Zinc alloy and aluminum alloy difference are reflected in the composition, processing, mechanical properties and application areas.
Zinc alloy and aluminum alloy difference
Aluminum alloys and zinc alloys are widely used in a wide range of industries due to their unique properties and characteristics. Here are some of the main differences between aluminum alloy and zinc alloy.
Compositional differences:
- Zinc alloys are mainly based on zinc with other elements such as aluminum, magnesium, copper, cadmium, lead and titanium added as low temperature zinc alloy elements.
- These added elements increase the strength and hardness of the alloy.
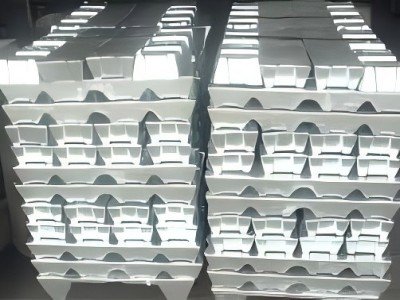
- Aluminum alloys, on the other hand, are based on aluminum as the main component. And it usually add elements such as copper, silicon, magnesium, and manganese.
- It help to improve the strength, corrosion resistance, and electrical conductivity of the alloy.

Melting point and processing:
- Zinc alloys have a lower melting point, usually above 400 degrees, and therefore require lower temperatures and pressures during casting. Which gives them good fluidity and makes them easy to weld and plasticize.
- Aluminum alloys have a higher melting point, usually requiring more than 700 degrees Celsius. And therefore require the use of more sophisticated equipment and higher temperatures during casting.
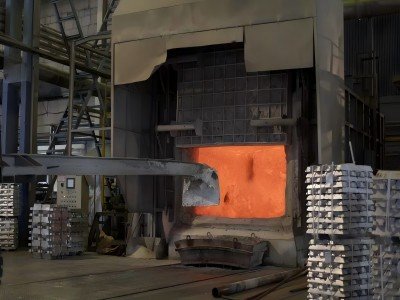
Mechanical properties:
- Zinc alloys typically have a hardness between 65-140 and a tensile strength of 260-440 N/mm², with a higher overall hardness and tensile strength than aluminum alloys.
- Aluminum alloys have a lower hardness, usually between 45-90, and a tensile strength of 120-290 N/mm². Despite their lower strength, aluminum alloys have higher plasticity and specific strength, making them suitable for medium structural materials that carry large weights.
Application Areas:
- Zinc alloys are commonly used in the manufacture of complex shaped parts, such as die-casting molds and automotive parts, due to their low melting point and good casting properties.
- In addition, zinc alloy also has good corrosion resistance and oxidation resistance, suitable for applications under atmospheric environment.
- Aluminum alloy, on the other hand, is widely used in aviation, aerospace, automotive manufacturing, machinery manufacturing and other fields, favored for its high strength, light weight and good electrical conductivity.
Haichen die casting machine supplier
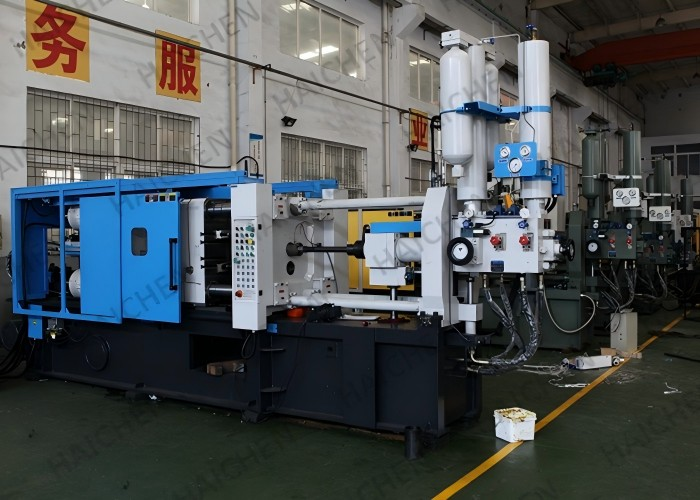
Zinc alloys and aluminum alloys each have their advantages and disadvantages, and the choice of which alloy to use depends on the specific needs of the application and the working environment.
Haichen Machinery, a die casting machine supplier. We mainly supply cold chamber and hot chamber die casting machines. Our die casting machines are capable of casting all kinds of zinc alloys, aluminum alloys and various alloys. In addition, we also supply die casting auxiliary machines, welcome to contact us.