Die casting molds, also known as die casting dies, are essential tools used in the die casting process to shape molten metal into desired parts. Here are the main components of a die casting mold:
These components work together to ensure the efficient and accurate production of high-quality die castings. The design and construction of the mold are critical factors in achieving the desired part geometry, surface finish, and overall quality.
Components of Die Casting Mold
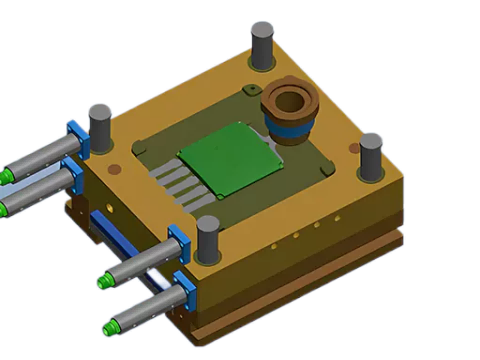
Cavity and Core
- Cavity: The cavity is the main part of the mold that forms the external shape of the casting. It can match the geometry of the final part. The cavity is usually located in the mold’s two main sections: the cover die and the ejector die.
- Core: Cores can create internal features or holes in the casting. They can be fixed or movable. Movable cores can be designed to slide or rotate to allow for more complex geometries. For example, a core might be used to create a threaded hole or a hollow section within the part.
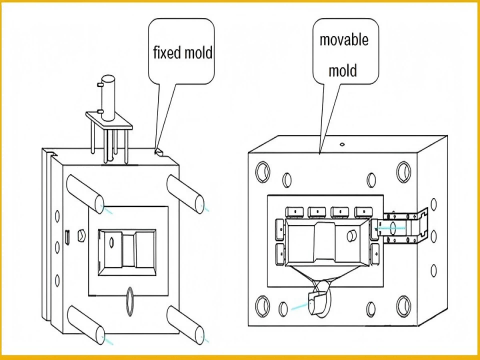
Sprue and Gating System
- Sprue: This is the main channel through which molten metal enters the mold. It can control the flow rate and direction of the metal. The sprue must be able to handle the high pressure and temperature of the molten metal.
- Gating System: This includes runners and gates. Runners are channels that distribute the molten metal from the sprue to the individual cavities. Gates are the narrow openings that allow the metal to enter the cavity. The design of the gating system is critical for ensuring proper filling of the cavity and minimizing defects such as turbulence or air entrapment.
Venting System
- Vents: Vents are small channels or openings in the mold that allow air to escape as the molten metal fills the cavity. Without proper venting, air can become trapped, leading to defects like porosity or incomplete filling. Vents are usually located at the highest point of the cavity to ensure that air is pushed out as the metal flows in.
Ejector Pins and Mechanism
- Ejector Pins: These pins can push the finished casting out of the mold after it has solidified. The ejector die houses them, and their shape matches the part to enable smooth, damage-free ejection.
- Ejector Mechanism: This includes the mechanical components that drive the ejector pins. It may involve springs, hydraulic systems, or mechanical linkages to ensure consistent and reliable ejection of the part.
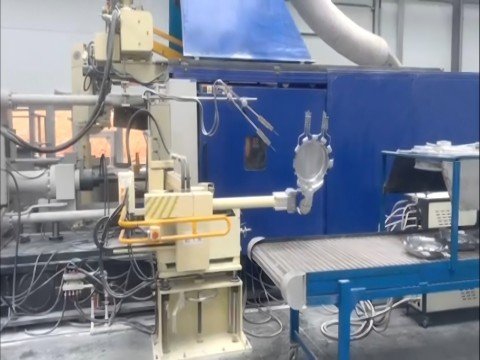
Mold Base and Support Structure
- Mold Base: The mold base is the framework that holds all the components of the mold together. It provides structural support and rigidity to withstand the high pressures and temperatures during the casting process. The mold base also includes mounting features for attaching the mold to the die casting machine.
- Support Structure: This includes various components like support plates, guide pins, and bushings. Guide pins ensure accurate alignment of the two halves of the mold when they close, while bushings provide smooth movement for the ejector pins and other movable parts.
Cooling System
- Cooling Channels: These are passages within the mold that allow cooling fluid (usually water) to circulate. The cooling system is essential for controlling the solidification rate of the casting. Proper cooling helps to prevent defects such as shrinkage or warping and ensures consistent part quality. The design of the cooling channels can provide uniform cooling across the mold.
Inserts and Inserts Holder
- Inserts: Inserts are small components that engineers place into the mold to create specific features or details on the casting. Manufacturers make inserts from different materials, and they often use them to form threaded holes, bosses, or other complex features directly in the casting, eliminating the need for secondary machining.
- Inserts Holder: This is a component that holds the inserts in place within the mold. Operators (or Engineers) must position and fasten the inserts accurately to prevent movement during casting.
Die Casting Mold supplier: Haichen Machinery
Haichen Machinery is a Chinese company specializing in the manufacturing and supply of high pressure cold chamber die casting machines, hot chamber die casting machines and related equipment.
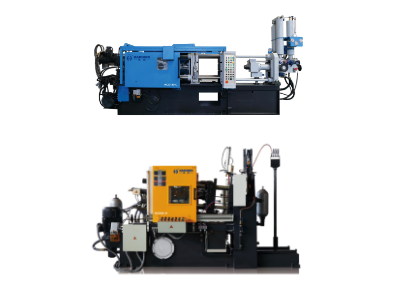
We have rich experience in designing and making molds for aluminum die casting, zinc die casting, and magnesium die casting.
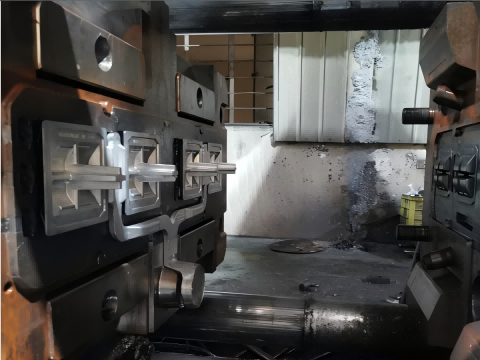
Die casting molds have complex and varied components, each with a specific function and role. These components work together to ensure that the die casting process runs smoothly and ultimately produces a high quality metal part.