Heat treatment types
The heat treatment process usually includes these four:
- Annealing
- Normalizing
- Quenching
- Tempering
These steps improve the mechanical properties of die castings, such as mechanical strength, fatigue strength, ductility and impact strength, as well as dimensional stability.
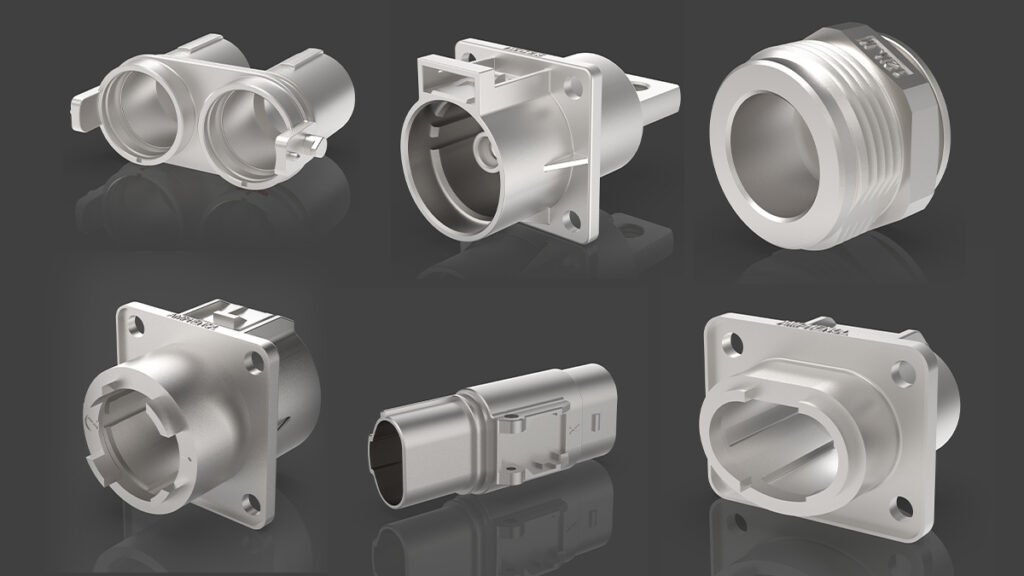
Die casting heat treatment
The heat treatment of die castings is a very critical part of their manufacturing process.
which directly affects the performance and quality of die castings.
Heat treatment mainly includes annealing, normalizing, quenching, and tempering processes, which are “four fires” in die casting.
Annealing
The purpose of annealing is to reduce the hardness of the material and improve the plasticity and toughness.
Soft annealing is usually employed, heated to 850°C, then cooled to 650°C at a rate of 10°C per hour, and finally air-cooled.
Normalizing
Normalizing is to heat the steel to 30~50 °C above AC3, keep it warm and cool it in the air to obtain a finer pearlite structure.
The cooling rate after normalizing affects the amount of ferrite precipitated and thus the hardness.
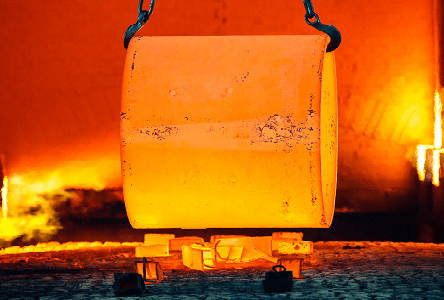
Quenching
Quenching is to heat the steel above the phase change temperature (AC1 or ACm).
And after heat preservation, at a fast cooling rate (such as water cooling)
That is greater than the critical cooling rate of the steel to obtain a martensitic structure with high hardness.
Preheating temperature
600-900°C, usually preheated in two stages, the first stage is at 600-650°C, and the second stage is at 820-850°C.
Austenitization temperature: 1000-1030°C.
Quenching medium: high-speed gas/circulating atmosphere, vacuum quenching, salt bath furnace or flow pellet furnace, etc.
Tempering
Tempering is a heat treatment process that reheats quenched parts to a temperature below the AC1 line, with enough time to stay warm, and then cools down to room temperature.
Temperature
Die-casting die tempered three times, hot forging die and extrusion die tempered twice to achieve the required hardness
Holding time
Lasts for two hours and guarantees the tempering temperature to avoid tempering brittleness.
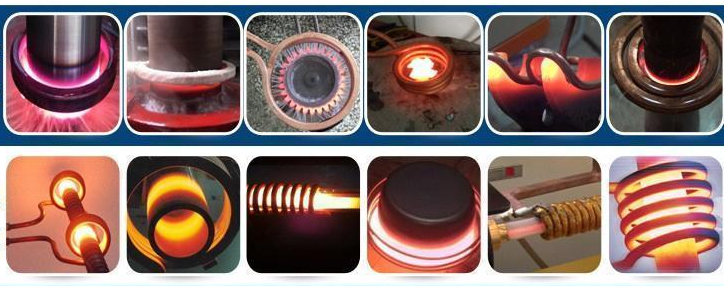
The role of heat treatment
Through heat treatment technology, the stress and deformation in the die casting can be effectively eliminated.
Annealing treatment: heat the casting to an appropriate temperature (such as 550 °C ~ 650 °C), and then keep it warm for a period of time.
So that the temperature of all parts of the casting and the surface and the inside is uniform, and the residual stress is relaxed and stabilized under this heating temperature.
After that, it is cooled to room temperature at a slow cooling rate (such as 20°C/h~40°C/h), which can basically eliminate the internal stress of the casting.
Stress-relieving annealing
For steel castings, stress-relieving annealing is usually used to eliminate the internal stress of the casting and prevent cracking.
This treatment generally includes high-temperature diffusion annealing, complete annealing or incomplete annealing.
Isothermal quenching
The study shows that during the isothermal quenching process, the surface hot compressive stress decreases with the increase of isothermal temperature.
Therefore, it is necessary to control the magnitude of residual stress and adjust the temperature of isothermal quenching.
Solution treatment and aging treatment
For aluminum alloys, solution treatment (e.g., 555°C, 2 hours) and aging treatment (e.g., 170°C, 7 hours) can effectively reduce residual stress.
However, it is important to note that quenching may increase residual stresses.
So careful selection of the appropriate heat treatment process is important.
ABP treatment
In the die casting mould, after a certain number of times each die casting,reduces residual tensile stress on the mold surface, thereby increasing mold life.
High-temperature annealing
Annealing of gray iron castings at high temperatures, eliminating the white mouth structure and reducing the hardness.
Above eutectic temperatures, cementite decomposes into graphite, which relieves casting stresses.
Thermodynamic simulation
The thermodynamic simulation of the casting using finite element software can predict the stress distribution of the casting at different temperatures.
And optimize the heat treatment process accordingly to achieve the best stress relief effect.
Haichen’s Heat Treatment Specifications
Equipment requirements
The annealing furnace should be closed, insulated, and equipped with an exhaust device; Local air supply and cooling devices should be installed at the job post.
During heat treatment, especially when heated to high temperatures without protection, this can easily lead to scrapping of the mold or burning the surface layer.
For this reason, Haichen usually uses equipment such as vacuum furnaces, salt bath furnaces or inert gas furnaces for heat treatment.
Operation specification
Haichen requires the operator to handle the material as gently as possible when loading and unloading to reduce the noise caused by the collision of the casting.