Die casting techniques are the manufacturing process in which liquid metal is injected into a mold cavity under high pressure.
This die casting techniques often use to produce small, thin-walled, precision parts from non-ferrous metals, such as those in the automotive and aerospace industries.
The die casting process involves using two mold halves (a movable mold and a fixed mold), injecting liquid metal into the mold through a hydraulic or pneumatic system. And then opening the mold to remove the casting after the metal cools and solidifies. There are two main types of die casting techniques: hot chamber die casting and cold chamber die casting.
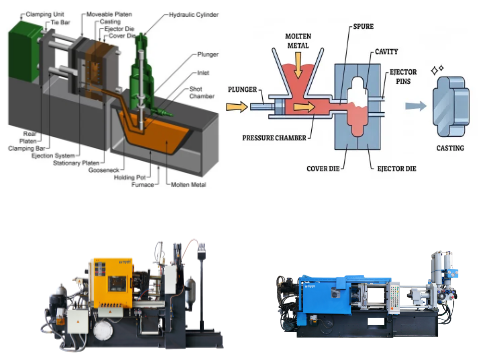
What is Die Casting?
Die Casting is a precision casting process that uses high pressure to inject molten metal into the mold cavity, and then opens the mold to take out the finished product after the metal cools and solidifies. This process has been widely used in modern manufacturing due to its high efficiency, high precision and high quality, especially in the field of large-scale production.
Hot chamber die casting techniques
Hot chamber die casting mainly uses for low melting point metals such as zinc, tin, and lead, because these metals have low melting points and can be kept in the mold cavity.
In hot chamber die casting, molten metal is poured directly from a heated container into the mold cavity.
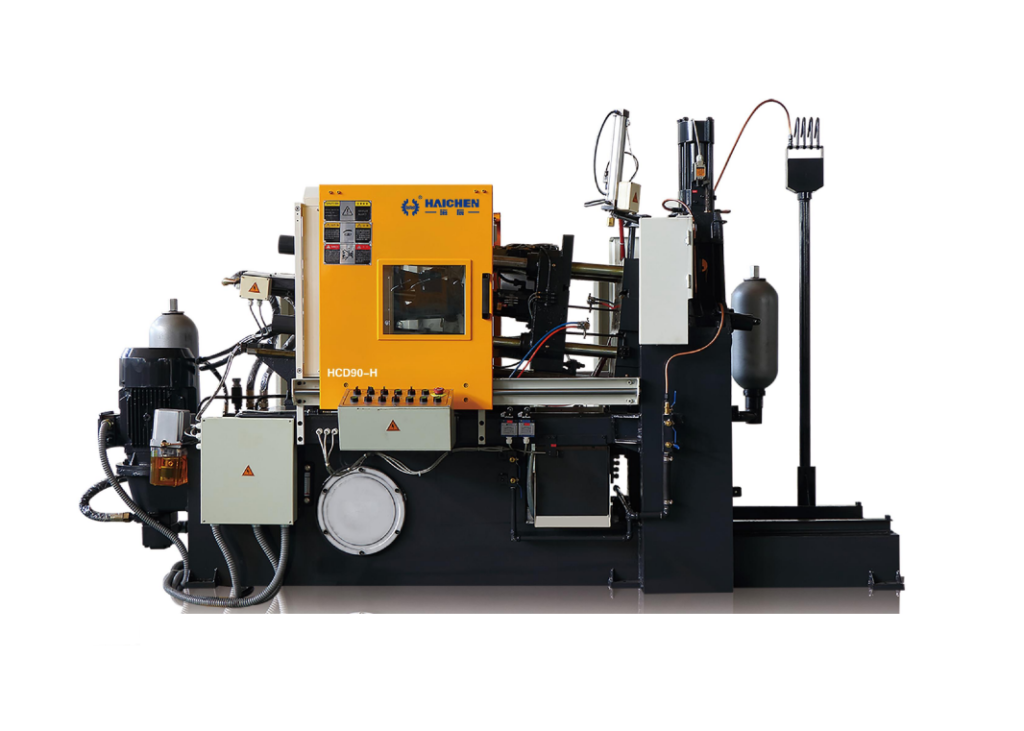
Hot Chamber Die Casting Machine is a device for metal die casting, which is characterized by integrating the storage part of molten metal inside the machine. This equipment is mainly used for die casting of low melting point alloys (such as zinc, tin and lead) because these materials have low melting points and are suitable for operation in hot chambers.
Hot chamber die casting working principle
The working principle of the hot chamber die casting machine includes the following steps:
- Metal melting: The metal is heated to a molten state in the melting container inside the machine, usually at a temperature of about 700°C or below.
Metal injection: When the mold is closed, the piston rod drives the piston to inject the molten metal into the mold cavity through a gooseneck or a submerged pouring system.
Cooling and solidification: The metal cools and solidifies in the mold, and the mold remains closed at this time.
Mold opening and removal: After the metal solidifies, the mold opens and the completed casting is pushed out through the ejection mechanism.
Equipment composition
The hot chamber die casting machine mainly consists of the following parts:- Frame: The main structure of the machine.
Melting unit: used to store and heat metal, usually a melting pot made of cast iron- Transfer mechanism: including piston rod and pressure cylinder, used to transfer metal from the melting unit to the mold
- Mold closing mechanism: used to control the opening and closing of the mold
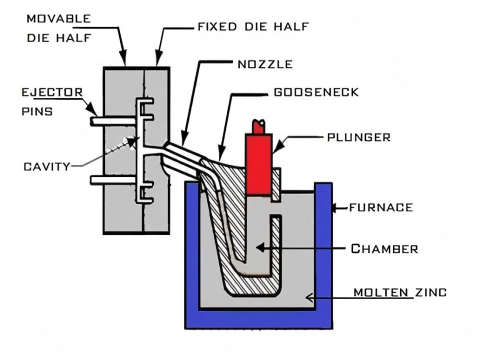
Hot chamber die casting application fields
Hot chamber die casting machines are widely used in automobiles, motorcycles, 3C products, household appliances, and aerospace. In recent years, with the advancement of technology, some magnesium alloys have also been successfully produced through improved hot chamber die casting processes.
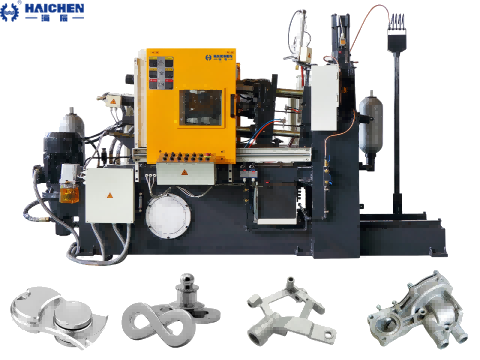
Hot chamber die casting development trend
With the growth of market demand, hot chamber die casting machines have gradually developed towards large-scale to meet the automotive industry’s demand for large parts. In addition, modern hot chamber die casting machines are also integrated with automatic control systems (such as Siemens PLC), which improves production efficiency and ease of operation.
Hot chamber die casting machines are efficient and economical metal die casting equipment, especially suitable for the production of low melting point alloys. However, its application range is limited by the melting point of the material, so it relies more on cold chamber die casting machines in the field of high melting point alloys.
Cold chamber die casting techniques
Cold chamber die casting is suitable for high melting point alloys such as aluminum, magnesium, and copper. Because these metals have high melting points and need to be operated at lower temperatures to avoid damage to the mold.
In cold chamber die casting requires the transfer of molten metal from the furnace to the injection system.
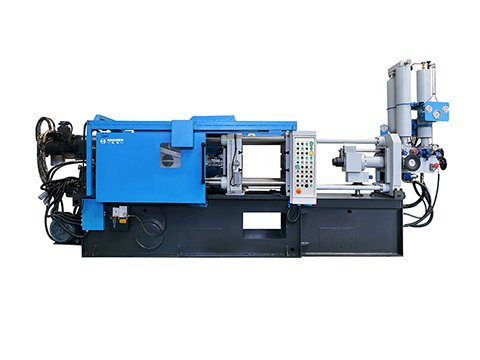
Cold chamber die casting working principle
The core of the cold chamber die casting machine is to pour molten metal from an external furnace into the cold chamber, and then inject it into the mold cavity under high pressure through a piston. This process usually includes the following steps:
Close the mold and pour molten metal from an external furnace into the cold chamber.
The piston pushes the metal into the mold cavity, maintaining high pressure during cooling and solidification.
After the metal solidifies, the mold is opened and the casting is ejected.
Cold chamber die casting Main Features
- Efficient and stable clamping system: The clamping device made of high-strength ductile iron or alloy steel ensures that the mold is stably closed under high pressure and avoids pressure shock caused by rapid mold closing.
High-precision injection system: Modern cold chamber die casting machines are usually equipped with advanced servo valves and hydraulic systems, which can achieve a fast and smooth injection process, reduce pores and defects, and improve casting quality.
Cooling system: The cold chamber design allows the mold to maintain a lower temperature during the injection process, thereby extending the mold life and improving the casting accuracy.
Cold chamber die casting application fields
Cold chamber die casting machines are widely used in the fields of automobiles, communications, electronics, aviation, construction, etc., mainly used to produce non-ferrous metal castings of high melting point alloys such as aluminum, copper, and magnesium.
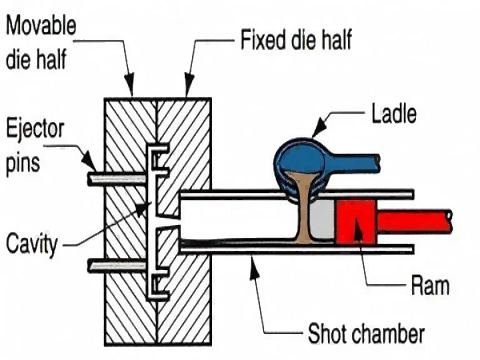
Cold chamber die casting technical advantages
Suitable for high melting point alloys: Since the cold chamber die casting machine can maintain a low mold temperature, it is particularly suitable for the production of high melting point alloys such as aluminum, copper, and magnesium.
Improve production efficiency: By optimizing the injection time and pressure curve, the cold chamber die casting machine can complete the production of high-quality castings in a shorter time.
Reduce energy consumption: The new generation of cold chamber die casting machines adopts energy-saving designs, such as servo control systems and hydraulic optimization designs, which significantly reduce energy consumption
Die casting machine key parameters
To improve the service life of the mold and the quality of the casting, the mold usually cools and heates by a water cooling or oil heating system.
Mold requirements
- Material: tool steel, mold steel (high hardness, high pressure resistance)
- Lifespan: zinc alloy molds can reach millions of times, aluminum alloys about hundreds of thousands of times
Product features
- Thin-wall capability: wall thickness 0.8–6.0 mm (0.8–3 mm for small parts, 2–6 mm for large parts)
- High precision: dimensional tolerance CT4–7 (aluminum alloy CT5–7, zinc alloy CT4–6), surface roughness ≤12 μm
- Insert technology: metal inserts can be pre-set to enhance local performance
Material restrictions
Mainly applicable to non-ferrous metals (aluminum, zinc, magnesium, copper alloys), ferrous alloys are vulnerable to mold damage due to their high melting point
Cold chamber die casting machines play an important role in modern manufacturing due to their high efficiency, stability and suitability for high melting point alloys. Their technology continues to improve, especially in the optimization of injection systems and clamping systems, giving them significant advantages in the production of high-end castings.
Haichen die casting machine
Haichen is one Chinese die casting machine manufacturer for more than 10years. We produce both high pressure cold chamber die casting machine and hot chamber die casting machine.They have durable and highly precise features. Haichen also produce die casting machine auxiliary equipment. Such as conveyor, vacuum machine, mold temperature controller, industrial robot, sprayer and so on.
Die casting techniques have two basic types: cold chamber die casting and hot chamber die casting, each type has its specific applications and advantages.
They have the advantages of high production efficiency, good dimensional accuracy, and high surface finish. But it also has problems such as high mold cost and limited applicable material range. Therefore, these techniques are mainly suitable for complex shape parts in large production quantities.
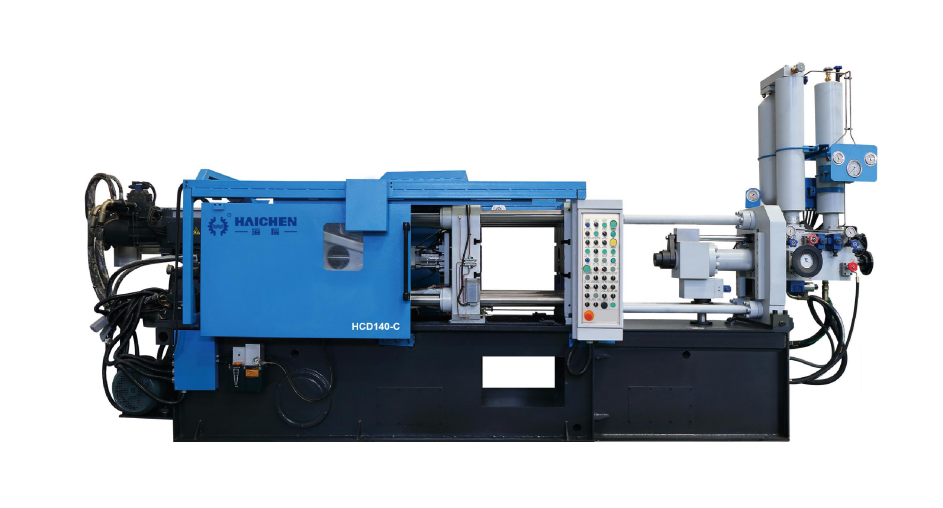
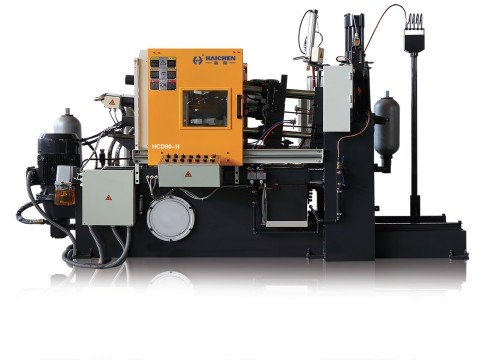
Haichen also produce die casting machine auxiliary equipment. Such as conveyor, vacuum machine, mold temperature controller, industrial robot, sprayer and so on.
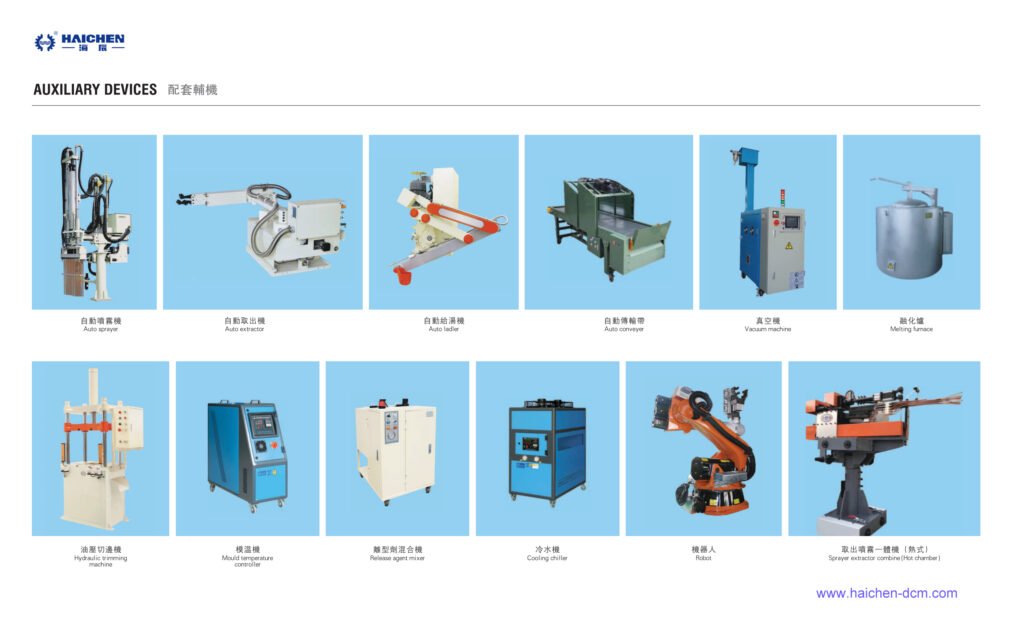
We supply cold chamber and hot chamber die casting machine spare parts.
Welcome contact us.