There are three platen types of Die casting machine:
- Fix platen: the first platen
- Movable platen: Open and close the mold
- Third platen: platen to adjust the mold thickness
A die casting machine platen is a large, thick, flat steel plate that holds the two halves of a die in place during the die casting process. We focus on the movable platen and the fixed platen.
Total 3 platen types of Die casting machine on the clamping unit.
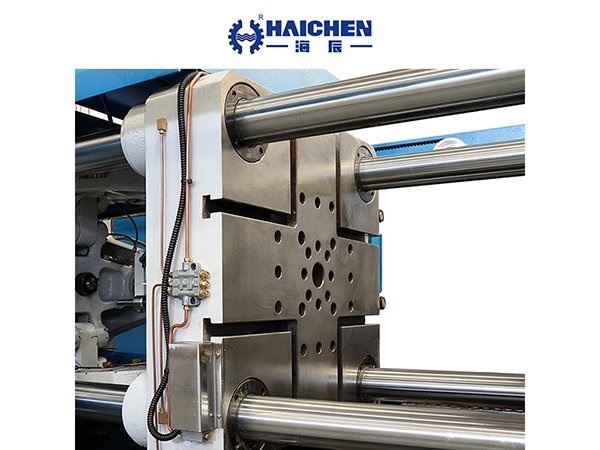
The movable platen for die casting machine
- It is fixed on the die-casting machine’s die-opening mechanism and can move horizontally with the drive of the die-opening mechanism, thereby realizing the closing and opening of the mold.
- The movable platen is usually equipped with a cavity and a core, which are used to form the outer contour of the casting.
- The movable platen is equipped with mechanisms such as a push rod and a reset rod, which are used to eject and remove the casting from the movable mold after the mold is closed;
- The movable platen also bears the task of bearing the molding pressure to ensure that the mold remains stable and accurate during the production process
The fixed platen for die casting machine
- It is fixed on the fixed die plate of the die casting machine and is the part where the molten metal enters the die casting mold cavity.
- The fixed platen is also provided with a cavity to form the outer contour of the casting and complete the overall shape of the casting together with the cavity on the movable platen.
- The fixed platen fixes the mold to the injection molding machine through a fixing clamp, and enables the ejector rod of the ejection mechanism to smoothly push the ejector platen, thereby pushing the casting out of the mold.
- The fixed platen also bears the task of bearing the molding pressure to prevent the mold from shifting during the production process.
The third platen of die-casting machine
- Adjusting the mold template by adjusting the thickness and position of the mold
- Ensure stable clamping force of the mold,To avoid production problems caused by improper installation or inaccurate adjustment of molds.
- In addition, adjusting the mold template can also shorten the installation time of the mold, improve production efficiency. And optimize the design to make the stress distribution of the template uniform. Thereby improving the durability and service life of the mold.
The third platen is the last type platen types of Die casting machine.
Optimize design
- Topology optimization: In order to reduce the weight of the die casting machine platen and improve its performance, topology optimization techniques are often used in the design of modern die-casting machine platens. Through software simulation and calculation, optimize the material distribution of the template, reduce unnecessary material usage, while maintaining or enhancing the strength and stiffness of the structure.
- Material selection: The selection of die casting machine platen materials is also crucial, and commonly used materials include ductile iron, which has good mechanical and processing properties.
- Precision machining: The manufacturing of die casting machine platen usually requires high-precision mechanical machining to ensure the smoothness and dimensional accuracy of the template surface, which is crucial for ensuring the quality of die-casting parts.
Platen on Haichen machine
Haichen machinery produces high pressure die casting machines. It includes both cold chamber die casting machines and hot chamber die casting machines.They are characterized by high durability and precision.
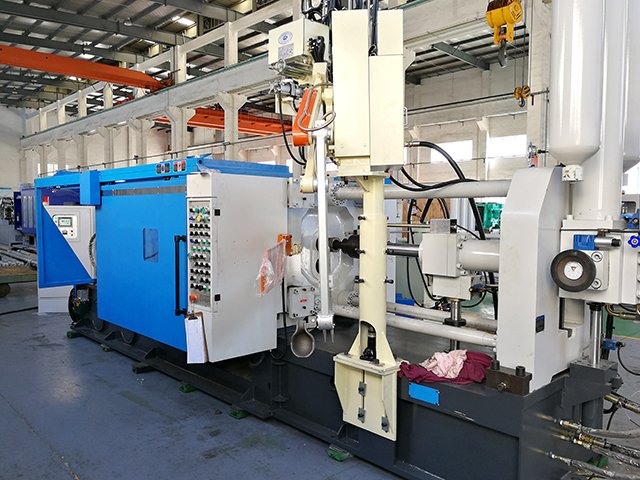
Summary
A die casting machine platen type mainly includes stationery platen and movable platen, which work together through precise mechanical structures and hydraulic systems to achieve efficient casting processes. The design of these templates not only needs to consider the fluidity and cooling characteristics of the materials, but also the stability and durability of the molds to ensure product quality and production efficiency.