The Injection System in Die Casting

The injection system is the core mechanism in die casting that forces molten metal into a mold under high pressure. It ensures precise, rapid filling of the mold cavity to create complex, high-quality parts. Here’s a breakdown of its key aspects:
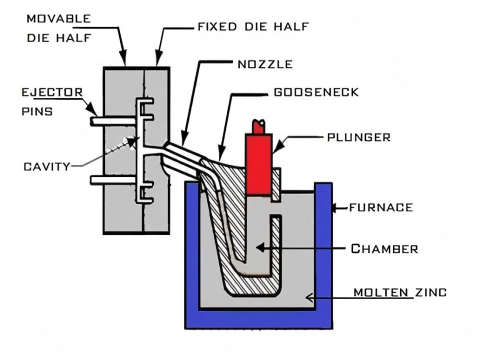
1. Core Components
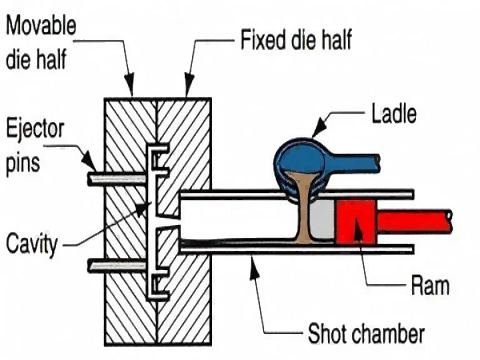
- Plunger (Piston):
- Drives molten metal into the mold.
- Made of heat-resistant steel (e.g., H13) to handle high temperatures.
- Die casting Chamber:
- Holds molten metal before injection.
- Cold Chamber: Separate from the furnace (for aluminum, copper).
- Hot Chamber: Submerged in molten metal (for zinc, magnesium).
- Nozzle:
- Connects the shot chamber to the mold, directing metal flow.
- Hydraulic or Servo Motor:
- Powers the plunger’s movement with precise speed/pressure control.
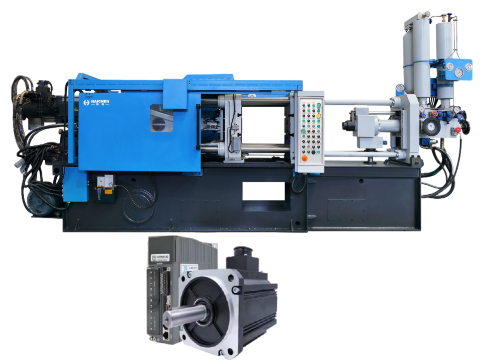
2. How It Works
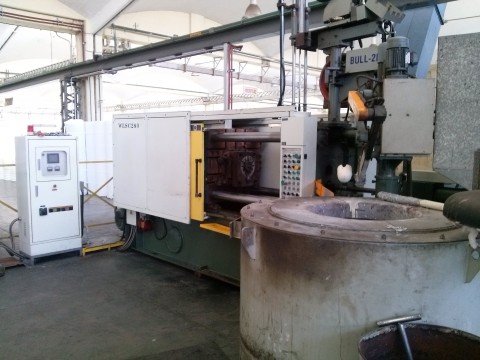
- Step 1: Molten metal is loaded into the shot chamber (manually in cold chamber machines; automatically in hot chamber).
- Step 2: The plunger pushes the metal through the nozzle into the mold cavity at high speed (1–10 m/s).
- Step 3: Intensification pressure (up to 200 MPa) ensures the mold is fully filled and minimizes defects like porosity.
3. Why It Matters
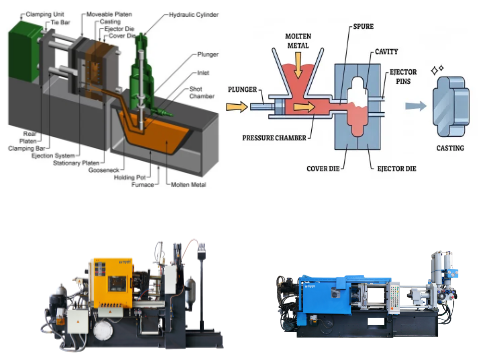
- Speed & Precision: Delivers molten metal in milliseconds, critical for thin-walled parts (e.g., smartphone cases).
- Pressure Control: Prevents air bubbles and incomplete filling.
- Consistency: Replicates parts with tight tolerances (±0.1 mm).
4. Types of Injection Systems
Type | Best For | Example Applications |
---|---|---|
Cold Chamber | High-melting metals (Al, Cu) | Automotive engine blocks, housings. |
Hot Chamber | Low-melting metals (Zn, Mg) | Zippers, electronic connectors. |
5. Innovations
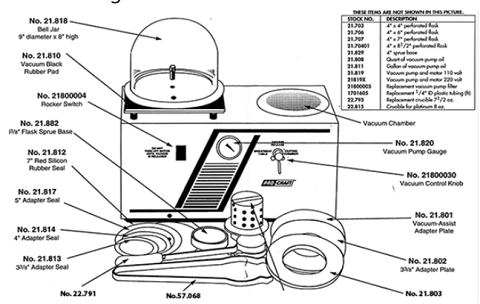
- Vacuum-Assisted Injection: Removes air from the mold for defect-free parts.
- AI-Driven Control: Sensors adjust pressure/speed in real time for optimal quality.
- Servo-Electric Systems: Energy-efficient, quieter, and more precise than hydraulic systems.
6. Common Challenges & Fixes
- Porosity: Use vacuum systems or optimize injection speed.
- Die Soldering: Apply non-stick coatings (e.g., TiN) to the mold.
- Plunger Wear: Regular maintenance and heat-resistant materials.
Real-World Example
For an aluminum car part:
- Molten aluminum is ladled into a cold chamber.
- The plunger injects it at high pressure into the mold.
- Intensification pressure ensures the part solidifies without voids.
- Result: A lightweight, durable component ready for assembly.
Key Takeaway
The injection system’s precision and power determine the quality of die-cast parts. Advances like smart sensors and eco-friendly servo motors are revolutionizing efficiency and sustainability in industries like automotive and electronics.
Two injection systems in die casting
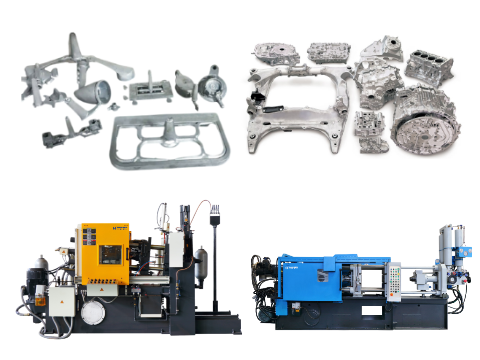
1. Hot Chamber Die Casting
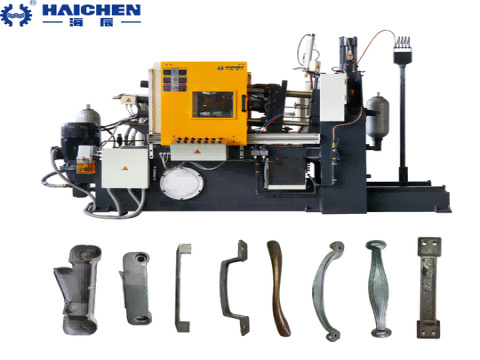
- Principle:
The injection system (including the plunger and injection cylinder) is submerged directly into a molten metal bath. A hydraulic-driven plunger forces the metal through a gooseneck and nozzle into the mold cavity. - Suitable Materials:
Ideal for low-melting-point metals (e.g., zinc, magnesium, lead alloys) because these metals do not cause thermal damage to the injection components. - Advantages:
- High efficiency for mass production.
- Reduced oxidation risk due to a closed metal delivery system.
- Faster cycle times.
2. Cold Chamber Die Casting
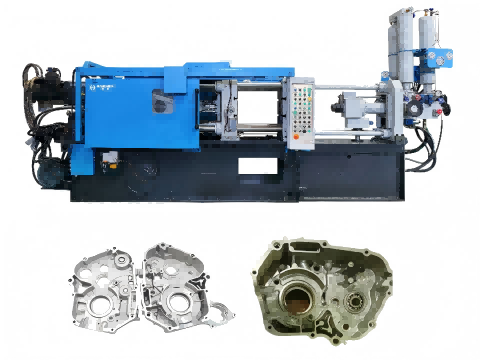
- Principle:
Molten metal is manually or mechanically ladled into a separate injection chamber (cold chamber). A high-pressure plunger then forces the metal into the mold. The injection system is isolated from the furnace to avoid prolonged exposure to high temperatures. - Suitable Materials:
Used for high-melting-point metals (e.g., aluminum, copper alloys) that could damage hot chamber components. - Advantages:
- Capable of handling metals with higher melting points.
- Suitable for larger or thicker components.
- Higher injection pressures (often exceeding 140 MPa) ensure complete mold filling.
Key Differences:
Aspect | Hot Chamber | Cold Chamber |
---|---|---|
Metal Contact | Plunger submerged in molten metal | Metal ladled into a separate chamber |
Pressure | Lower pressure (~7–35 MPa) | Higher pressure (~35–140+ MPa) |
Applications | Small, thin-walled parts (e.g., zippers) | Larger, complex parts (e.g., engine blocks) |
Oxidation Risk | Low | Higher (due to exposure during transfer) |
Both systems are critical in die casting, with selection depending on material properties, part geometry, and production requirements.
Haichen die casting machine precise injection system
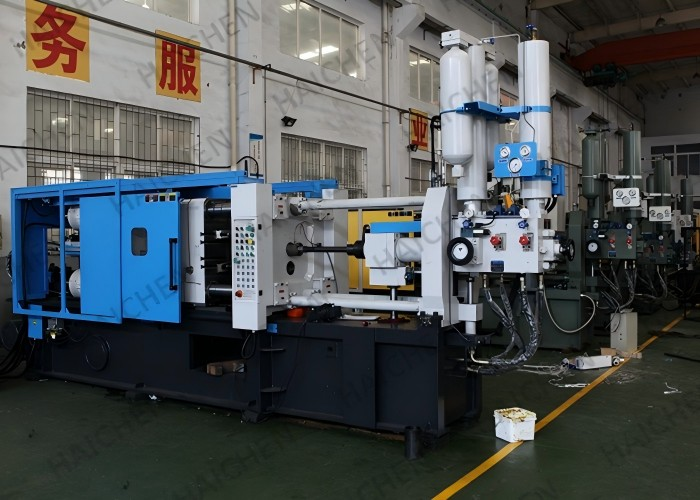
Haichen Die Casting Machine’s Precision Injection System incorporates multiple advanced technologies, with the following core features and technical details:
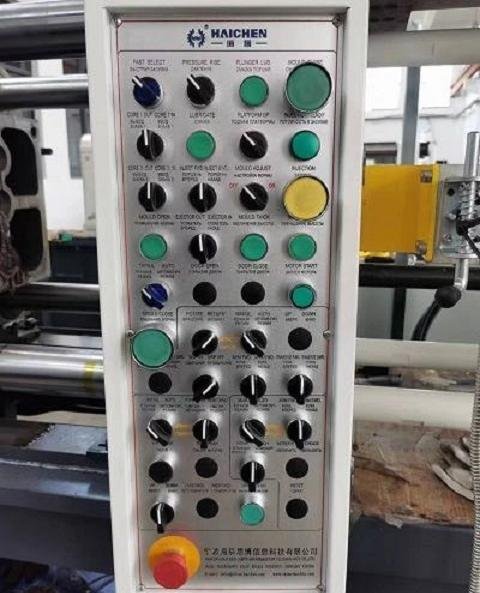
- Multi-Stage Pressure & Speed Control
Haichen’s C-series cold-chamber die casting machines utilize a four-stage injection process (slow injection, first fast, second fast, and intensification), delivering smoother transitions than traditional three-stage systems. This enables linear acceleration of molten aluminum, minimizing defects caused by turbulence or splashing. For example, its 200-ton model employs a dual-stage pressure/speed control combined with piston-type accumulators, achieving stable high-speed injection with an empty-shot speed of up to 4 m/s. - High-Precision Position Control
Real-time monitoring via magnetic encoder scales and Siemens PLC systems ensures digital precision adjustment, reducing positional errors to <0.14 mm. This eliminates the inefficiency of manual displacement sensors used in conventional systems. - Closed-Loop Energy Storage & Intensification
Proprietary closed-loop energy storage technology stabilizes intensification pressure. Pressure sensors provide real-time feedback during the intensification phase, enhancing product density and surface finish, particularly for thin-walled or structural components requiring high dimensional accuracy. - Critical Component Materials & Hydraulics
- Injection unit thermal components use premium alloy steel to withstand high temperatures (up to 700°C) and pressures.
- Hydraulic systems integrate Rexroth (Germany) and Yuken (Japan) components, paired with dual proportional valves for precise flow/pressure control, reducing noise and energy consumption by 15–20%.
- AI-Powered Parameter Optimization
Advanced models feature auto-calculation of injection parameters based on casting weight and overflow pocket data, minimizing human error. Real-time injection process curves (pressure vs. position) enable rapid process tuning and traceability. - Structural Design & Validation
Key components (e.g., platen, tie-bars) are optimized via finite element dynamic analysis. Dynamic/static template parallelism is maintained within 0.12 mm under heavy loads, ensuring precise alignment between the injection axis and mold cavity.
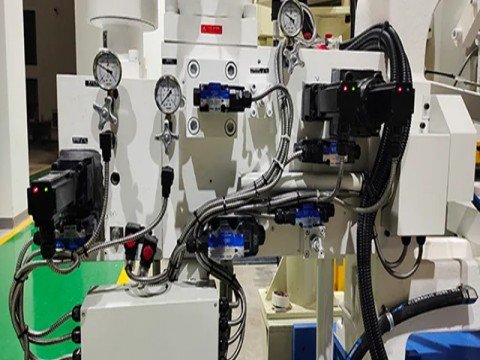
Model Differentiation:
- 200-ton model: Entry-level with dual-stage control for general aluminum castings.
- C-series: High-end with four-stage control + magnetic encoder positioning, ideal for automotive parts.
- Closed-loop energy storage: Haichen-exclusive technology for ultra-stable injection.
Haichen integrates multi-stage control, precision sensing, premium components, and intelligent algorithms to deliver a responsive, stable injection system adaptable to both standard and high-precision die casting applications.
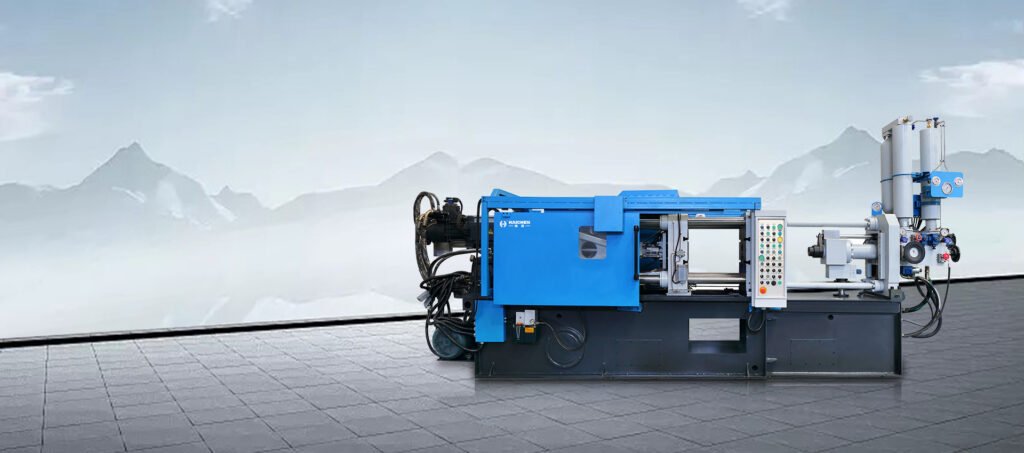
You are welcome to call or email us at any time to let Haichen provide you with more die-casting technical support.