The comparison of the technical parameters of the cooling chiller in die casting includes constant temperature range, fluctuation, temperature resolution, refrigeration capacity, circulating pump pressure and flow, water tank capacity, etc.
A die casting chiller is a type of equipment used for mold cooling in the die casting process.
Which reduces the mold temperature through the refrigeration system.
Thereby improving production efficiency, shortening casting setting time, reducing scrap rate, and extending mold life.
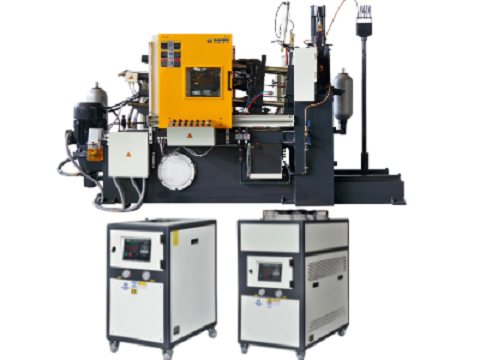
Water Cooling Technical Parameters
Temperature Range: 10–30°C (maintained by closed-loop chillers)
Cooling Speed: High (ideal for high-volume production)
Heat Transfer Efficiency: ~2–4x higher than oil cooling
Maintenance: Moderate (risk of corrosion, requires water treatment)
Applications: Aluminum, zinc alloys (e.g., automotive parts)
Critical Design Parameters
Channel diameter: 8–20 mm (optimized for turbulent flow)
Distance from die surface: 2× channel diameter (e.g., 16–20 mm to avoid cracking)
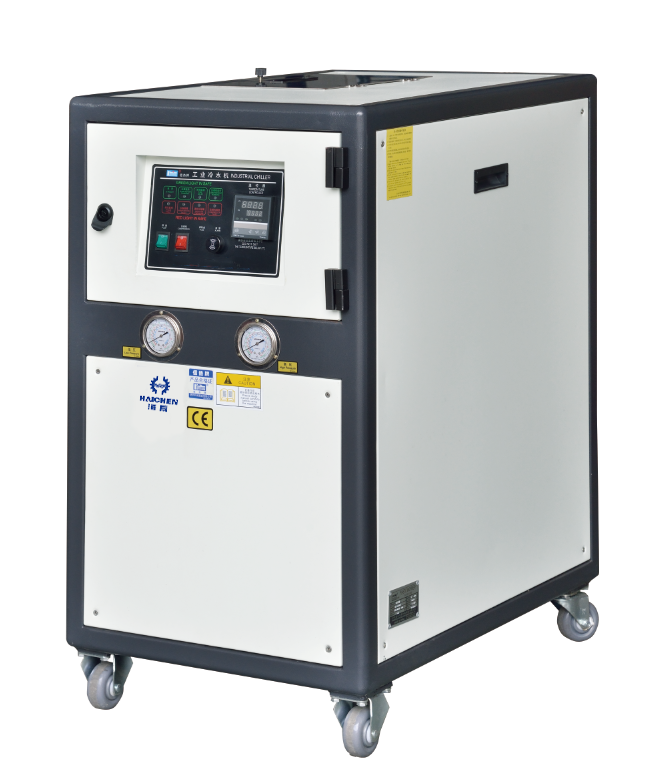
Oil Cooling Technical Parameters
Temperature Range: 200–300°C (thermal oil)
Cooling Speed: Moderate (slower heat transfer vs. water)
Thermal Stability: Excellent (uniform high-temperature control)
Maintenance: High (oil leakage risks, fire hazards)
Applications: Magnesium alloys (e.g., thin-walled laptop housings)
Key Considerations:
Preheated coolant (50°C recommended to reduce thermal shock)
Conformal Cooling Technical Parameters
Cooling Speed: Very high (30% faster cycle times vs. traditional methods)
Channel Design: 3D-printed, contour-following channels (0.5–2 mm resolution)
Cost: High (additive manufacturing expenses, e.g., DMLS)
Applications: Complex geometries (medical devices, aerospace components)
Limitations: Limited to dies with intricate shapes
Air Cooling Technical Parameters
Temperature Range: Ambient (forced-air systems with fans/blowers)
Cooling Speed: Low (suitable for low-volume runs)
Cost: Very low (no plumbing required)
Defect Risks: Warping due to uneven cooling
Optimization Parameters:
Hole diameter (4 mm optimal), spacing (5 mm), and depth (uncontrollable factor)
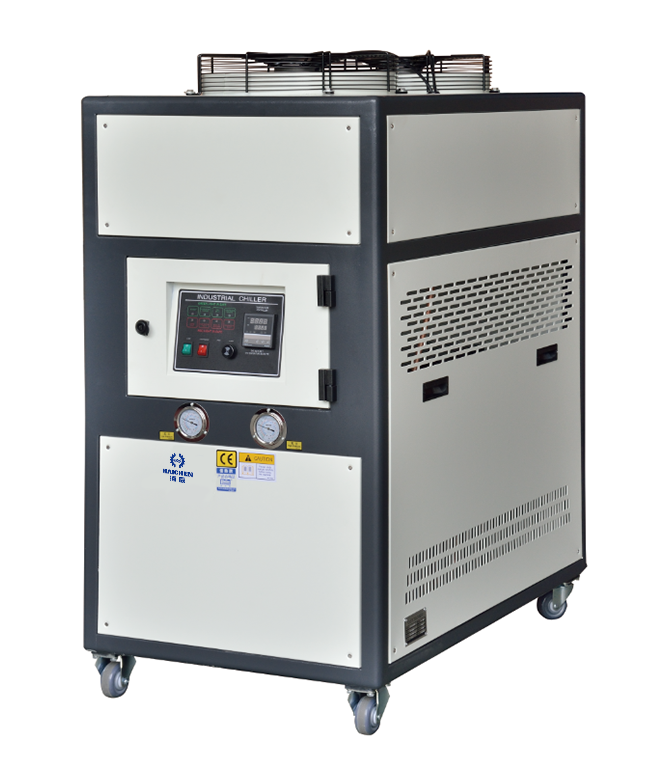
Spray/Mist Cooling Technical Parameters
Cooling Speed: High (effective for thick sections)
Fluid Types: Water-based mist or specialized coolants
Risks: Thermal shock if overused; requires drainage systems
Applications: Aluminum wheels, structural components
Critical Design & Operational Factors
Channel Geometry
Diameter: 8–20 mm (smaller diameters improve cooling uniformity)
Placement: Strategically near “hot spots” (e.g., thick sections)
Distance from surface: 20 mm optimal to balance cooling and stress
Thermal Balancing
Use temperature sensors and infrared imaging for real-time adjustments.
Cooling-heating hybrid systems for dies with large thermal gradients.
Energy Efficiency
Thermoelectric cooling (Peltier modules) consumes high energy but offers precision.
Air-cooling modifications (e.g., nozzle diameter reduction) cut air consumption by 29%.
Safety & Longevity
Avoid coolant temperatures <20°C (risk of die cracking).
Use nitrided surfaces to enhance die durability.
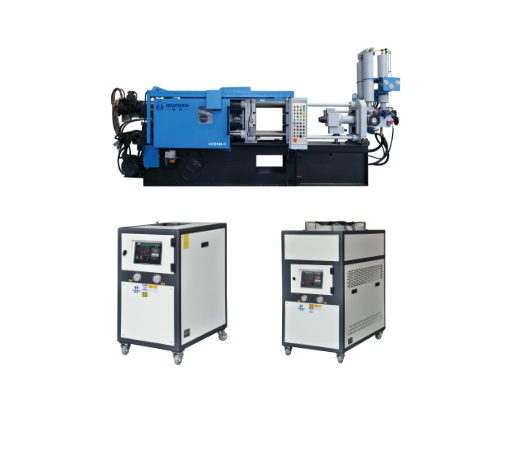
Haichen chiller parameters
Water cooled cased
The industrial chiller is specially designed on purpose to be used inthe plastic manufacturing industry.
This equipment can greatly raisethe working efficiency of manufacturing machines and obviously improve the quality of products and thus,earnmore profit.
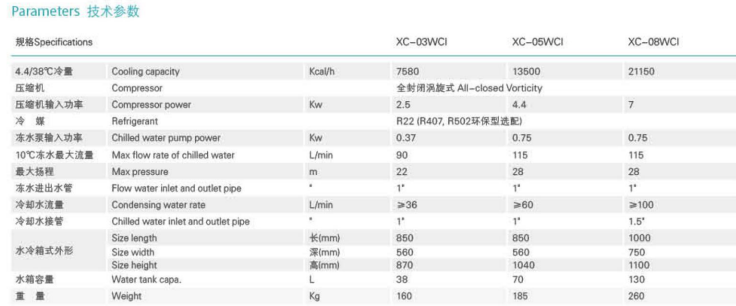
Air cooled cased
The industrial chiller is specially designed on purpose to be used inthe plastic manufacturing industry.
This equipment can greatly raisethe working efficiency of manufacturing machines and obviously improve the quality of products and thus,earnmore profit.
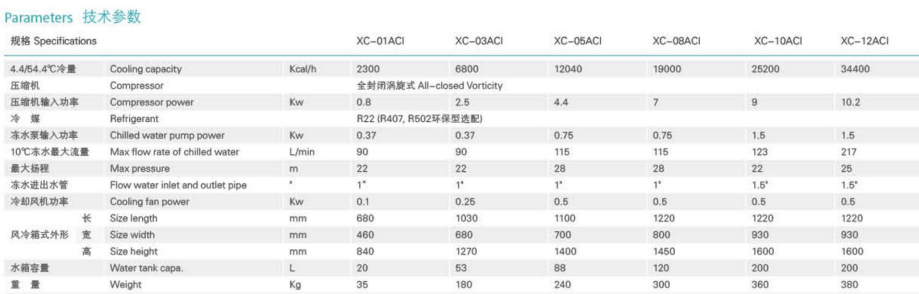
Common Cooling Problems in die-casting
Shrinkage Porosity
As the molten metal cools down and solidifies, it shrinks.
This could result in shrinkage porosity if cooling is not uniform or controlled.
This results in small cavities or internal voids that can weaken the structural integrity of the product.
Thereby making low-quality parts that could eventually fail when under stress.
Thermal Stresses
This may lead to uneven cooling, and therefore, thermal stresses in the die and the cast part.
The inhomogeneous contractions at various parts may lead to warping, cracking, and even premature failure of the mold.
To avoid such cooling, therefore, uniform cooling across the mold is maintained.
If the cooling is poor, then it will create excessive heating in the mold.
As a consequence, it causes rapid acceleration in wearing down.
Gradually, it contributes to distortion in the mold, low dimensional accuracy, and more maintenance or replacement.
Proper cooling maintains the performance for many cycles as well as increases the lifespan of a mold.
Effect on the Final Product from the Improper Cooling
The final product will suffer from various defects due to improper cooling management.
Such as warped parts, cracks, poor surface finish, and internal voids.
All these problems usually lead to decreased mechanical properties and appearance of the cast part.
Thus requiring rework or rejection, therefore impacting production time and cost.
Inconsistent cooling can also increase cycle times, again reducing overall efficiency.