−e(t0)Et=e(t)−e(t0)where tt is the measuring junction temperature and t0t0 is the reference junction temperature. - Material Properties
Different metal pairs (e.g., Type K, J, T) exhibit unique thermoelectric voltage-temperature relationships. For example:- Type K (Nickel-Chromium/Nickel-Silicon): Measures -200°C to +1300°C.
- Type T (Copper/Constantan): Suitable for -200°C to +350°C.
2. Technical Implementation in Die Casting
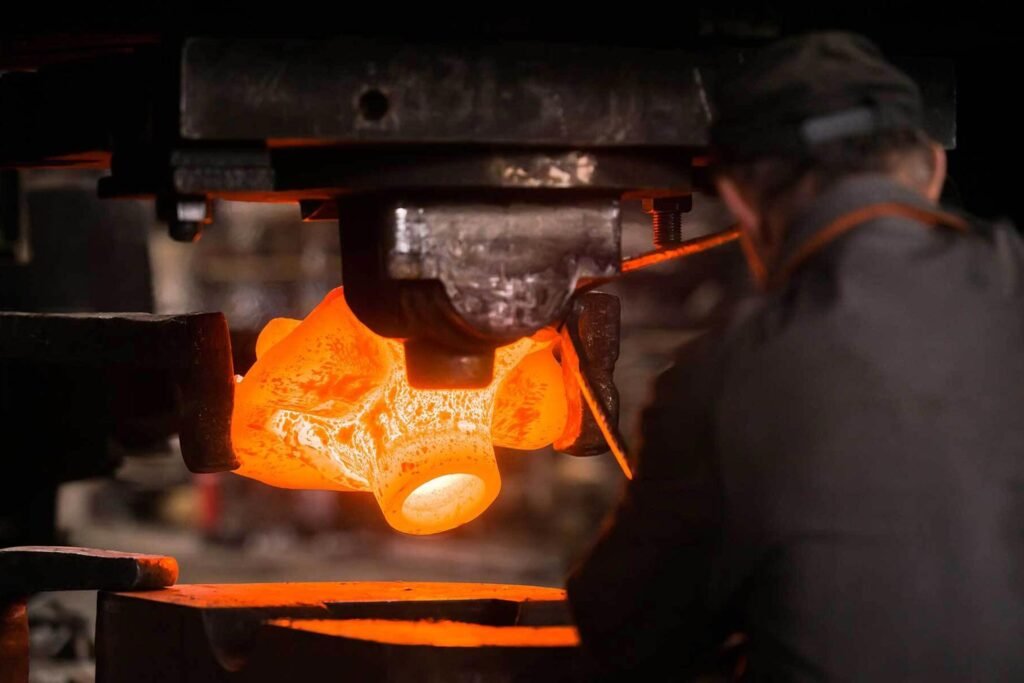
- Installation Methods
- Drilled Embedding: Micro-thermocouples are embedded into deep-drilled holes in the mold (e.g., 0.35 mm or 12.5 mm from the cavity surface) using mechanical fixation (screws, steel sleeves) or high-temperature cement for optimal contact.
- Armored Protection: Magnesium oxide-insulated, stainless steel-sheathed thermocouples provide vibration resistance, high-pressure tolerance (up to 40 MPa), and rapid response (time constant: 0.05 sec).
- Integrated Sensors: In rotationally symmetric molds, multiple thermocouples (e.g., four Type K) are integrated into custom sensors. Electron-beam welding ensures mechanical stability, while proximity to the mold surface (≤0.25 mm) captures transient thermal gradients.
- Temperature Monitoring Functions
- Thermal Balance Control: Thermocouples are positioned on the mold’s cover and ejector sides to regulate component density and surface quality via differential heating/cooling. For example, with mold oil controlled at 100°C, a TC1-TC12 thermocouple array monitors cavity temperature distribution.
- Process Optimization: Multi-point measurements (e.g., T1-T4 thermocouples) correlate temperature with cooling water flow rates. Fourier’s Law calculates local heat flux (qn∗=−kdTdnqn∗=−kdndT), reducing cycle time by 10–15%.
3. Environmental Adaptability Measures
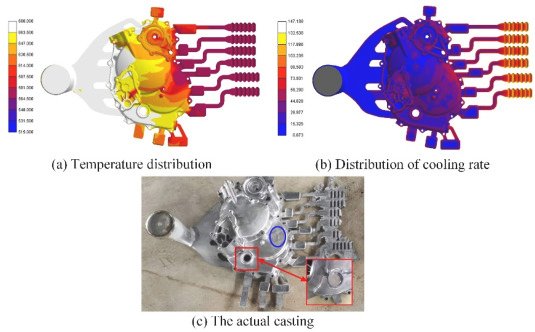
- High-Temperature Protection
- Ceramic coatings (e.g., Fiberfrax) shield thermocouples in molten metal contact zones.
- Alumina or corundum protection tubes withstand temperatures >1000°C.
- Cold Junction Compensation
Automatic compensation (e.g., PT100 platinum resistance sensors) minimizes reference junction temperature drift, limiting errors to ±2°C. - Anti-Interference Design
- Shielded twisted-pair cables reduce electromagnetic noise.
- In high-pressure die casting (HPDC), thermocouples are buried ≥2 mm below ejector pins to avoid alloy adhesion-induced signal distortion.
4. Case Studies
- Gravity Casting Experiment: Twelve Type K thermocouples (TC1-TC12) detected rapid temperature drops (\sim50°C/s) at the core-casting interface due to air gap formation, providing critical data for thermal conductivity calculations.
- Simulation Validation: Comparing 14-cycle T3 thermocouple data with simulations (30°C error) highlighted improvements in pouring temperature control and mold heat transfer modeling.
Conclusion
Thermocouples serve as the cornerstone of die casting thermal management, enabling defect reduction (e.g., porosity, sticking), mold longevity, and process efficiency. Their reliability hinges on systematic design in material selection, installation, and environmental adaptability.
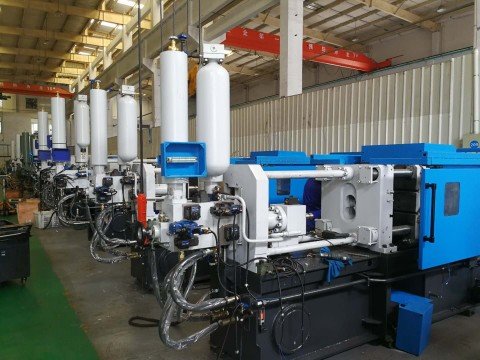
Feel free to contact Haichen, a professional die casting machine manufacturer.
Let us answer more technical questions about die casting machines for you.