The most suitable material for die casting
Aluminum is the most suitable material for die casting. It has the advantages of light weight, high strength, good corrosion resistance, and high thermal conductivity, making it one of the most commonly used materials in die casting.
In addition, aluminum has excellent mechanical properties and provides good dimensional stability and surface finish during the die casting process.
Therefore, considering the performance, cost and range of applications, aluminum is the most suitable material for die casting.
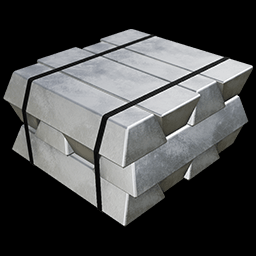
Aluminum die casting material
Aluminum exhibits good mechanical properties during the die casting process, especially in terms of tensile strength, impact toughness, and electrical conductivity.
Tensile strength and ductility
The tensile strength of aluminum is generally between 240 and 248 MPa, and the ductility is low, about 1%.
However, some aluminum alloys can have ductility of up to 7%.
Hardness and impact toughness
Aluminium typically has a Brinell hardness between 60 and 80 HB, while impact toughness is higher and can reach 70 J.
In addition, the Young’s modulus and elastic limits for some aluminium alloys: the Young’s modulus of aluminium is between 130 and 148 GPa, and the elastic limit is about 90 MPa.
Fatigue strength
Aluminum has a low fatigue strength of about -90 MPa. Impact toughness can even reach 65 J.
Other mechanical properties
Aluminum alloy exhibits excellent mechanical properties at high temperature and room temperature, especially impact toughness.
In addition, aluminum alloy die castings have good electrical and thermal conductivity.
Die-casting performance
Aluminum alloy die-casting parts have good die-casting performance, moderate surface roughness, and less heat.
However, aluminum alloy has the problem of large volume shrinkage, and when the die casting is cooled and solidified, a large concentrated shrinkage hole may be formed at the final solidification.
Economy and production efficiency
Aluminum die-casting technology has high production efficiency and economic benefits
Due to the accurate size of die-casting aluminum parts, smooth surface, small processing volume, improve metal utilization, reduce processing equipment and working time.
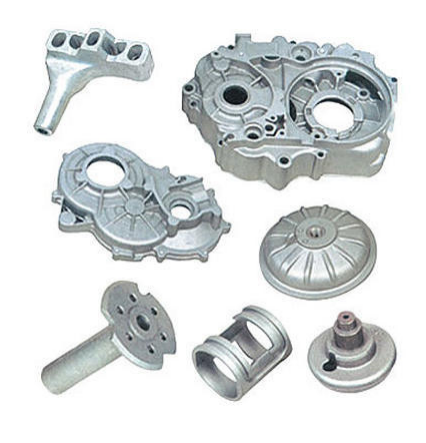
Advantages of Aluminum die casting material
Light weight
Aluminum alloy die castings have low density and light weight, but high strength.
which is suitable for fields that need to reduce overall weight, such as automotive, aerospace and transportation equipment.
This gives aluminium a clear advantage in the manufacture of lightweight parts.
Good corrosion resistance
Aluminum and its alloys have good corrosion resistance and can be used for a long time in a variety of environments without being easy to rust or corrode.
This is especially important in applications where durability is required.
Excellent thermal and electrical conductivity
Aluminum alloys have excellent thermal and electrical conductivity, making them widely used in the field of heat sinks and electronic packaging.
This feature is also suitable for applications that require efficient heat dissipation.
Good die casting mechanical properties
Die-cast aluminum alloys enable the manufacture of high-precision, dimensionally stable parts for applications that require tight dimensional control.
In addition, aluminum alloys maintain good mechanical properties in both high and low temperature environments, making them suitable for use in a wide range of temperatures.
Surface finish
The surface quality of aluminum alloy die castings is good, and there is no need for subsequent machining, which reduces production costs.
At the same time, aluminum alloys can be polished and other surface treatments to improve the appearance quality.
High recycling rate Aluminum die castings have a high recycling rate, with more than 95% of aluminum castings produced in North America.
Made from post-consumer recycled aluminum, and recycled aluminum alloy production is more economical than virgin aluminum.
Application of aluminum die casting material
The specific application cases of aluminum alloy die-casting materials in automotive parts are very wide, covering many aspects from body structural parts to power systems.
Body structural parts
Aluminum alloy die-casting materials are widely used in the manufacture of body structural parts, such as subframe beams, rear longitudinal members, A-pillars, etc.
These components are produced through a die-casting process that not only improves the strength and rigidity of the body.
But also reduces the weight of the vehicle, thereby improving fuel efficiency and drivability.
Powertrain components
In the manufacture of engines and transmissions, aluminum alloy die castings are used in key components such as cylinder blocks, cylinder heads, and crankcases.
These components take advantage of the high strength and lightweight properties of aluminum alloys to improve the efficiency and reliability of the engine.
Brake system
Aluminum alloy die castings also have important applications in braking systems.
And their excellent heat dissipation properties help to improve braking performance and extend the life of braking systems.
Battery bracket for new energy vehicles
With the development of electric vehicles, aluminum alloy die castings, as lightweight and high-strength battery bracket materials, help improve energy efficiency and extend battery life.
Integrated large body parts
For example, large car companies are trying to consolidate body parts into a single die-casting mold to reduce factory construction time, operating costs, and the number of molds, while improving quality control.
The application of this integrated die casting technology not only reduces the cost of the manufacturing process, but also improves the production efficiency.
Luxury brand models
In models such as the Audi A8, Jaguar XJ, and VW Phaeton,
Aluminum alloy die casting materials are used to make rear side members, door inner panels, shock absorber towers and other components.
Which avoids possible deformation during heat treatment and subsequent shaping processes, thus reducing production costs.
Chassis assembly
Aluminum alloy die casting parts are also used to manufacture chassis assembly components
Such as suspension brackets and beams, which are produced by the die-casting process with high integration and manufacturing efficiency.
Haichen’s Aluminum die casting material
In the production process, the forming of castings is affected by a variety of factors
And it is very easy to produce defects, such as flow marks and other defects.
Haichen solves these problems by improving the mold design and optimizing the process parameters.
Research and development of new materials and production processes, and cooperate with R&D and design institutions to develop new products.
Therefore, despite the multiple challenges of production defects, rising costs, environmental pressures and rapid technological changes.
Haichen’s aluminum alloy die casting technology is moving towards efficiency, precision, intelligence and sustainable development.