In crankcase manufacturing, materials like aluminum and cast iron are predominantly used for their strength and durability.
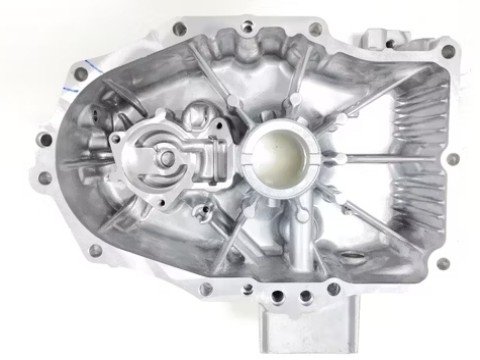
We typically manufacture crankcases, essential components of internal combustion engines, using materials with specific properties necessary for their function.
The choice of material for crankcase construction depends on factors such as engine type, performance requirements, and manufacturing considerations.
Crankcase manufacturing materials
Here are some common materials we use to make crankcases:
1. Crankcase manufacturing materials–Aluminum Alloys
- Advantages: Aluminum alloys are widely used in crankcase manufacturing due to their lightweight nature, good thermal conductivity, and ease of casting.
- Properties: Aluminum offers a good balance of strength, durability, and corrosion resistance, making it suitable for a wide range of engine applications.
- Applications: Aluminum crankcases are commonly found in automotive engines and small to medium-sized engines in various industries.
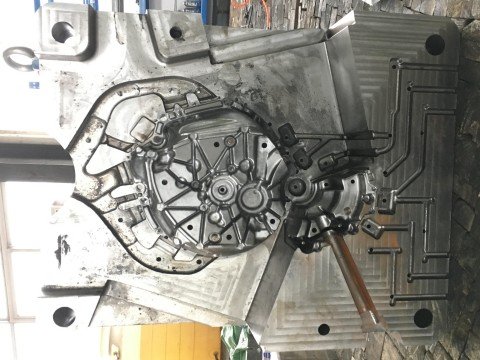
2.Crankcase manufacturing materials– Cast Iron
- Advantages: Cast iron is known for its high strength, wear resistance, and thermal stability, making it suitable for heavy-duty applications.
- Properties: Cast iron crankcases provide excellent durability and vibration damping properties, which are beneficial for certain engine designs.
- Applications: We often use cast iron crankcases in heavy-duty engines, such as those in trucks, tractors, and industrial equipment.
3. Magnesium Alloys
- Advantages: Magnesium alloys offer high strength-to-weight ratio, making them ideal for applications where weight reduction is critical.
- Properties: Magnesium crankcases are lightweight, corrosion-resistant, and exhibit good machinability, but they can be more expensive than aluminum.
- Applications: We use magnesium alloy crankcases in high-performance engines where weight savings are a priority, such as in racing cars and aircraft engines.
4. Crankcase manufacturing materials–Steel Alloys
- Advantages: Steel alloys provide exceptional strength, impact resistance, and thermal stability, making them suitable for demanding engine applications.
- Properties: Steel crankcases offer high durability and resistance to wear, making them ideal for heavy-duty engines subjected to harsh operating conditions.
- Applications:We commonly use steel alloy crankcases in large industrial engines, marine engines, and applications that need extreme durability.
5. Composite Materials
- Advantages: Composite materials offer a unique combination of properties, including high strength, lightweight, and corrosion resistance.
- Properties: We can tailor composite crankcases to specific requirements, offering flexibility in design and optimizing performance.
- Applications: We use composite materials in specialized engine applications where weight reduction, vibration damping, and specific material properties are crucial.
HAICHEN aluminum alloy die casting machine manufacturer
HAICHEN is a well-known die casting machine manufacturer.We designs their cold chamber die casting machines for producing crankcases with aluminum alloys and magnesium alloys as the raw materials.
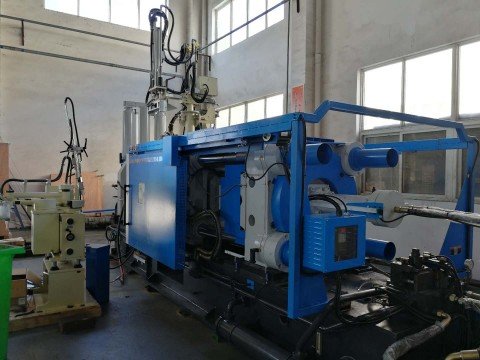
Material Versatility
HAICHEN cold chamber die casting machines are capable of processing aluminum alloys and magnesium alloys, providing manufacturers with the flexibility to choose materials according to specific project requirements.
Precision Engineering
We design HAICHEN machines with precision and attention to detail, ensuring consistent and high-quality output of complex components such as crankcases.
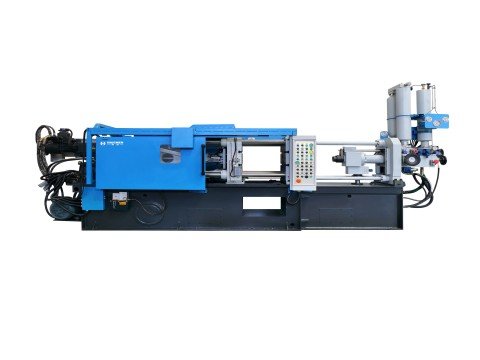
The choice of crankcase manufacturing materials depends on a range of factors, including performance requirements, cost considerations, manufacturing processes, and the intended use of the engine.
Manufacturers need to carefully select materials to ensure that the crankcase meets the necessary performance, durability, and functionality requirements of the engine in which it is installed.