Mould temperature controller‘s main function of mould is to control the temperature of the mould precisely.
It ensures that the mould can maintain a consistent and stable temperature during the production process.
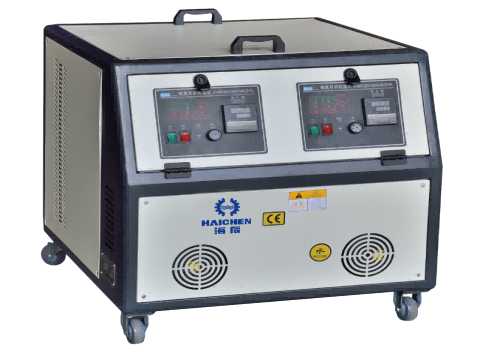
This improves product quality and production efficiency.
Mold Temperature Controller plays a vital role in the plastic injection moulding process.
In practice, the mould temperature controller is commonly used in metal die casting, plastic injection moulding, rubber moulding, composite material moulding and other manufacturing processes.
Its main role includes:
1. Improve product quality
2. Energy saving and consumption reduction
3. Improve production efficiency
4. Extend the life of the mould
1. Improve product quality:
By precisely controlling the mould temperature, internal stress can be reduced.
Avoid problems such as product deformation, shrinkage or structural failure caused by uneven temperature.
2.Energy saving and consumption reduction:
The mould temperature controller can heat or cool according to the actual need.
It reduces energy waste, thus reducing energy consumption and operating costs.
3.Improve production efficiency:
By keeping the mould temperature stable, it can shorten the production cycle, improve the production efficiency and reduce the scrap rate.
4. Extend mould life:
By avoiding thermal shock to the mould caused by overcooling or overheating.
It can prolong the service life of the mould and reduce the maintenance cost.
Mould temperature controller is an indispensable equipment in modern manufacturing industry, which ensures the consistency of product quality and high efficiency of production by precisely controlling the mould temperature.
How mould temperature controllers improve product quality?
Mould Temperature Controller can improve productivity and product quality by regulating the mould temperature, manufacturers can ensure consistent quality of each product.
Mould temperature controllers are able to accurately control the temperature of the mould, which is essential for the production of complex parts with specific dimensional requirements.
This feature plays an important role in improving product quality.
The influence of mould temperature on product quality is mainly reflected in the following aspects:
1. Surface quality
2. Shrinkage and dimensional stability
3. Production efficiency
4. Material properties
5. Defect control
1.Surface quality:
The mould surface quality of the product can be affected by either too high or too low a mould temperature.
Too low a mould temperature can lead to knit lines, while too high a temperature can lead to product distortion or blistering.
These problems can be avoided by precisely controlling the mould temperature, thus improving the appearance of the product.
2. Shrinkage and dimensional stability:
Mould temperature control helps to reduce product shrinkage and dimensional errors and ensures product uniformity during the moulding process.
This is especially important for parts that require high precision and consistency.
3.Production efficiency:
Proper mould temperature control reduces downtime and speeds up production, thereby increasing productivity.
By optimising mould temperature control, production cycles can be shortened and energy consumption reduced, resulting in cost savings.
4.Material properties:
Different materials have different sensitivities to mould temperature.
For example, certain polymers may thermally degrade or oxidise at too high a mould temperature, resulting in a decrease in molecular weight and mechanical properties.
Therefore, by accurately controlling the mould temperature, these adverse effects can be avoided and the full performance of the material can be ensured.
5. Defect control:
Mould temperature controller can effectively control defects in the production process, such as cold flow, shrinkage holes, flow lines, sticking, etc..
By accurately controlling the mould temperature, the incidence of these defects can be significantly reduced and the product qualification rate can be improved.
In order to achieve the best mould temperature control results, manufacturers need to choose the right temperature controller and configure it according to specific needs.
For example, use water or oil as the heat transfer medium and ensure that the flow and pressure of the cooling system meets the requirements.
In addition, temperature sensors installed inside the mould can provide higher control accuracy, but the location of the sensor needs to be considered to ensure that its impact on product quality is minimised.
By accurately controlling mould temperature, mould temperature controllers can significantly improve product quality, productivity and material properties, while reducing production costs and defect rates.
This is a critical technological tool for the modern plastic injection and metal die casting moulding industries.
Mould temperature controller extends the life of the mould
Mould temperature controllers play an important role in extending the life of the mould.
The following are its main mechanisms and methods:
1. The importance of temperature control:
2.Temperature control technology:
3.Temperature control strategy:
4. Maintenance and upkeep:
5. Optimise the design:
1. The importance of temperature control:
Mould temperature has a significant effect on the quality of die castings and mould life.
Uneven or excessive mould temperature can lead to problems such as dimensional instability and deformation of castings, thus shortening mould life.
By precisely controlling the mould temperature, it can effectively reduce the scrap rate, improve the production efficiency and prolong the mould life.
2.Temperature control technology:
2.1 heat conduction oil circulation system:
In magnesium alloy die casting, the use of high temperature heat conduction oil circulation system for temperature control, through the adjustment of heat conduction oil flow or temperature to control the heating and cooling of the mould, so as to maintain a constant mould temperature.
This method can effectively solve the mould preheating and cooling problems, improve the quality of die casting and production efficiency.
2.2 PID control:
The application of PID controller in plastic injection moulding can achieve precise regulation of the mould temperature, optimize the efficiency of the injection cycle and temperature control algorithm, ensure uniform temperature on the surface of the mould, and improve the cooling efficiency.
3.Temperature control strategy:
3.1 Temperature balance:
Maintain uniform temperature distribution inside the mould to avoid concentration of thermal stress caused by excessive temperature difference, thus reducing fatigue damage and crack generation in the mould.
3.2 Preheating and cooling management:
During the die casting process, the die needs to be gradually heated up to operating temperature and preheated to the required average die temperature before production begins. This helps to reduce high stresses on the tool surface and extends mould life.
4. Maintenance and upkeep:
4.1 Regular inspection and maintenance:
Keep the working environment clean and regularly check the piping connections and cooling water circulation to avoid equipment damage.
For oil heaters, change the heat transfer oil regularly according to the usage temperature to prevent scaling and clogging.
4.2 Use wear-resistant materials:
Consider using wear-resistant materials or coatings to enhance the wear resistance of mould parts, such as cavities, cores and slides, etc. These measures can improve the wear resistance of the mould and extend its service life.
5. Optimise the design:
5.1 Cooling system design:
Optimise the design of the cooling water pipe to ensure that the flow of coolant and cooling rate are appropriate.
Avoid too strong or too weak cooling affecting the quality of the workpiece.
5.2 Rapid thermal cycle technology:
Rapid thermal cycling injection moulding technology improves product quality and productivity through rapid heating and cooling, while reducing thermal stress and fatigue damage to the mould.
Through the above methods, the mould temperature controller can not only improve the moulding quality and productivity of the products, but also significantly extend the service life of the moulds, reduce the production cost and improve the profitability of industrial projects.
How mould temperature controllers save energy and reduce consumption?
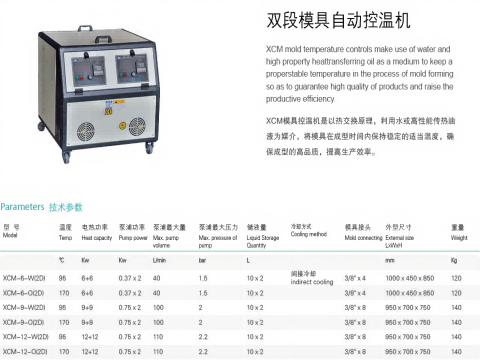
Haichen’s Mould Temperature Controllers (MTC) have a significant role to play in saving energy and reducing consumption through a variety of precise control systems.
The following are our main energy saving mechanisms:
1. Precise temperature control:
2. Intelligent control systems:
3. Variable frequency drives and energy saving circuits:
4. Circulating Water System:
5. Automation and automatic exhaust function:
6. Reduced maintenance requirements:
7. Energy-saving design:
8. Reduce production cycle time:
9. Recycling of waste heat:
1. Precise temperature control:
The Mould Temperature Controller is able to ensure consistent heating conditions during the injection moulding process by precisely controlling the temperature of the mould.
This precise control helps to reduce energy wastage as the heating system operates only when required, thereby reducing energy consumption.
2. Intelligent control systems:
Haichen’s mould temperature controllers incorporate an intelligent control system.
Advanced algorithms and predictive analyses are used to adjust temperature parameters in real time to changes in environmental conditions or material properties.
These systems optimise energy use and reduce unnecessary energy consumption.
3. Variable frequency drives and energy saving circuits:
Haichen mould temperature controllers are designed with energy efficiency in mind, using variable frequency drives and energy saving circuits to minimise energy consumption.
These designs not only reduce operating costs, but also comply with sustainable manufacturing practices.
4. Circulating Water System:
Mould temperature controllers typically use water as the heat transfer medium to achieve heat exchange through direct or indirect cooling.
This design in use at Haichen offers the advantages of high heat transfer efficiency, low pollution, easy access to water and low cost.
5. Automation and automatic exhaust function:
Mould temperature controllers are equipped with an automatic air venting function that removes air from the system at start-up, reducing the increase in energy consumption caused by air blockage.
6. Reduced maintenance requirements:
By optimising the configuration of the temperature control system, it is possible to reduce maintenance requirements and extend equipment life.
For example, Haichen Smart Configuration can reduce the number of temperature control units while improving product quality and productivity.
7. Energy-saving design:
Our mould temperature controllers feature energy-saving designs, such as PID multi-stage temperature control systems, which can save up to 35% of electricity.
In addition, some special models also adopt heating design, which is suitable for use in different temperature control places to further improve energy-saving effect.
8. Reduce production cycle time:
By accurately controlling the mould temperature, the injection cycle time can be reduced, thus increasing productivity and throughput rate.
This not only reduces energy consumption, but also lowers production costs.
9. Recycling of waste heat:
Haichen mould temperature controllers are able to recycle waste heat.
By incorporating special heat exchange circuits the preheating time can be significantly shortened and power consumption reduced.
Through these mechanisms, Haichen mould temperature controllers significantly reduce energy consumption and operating costs while improving product quality.
Environmentally friendly and cost-effective.