Many materials can be used as a crucible, including Yttria, Iridium, Silicon Nitride (Si3N4), Molybdenum, Aluminum Coating, Quartz, and Silicon Carbide.
- Yttria: Ceramic crucible suitable for induction melting of TiAl alloys, with good thermal shock stability and low reactivity.
- Iridium: Iridium crucibles have greater advantages than platinum in chemical operations.
- Highly stable compounds (such as yttria, calcium zirconate or cerium sulfide): Crucible outer layer materials used to melt titanium, combined with refractory metals (such as tungsten, molybdenum or tantalum) to form a transition gradient coating.
- Highly refractory clay: Crucibles used for melting glass, these crucibles were found in historical archaeological sites in Ife, West Africa.
- Silicon Nitride (Si3N4): Reusable crucibles for the production of semiconductor-grade silicon ingots.
- Molybdenum: High-temperature resistant crucibles used in combination with crucible linings.
- Multilayer coating materials: Crucibles used for solidification of silicon ingots, these coatings are made of materials obtained by thermal decomposition of polysilane and/or polysiloxane.
- Aluminum-containing coatings: Crucibles used for silicon ingots, aluminum atoms are used to absorb impurities during the casting of polycrystalline silicon.
- Quartz: Crucibles used for solidification of silicon ingots, with a protective coating to reduce damage to the crucible body caused by crystal separation phenomena.
- Silicon Carbide: Crucibles used for polycrystalline silicon ingots, with a nucleation source layer that promotes rapid nucleation of silicon materials in the molten state.
In addition, there are some special-purpose crucibles, such as crucibles for metal film deposition, and technology for cold crucible directional solidification of titanium-based alloys. The design and material selection of these crucibles are all aimed at meeting specific industrial application needs, such as improving melting efficiency, reducing material contamination, and improving product quality.
Hot Chamber Die Casting Crucible Main Materials
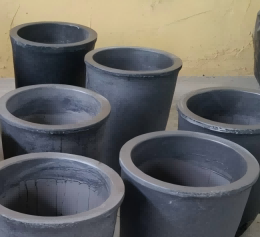
The main material of hot chamber die casting crucible is nickel-free, high cobalt rare earth martensitic heat-resistant, and corrosion-resistant alloy steel. This material has good high-temperature mechanical properties, wear resistance, and corrosion resistance to zinc and lead alloy liquids, and has obtained a national invention patent. In addition, there is a body-centered cubic ferritic heat-resistant steel, which has higher thermal conductivity and lower thermal expansion coefficient than face-centered cubic austenitic heat-resistant steel, thus having better thermal fatigue and wear resistance, and can better meet the demanding requirements of the service environment of the hot chamber die casting chamber for materials.
Main materials of cold chamber die casting crucible
The main materials of cold chamber die casting crucibles can include a variety of types, depending on the alloy and die casting process used. From the information I searched, we can see that several different materials are used in cold crucibles or related technologies.
Copper Crucible: In the study of cold crucible directional solidification of TiAl-based alloys, a split-type water-cooled copper crucible was used. This shows that copper is a suitable material for cold crucibles, especially when good thermal conductivity is required.
Refractory Material: In the study of cold crucible magnetic levitation melting of CrCoNi medium entropy alloy, CaZrO3 refractory material was used. This material has good resistance to hydration and is suitable for high temperature environments, and may also be suitable for cold crucible applications.
Dispersion Strengthened Pt-5Au Alloy: This is a new crucible vessel material with excellent high temperature mechanical properties and longer service life. Although this material is mainly used in other types of crucibles, its high performance characteristics may make it suitable for specific cold crucible applications.
Heat-resistant Steel: In the study of using heat-resistant steel crucibles for non-ferrous metal melting, 4Cr9Si2 heat-resistant steel was mentioned. This material is chosen for its heat resistance and strength and may also be suitable for cold crucible applications that need to withstand high temperatures and mechanical stress.
The main materials for cold chamber die casting crucibles can include copper, refractory materials such as CaZrO3, dispersion strengthened Pt-5Au alloys, and heat-resistant steels. The choice of material depends on the specific process requirements, such as temperature, chemical stability, thermal conductivity, and cost-effectiveness.
How to choose a suitable crucible for die casting machine
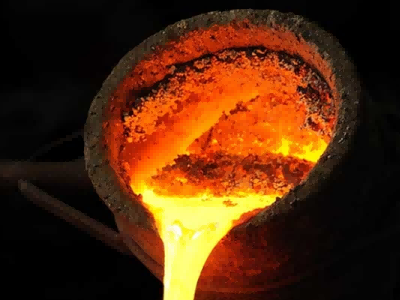
Selecting a suitable crucible for a die casting machine requires consideration of multiple factors, including the crucible’s material, design, corrosion resistance, oxidation resistance, high temperature resistance, and cost-effectiveness.
Material selection: According to the evidence, low-alloy cast iron containing elements such as chromium (Cr) and rare earth (Re) is a good choice as the crucible material because this material has excellent resistance to growth, oxidation, and aluminum melt corrosion. In addition, new aluminum-melting, galvanized low-alloy cast iron crucibles also show good resistance to oxidation, growth, and melting corrosion.
Design considerations: The design of the split crucible can effectively reduce the stress caused by solidification expansion, thereby avoiding ingot cracking. In addition, the shape and structure of the crucible should also be optimized to adapt to specific casting needs and improve efficiency. For example, the optimization of the crucible shape inside the directional solidification silicon ingot furnace can improve the temperature field distribution and reduce defects during the ingot casting process.
Corrosion and oxidation resistance: When selecting the crucible material, its corrosion resistance and oxidation resistance in high-temperature aluminum liquid should be considered. Studies have shown that the morphology and quantity of high carbon phases in steel materials have an important influence on their resistance to high-temperature aluminum liquid corrosion. In addition, fine and evenly distributed A-type graphite and appropriate chromium content can significantly improve the resistance to aluminum liquid corrosion.
Cost-effectiveness: Although the initial cost of new crucibles may be higher, their long service life can significantly reduce long-term operating costs. For example, the service life of low-alloy cast iron crucibles containing elements such as Cr and Re is 2 to 3 times that of ordinary cast iron crucibles.
Other considerations: Thermomechanical coupling analysis of crucibles is also one of the factors that need to be considered when selecting to ensure the stability and safety of crucibles under high temperature and internal compressive stress.
The selection of suitable crucibles for die-casting machines should comprehensively consider materials, design, corrosion resistance, oxidation resistance, cost-effectiveness and other relevant performance indicators. By comparing crucibles of different materials and designs, combined with actual production needs and budget, the most suitable crucible type can be selected.
Key points for using our Haichen’s die-casting crucible
The following points should be noted when using Haichen’s die-casting crucible:
Temperature control: According to, during the use of the crucible used in the magnesium alloy hot chamber die-casting machine, if there is a temperature gradient along the cross section, especially at the junction of the bottom and the side near the outer flame, severe deformation and cracking are prone to occur. Therefore, when using Haichen’s die-casting crucible, it is necessary to ensure that the temperature distribution is uniform and avoid local overheating to reduce the risk of stress concentration and cracking caused by the temperature gradient.
Maintenance and care: The cast iron crucible is subjected to high temperature, corrosion, and strong thermal expansion and contraction. If it is not properly maintained, it will seriously affect the service life. Therefore, Haichen’s die-casting crucible should be regularly maintained and maintained, including but not limited to checking the integrity and cleanliness of the crucible, avoiding corrosion and damage, and taking appropriate cooling measures to reduce the impact of thermal expansion and contraction.
Material selection: Considering the problem that the magnesium alloy crucible is prone to cracking during use mentioned in, choosing the right material is crucial to extending the service life of the crucible. Although the specific materials of Haichen’s die-cast crucibles are not mentioned in the evidence, it is recommended to select materials that are resistant to high temperatures, corrosion, and able to withstand the effects of thermal expansion and contraction to improve the overall performance and service life of the crucible.
Operating specifications: Following correct operating procedures is also key to ensuring the normal use of the crucible. This includes but is not limited to correct start and stop procedures, avoiding sudden temperature changes, and regularly checking and adjusting equipment settings to ensure that the crucible operates in optimal conditions.
The correct use and maintenance of Haichen’s die-cast crucibles requires comprehensive consideration of temperature control, maintenance, material selection, and operating specifications to ensure the long-term stable operation and service life of the crucible.