Zinc die casting services includes optimize zinc alloy compsition and performace, mold design, surface treatment, production problems solutions, etc.
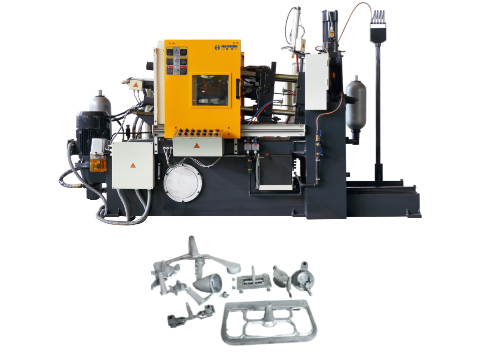
Zinc Die Casting Services involves a variety of technologies and processes, including composition optimization of zinc alloys, mold design, surface treatment, and quality control during production.
1. Zinc die casting services: Optimization of zinc alloy composition and performance
High-fluidity zinc alloy (HF alloy) significantly improves the fluidity of zinc alloy by adding elements such as aluminum and magnesium, enabling it to produce thinner-walled parts while reducing defects such as cold shut and pores.
Adding a small amount of low-melting-point metal elements (such as bismuth, gallium and indium) can improve the mechanical properties and hardness of zinc alloys while achieving lightweight.
For hot die casting process, research has found that by adjusting the composition ratio of zinc-based alloys (such as the ratio of aluminum, magnesium and copper). Its casting performance and mechanical properties can effectively improve.
2. Zinc die casting services: Mold design and optimization
In the design of zinc alloy die-casting molds, it need consider the pouring system, cooling system and ejection structure. To ensure the stability of the mold and the high-quality production of parts.
For large thin-walled zinc alloy parts, it can optimize the temperature distribution and pressure field of the mold. Through numerical simulation and process improvement. Thereby reducing defects and improving production efficiency.
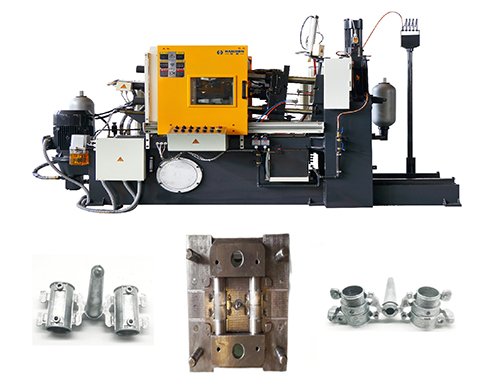
3. Zinc die casting services: Surface treatment and decorative performance
Zinc alloy die castings are usually surface treated by electroplating, painting and other methods to improve their corrosion resistance and aesthetics. For example, electroplating nickel and copper coatings can effectively prevent the corrosion of zinc alloys.
Surface-treated zinc alloy die castings may show color changes, such as blue spots, in long-term use. This is related to the diffusion mechanism of the coating and environmental factors. Therefore, it is necessary to select appropriate coating materials and processes to extend their service life.
4. Problems and solutions in the production process:
Common problems in the die casting process include cold shut, sticking, thermal fatigue, etc. These problems can solve by optimizing injection speed. And adjusting mold temperature and improving lubricant formulation.
The performance and production efficiency of zinc alloy die castings can be further improve by using advanced casting technologies. Such as high pressure die casting (HPDC) and semi-solid casting technology.
5. Problems and solutions in the production process:
Common problems in the die casting process include cold shut, sticking, thermal fatigue, etc. These problems can be solved by optimizing injection speed, adjusting mold temperature and improving lubricant formulation.
It can further improve the performance and production efficiency of zinc alloy die castings by using advanced casting technologies. Such as high pressure die casting (HPDC) and semi-solid casting technology.
6. Application areas of zinc alloy:
Zinc alloy die castings widely use in automobiles, electronic products, household appliances and other fields. Its advantages include high strength, good corrosion resistance and the ability to manufacture complex shapes.
Especially for products with lightweight and high performance requirements, such as smartphone housings and toys, zinc alloy has become the preferred material due to its excellent surface quality and lightweight characteristics.
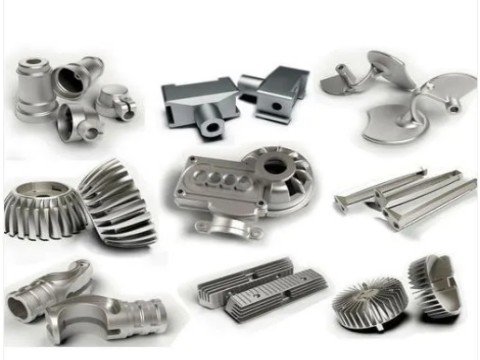
Zinc die casting services cover multiple links from alloy composition design, mold development to surface treatment and production process optimization. By continuously optimizing these links, the performance and quality of the product can be significantly improved while reducing production costs and environmental impact.
Haichen die casting machine
At the same time, we produce both high pressure cold chamber die casting machine , hot chamber die casting machine and spare parts. They have durable and highly precise features.
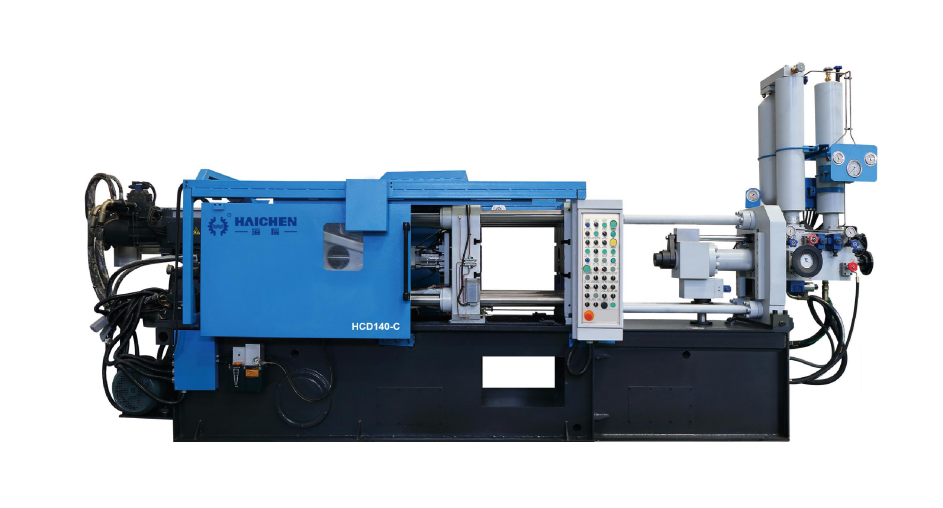
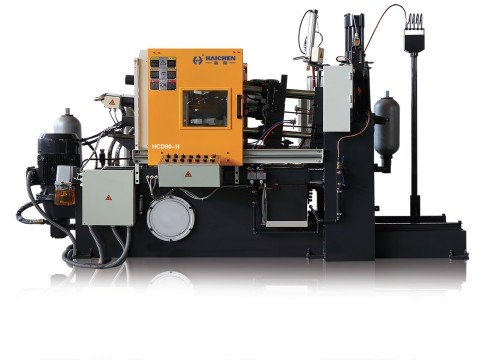
Haichen also produce die casting machine auxiliary equipment. Such as conveyor, vacuum machine, mold temperature controller, industrial robot, sprayer and so on.
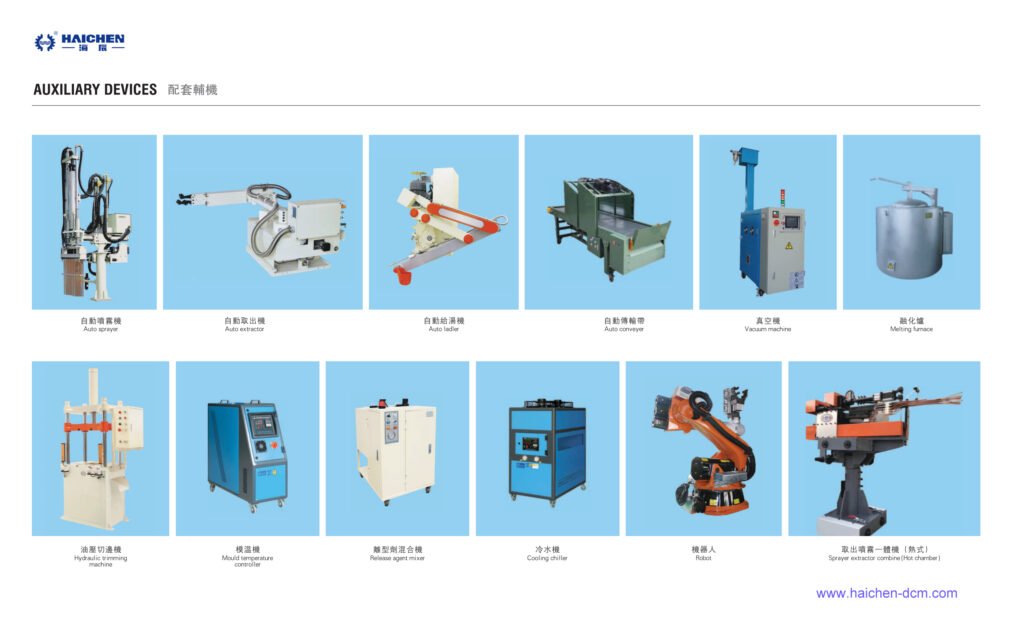
We supply cold chamber and hot chamber die casting machine spare parts.
Welcome contact us.