Frying pan production steps involves several steps, from preparing the die to casting and finishing the frying pan.Here’s a step-by-step guide to producing a die-cast frying pan.
Design and preparation of the mold
Melt the metal
Inject the molten metal
Cooling and solidification
Demolding and post-processing
Assembly and Packaging
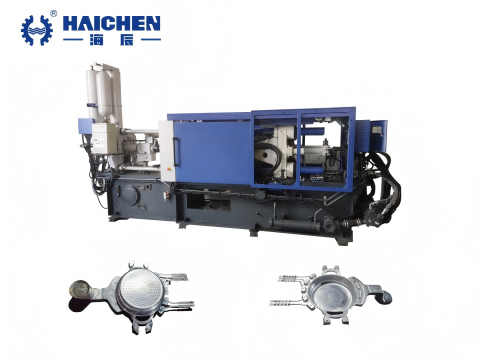
Die casting is primarily used for creating metal parts with high precision, and it’s typically employed for non-ferrous metals like aluminum, zinc, or magnesium.
Frying pan production steps
Design and preparation of the mold
Designing the Mold:
- Design the mold based on the shape and dimensions of the frying pan.
- And CAD can be used to design the mold by considering the structure of mold parting surfaces, cavities, cores, gating system, cooling system and ejector pins.
Manufacture the mold of frying pan production steps:
- The professional mold maker uses high precision CNC machine (CNC) for processing and manufacturing accrording to the mold.
Mold Preparation:
- Prior to die casting, workers need to clean and heat the mold, and its inner surfaces sprayed with a lubricant or refractory material.
Melt the metal of frying pan production steps
Selection of materials:
- The commonly used materials for die-casting frying pans are aluminum alloy, and magnesium alloy and zinc alloy.
- Aluminum alloys have good strength and lightweight properties. And zinc alloys are suitable for complex shapes, and magnesium alloys have a high strength-to-weight ratio.
Inject the molten metal of frying pan production steps
Injection process:
- The molten metal is transferred into the die casting machine and then injected into the mold cavity under high pressure.
- The piston of the die casting machine pushes the molten metal into the mold at very high speeds and pressures (up to 100-1800 bar).
Cooling and solidification of frying pan production steps
Cooling phase:
- After injection, the mold remains closed, allowing the metal to cool and solidify within the mold.
- The high thermal conductivity of the metal and mold material contributes to rapid cooling, which is critical for fast production cycles. Also, controlling the cooling rate prevents warpage or defects in the casting.
Demolding and post-processing
Mold Release:
- When the metal is fully solidified, also the mold is opened and the casting is pushed out of the mold using an ejector mechanism.
Post-processing:
After demolding, the casting may require some post-processing operations such as removal of sprue system components such as gates and risers.
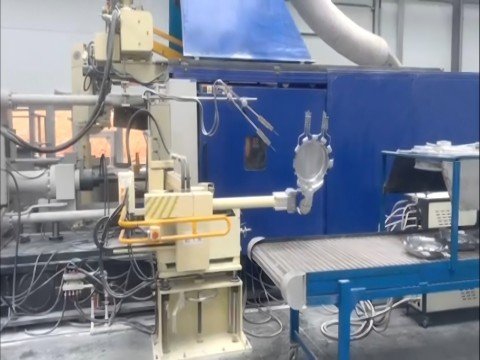
Assembly and packaging
Assembly:
- If the skillet consists of more than one part, you need to assemble these parts. For example, attaching components such as handles to the body of the skillet.
Packaging:
- Finally, the finished skillet is packaged for transportation and sale. You should package the skillet to ensure that it is not damaged during transportation.
Haichen Frying Pan with die casting machine
Haichen is a die casting machine factory located in Ningbo, China, mainly supplying cold chamber die casting machine, hot chamber die casting machine and some auxiliary machines for die casting machine. And we have rich experience in producing frying pan.
So with the above steps, you can efficiently produce high quality cast aluminum frying pans using die casting machines. This production method not only improves productivity, but also ensures the strength and durability of the product.