Die casting mold metals need to meet the stringent requirements of high temperature, high pressure, wear resistance and thermal fatigue resistance.
Die cast mold metals–Aluminum Alloys
Lightweight
The density is only 2.7 g/cm³, which is 1/3 of steel, and is widely used in fields that require weight reduction (such as automobiles, aerospace).
Corrosion resistance
The surface is prone to the formation of an alumina protective layer, which is suitable for parts exposed to moisture or corrosive environments.
High thermal conductivity
Excellent heat dissipation performance, commonly used in engine components and electronic equipment radiators.
Ease of processing
Complex structures can be formed by cold chamber die casting with low subsequent processing costs.
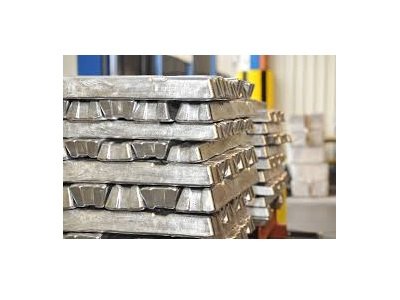
Common alloy types
ADC12 (A383): High silicon content (9.6%-12%), good flowability, suitable for thin-walled parts (e.g. automotive dashboards).
A380: Balanced strength and casting performance for engine mounts and pump bodies.
AA 413: Outstanding heat resistance for building components in high-temperature environments.
Applications
Automotive industry: engine blocks, transmission housings, suspension systems (accounting for more than 40% of automotive lightweight materials).
Consumer electronics: laptop cases, mobile phone frames (taking advantage of their electromagnetic shielding properties).
Industrial machinery: hydraulic valve bodies, pump casings (depending on their high strength and fatigue resistance).
High melting point (about 660°C), cold chamber die casting machine is required, and the equipment cost is higher than that of zinc alloy.
Creep may occur after long-term exposure to high temperatures, which requires alloy design optimization (e.g. addition of copper and magnesium).
Die cast mold metals–Zinc Alloys
High fluidity: Low melting point (380-420°C), suitable for hot chamber die casting, can form ultra-thin walls (below 0.5mm) and fine textures.
Excellent surface quality: the surface finish of the casting is up to Ra 0.8-1.6μm, and it can be straight.
Zamak 3: North American mainstream alloy, containing 4% aluminum, 0.1<% copper, balanced strength and ductility (tensile strength 283 MPa).
Zamak 5: Added 1% copper, hardness increase (Brinell 91), used in European car door locks and gears.
ZA-8: 8.4% aluminum, the only high-strength zinc alloy that can be die-cast in a hot chamber to replace brass parts.
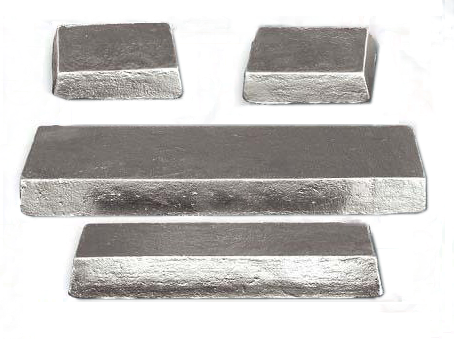
Applications
Hardware: door handles, locks (chrome or nickel plated surface).
Electronic devices: connector housings, heat sinks (RF shielding performance is better than plastic).
Precision instruments: watch movements, gears, medical devices (relying on their high dimensional accuracy).
Limitations
High density (6.6 g/cm³), not suitable for very lightweight scenarios.
The ductility of copper-containing alloys decreases after long-term aging, and impurities (lead, cadmium< 0.005%) need to be strictly controlled.
Die cast mold metals–Magnesium Alloys
Core features
Ultra-lightweight: 1.8 g/cm³ density, 33% lighter than aluminum, higher specific strength (strength/density ratio) than steel.
High shock absorption: The damping coefficient is 30 times that of aluminum alloy, which is used to reduce mechanical vibration.
Fast solidification: 50% shorter die casting cycle than aluminum alloy, longer mold life (no iron erosion).
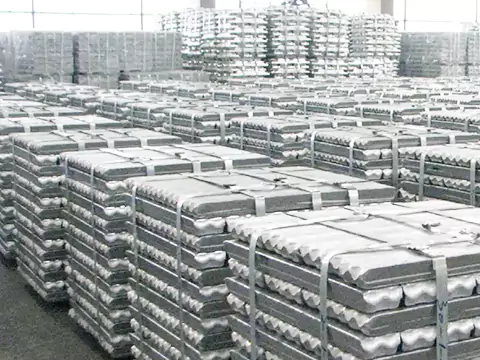
Common alloy models
AZ91D: 9% aluminum, 1% zinc, the best comprehensive performance, accounting for 70% of the market (automobile steering wheel skeleton, drone fuselage).
AM60B: Outstanding ductility (12% elongation) for automotive seat frames and dashboard brackets.
AE42: High temperature resistance (continuous operation at 180°C), replacing aluminum alloy engine cylinder head.
Applications
Aerospace : satellite mounts, helicopter gearboxes (significant weight reduction).
3C products: laptop cases, camera bodies (stronger than plastic and recyclable).
New energy vehicles: battery tray, motor housing (combined with lightweight and electromagnetic shielding requirements).
Limitations
Inert gas protection (e.g. CO₂) is required for melting, and the equipment is complex and costly.
Poor corrosion resistance and requires surface treatment (micro-arc oxidation or coating).
Other Alloys
Copper Alloys: High conductivity (58-100% IACS), used in electrical connectors and ship components, but expensive and difficult to die cast (melting point 1083°C).
Iron Alloys: Excellent wear resistance, used in heavy machinery gears, but high density (7.8 g/cm³) and fast die loss.
Tool steels and hot work die steels-die cast mold metals
H13 steel (4Cr5MoSiV1)
Characteristics
High toughness, excellent heat fatigue resistance, working temperature ≤ 600°C, suitable for repeated thermal cycling environment.
The surface hardness can reach 750HV through nitriding treatment, which prolongs the service life.
Application
The mainstream choice of aluminum alloy and magnesium alloy die-casting molds, such as automobile engine blocks, gearbox housings, etc.
Advantages
Cost-effective, domestic H13 is widely used in small and medium-sized batch production.
Imported H13 (such as SKD61) has higher purity and longer life span by more than 30%.
SKD61 (Japanese standard, corresponding to H13)
Characteristics
Similar to H13 composition, but the production process is better, the impurity content is low, and the toughness and polishing effect are better.
Application
High-precision, high-volume production scenarios, such as consumer electronics shells, complex structural parts.
Cost
The price is about 2 times that of the national standard H13, which is suitable for high-end needs.
3Cr2W8V
Characteristics
High tungsten content (8%), high temperature resistance up to 650°C, but the toughness is only half of H13, prone to thermal fatigue cracks.
Application
Cold chamber die casting molds, copper alloy die casting (such as copper radiators), some zinc alloy molds.
Limitations
It is gradually replaced by H13, but it still has applications in superalloy die casting.
DIEVAR Steel (Modified H13)
Characteristics
Improved red hardness and ductility, enhanced crack resistance, suitable for very large molds or continuous production.
Application
Integrated die-casting mold for new energy vehicles, such as Tesla Model Y rear bottom plate.
8407 steel
Characteristics
High purity, excellent resistance to hot cracks, and 50% longer life than ordinary H13.
Application
High-end aluminum alloy die-casting, such as aviation parts, precision instrument housings.
Copper-based alloys (e.g. CuCr, beryllium copper)
Characteristics
Excellent thermal conductivity (5 times that of steel), rapid heat dissipation reduces thermal stress, but high cost.
Application
Partial inserts are used in areas with high heat loads, such as gate sleeves or ejector pins for die-casting molds.
Maintenance and use recommendations
Preheating & Cooling Control
The mold is preheated to 200-300°C (aluminum alloy) to reduce thermal shock.
The temperature difference of the cooling water is controlled within ±5°C to avoid local stress concentration.
Regular maintenance
The parting surface wear is checked every 5000 molds, and the microcracks are repaired by laser cladding.
Clean up carbon deposits in the exhaust groove to prevent air bubble defects caused by gas entrapment.
Through reasonable material selection and process optimization, the life of die-casting molds can be increased from 100,000 molds to more than 300,000 molds, significantly reducing production costs.