Zinc die casting is an efficient and precise metal manufacturing process that is widely used to produce complex and precision metal components.
Zinc die casting process
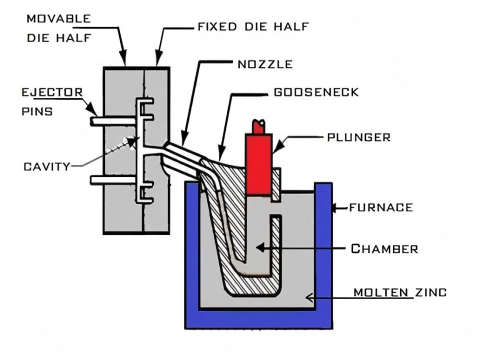
Its main features and processes are as follows:
Melting and Control of Zinc Alloy
Zinc alloy is typically heated to its melting temperature of 380 to 480°C (776 to 902°F) in a melting furnace. And then maintained within this temperature range for stable control. This ensures the uniformity of the molten metal, thereby enhancing the dimensional accuracy and surface quality of the finished products.
Mold Preparation
Die casting molds consist of two halves. It is usually made of hardened steel, which are used to form the shape of the final product. The molds need to be precisely machined and lubricated to ensure that the molten zinc can be smoothly injected into the mold and facilitate the subsequent demolding operations.
Injection and Cooling
The molten zinc is injected into the mold under high pressure, typically through a component known as a “gooseneck.” After injection, the zinc solidifies rapidly as it cools, forming the desired part. The cooling time depends on the size and complexity of the part. It usually ranging from a few seconds to several minutes.
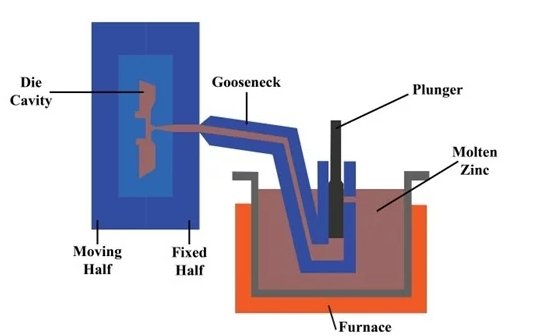
Mold Opening and Part Ejection
The cooled zinc part is pushed out of the mold, generally using ejector pins or other mechanical devices. After demolding, the part may have burrs or flash that require further processing.
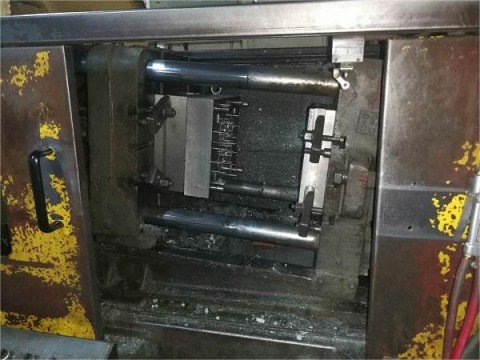
Post-Processing
The demolded parts may need to undergo subsequent machining processes such as grinding, polishing, drilling, and tapping to improve surface quality or add functionality. Additionally, surface treatments like electroplating, painting, and anodizing can be applied to enhance the corrosion resistance and aesthetic appearance of the parts.
Quality Inspection
Finally, the finished products undergo strict quality inspection, including dimensional tolerances, surface defects, and mechanical properties, to ensure that all parts meet the required standards of the customers.
Advantages of Zinc Die Casting
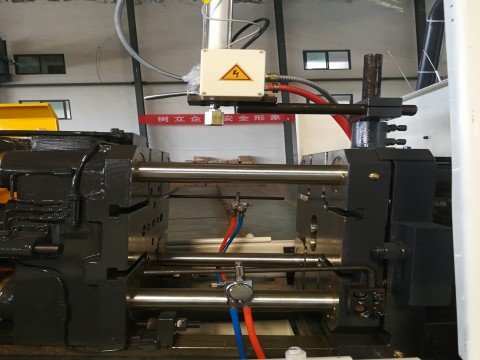
High Precision and Dimensional Consistency:
Zinc alloy has good fluidity, enabling the production of parts with high precision and complex shapes.
High Production Efficiency:
Due to the low melting point and rapid cooling characteristics of zinc alloy, the zinc die casting process is fast, typically producing multiple parts per minute.
Cost-Effectiveness:
Compared to other metals such as aluminum and magnesium, zinc has a lower melting point, longer mold life, and lower processing costs, making it highly cost-effective.
Wide Range of Applications:
Zinc die castings are widely used in industries such as automotive, electronics, consumer electronics, and machinery. And they are suitable for manufacturing complex parts like car door locks and electronic enclosures.
Zinc die casting machine supplier: Haichen Machinery
Haichen Machinery (Haichen Machinery) is a professional supplier of zinc alloy die casting machine, the following is a detailed introduction about its zinc alloy die casting machine and related services:
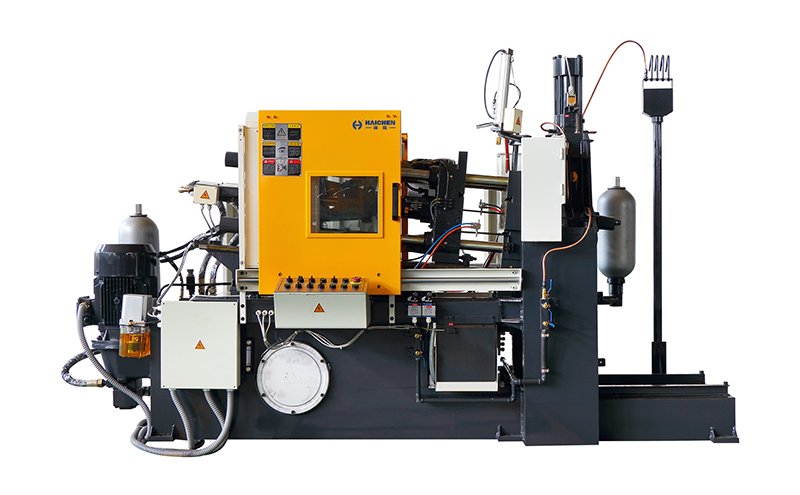
Product Features
Professional design:
Haichen’s zinc alloy die casting machines adopt advanced design concepts, and its H series hot chamber die casting machines are specially designed for low melting point metals (such as zinc alloy and lead alloy). The injection cylinders and pressure chambers of these machines are arranged vertically, and the pressure chambers are immersed in the molten metal in the furnace, simplifying the operation process.
High efficiency and energy saving:
Haichen’s die casting machines offer both fixed pump and servo system options for energy saving. Its hot chamber die casting machines allow the injection and solidification processes to be carried out quickly and continuously due to the fact that the molten metal liquid is always in a molten state, thus increasing production efficiency.
High-quality castings:
High-quality castings can be obtained using lower pouring temperatures due to the fact that the molten metal flows in a closed pipe, with little temperature fluctuation and less possibility of oxidized inclusions.
If you are interested in Haichen’s zinc alloy die-casting machine, welcome to consult us.