The global aluminum die casting market reached approximately USD 28.1 billion in 2023.
And is expected to grow to USD 40 billion by 2032 at a compound annual growth rate (CAGR) of 3.9%.
This growth is primarily driven by sustainable manufacturing practices.
Particularly in the aerospace sector and efforts to reduce fuel consumption and improve energy efficiency.
Regionally, Asia-Pacific is the largest contributor to the aluminum die casting market.
While North America and Europe also maintain strong growth momentum.
North America is leading the way in terms of technological advancement and market share.
While Asia-Pacific is growing rapidly due to industrialization and demand from the automotive industry.
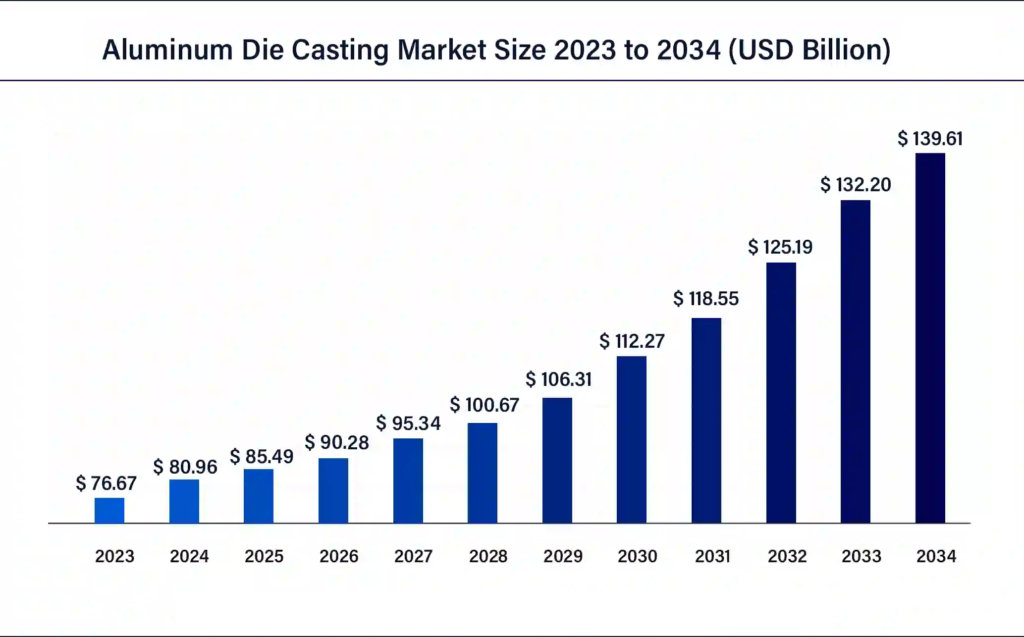
Aluminum Die Casting Machinery Market Growth Forecast
Market size and growth rate
The global aluminum die casting machinery market reached USD 5,776.9 million in 2022.
And is expected to grow to USD 8,875.6 million by 2032, registering a compound annual growth rate (CAGR) of 4.4%.
Another report pointed out that the global aluminum die casting machinery market reached 53.341 billion yuan in 2023.
And is expected to grow to 71.031 billion yuan by 2029, with an average annual compound growth rate of 4.40%.
Fields of application and technological advancements
Aluminum die casting machines are widely used in aerospace, automotive, shipbuilding.
And other industries to meet the growing demand for lightweight components and complex parts.
Technological advancements, such as high-pressure die casting and vacuum die casting, have increased production capacity and quality, driving the market growth.
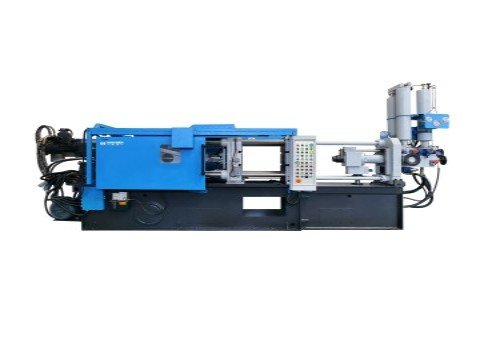
Regional Market Analysis
Asia-Pacific dominates due to industrial development and growing demand from the energy sector.
While Europe is the second largest market due to emissions regulations.
The Chinese market accounts for a significant share of the global aluminum die casting machinery market.
Industry Players and Competitive Landscape
Key industry players are expanding their market share through collaborations, new product launches, and M&A strategies.
The report provides a detailed analysis of Frech, UBE, Japan Steel Works (JSW), HMT Machine Tools Limited, ItalPresse, Toshiba, and Toyo Machinery
Market drivers
The focus on lightweight materials is contributing to the market growth as automakers increase the use of aluminum due to environmental pressures and cost considerations, especially in Europe.
The development of new energy vehicles has promoted the application of aluminum alloy die castings in auto parts.
Challenges and constraints
High capital costs and shortage of skilled workers are the restraints for the growth of the market. Fluctuating raw material prices are likely to restrain the market growth.
The growth forecast for the Aluminum Die Casting Machinery market during 2023 – 2032 is based on forecasts of market size and growth rate.
Application fields and technological advancements, regional market analysis, industry players and competitive landscape, market drivers, and challenges and restraints.
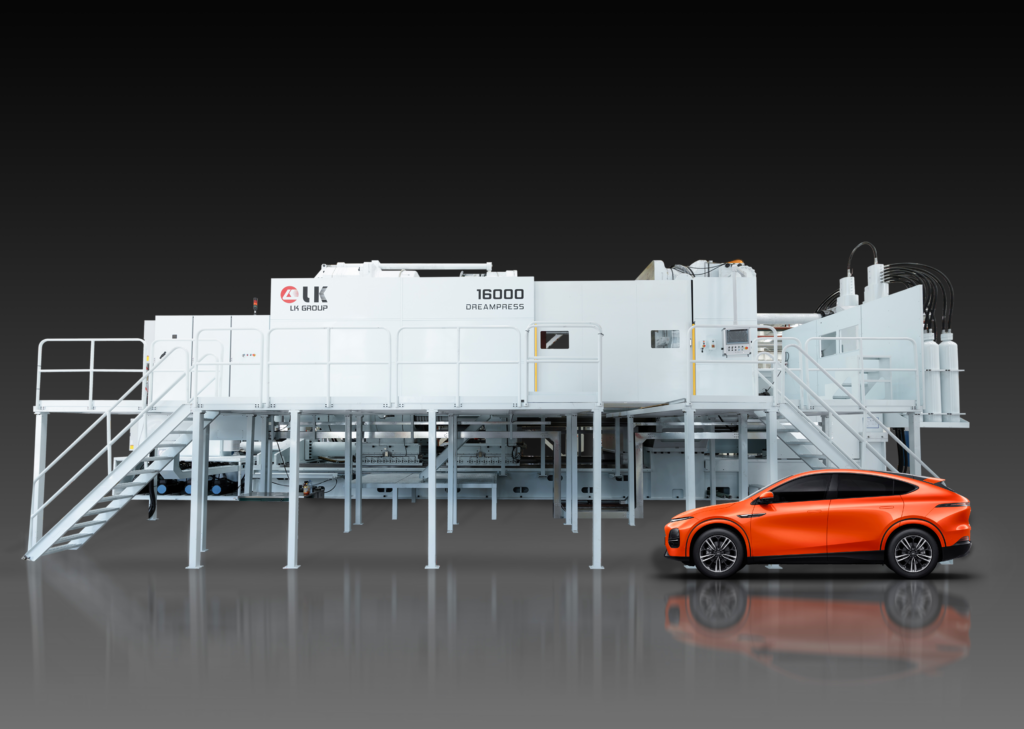
Asia Pacific Aluminum Die Casting Market Size and Growth 2025 to 2034
The Asia Pacific aluminum die casting market size was estimated at USD 41.29 billion in 2024 and is anticipated to reach around USD 71.20 billion by 2034, at a CAGR of 5.7% from 2025 to 2034.
Asia Pacific dominated the aluminum die casting market with the largest share in 2024.
The market growth in the region is driven by the increasing presence of skilled labor, low labor costs.
And the easy availability of raw materials, which makes it the leading region for manufacturers to build production facilities.
China accounted for a major market share in 2023 and is one of the largest manufacturing hubs across the globe.
Moreover, the rising industrialization in the region contributed to the regional market expansion.
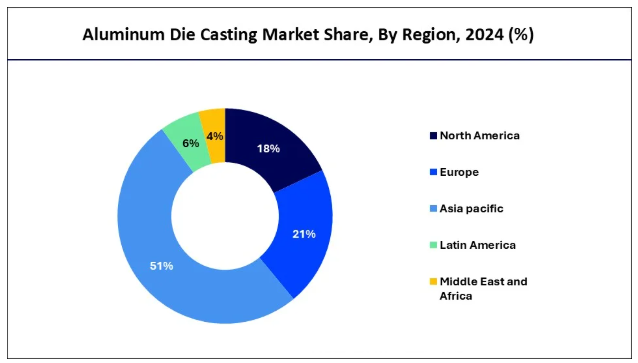
Factors for the growth of the aluminum die casting machinery market
High Pressure Die Casting (HPDC) technology
This technology is widely used in complex automotive and aerospace applications to improve the accuracy and surface quality of castings while reducing defects.
Automation and robotics
The application of automated equipment reduces manual intervention and improves production efficiency and quality stability.
Integrated die-casting technology
Tesla’s technology uses large-tonnage die-casting equipment to integrate multiple parts into a single molding.
Which greatly reduces manufacturing costs and weight, and improves the safety and durability of the body.
Mould technology innovation
New mold design and manufacturing technology has improved casting forming quality and production efficiency.
Advances in materials science
The research and development of new aluminum alloy materials has improved the strength, corrosion resistance and wear resistance of castings, and further met the diverse needs of different industries.
Intelligent and digital technology
Through digital technology and Internet of Things technology, improve production efficiency and quality, and reduce manufacturing costs.
Vacuum die casting and high pressure die casting
These processes help reduce defects and improve surface finish.
Thin-walled die casting molding technology
This technology enables the wall thickness of aluminum alloy die castings to reach 0.3mm, and the wall thickness of aluminum-magnesium alloy die castings is less than 1mm.
Which is conducive to achieving the goal of lightweight.
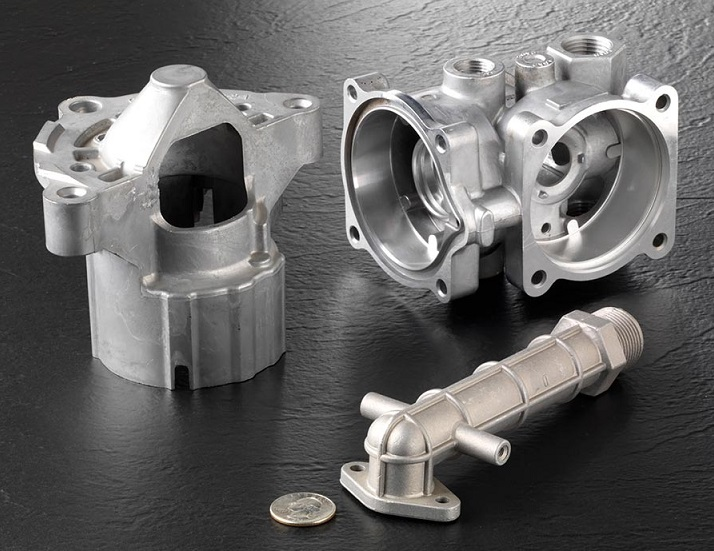
Semi-solid die casting technology
By agitating the liquid metal while it is solidifying, a slurry with about 50% solid composition is obtained, and then die-casting, which improves the yield and surface quality.
Haichen Die casting machinery market response
Aluminum alloy die-casting manufacturers need to strengthen supply chain management.
Reduce raw material procurement costs, and improve production efficiency and profitability.
Increase your sales channels and sales by diversifying your markets, thereby increasing your profit margins.
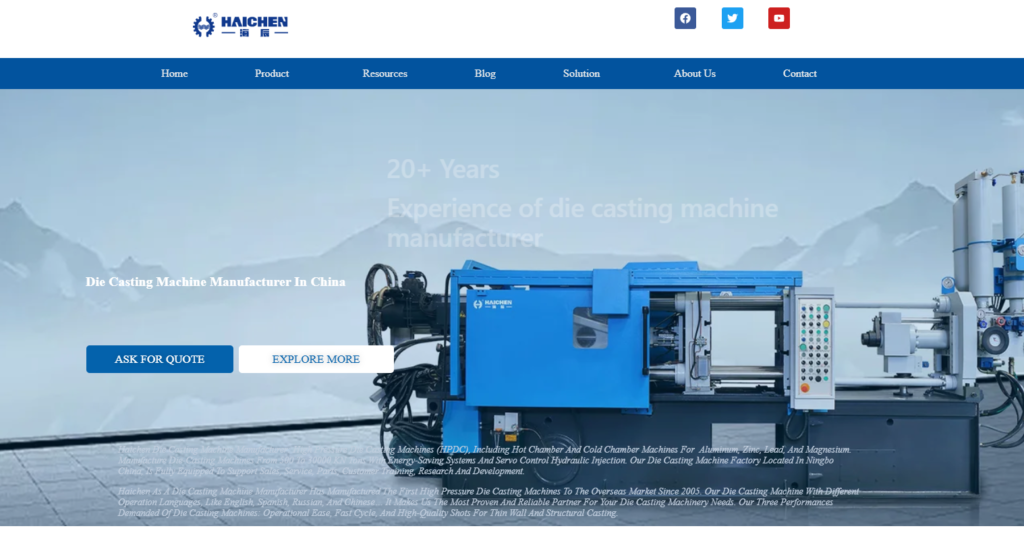