Zinc vs Aluminum Die Casting,covering material properties, production processes, costs, application areas and environmental impact.
Die Casting–Zinc
Zinc die casting is a metal forming process in which molten zinc alloy is quickly injected into a precision steel mold under high pressure.
Combining the three elements of die casting machine, alloy material and mold to achieve high-efficiency and high-precision part production.
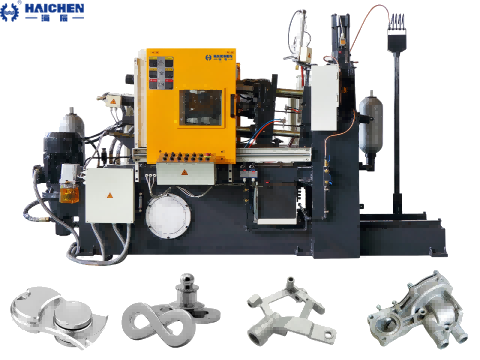
Zinc Die Casting principle
It mainly uses high pressure (usually provided by a hot chamber or cold chamber die casting machine) to fill the mold cavity with liquid metal.
And applies continuous pressure during the cooling process to eliminate shrinkage defects.
So as to obtain castings with dense structures and smooth surfaces.
The low melting point of zinc alloys (approx. 419°C) makes them suitable for hot chamber die casting (furnace and injection system integrated).
With faster cycle times (150-200% higher cycle speed) and longer tool life (up to more than one million cycles) compared to cold chamber processes for aluminium and magnesium.
This property gives it an advantage in the manufacture of small and complex parts.
Such as electronic components and automotive components.
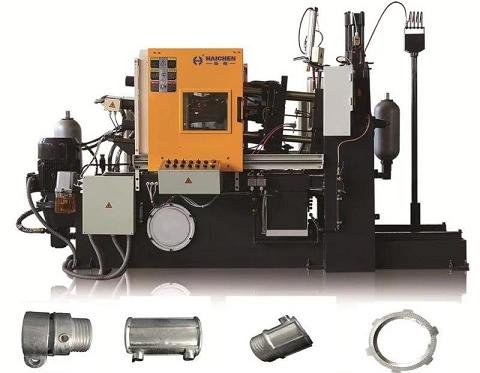
The main process flow
Mold preparation: Use high-hardness steel (e.g., H13) to make a two-half mold, clean and lubricate the inner cavity to ensure smooth demoulding.
Alloy melting: During the melting process, an automatic feeding system first heats zinc alloys (e.g., Zamak 3, ZA-8) to 380–480°C and then maintains the temperature within this range
High-pressure injection: In a hot chamber die casting machine, molten metal is pressed into the mold cavity at high velocity by a plunger through a gooseneck, typically in the pressure range of 100-150 MPa.
Cooling and demoulding: The part solidifies in a few seconds, and the ejector takes out the casting after the mold is opened.
And the trimming (removal of flash) and surface treatment (e.g. polishing, plating) are carried out.
Post-processing: including machining (turning, tapping), polishing (sandblasting, grinding) and coating (nickel plating, chrome, etc.) to improve dimensional accuracy and corrosion resistance.
Zinc alloy material properties
Zinc alloy (mainly Zamak and ZA series) has become the preferred material in the field of die casting due to its unique physical and chemical properties.
Mechanical properties: tensile strength 230-365 MPa, higher than gray cast iron and some aluminum alloys.
With an impact strength of 43 ft-lb, it is tough enough to withstand short-term, high loads.
Processability: Excellent flow (up to 0.4 mm thin walls) and low shrinkage (<0.7%), supporting complex geometries and high dimensional accuracy (tolerance ± 0.0005 inch).
Thermal and electrical properties: thermal conductivity of 113 W/mK, conductivity of 27% IACS, suitable for heat sinks, connectors and other electronic components.
Corrosion resistance: A naturally occurring zinc oxide layer provides basic protection, and a coating (e.g., chromate conversion) can further enhance its performance in wet environments.
Limitations: However, high temperatures significantly reduce its strength, making long-term use above 200°C not recommended.
Additionally, its high density (6.6 g/cm³) limits its application in lightweight scenarios.
Aluminum Die Casting
Aluminum Die Casting is a precision manufacturing process in which a molten aluminum alloy is injected into a steel mold under high pressure.
The process utilizes reusable molds (consisting of fixed dies and ejector dies) that are rapidly prototyped under high pressure (typically above 90MPa).
To form parts with high dimensional accuracy (tolerance ± 0.1mm), thin walls (as thin as 0.3mm), and complex geometries.
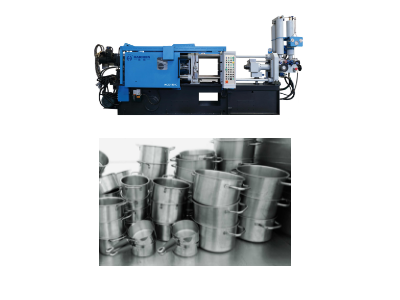
Aluminum die-casting core equipment
The aluminum die-casting process relies on special equipment and precision processes to achieve efficient production.
And its core equipment is a cold chamber die-casting machine.
Which cooperates with molds and automation systems to form a complete production system.
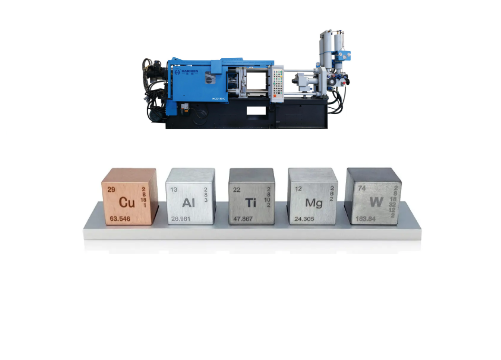
Aluminum die-casting process
Mold pretreatment
Cleaning and preheating: Gas spray gun soft flame heats the mold to working temperature to avoid thermal stress cracks.
Release agent spraying: Silicone-based emulsifier forms a 5-10μm film to reduce the risk of mold sticking
Preparation of molten aluminium
Raw material: ADC12 (Si 9.6-12%) or Al-Mg alloy, composition test after melting (Fe/Si ratio ≤ 1:2). Impurity removal: Patented ceramic filter to remove oxides (inclusion content≤0.1%).
High-pressure injection molding
Slow filling: piston speed 0.1-0.3m/s, vent sleeve gas High-speed filling: 4-6m/s to ensure complete thin-walled (0.3mm) filling
Pressurization and retention: 10,000psi pressure compensates for solidification shrinkage and eliminates microscopic shrinkage.
Cooling & Pick-up
Dynamic temperature control: mold zone water cooling (flow rate 20-50L/min), thermal imaging camera to monitor temperature uniformity.
Automatic pick-up: six-axis robot clamping, cycle time ≤ 5 minutes.
Post-processing process
Edge cutting and cleaning: laser cutting gate (accuracy ± 0.1mm), plasma removal of slag bag.
Surface strengthening: Micro-arc oxidation to form an Al₂O₃ layer (5 times more corrosion resistance).
Quality inspection: X-ray flaw detection (porosity <3%), three-coordinate measurement (tolerance±0.1mm).
Zinc Die Casting material vs. Aluminum Die Casting material
Density
First of all, zinc die casting has a density of 6.6 g/cm³, and the material is heavier, which is suitable for scenarios that require high density.
At the same time, the density of aluminum die-casting is only 2.7 g/cm³.
Which has significant advantages in light weight, and is suitable for fields with high weight reduction requirements.
Melting point
In fact, zinc has a low melting point (420°C), which makes it suitable for hot chamber processes for direct injection of molten metal.
In contrast, aluminium has a higher melting point (660°C) and requires a cold chamber process that requires additional melting and scooping of the metal, resulting in a more complex process.
Tensile Strength
First of all, zinc has a tensile strength of 280-330 MPa, which is naturally stronger and suitable for load-bearing components.
Secondly, the tensile strength of aluminum is 230-260 MPa, but the properties can be improved by alloying (e.g. adding silicon, magnesium).
Thermal conductivity
In fact, zinc has excellent thermal conductivity and is commonly used in heat dissipation components such as heat sinks and electronic connectors.
Although aluminum also has good thermal conductivity, it is slightly lower than zinc, and it is necessary to optimize heat dissipation through structural design.
Ductility
Zinc has a ductility of 3-6% and can be adjusted to improve plasticity.
Although aluminum is more malleable and natively performant.
It is not much different from zinc in practical applications.
Surface treatment
Zinc parts have a smooth surface, are easy to plate, spray, and have a low cost.
However, aluminium parts are prone to porosity and require additional treatment, such as anodizing, to improve the surface quality.
Zinc Die Casting production process vs. Aluminum Die Casting production process
Casting process
Zinc die casting adopts a hot chamber process, and the molten metal is directly formed through the injection machine, and the production cycle is 150-200% faster than aluminum.
However, aluminum die casting requires the melting of the ingots through an external furnace.
And the scooping of the metal with a cold chamber injection machine,which is a complex and energy-intensive process.
Mold life
The life of zinc die-casting molds can reach more than 1 million times, because the melting point of zinc is low, and the mold wear is small.
However, the life of aluminum die-casting molds is only about 100,000 times, and high-temperature molten aluminum will accelerate the aging of molds.
Molding capacity
Zinc enables casting with ultra-thin walls (minimum 0.3mm), making it particularly suitable for precision electronic components such as miniature connectors.
In comparison, aluminum exhibits slightly lower fluidity; however, this material remains widely applicable for large structural applications including car chassis and robotic arm components.
Comparison of application areas
Automotive
Zinc die casting is used for door handles, fuel system components (high corrosion resistance is required).
Aluminum die-casting is used for engine components and body structural parts (lightweight demand is preferred).
Electronics industry
Zinc die casting is suitable for heat sinks, electromagnetic shielded housings (high thermal conductivity).
In addition, aluminum die-casting is used in electronic housings and heat sinks (both light weight and heat dissipation).
Aerospace
In this industry, zinc die casting is rarely used (weight restrictions are strict).
More options for aluminum die casting for brackets, structural parts (high strength-to-weight ratio).
Industrial equipment
Usually chooses zinc die casting for valves, pump bodies (wear resistance required).
Then choose aluminum die-casting for hydraulic systems, high-temperature resistant mechanical parts.