The injection process in die casting is a critical phase where molten metal is forced into a mold cavity under high pressure to create parts.
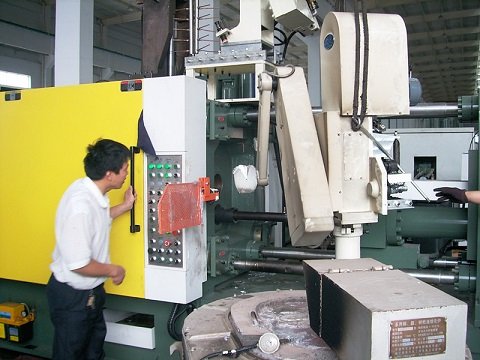
Die casting is a highly efficient manufacturing process used to produce complex metal parts with high precision and consistency. The injection phase, the heart of this process, involves high pressure forcing molten metal into a mold cavity.
The Injection Process in Die Casting
Preparation of the Mold
Before the injection process begins, the mold must be properly prepared. This involves applying a release agent to the mold cavity to prevent the metal from sticking and to ensure easy ejection of the finished part. Then securely close the mold, ensuring it can withstand the high pressures involved in the injection process.
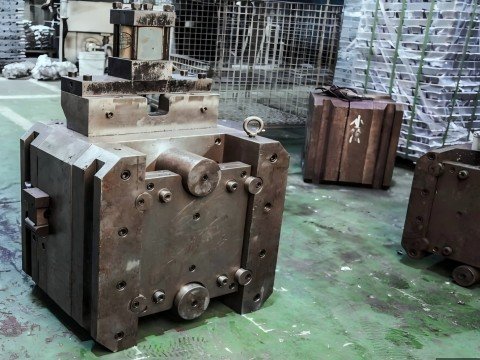
Melting the Metal
The metal used in die casting is typically an alloy of aluminum, zinc, magnesium, or other metals. We choose these materials for their mechanical properties and ability to flow easily when molten. We heat the metal to its melting point in a furnace and maintain a consistent temperature for uniformity.
Injection of Molten Metal
Once the mold is ready and the metal is molten, the injection process begins. The molten metal is forced into the mold cavity at high speed and under significant pressure. Typically ranging from 1,000 to 20,000 psi. This pressure ensures that the metal fills every detail of the mold cavity. Resulting in a part with high precision and minimal defects.
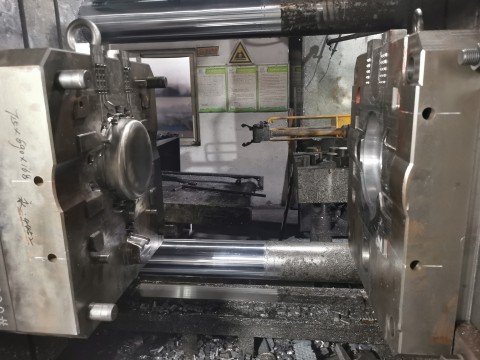
Cooling and Solidification
After filling the mold cavity, the metal begins to cool and solidify. Careful control of the cooling process prevents defects such as shrinkage or porosity. Modern die casting machines, like those from HAICHEN, often incorporate advanced cooling systems to ensure uniform cooling and reduce cycle times.
Ejection of the Part
Once the metal has solidified, the mold opens, and the machine ejects the finished part. The part may then undergo secondary operations. Such as trimming or surface treatment to remove any excess material and achieve the desired finish.
The Importance of Advanced Die Casting Machines
The success of the injection process in die casting depends heavily on the quality and precision of the die casting machine. HAICHEN, a leading manufacturer of die casting machines, offers advanced technology that ensures high precision, reliability, and efficiency.
- Maintain Consistent Pressure and Temperature: Ensuring that the molten metal flows smoothly and fills the mold cavity completely.
- Optimize Cooling Systems: Reducing cycle times and improving part quality by ensuring uniform cooling.
- Enhance Precision and Reliability: With advanced control systems and high-quality components, HAICHEN machines deliver consistent results every time.
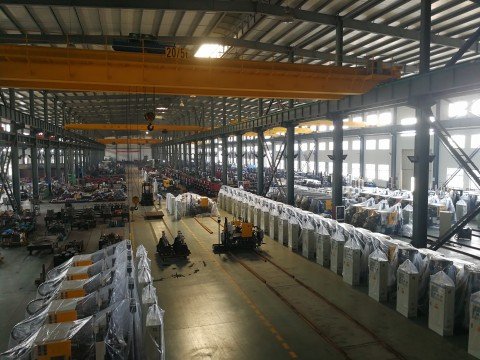