The fundamentals of die casting mainly includes the following steps:
- Mould clamping
- Injection
- Cooling and solidification
Die Casting is a metal forming process that uses the basic fundamentals of injecting molten metal under high pressure into a cavity called a mold, allowing it to cool and solidify into the desired shape.
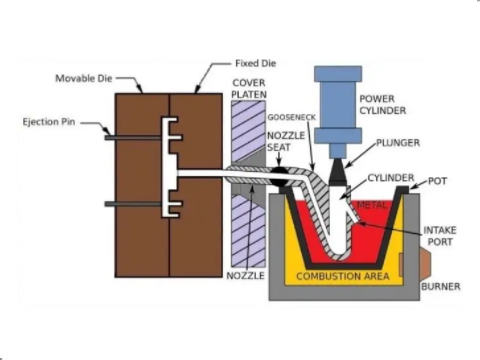
What is Die Casting?
Die casting is a manufacturing process that allows the production of metal parts with a high degree of precision.
In this casting process, workers inject molten metal into a mould; subsequently, the metal cools and hardens within this cavity to form the desired shape.
Moreover, this method enables manufacturers to create diverse metal components, such as gears, engine blocks, door handles, and electrical parts.
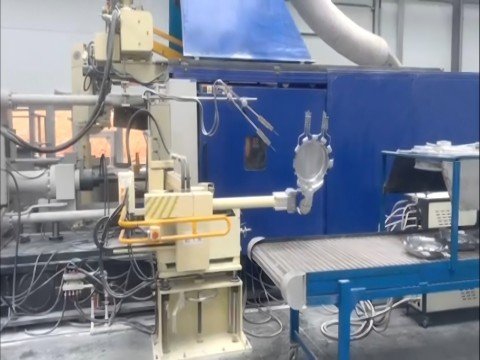
Fundamentals of die casting——Mould clamping
The clamping mechanism of the die-casting machine closes the moving and fixed moulds of the mould to form a sealed cavity.
This step ensures that the mould does not swell during the injection filling process.
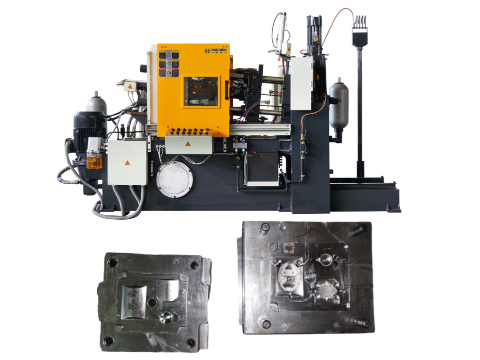
Fundamentals of die casting——Injection
The injection mechanism injects molten metal into the cavity of the mould at high speed and pressure.
Slow Injection
where the system hydraulic oil pushes the injection piston to the left to achieve a slow injection process with the aim of removing air from the ballast chamber and preventing the molten metal from splashing out of the gate.
Rapid injection
When the injection punch exceeds the barrel pouring port, the hydraulic oil quickly enters the cavity.
So that faster injection, molten metal quickly fills the mold cavity.
The third stage,pressurization movement, the molten metal begins to solidify, the forward resistance of the punch increases.
At this time, the push of the hydraulic oil completes the pressurization process of the pressurized piston, and the molten metal cools and solidifies.
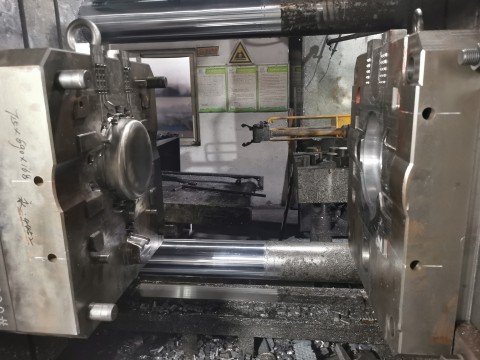
Fundamentals of die casting——Cooling & Solidification
The molten metal cools and solidifies rapidly in the mold to form the desired casting.
Open the mold and the ejection mechanism ejects the casting from the mold to complete the die casting cycle.
The machines required for the die casting——Die casting machines
Hot chamber die casting machines
Are suitable for low melting point alloys, such as zinc, tin, and magnesium alloys, and are characterized by the fact that the chamber is connected to a furnace, from which the molten metal flows directly into the chamber.
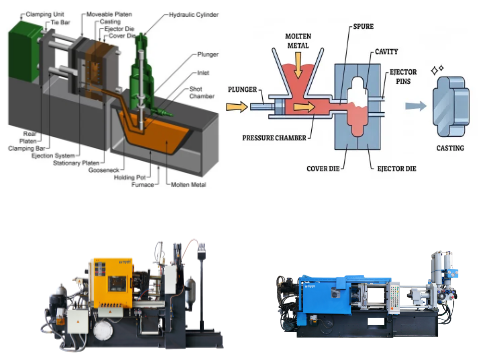
Cold chamber die casting machines
Are suitable for alloys with high melting points, such as aluminum and copper alloys.
which are characterized by the separation of the chamber from the furnace, from which the molten metal is poured into the chamber.
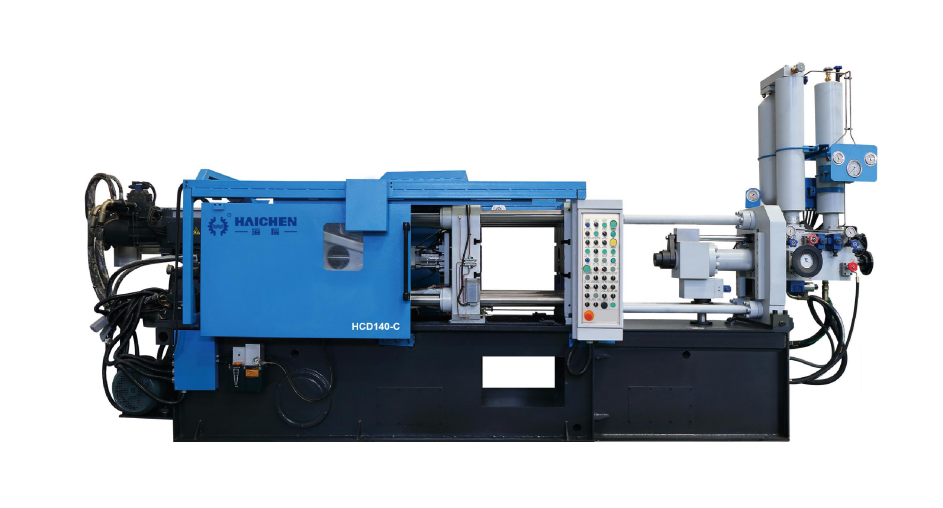
Die casting mould
Mould used in the pressure casting process, its main function is to inject molten metal into the cavity under high pressure, and cool and solidify the shape under high pressure.
Instead,the die-casting mould is usually composed of a moving mould and a fixed mould, the moving mould is fixed on the middle plate of the die-casting machine.
And the fixed mould is fixed on the fixed plate of the die-casting machine.
When the mould is closed, a cavity is formed, and the liquid metal fills the cavity under high pressure.
When the mould is opened, the moving mould is separated from the fixed mould.
And the casting is pushed out with the help of the push-out mechanism located on the moving mould.
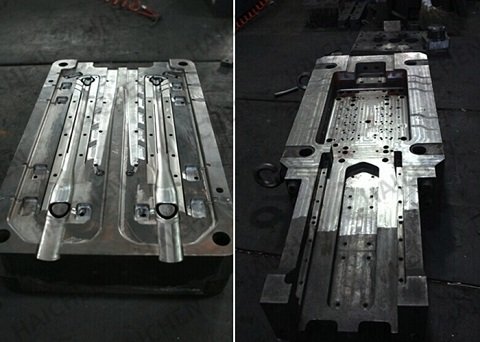
Die casting raw materials
Alloy raw materials mainly include:
- Zinc
- Aluminum
- Magnesium
- Copper
- Ferroalloys
Zinc alloy
Zinc alloy has good fluidity, low melting point, and can be processed after electroplating.
And is widely used in the mobile phone industry and bathroom industry.
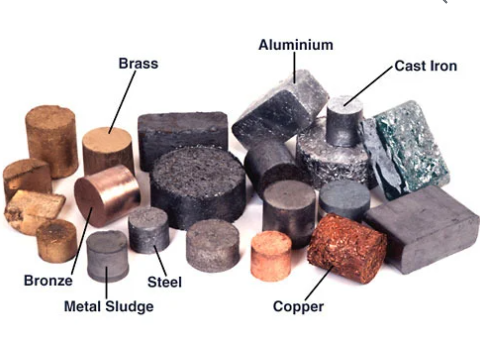
Aluminum alloy
Aluminum alloy has low density, high strength, excellent electrical and thermal conductivity.
And is widely used in aircraft, ships, automobiles, electronic instruments and other fields.
Magnesium alloy
Magnesium alloy has low density, high specific strength, good heat dissipation and good shock absorption.
And is suitable for mobile phones, communication equipment, auto parts and medical equipment.
Copper alloys
Copper alloys have high strength and toughness, good corrosion resistance and wear resistance,
And are commonly used in fields such as electronic communications, aerospace and shipbuilding.
Ferroalloys
Ferroalloys have high strength and hardness, and are widely used in industrial fields such as automobiles and machinery.
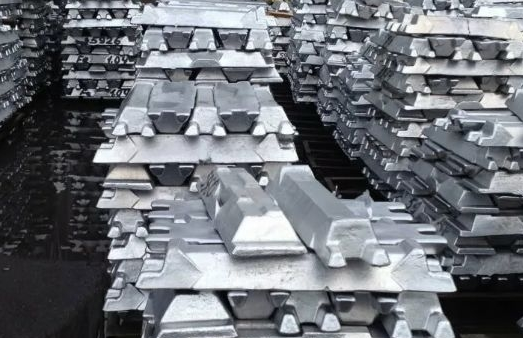
Haichen die casting Technology
Haichen currently has several innovative die casting technologies or methods that can effectively deal with them:
- Integrated Die Casting
- Semi-solid rheological die-casting
- Local extrusion technology
- Binder-free, mould-wall-free die casting
- Vacuum die casting
Integrated Die Casting
This technology uses a large tonnage die casting machine to highly integrate multiple individual and dispersed aluminum alloy parts.
And form die casting into 1-2 large aluminum castings at one time.
Semi-solid rheological die-casting
Compared with traditional die-casting, this process has the advantages of low forming temperature, stable filling and small solidification shrinkage.
It is able to improve the porosity defects of the casting and improve the overall quality of the casting.
Local extrusion technology
For surface and internal defects such as wrinkling, cold separation, poor filling, shrinkage porosity, and porosity of die castings.
Local extrusion technology can distinguish good products from bad products before casting processing.
Following, has advantages in the production of airtight products and thick-walled die castings.
Binder-free, mould-wall-free die casting
The new mould design allows metal powders such as iron, copper, and aluminum to die cast without the need for binders and mould wall lubricants.
This design reduces mould wear and improves the life of the mould.
Vacuum die casting
By performing die casting in a vacuum environment.
Generally,It can effectively reduce porosity and other defects in the casting, thereby improving the strength and quality of the casting.
Haichen’s die casting application
Haichen’s die-casting technology is suitable for automotive engine components such as engine blocks, crankcases, and transmission housings.
In addition, aluminum alloy die-casting parts have broad application prospects in new energy vehicles, including lithium battery housings, gearbox boxes.
The development trend of die casting technology is to develop in the direction of serialization, large-scale and automation,
And at the same time, combine computer simulation technology and CAE software for simulation to optimize the die casting process.
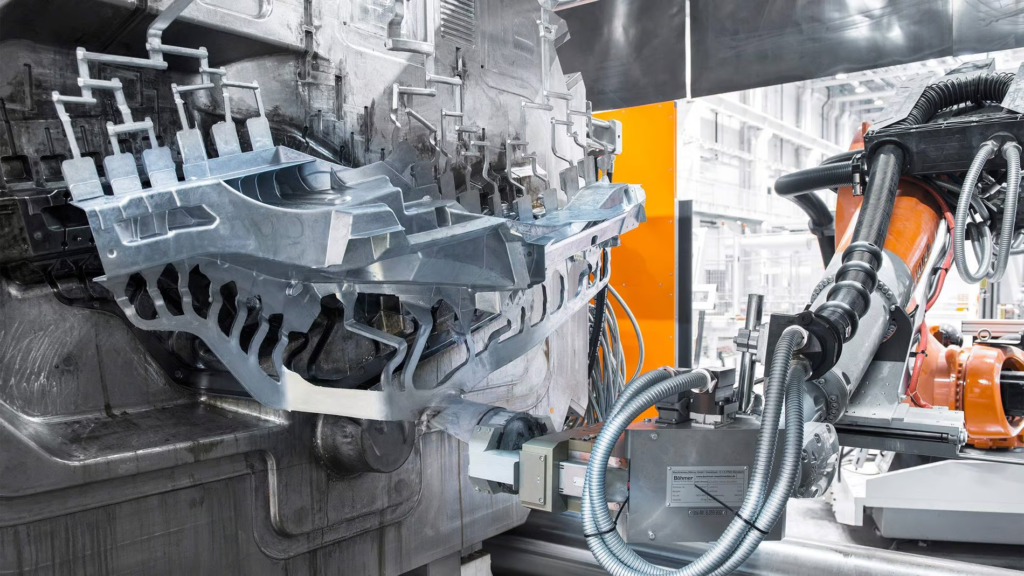