How Mold Temperature Controller Work : It precisely regulates mold temperature via coolant circulation to ensure consistent casting quality .
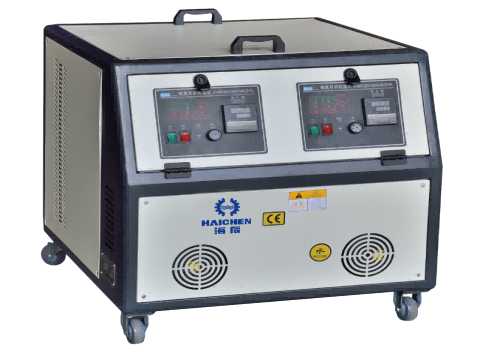
Mold temperature control must be done to exact specification as it is extremely important in achieving quality part production using die casting.
A machine that seeks to maintain even heating during the die casting process is known as a mold temperature controller. It is designed to automate the heating of the mold and to maintain a set mark throughout the cycle plan.
This document will discuss the function of controllers to the process of die casting and why temperature control is of utmost importance.
The Value of Controlling a Molds Temperature
- Even Repeative Quality
- Minimum Possible Faults
- Faster Cycle Counts
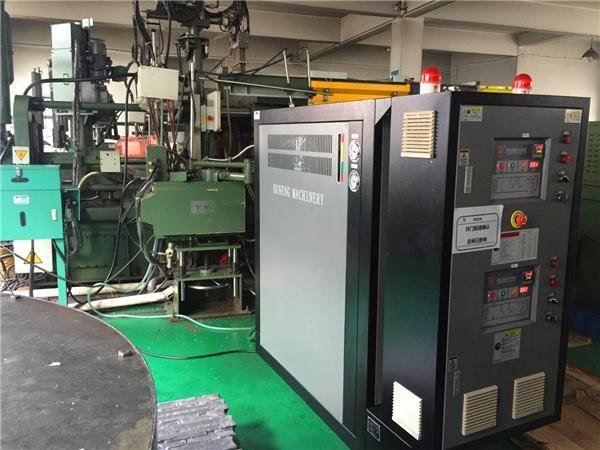
Even Repeative Quality
Industry set standards have to be met in terms of precise measurements and contour shape. Guaranteeing proper temperature setting in pre-defined intervals ensures that the parts produced will, albeit sometimes uniformly replicated. This is step is necessary towards achieving zero defect production with close-tolerance advanced feature technology.
Minimum Possible Faults
Lacking inspection or low supervision increases defects which can randomly occur in gap measurement, molding, and processing such as porous space, reduction in volume, and formation of bends. The above mentioned factors are greatly reduced due to accurate temperature management when the mold is retained within preset boundaries.
Faster Cycle Counts
The ability to produce more within a period lowers the cost per unit. climbing the temperature reduces cycle time. This saves time with every injection. Keeping the internal environment of the mold free of thermal variations leads to stable temperature which boosts the production rate.
Basic Principles of Mold Temperature Controllers
- Spot Checking
- Mold Temperature Controllers (MTCs)
- Control algorithms
- User Interface
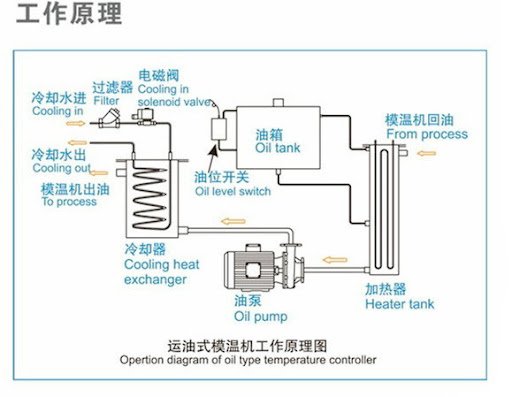
Mold Temperature Controllers (MTCs)
MTCs have a temperature management system that allows the mold temperature to be raised or lowered to the desired temperatures. The heat can be provided by heating elements while the cooling can be done by cooling channels or heat exchangers. The controllers rely on sensor data to modulate these systems.
Control algorithms
Technologically advanced control algorithms and artificial intelligence embedded in the MTC make sure that the optimum temperature required is maintained by implementing changing process parameters such as injection speed, physical characteristics of the material being used, and even external factors like environmental conditions.
User Interface MTC
comes equipped with a user interface that is specially designed for each operator to monitor and set the desired temperature of the mold.Set and monitored real time feedback, changes can be made as required.
Practical Applications and Benefits of Mold Temperature Controllers
- Automotive Industry
- Electronics Industry
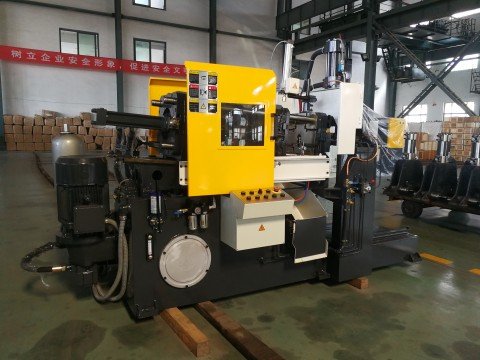
Automotive Industry
Mold temperature controllers are precise components like engine parts, transmission housings, and structural components. All these parts requires absolute precision and indredible structural integrity. Very precise temperature regulation is the answer.
Electronics Industry
Mold temperature controllers are crucial for the production of high precision enclosures and connectors. Quite often they feature complex geometries that have very tight tolerances and use gaps for proper functions and fitting.
HAICHEN: Your Partner in Die Casting Solutions
At HAICHEN, our passion lies in crafting die casting machines that exhibit precision and reliability in their operation. To maintain production quality and efficiency, all our machines outfitte with advanced mold temperature controllers. Regardless of whether you are producing automotive parts, aerospace components, or other high-precision products, HAICHEN has the tools and experience to help accomplish your production goals.
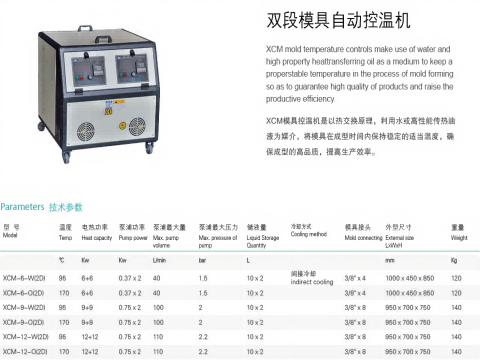
Why Choose HAICHEN?
- Advanced Technology: Our die casting machines guarantee the production of high-quality components through the implementation of cutting-edge control systems, and advanced precision parts, including integration into our vertical die casting systems.
- Custom Solutions: For specific requirements, we provide custom configurations of our machines including the capability of controlling mold temperature.
- Quality and Reliability: HAICHEN machines manufactured to provide the greatest level of quality and reliability, maintaining consistent productivity while averting unscheduled downtimes.
- Comprehensive Support: Beyond customer satisfaction, HAICHEN dedicated to providing extensive after-sales support, in addition to technical and maintenance assistance.
Mold Temperature Control Innovations and Trends for the Future
- Smart Control Systems
- Energy Efficiency
Smart Control Systems
- Integration into IoT: In the future, mold temperature controllers will most likely have the ability to interface with the Internet of Things (IoT), enabling remote temperature adjustment of the mold. This capability will streamline the optimization of production processes and boost efficiency on a larger scale.
- Predictive Maintenance: Advanced analytics and machine learning algorithms will used to predict potential issues with the mold temperature control system. This will allow for proactive maintenance, reducing downtime and improving the reliability of the production process.
Energy Efficiency
- Energy Recovery Systems: New developments in mold temperature control will focus on energy recovery systems that can capture and reuse heat from the cooling process. This will not only reduce energy consumption but also contribute to a more sustainable manufacturing process.
- Adaptive Control: Adaptive control systems will adjust the mold temperature in real-time based on the specific requirements of the part being produced. This will ensure optimal conditions for each production run, further enhancing part quality and consistency.
Mold temperature controllers play a vital role in the die casting process by ensuring consistent and optimal mold temperature. Mold Temperature Controller Work achieves this through advanced thermal regulation systems that maintain precision ±1°C stability for defect-free production. By maintaining precise temperature control, manufacturers can produce high-quality parts with fewer defects and higher production efficiency.