An aluminum die casting design guide provides essential information on optimizing part design, material selection, and process parameters to ensure high-quality, efficient production of aluminum castings.
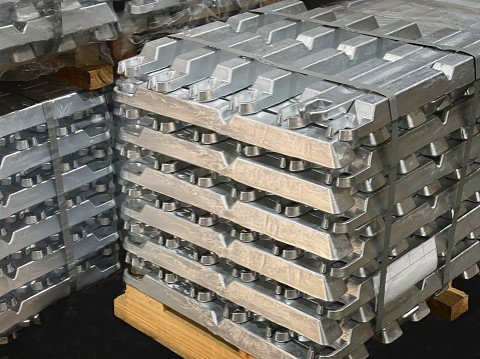
Die casting is a process of manufacturing where parts are made by injecting metal under high pressure into a metal mold.
This guide will help understand principles of aluminum die casting. As well as things to consider when designing parts that are easier and more efficient to produce using this technique.
Understanding Aluminum Die Casting
Aluminum die casting refers to the process of casting aluminum alloys that are at least partially molten into steel dies. Some characteristics of this process include:
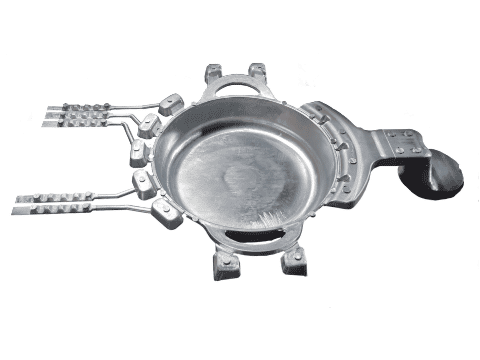
- Speed: Aluminum die casting is an incredibly fast process; it permits the mass production of complex parts.
- Precision: Parts with intricate details, shapes and dimension will be accurately and precisely produced.
- Surface Finish: Parts have negligible post-processing performed on them, thus having good surface finish.
Aluminum die casting design guide-Design Considerations
The following should also be considered as you design the parts to be used in aluminum die casting:
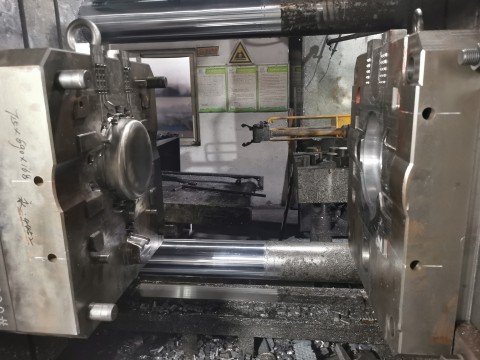
- Wall Thickness: Uniform wall thickness should be maintained for even cooling to prevent warping.
- Draft Angles: Suitable draft angles should be there for core and cavity portions that allow for easy removal from the die.
- Rib and Boss Design: Ribs and bosses should be placed in thin sections in reinforcement without causing over stress concentrations.
- Gating and Risering: Effective gates and risers are critical to achieve complete filling of the mold cavity. And to account for material contraction.
- Material Selection: Each part of the assembly has a unique set of properties that demands an appropriate corrosion resistant aluminum alloy.
Common Problems and Remedies in the Design of Aluminum Die Casting
- Pore Defects and Shrinkage
- Surface Defects
- Deficient Mechanical Strength
Pore Defects and Shrinkage
- Causal Analysis:
- Elevated Injection Velocity: Excessive injection flow rates can cause entrapment of air in the cavity which leads to void formation.
- Inadequate Ventilation of Molds: Poorly constructed exhaust ports can obstruct the free passage of air and cause the formation of voids.
- High Gas Content in the Material: The availability of gases within the raw material can become released during injection, leading to void formation.
- Irregular Cooling Rates: Sub-optimally designed cooling systems can result in uneven cooling, resulting in pore formation.
- Solutions:
- Modification of Injection Rate: Increase the injection rate to allow smooth movement of materials and reduced air pockets.
- Enhanced Ventilation of Molds: Increase the amount and diameter of sumping pipes to enable smooth passage of air.
- Vacuum Casting Technology: Use vacuum casting methods to minimize the gases within the material.
- Enhanced Cooling System: Develop better increased temperature control channels for stable temperature regulation without causing pores or shrinking voids during the cooling process.
Surface Defects
- Cause Analysis:
- Poor Mold Surface Treatment: Wearing down of parts or uneven coating on molds leads to scratches which surface defects on parts.
- Material Quality Issues: Any specks of unwanted materials gives rise to numerous minor holes or scratches on surfaces of components.
- Higher than normal mold injection speed or Pressure: Achieving surface quality can negatively be affected by turbulence from high surfaces injection speed or pressure.
- Solutions:
- Regular Mold Maintenance: Regular Maintenance on Molds: Repair scratches and wear while inspecting mold which aids in a smooth surface for the molds to achieve surface interaction.
- Use High-Quality Materials: Utilize raw resources with minimal specks in excess materials making them the primary constituents.
- Optimize Injection Parameters: Adjusting the speed and pressure at which material flows controls both smoothing and turbulence.
Deficient Mechanical Strength
- Cause Analysis:
- Improper selection of alloys hinders designs: Put forth ensures any selected alu contributes towards work rate targets.
- Changes in the Speed of Withdrawal: Freezing the body of an object too fast during the cooling stage creates internal pressure while doing it at a slower pace renders material ineffective.
- Parameterization of Injection and Delay: Increase in parameters alongside pressure, speed of injection results in changes in structure and properties of a component.
- Solutions:
- Optimize Material Selection: Choose the appropriate aluminum alloy to ensure its chemical and physical properties meet the design requirements.
- Adjust Cooling System: Design efficient cooling channels to ensure uniform cooling and reduce internal stresses.
- Optimize Injection Parameters: Adjust injection speed, pressure, and hold time to optimize the microstructure of the part and improve mechanical properties.
- Post-Treatment Processes: Use heat treatment and other post-processing techniques to further enhance the strength and toughness of the part.
By addressing these common issues with the appropriate solutions, manufacturers can effectively improve the quality and performance of aluminum die castings.
Advantages of Aluminum Die Casting – Aluminum die casting design guide
- Strength and Durability: The Aluminum Parts Exhibit strength, lightness, and durability.
- cost-effectiveness: Low costs for complex shapes because of high production efficiency.
- Versatility: From automotive to consumer electronics, the application range is wide.
Haichen Machinery – manufacturer of aluminum die casting machine
We can process a variety of complex components with consistent quality and performance because the Haichen Machinery aluminum die casting machines that we provide are built to aluminum die casting precise standards.
Reduce costs and improve production efficiency with advanced die-casting solutions from Haichen Machinery.
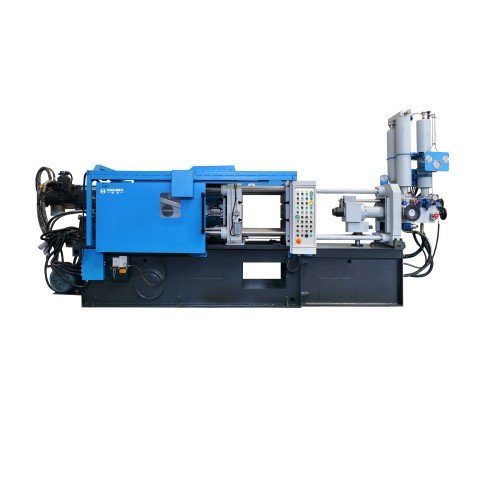
To fully utilize the advantages of aluminum die casting, the design guidelines of aluminum die casting need to be understood.
The guidelines can be followed to produce high quality parts meant to serve a variety of industries.