How to choose release agent mixer
Rrelease agent mixer for a die casting machine, there are several factors to consider,to ensure that the release agent can be effectively applied to the die casting process and meet the production needs.
Type of release agent
According to the material and process requirements of the die casting, select the appropriate type of release agent.
For example, water-based release agents are often used for aluminum alloy die casting.
Because of their good high temperature resistance and environmental protection properties.
Therefore, the choice of release agent should consider its composition, concentration, and compatibility with the mould temperature.
The mixing ratio of the release agent
The mixing ratio of the release agent to water should be adjusted according to the specific process needs.
The common ratio is 1:80 to 1:150, but the specific ratio needs to be optimized according to the size, wall thickness and complexity of the die casting.
In some cases, such as aluminum alloy die casting, the ratio of release agent to water may be 1:200.
Configuration of the release agent mixer
Precise proportioning and homogeneous mixing can be achieved with a fully automatic release agent proportioning machine.
This type of equipment typically includes components such as dope suction tubes, dispensers, mixing drums, diaphragm pumps, etc.
Which can automatically control the amount of water inlet and the supply of release agent.
The design of the proportioning machine should be able to adapt to different tonnage die-casting machines.
Such as the single type is suitable for die-casting machines ranging from 250 tons to 3000 tons.
While the centralized type is transported to each die-casting machine through pipelines.
Environmental and safety considerations
When choosing a release agent, consider its impact on the environment.
For example, water-based release agents do not produce harmful gases at high temperatures, making them more environmentally friendly.
The thermal stability of the release agent is also important to prevent decomposition at high temperatures or the formation of harmful substances.
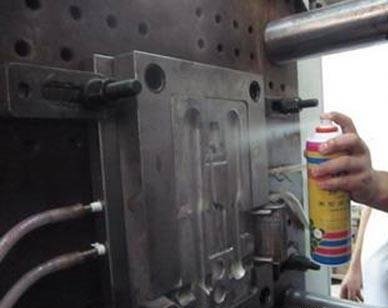
Choose the right release agent
Die casting machine release agent is a lubricant used in the metal die casting process.
Its main role is to help metal products from the mould smoothly and maintain the integrity and subsequent processability of the casting.
The die casting release agent forms a thin film on the surface of the mould to prevent the casting from sticking to the mould.
Thereby improving production efficiency and product quality.
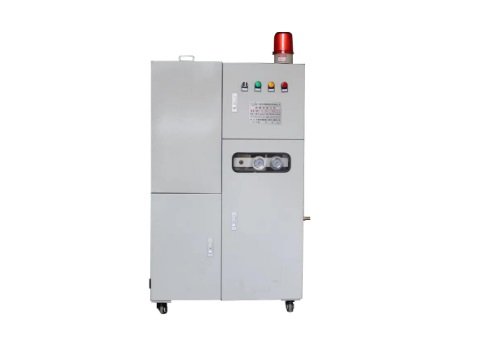
Type of release agent
Oil-based release agents
These release agents typically consist of mineral or synthetic oils, silicone oils, and lubrication additives.
They have good lubricating properties, but they are gradually phased out due to environmental pollution and health risks.
Water-based release agent
This release agent uses water as a carrier and can be diluted into a variety of concentrations.
Which is widely used in aluminum alloy die casting. Its main components include base materials (such as oils, waxes, silicones, etc.), emulsifiers, and water.
Water-based release agents are favored for their environmental friendliness and cost-effectiveness.
Powder release agent
Powder release agents are mainly made of wax and other materials, are suitable for high temperature and high pressure environments, have good chemical stability, and do not pollute water quality.
The mixing ratio of the release agent
When using water-based release agents, the ratio of release agents to water needs to be tightly controlled to avoid the formation of overly thick surface coatings or overly thin effects.
If the proportions are not right, it can lead to mould adhesion or surface defects.
Oil-based release agents are typically mixed between 70% and 98%, with the solvent ratio adjusted for the specific application.
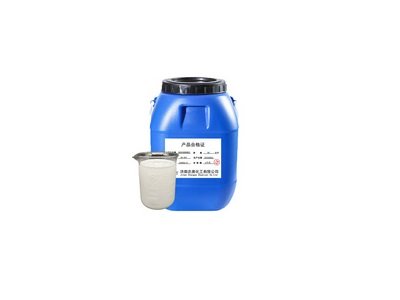
The effect of mould temperature on the release agent
Too high or too low a mould temperature will affect the adsorption effect of the release agent.
If it is too low, the paint will not be deposited, and if it is too high, the paint will be washed away by the vapor.
In die casting production, uneven mould surface temperatures can lead to different degrees of heating of the release agent.
Which can affect the thickness and uniformity of the lubricating film.
Optimal mould temperature
Generally, the optimal mould temperature is about 40% of the casting temperature.
For example, the optimal mould temperature for aluminum alloy die-casting is 250-300°C.
Water-based release agents evaporate quickly at high temperatures.
So it is important to choose a release agent that can withstand higher temperatures.
Precautions
Different presses, mould structures and mould temperature control methods may lead to mould temperature differences.
And it is necessary to choose the appropriate release agent according to the actual situation.
In practice, the most suitable release agent can be selected through experimentation and optimized in combination with mould temperature control technology.
Choosing the right release agent requires a combination of mould temperature.
Thermal stability of the release agent, and the specific conditions of the mould.
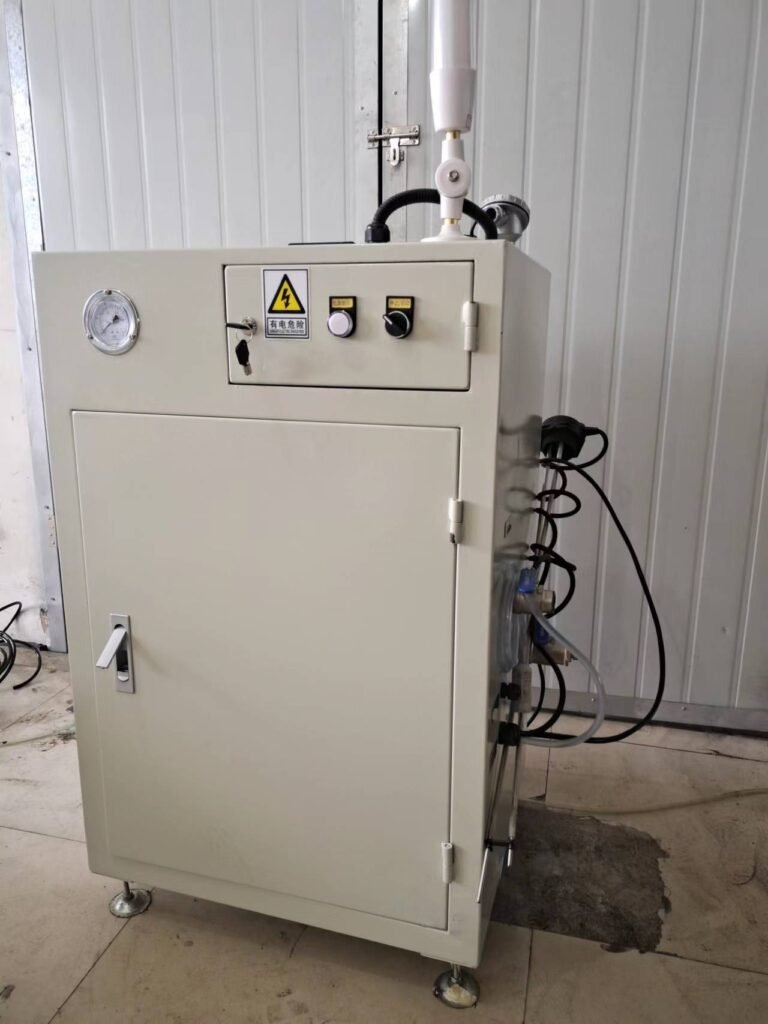
Haichen’s release agent mixer
Automation equipment
Die-casting release agent recovery, filtration and reuse ratio all-in-one machine, using automatic design, solves the problem of waste release agent discharge, avoids high disposal costs.
And eliminates the environmental problems and waste of resources caused by the accumulation of waste release agent.
Intelligent automatic monitoring and proportioning system
The integrated machine for the recovery of mould release agent has realized the efficient recovery and secondary use of the mould release agent waste liquid, and significantly reduced the consumption of release agent.
The equipment can remove wax, particles, miscellaneous oils, sterilization and deodorization.
And only 2% of the waste liquid is left after purification, which greatly reduces the cost of sewage treatment.