In the die-casting process, “ladle cup” usually refers to the pouring cup (also called external gate). Its core function is to receive the molten metal from the ladle and guide it smoothly into the mold pouring system, while realizing the functions of slag blocking, exhaust and regulating the flow state of the molten metal.
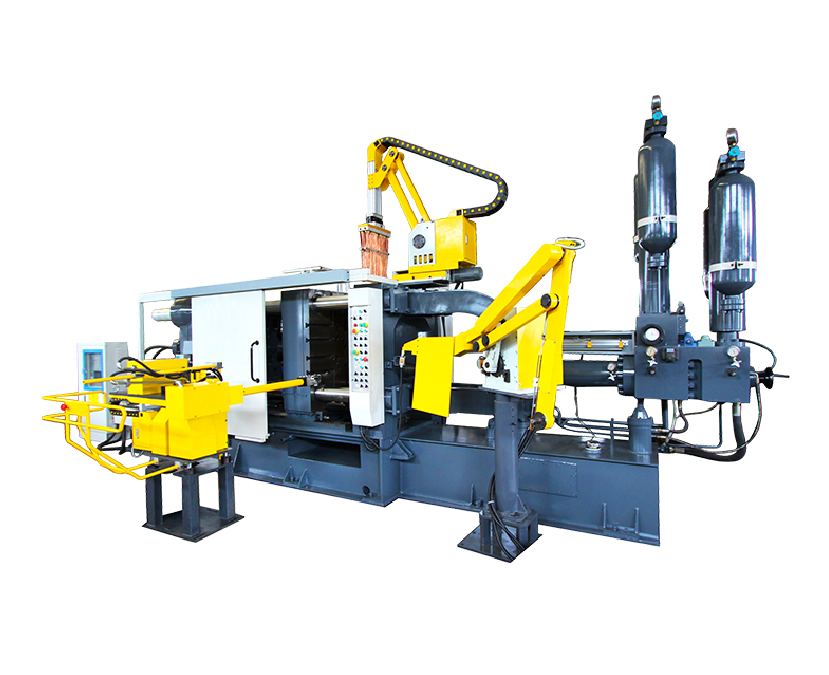
1. Cast Iron Ladle Cups
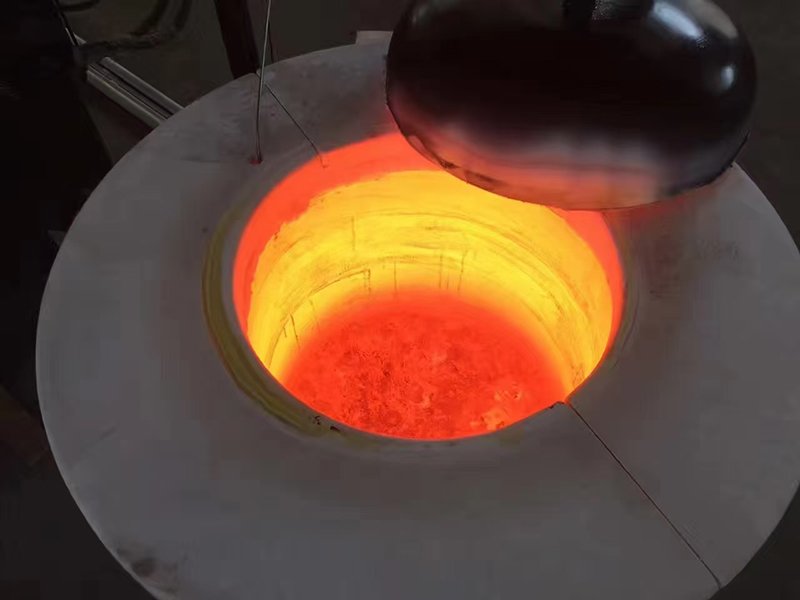
- Material and Coating Innovations
- Modern cast iron ladles are made from high-chromium cast iron or heat-resistant alloy steel to withstand high-temperature erosion from molten aluminum/zinc.
- Surface treatments like thermal-sprayed ceramic coatings (e.g., alumina or tungsten carbide) reduce metal adhesion and extend service life.
- Emerging nanocoatings with superhydrophobic properties are being tested to minimize residual metal droplets.
- Modular Design
- Quick-release mechanisms enable rapid replacement of critical components (e.g., nozzles or liners) without stopping production.
- Standardized interfaces ensure compatibility with various die-casting machine arms.
2. Electric/Automated Ladles
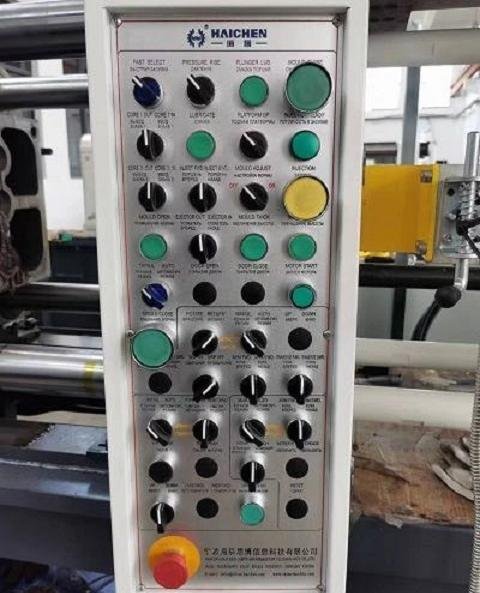
- Smart Control Systems
- Integrated servo motors and closed-loop feedback systems adjust pouring speed and tilt angle in real time, achieving flow-rate stability (<1% error).
- Infrared temperature sensors monitor molten metal to prevent defects like cold shuts or oxide inclusions.
- Collaborative Robotics (Cobots)
- Lightweight cobots (e.g., ABB’s YuMi) paired with vision systems enable flexible, high-precision pouring for small-batch production.
3. Customized Ladles
- Design for Specific Processes
- Sand-casting ladles require larger reservoirs to account for metal shrinkage, while die-casting ladles prioritize fast filling and turbulence reduction.
- Magnesium alloy die-casting demands inert gas-shielded ladles to prevent oxidation and explosions.
- 3D-Printed Ladles
- Metal additive manufacturing (e.g., GE’s Concept Laser) creates complex internal geometries to optimize metal flow. Case: Titanium alloy ladles for aerospace components.
4. Pony Ladles and Vacuum Casting
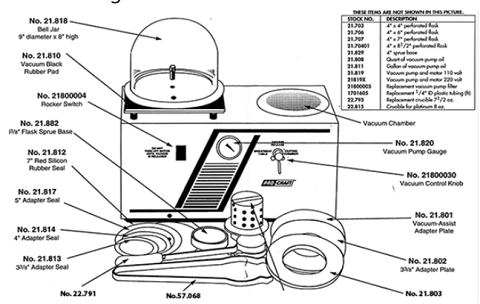
- Vacuum Die Casting
- Sealed ladles maintain stable metal levels during vacuum cycles to avoid air entrapment.
- Dual-chamber ladles separate molten metal storage from controlled dispensing.
- Ladle-to-Ladle (L2L) Systems
- Distribute molten metal to multiple sub-ladles for multi-cavity molds or continuous casting. Example: Automotive engine block production.
5. High-Pressure Die Casting (HPDC) Ladles
- Servo-Controlled Ladles
- Synced with high-speed die-casting machines (e.g.,HCD-880-C) to match injection profiles and reduce air entrapment via dynamic pressure compensation.
- Integrated Dosing Systems
- Fully automated die-casting ladles cup linked to dosing furnaces (e.g., IDRA’s Giga Press for Tesla’s gigacastings) enable continuous metal supply.
6. Emerging Technologies
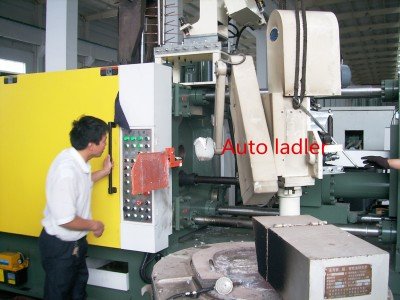
- Induction-Heated Ladles
- Built-in induction coils maintain temperature for thin-walled parts (e.g., 5G heat sinks). Energy-saving designs recover waste heat (20–30% efficiency gains).
- Smart IoT-Enabled Ladles
- Embedded sensors monitor wear, temperature, and lifespan, feeding data to platforms like Siemens MindSphere for predictive maintenance.
- Eco-Friendly Designs
- Recyclable refractory materials (e.g., biomass-reinforced ceramics) and closed-loop metal recovery systems reduce waste and emissions.
7. Industry Applications
Application | Ladle Type | Key Requirements |
---|---|---|
Automotive (Mega Castings) | Servo-dosing ladles | High precision, large capacity (>50kg) |
Consumer Electronics | Induction-heated micro-ladles | Temperature stability, <1kg dosing |
Aerospace (Titanium) | Vacuum-sealed 3D-printed | Oxidation resistance, lightweight |
Medical (Magnesium) | Gas-shielded ladles | Explosion prevention, cleanliness |
Trends and Future Outlook
- Convergence of Technologies: AI-driven parameter optimization, hybrid systems combining robotics and IoT.
- Material Breakthroughs: Graphene coatings, ceramic matrix composites (CMC).
- Market Drivers: EV mega-castings, 3C product lightweighting, and sustainable manufacturing.
Selecting a ladle type requires balancing material compatibility, process demands, volume, and cost. Future systems will emphasize flexibility to support mixed-product production.
Durable die-casting ladle cup willhelp you achieve automation stability in production.
Haichen die casting machine ladler
1. Optional Configuration for Cold Chamber Die Casting Machines
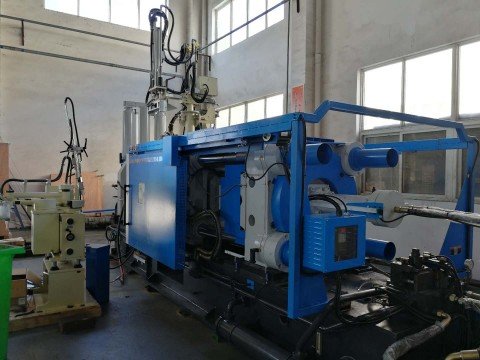
- In the Haichen C-Series Cold Chamber Machines (HCD-C Series), the “Automatic Ladler” is explicitly listed as an optional feature in the configuration specifications.
- For example, under sections like hydraulic systems and mold units, it is noted that the ladler can be added based on customer requirements.
- Haichen also highlights that auxiliary equipment (e.g., automatic sprayers, part extractors, or ladlers) can be integrated during machine purchase to enhance automation levels in production lines.
2. Optional Configuration for Hot Chamber Die Casting Machines
- The H-Series Hot Chamber Machines (HCH Series) also support optional automatic ladlers, particularly for low-melting-point alloys like zinc or lead.
- The integrated furnace design of hot chamber machines, combined with an automatic ladler, enables continuous molten metal supply, optimizing efficiency for high-volume production.
3. Comprehensive Auxiliary Equipment Supply
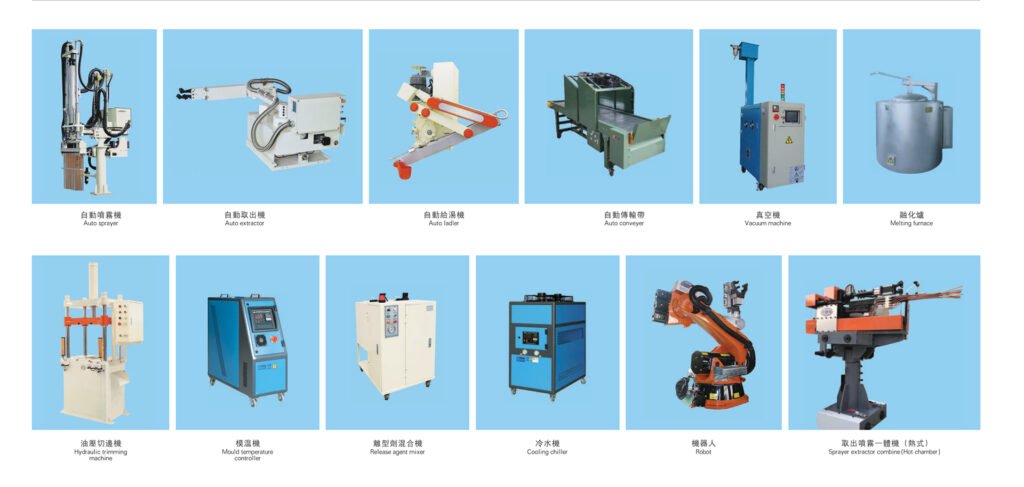
- As a full-service die casting solution provider, Haichen supplies not only the main machines but also auxiliary automation equipment.
- Their auxiliary offerings include automatic ladlers, spray systems, robotic extractors, and more. Purchasing directly from Haichen ensures compatibility, reduces costs by eliminating intermediaries, and streamlines production line integration.
4. Applications and Benefits
Automatic ladlers are ideal for high-precision or large-scale production scenarios, such as:
- Aluminum Heat Sink Casting: Haichen’s cold chamber machines with automation can efficiently produce heat sinks.
- Zinc Alloy Door Handle Casting: For example, a 90-ton zinc alloy machine paired with automation enables multi-cavity mold production, boosting output.
Both cold chamber and hot chamber die casting machines from Haichen can be equipped with automatic ladlers. Customers should specify their automation requirements during ordering to receive tailored quotes. These systems are particularly valuable for manufacturers prioritizing automation, precision, or large-scale production efficiency.
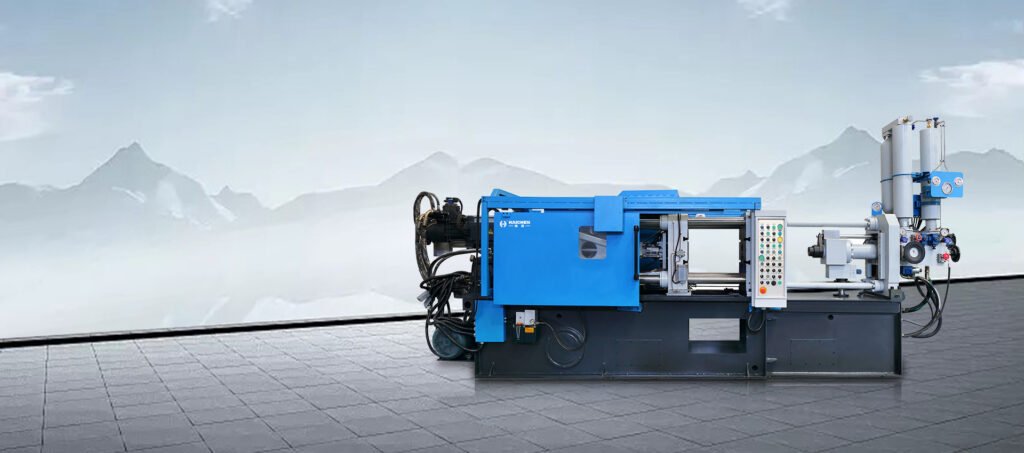
We provide durable die-casting ladle cup.