5 types of die-casting metal alloys are most commonly used as die-casting materials:
- Aluminium
- Zinc
- Magnesium
- Copper
- Lead
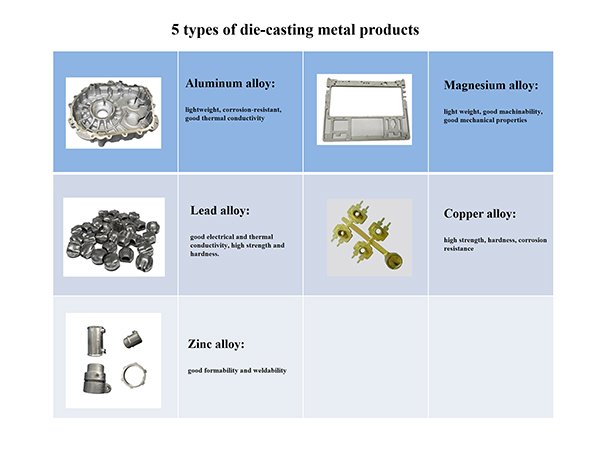
In summary, aluminium, zinc and magnesium are by far the most commonly used die casting materials, and each has unique advantages and areas of applicability that make them important in a variety of industrial applications.
What is the diffferent of 5 types of die-casting metal alloys
Among these three raw materials, aluminum alloy will be the most used by cold chamber die casting machine. Zinc will be use on hot chamber.
Aluminium
The most commonly used material in die casting is Aluminium, with low density, good corrosion resistance, good mechanical properties, and dimensional stability.
Common aluminium alloys include ADC12, A380, A413. It can produce all kinds of electronic products, home furnishing products, auto parts.
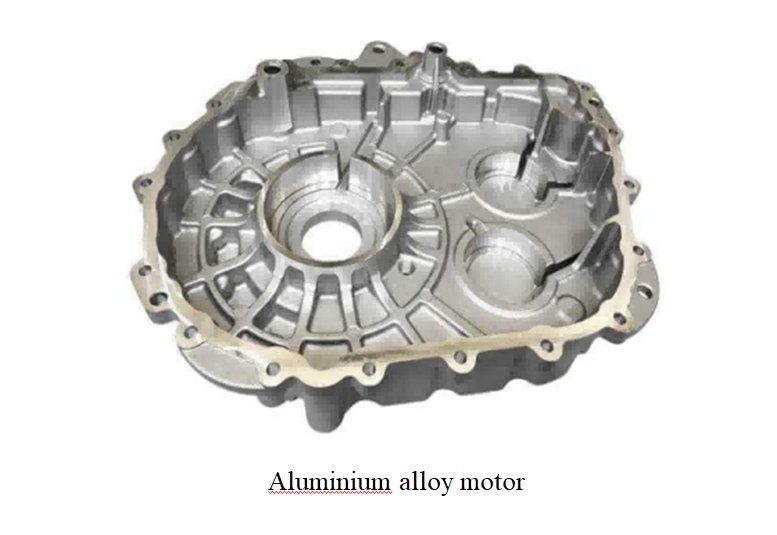
Zinc
Zinc are the most common die-casting materials, accounting for more than 90 per cent of total production.Because of their excellent strength and ease of machinability, we widely use the Zinc-based alloys.
while zinc-based alloys are capable of producing very fine die castings because of their excellent fluidity.
Zinc alloy is the easiest material to cast in die-casting, has high ductility and good impact strength. The small parts always will use ZInc alloy. It is also the main material for many metal jewellery items.
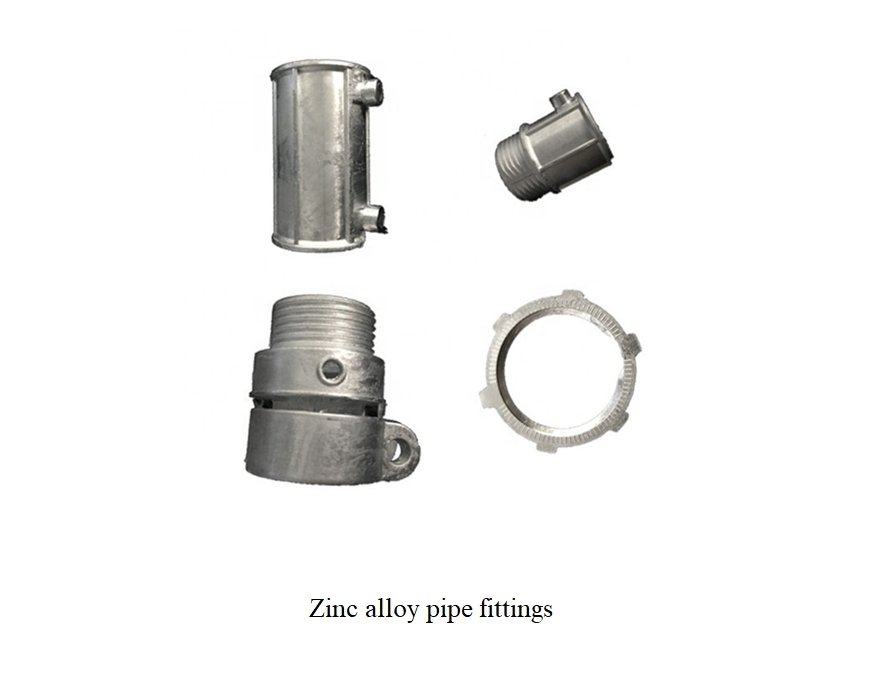
Magnesium
Magnesium alloys are used in applications where weight reduction is required due to their lightweight properties.
Because of cost and higher melting points, we willl not choose magnesium alloys. But the advantages of magnesium in specific applications are still significant.
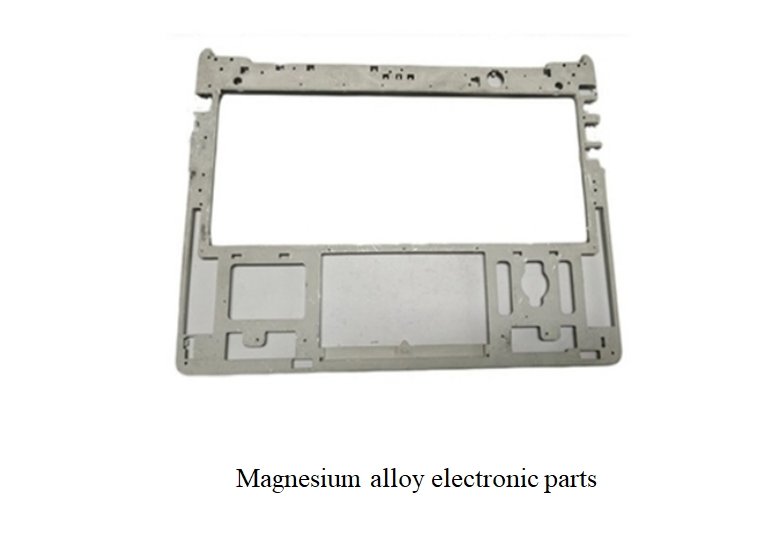
Magnesium alloy is the lightest alloy in die-casting, with excellent strength-to-weight ratio and good thermal properties, commonly used in the manufacture of parts that require lightweight and high strength. In this case, in the automotive and aerospace industries, we use magnesium widely.
Copper
Copper alloys are widely used in electrical components for their excellent wear resistance and mechanical properties. Common copper alloys include brass (composed of copper and zinc) and bronze (composed primarily of copper and tin/lead).
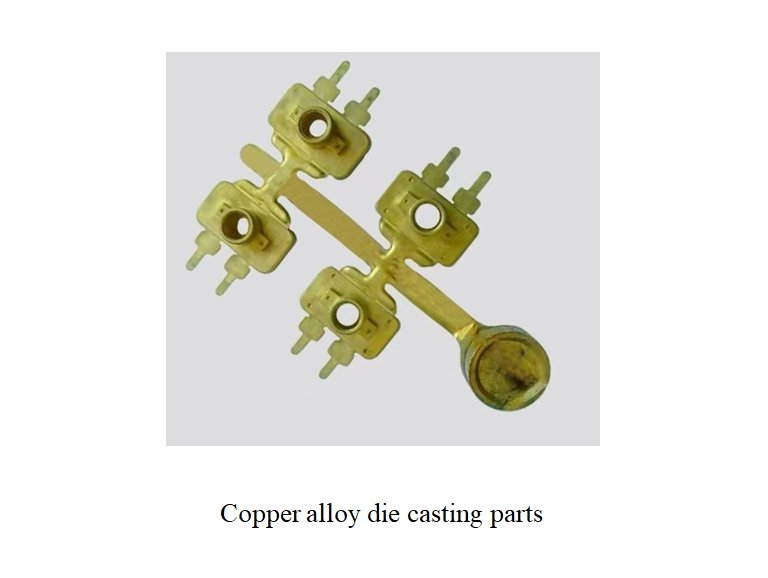
Lead
The Lead alloys are commonly used in specialised applications where a low melting point and specific mechanical properties are required, such as pipe fittings and cast wire mesh.
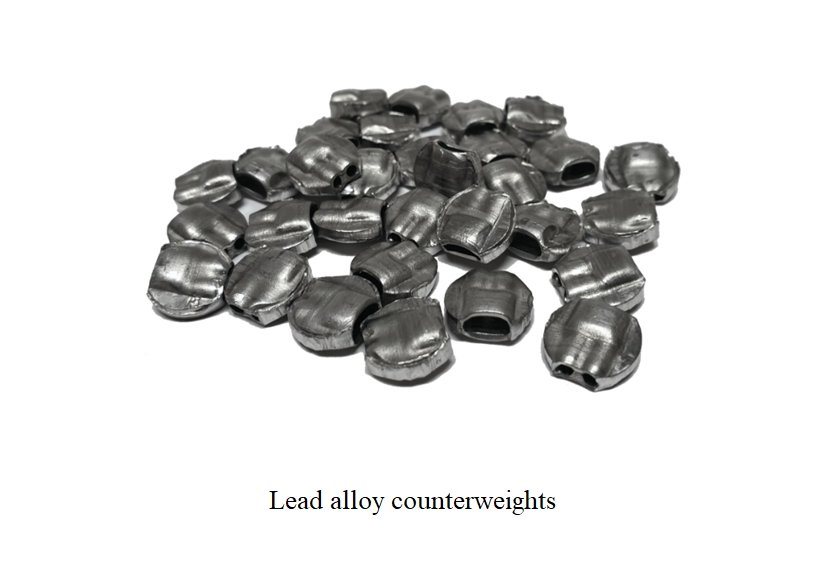
In summary, the high-pressure die-castingcovers industy will chosse this 5 types of die-casting metal alloys very commen. It almost cover the 90% die casting area.
What kind of machine must you choose for 5 types of die-casting metal alloys materials?
Normally, we just have 2 kinds of die casting machine. Cold chamber and hot chamber die casting machine. Follow the below two ways to choose the die casting machine for materials:
- Choose Cold chamber die casting machine, for the below materials:
- Aluminium
- Magnesium
- Copper
- Choose Hot chamber die casting machine, for the below materials:
- Lead
- Zinc
Two machines with different metalling temperatures. Cold chamber machine with higher metal temperature than hot chamber.
What kind of machine do you need to choose to use aluminium alloy die-casting materials?
For aluminium alloy materials, cold chamber die casting machines, especially cold chamber horizontal die casting machines, are usually recommended as they are the most widely used in applications.
The selection of the machine required for aluminium alloy die casting materials depends mainly on factors such as the material variety of the die casting, external dimensions, weight, accuracy requirements, internal quality (performance indicators), the output of the die casting and the requirements of the production environment.
In addition, integrated die casting technology is also applicable to new energy vehicle enterprises, and the core of this technology lies in the performance of large-scale die casting machines.
For specific aluminium alloy die castings, such as aluminium alloy cover plate, you can choose HCD200-C horizontal cold chamber die casting machine, this kind of machine is easy and safe to operate in the process of using, stable and reliable work, and can meet the technical requirements of the products. And for aluminium alloy bracket and so on need high precision and high productivity die casting, can choose HCD480-C horizontal cold chamber die casting machine, and according to the casting shape characteristics and processability analysis to develop the process parameters of die casting production.
When choosing the machine required for aluminum alloy die-casting materials, we need to consider:
Specific die-casting requirements and production conditions;
Consider the type of machine, degree of automation, performance, and production capacity;
To ensure production efficiency and product quality.
What type of machine is used for zinc alloy die casting material
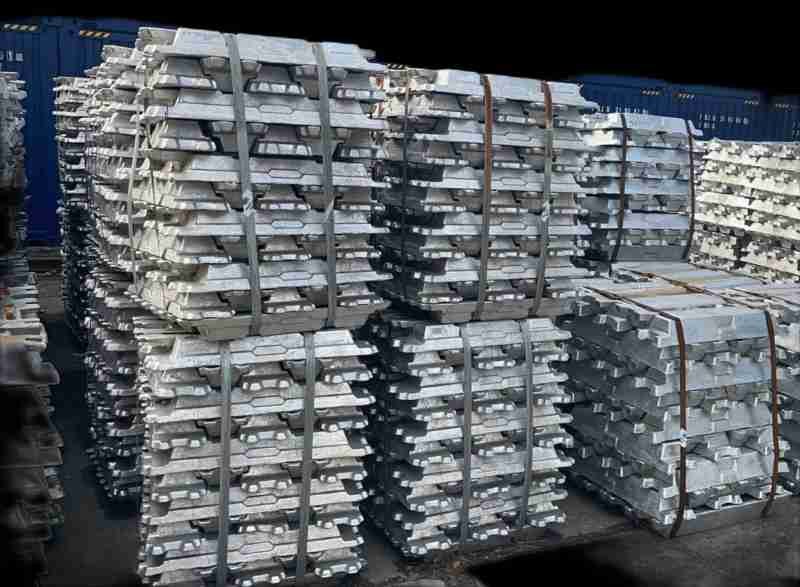
Zinc alloy die casting materials are usually produced using hot chamber die casting machines. Hot chamber die casting machines are suitable for the die casting of low temperature alloys such as zinc, because the casting temperature of zinc alloys does not exceed 450°C, and hot chamber die casting machines are able to provide the required heating conditions. In addition, hot chamber die casting machines come with circuits and pouring systems that automate the melting and ejection of the metal. Although, cold chamber die casting machines can use zinc alloys. But hot chamber die casting machines are more common in practice.
The Haichen multi-slide precision high-speed hot-type die casting machine is currently the more advanced equipment in the zinc alloy precision die casting, it can significantly reduce the production cost and labor costs, and has a high production efficiency.
This type of machine is usually with multiple independent slides that slide within a precision cross-die frame, allowing for more complex die operations.
Therefore, in summary, zinc alloy die-casting materials mainly use hot chamber die-casting machines, especially multi-slide precision high-speed hot-type die-casting machines, in order to meet the demand for efficient, high-quality production.
How to choose special brass and magnesium alloy die casting material die casting machine

When selecting a die casting machine suitable for the particular brass and magnesium alloy die casting materials, there are several key factors to consider:
Material properties
Brass and magnesium alloys have different physical and chemical properties, which directly affect the choice of die casting machine. For example, magnesium alloys have a lower melting point and higher flammability, so you need to choose a die casting machine that provides proper temperature control and safety measures. Also we have to conside about the corrosion resistance and processability of brass.
Die casting machine type:
According to the characteristics of the material and production needs, choose the appropriate type of die casting machine. For magnesium alloys, hot chamber die casting machines are usually recommended because they provide better control of temperature and pressure and are suitable for the moulding requirements of magnesium alloys. It may be necessary to consider using a cold chamber die casting machine for brass casting. Especially when we produce the complex shapes or high precision parts.
Technical requirements:
With the development of technology, new die casting machine such as semi-solid die casting, vacuum die casting and other technologies are emerging, these technologies can improve the performance and production efficiency of magnesium alloy. For brass, low-pressure die casting method is a cost-effective production method for mass production.
Safety and environmental protection requirements:
Magnesium alloy in the melting and die casting process is flammable and explosive, so the choice of die casting machine must consider its safety performance and environmental protection characteristics. For example, DC160M magnesium alloy hot chamber die casting machine adopts fully enclosed gas protection furnace, effectively controlling the risk of magnesium combustion and oxidation.
Production efficiency and cost:
Considering that production efficiency and cost are important considerations for enterprises, they should choose die-casting machines that can meet production demands while being cost-effective. For example, IZP’s LEAP series of ultra-large die casting machine, not only to meet the needs of integrated die casting, but also has a high production efficiency and low cost.
Selection of die-casting machine should be comprehensive consideration of material properties, die-casting machine type, technical requirements, safety and environmental protection, as well as production efficiency and cost and other factors, in order to ensure that the choice of die-casting machine to meet the specific production needs and ensure product quality.
Haichen has rich experience in die casting production and can configure the right die casting machine for all kinds of different die casting metal raw materials. We have both of cold chamber and hot chabmer die casting machine suit for 5 types of die-casting metal alloys.