Die casting machine extractor application is a mechanism used to remove the solidified casting from the die (mold) after the metal has cooled and hardened.
Die casting machine extractor application and design is critical to ensure smooth demolding of castings. During the cooling shrinkage of most materials, extraction of the casting to prevent entanglement during the cooling process is necessary.
Therefore, the design of an extractor typically includes key components such as push-out pins, slides, guide slides, etc. that work in concert to accomplish the extraction action.
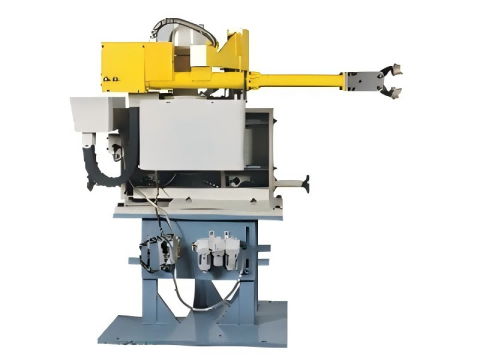
Die casting machine extractor application
Automated part removal
- Molten metal injects into the die and allowed to cool, the casting solidifies within the die cavity. And extractors automatically remove the part from the mold once it has cooled, helping to speed up the production process.
- This automation reduces the need for manual intervention and enhances production efficiency.
Preventing damage of die-casting machine extractor application
- The casting, once cooled, may be tightly adhered to the mold due to the cooling and solidification process.
- Extractors ensure smooth ejection without damaging either the casting or the mold. This reduces the risk of part defects and mold wear.
Increasing productivity
- With the ability to eject parts quickly and safely, extractors minimize downtime in between casting cycles.
- This allows the machine to produce more parts in less time.
Improved consistency
- The design of extractors can operate with precision, ensuring that ejection parts in a controlled manner, and improving consistency in the shape, dimensions, and surface finish of castings.
Benefits of die casting machine extractor
Faster cycle times
- Extractors help to shorten cycle times by speeding up the removal of the solidified casting, allowing the machine to start a new injection cycle more quickly.
Reduced labor costs
- By automating the part ejection process, extractors eliminate the need for manual labor to remove parts, which not only saves on labor costs but also reduces the risk of workplace injuries.
Higher quality parts
- Automatic and precise extraction prevents deformation or damage to parts, ensuring better part quality, with fewer defects and variations in dimensions.
Reduced maintenance of molds
- With automated ejection, the mechanical forces applied to the mold are consistent, reducing the wear and tear on mold surfaces.
Haichen die casting machine extractor
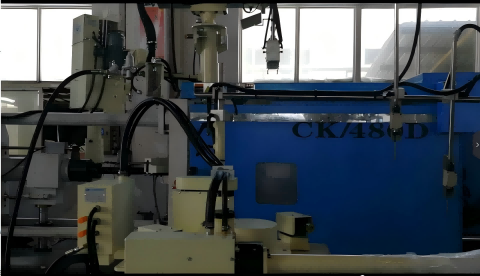
Haichen die casting machine is a well-known brand in the die-casting industry, and like other advanced die-casting machines, it integrates several key components, including extractors, to ensure the efficient and smooth removal of castings after the injection and cooling process.
Extractors are an essential component in die casting machines, ensuring the smooth removal of castings from the mold, improving productivity, reducing labor costs, and enhancing part quality.