The process of vacuum machine for a die casting machine is used to enhance the quality of cast parts by reducing air entrapment and porosity.
This technique involves using a vacuum system to evacuate air and gases from the die cavity before or during the injection of molten metal.
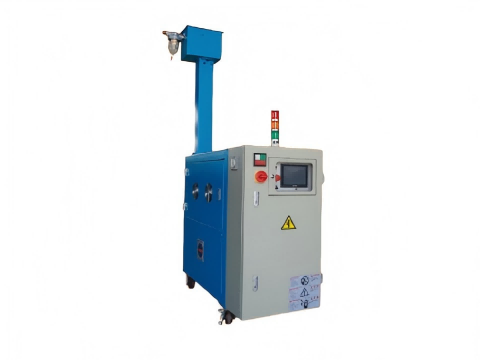
The process of vacuum machine
Die Preparation of the process of vacuum machine
- Die Coating: Coating the molds with a release agent to ensure that the castings drain smoothly.
- Sealing: The fuction of sealing is to create a closed system that can maintain a vacuum.
Setup of the Vacuum System
- Vacuum Channels: Fit the die with vacuum channels that connect the cavity to the vacuum pump.
- Vacuum Pump Connection: Connect vacuum pump to the channels to evacuate air from the die cavity.
Vacuum Application
- Air Evacuation: Before the molten metal is injected, the vacuum pump removes air, gases, and any moisture from the die cavity. This creates a low-pressure environment.
- Monitoring: Sensors monitor the pressure in the die cavity to ensure the vacuum reaches the desired level.
Metal Injection of of the process of vacuum machine
- Molten Metal Injection: Once the vacuum is achieved, the molten metal is injected into the die cavity under high pressure.
- Bubble Prevention: The vacuum eliminates or significantly reduces air pockets and gas entrapment, ensuring the metal fills the cavity completely and uniformly.
Solidification of the process of vacuum machine
- Cooling: The molten metal solidifies inside the vacuum-sealed die, often aided by cooling systems.
- Vacuum Maintenance: The vacuum may be maintained during solidification to ensure that no air enters the cavity and compromises the casting.
Mold Opening and Part Ejection
- Pressure Equalization: After solidification, the vacuum is released, and the die cavity is returned to atmospheric pressure.
- Part Removal: Eject the casting from the die, ensuring it is now free of porosity and other defects caused by trapped gases.
Benefits of Vacuum-Assisted Die Casting
- Reduced Porosity: Eliminates air and gas pockets, leading to stronger, denser castings.
- Improved Mechanical Properties: Enhances strength, fatigue resistance, and dimensional accuracy of cast parts.
- Better Surface Finish: Results in smoother surfaces with fewer defects.
- Increased Efficiency: Reduces scrap rates and minimizes the need for secondary operations like machining or welding.
- Larger Thin-Wall Castings: Enables the production of complex parts with thin walls due to improved metal flow.
Haichen vacuum machine for die casting machine
Haichen is a die casting machine factory located in Ningbo, China, mainly supplying cold chamber die casting machine and hot chamber die casting machine.
Besides machines, we also supply die casting auxiliary equipments, including vacuum machine, ladles and extractors and so on. Our vacuum machine reduces porosity and enhances the mechanical properties of cast components. And it Produces smoother surfaces, reducing the need for post-processing.
If there is any requirement, please feel free to consult us.
The advantage of vacuum die casting technology is that it can significantly reduce the porosity and dissolved gases in the castings, thus improving the mechanical properties and surface quality of the castings.